Between rising wages, inflation, and increasing costs of raw materials, the costs of construction projects keep rising.
Therefore, project managers and contractors are constantly looking for ways to lower costs without sacrificing safety or quality.
One way to combat excessive costs is to understand the factors that affect them. Considering each section in this article can prove valuable when working with the budget for a project.
They include client priorities, construction site location, market fluctuations, legislative constraints, and procurement and construction methods.
This post will provide a starting point for exploring all of these.
In this article...
Client Priorities
Client priorities are first on this list for a reason. They are the most important factor that affects the cost of a construction project, and they will differ on every single job.
Client priorities define what quality of work they are willing to pay for, how large the budget is, and the time frame in which they expect the project to be completed.
Requirements of quality, budget, and time always impact the cost of a construction project.
Other client priority considerations might include cost certainty, a desire to remain involved with the project, concerns about risk allocation, and requests for specific technology.
Naturally, one of these requirements can affect the other; for example, if a client’s first priority is to quickly finish a project, the contractor must emphasize that this might require a larger budget than usual.
Also, insisting upon a certain type of material for the build often delays completion time, but if that item is the top priority for the client, a longer wait is usually acceptable.
All other matters hinge on what the client wants and, more importantly, expects.
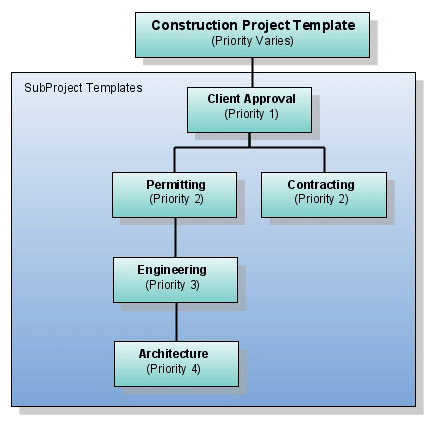
The above project template is a good way to organize the priorities of a construction project.
As you can see, client approval is only achieved after their other priorities have been met, such as permitting, contracting, engineering, and architecture.
To sum up, client priorities tend to be a crucial factor in determining the total cost of a construction project, so don’t underestimate their importance.
Construction Site Location
Building at high altitudes, in flood-prone areas, amongst rocky or heavily sloped fields, and on sites with a high water table adds extra stress and difficulty to a construction project.
A construction site that is difficult to access with construction equipment increases the cost of the project because more resources must be allocated to securing, maintaining, and safeguarding the site.
