One of the biggest challenges in the construction industry is the proper management of materials.
Material management consists of a whole host of activities, such as planning, purchasing, bill obtainment, tracking, adjusting to project scope changes, storing, and waste minimization.
Put that way, the process might sound simple, but the truth is that material management can be full of challenges and unexpected changes.
This is why it’s important to be aware of possible problems like breaking deadlines or going over budget.
Remember, preparation is always half the battle and if you want to find out more about top challenges in construction material management and how to deal with them, keep reading.
In this article...
Establishing an Efficient Material Procurement Process
The first challenge you’ll come across while dealing with material management is related to the procurement process.
Finding a dealer or supplier who can deliver the right materials at the right time and for the right price is often highly challenging.
It’s not uncommon for contractors to make the mistake of choosing their supplier based on who offers the lowest price.
We all want to save money, and while that’s perfectly understandable, sometimes choosing a supplier who costs more is the better option because they offer higher quality.
As a rule, you get what you pay for. So a more expensive supplier may offer you better service, and there is a bigger chance that he will deliver the materials on time and in the quantity and quality you want.