Here are a few more complicating factors to consider.
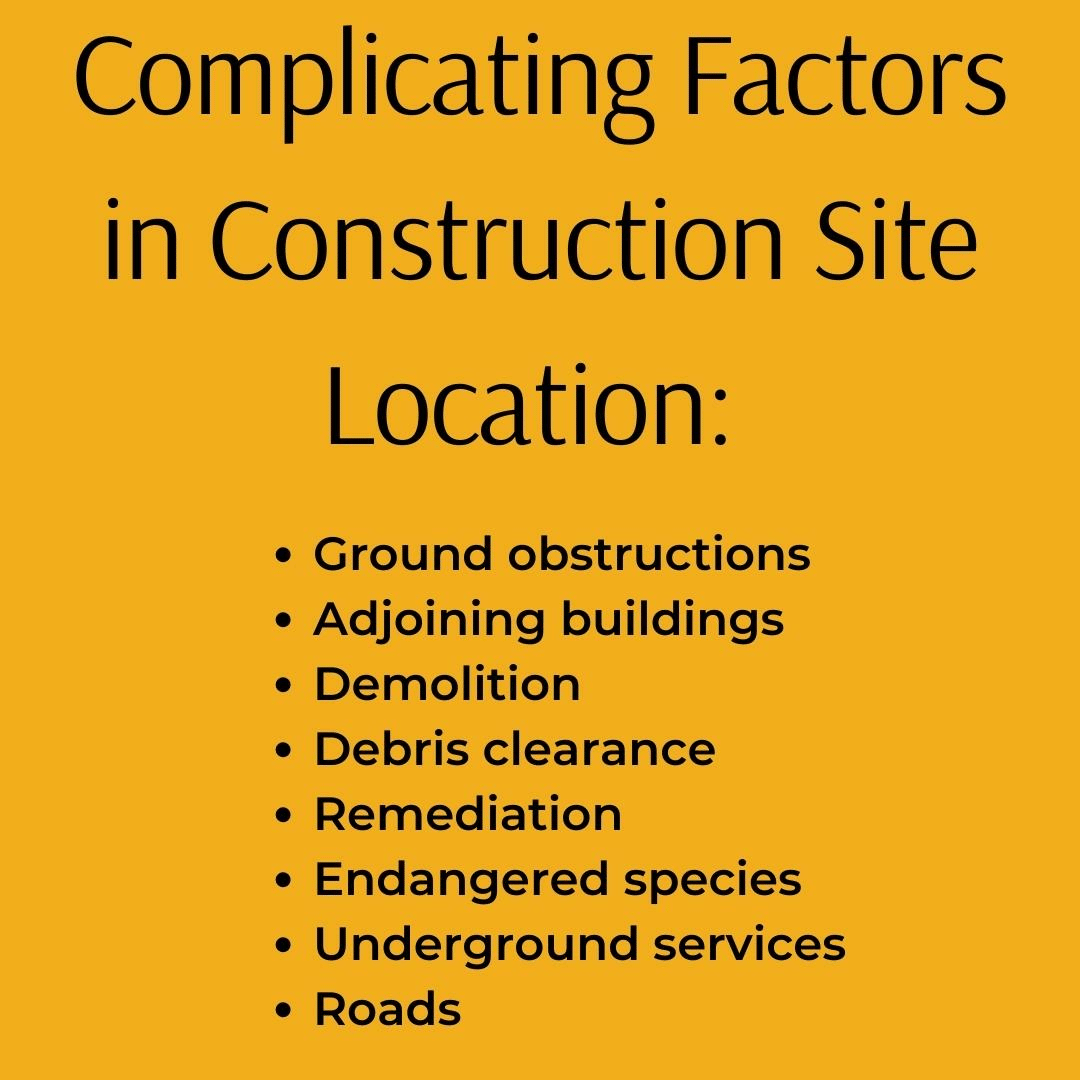
In some areas, varying soil, environmental hazards, insurance snags, and bodies of water might also present challenges.
Each complication adds to the cost of the construction project.
That doesn’t even take into consideration the sites located in rural areas, where construction labor may prove difficult to find and supplies are a long, expensive journey away.
Asking the client to think about the goals for the project and how the site will reflect or affect them is key. For example, how much are property taxes projected to increase year to year?
Is the land location appropriate for its purpose—for example, if the construction is a medical supply store, are there any hospitals, nursing academies, or medical schools nearby?
Sometimes clients who are unfamiliar with the precise location of the construction site do not take these questions into consideration, and end up asking for drastic changes that vastly increase the cost of the build.
Ensuring that every possible aspect of the site is well thought out can prevent this.
Procurement Method
The procurement method greatly affects the cost of a construction project.
Procurement refers to “the process of acquiring goods and services.” The profitability of a project can sometimes depend upon the procurement method alone.
Procurement methods include:
- Traditional Method: The client controls the operating and financing, while the design is left to an architect or engineer, leaving the contractor to concentrate only on the build itself.
- Management Contracting: Usually the first choice for complex projects. In management contracting, the client takes a more passive role than in the traditional method. Here, contractors become the project’s administrator. The contractor chooses and oversees third-party subcontractors as necessary.
- Design and Build: The contractor assumes all risks and undertakes not only the build itself, but also each aspect of the design elements. It is up to the client to ask for changes or adjustments. Once this process is complete, the cost of the project is negotiated.
- Joint Partnership or Venture: In a joint venture, the contractor joins forces with another entity, such as a financing provider, engineering firm, or landholder. The contractor and the partner form a new company solely for the project. Responsibilities and risks are split.
Settling on a procurement method can cause a great deal of stress. It’s daunting even for those who have worked for many years in the field.
This visual aid points out the enormous role of calculated risks in deciding between methods, as many fluctuating factors are in play:
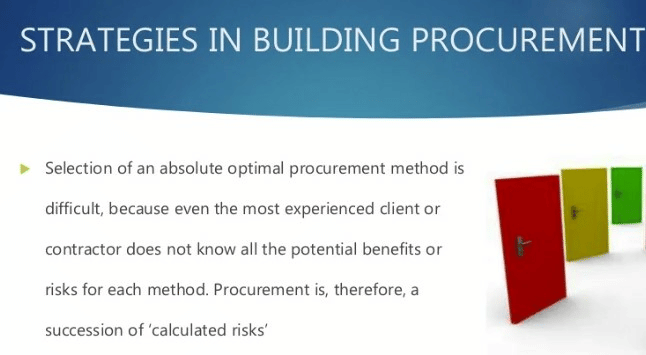
For obvious reasons, project managers tend to fret over choosing the most appropriate procurement method.
However, research indicates that, more often than not, experience guides the decision, and even if the initial procurement method wasn’t the best choice, “alterations were made in contract form to incorporate aspects of the ‘best’ procurement route.”
Studies show that, while picking the most effective procurement method deserves a great deal of attention and research, even if the choice wasn’t the most suitable one, the error in judgment is fixable.
So having the flexibility to make alterations to a procurement method can help to keep construction project costs down.
Construction Method
Choosing the most effective construction method can sometimes raise questions and cause friction between the client and the project manager.
If a third-party engineer or architect are on board, these discussions can become even more fraught.
In addition to specific client requests, the construction method will depend on the building’s function and design.
For example, clients who are concerned about environmental impacts may insist on using as many green building elements as possible. Here are just a few examples:
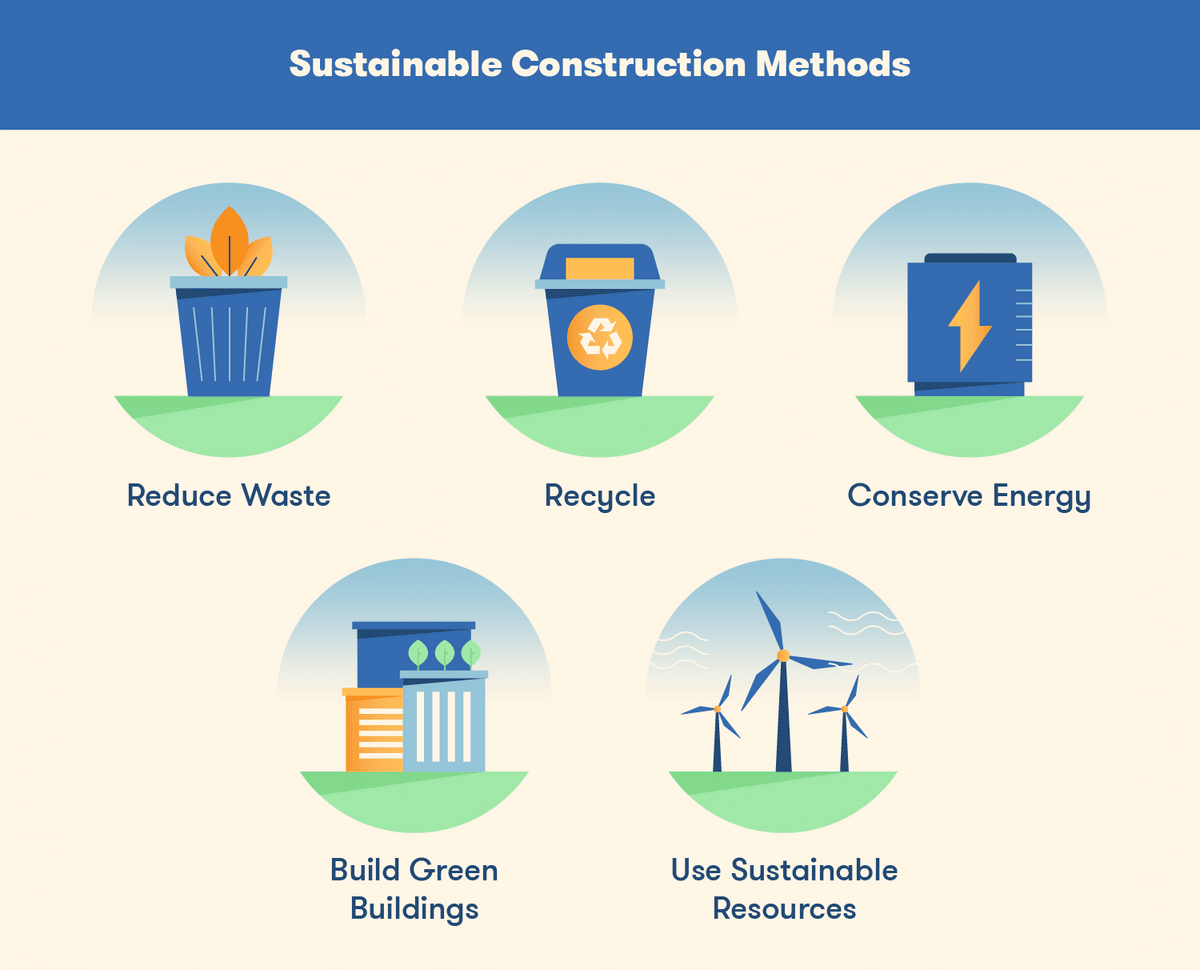
Using reclaimed materials and conserving energy is a good way to keep costs down.
However, “building green” can sometimes prove expensive or unreliable. For example, relying on solar panels for power in Minnesota mid-winter is not practical.
Data indicates that environmentally sensitive projects are 2.5 to 7% more expensive to build, compared to other construction methods.
Ensuring the client is aware of such price differences can help manage their expectations regarding the final cost of the project.
The construction method that is used can also affect the following:
- Price of materials
- Cost and availability of labor
- Subcontractor competition
- Supply chain backups
- Contingency funds
Each of these elements fluctuates, and remaining informed about their status requires time, thought, experience, and research.
Failing to take into consideration how the method of construction influences the final cost can prove highly unprofitable.
It is an exciting time to study construction methods.
Advanced technology, the use of robots, and computer modeling mean that changes are rapidly taking place in how project managers approach means of construction.
Market Fluctuation
Market fluctuations in construction often prove frustrating because stakeholders and project managers can often do little to predict the events that cause them.
For example, massive hurricanes, flooding, housing shortages, or “black swan events” such as COVID-19 are all beyond the control of individual contractors.
In the case of COVID-19, the effect was catastrophic, as supply chains became snarled and factories in each part of the world were forced by their governments to shut down or significantly slow production.
Major market fluctuations can affect construction years after the initial impact, as this graph indicates:
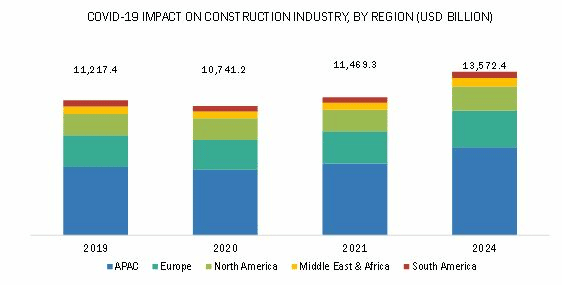
This forecast suggests that the shock of COVID-19 was so severe that it will continue to affect the construction industry even through 2024.
And the blow is experienced worldwide, not just in North America.
In general, construction projects are more in demand during good economic periods and more scarce when potential clients are buffeted by losses.
This often causes a chain reaction throughout the housing market.
For example, the cost of raw materials shoots up when a housing boom is on and must-haves such as lumber and steel are in high demand.
A project that begins in a favorable economic environment may have to limp through a stock market crash past its midpoint.
Preparing clients for these costs and insisting upon a contingency fund can blunt the force of these market changes.
Legislative Constraints
Working with minutely detailed zoning laws, permits, and regulations is a headache for just about every project manager.
More importantly to the client, the costs of these can result in an unpleasant surprise for those who may have thought they’d found an excellent site for a construction project.
Permit costs tend to rise with the complexity of a construction project. On a small scale, consider the differences in the permitting costs for the following single-home projects:
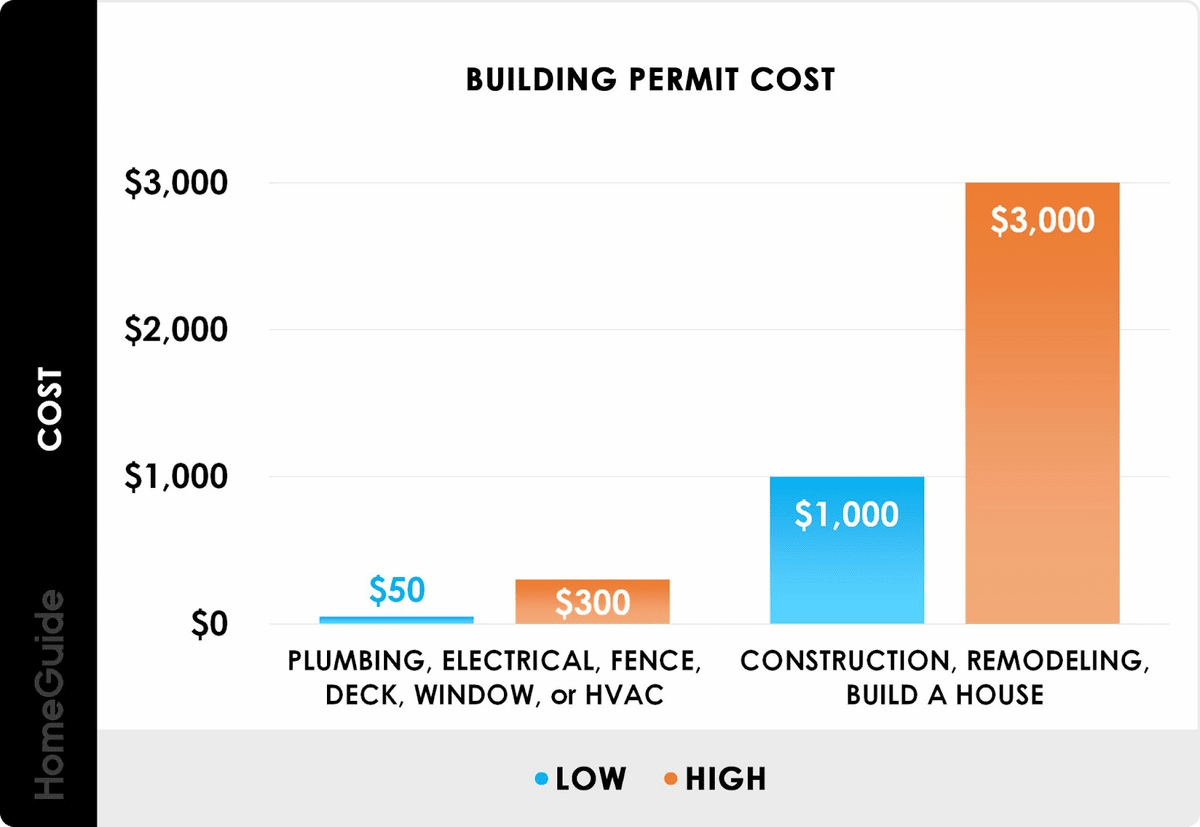
While permitting costs are almost never $0, there is an enormous difference between adding a property line fence and constructing a new home. These all contribute to the project’s final cost.
Usually, legislative hurdles vary by state and region.
Expensive markets with many administrative mazes to negotiate can balloon construction costs past the wallets of some clients.
In San Francisco, CA, for instance, where land is expensive, it costs $737,417 to build just one unit of “below market rate” housing.
On the other hand, an affordable housing program in Nebraska was able to build a stand-alone home for $238,000 in 2021.
Factoring in the time, resources, and fees dedicated to leaping legislative hurdles is frustrating, but inescapable.
Conclusion
While many factors can affect the cost of a construction project, the six we’ve written about are among the most culpable.
They include the priorities of the client and the site of the construction. Building procurement and construction methods also play a role.
Finally, market fluctuations and legislative constraints can greatly impact construction costs when least expected.
It’s important to take all of them into account when calculating the cost of your construction project and discussing it with the client.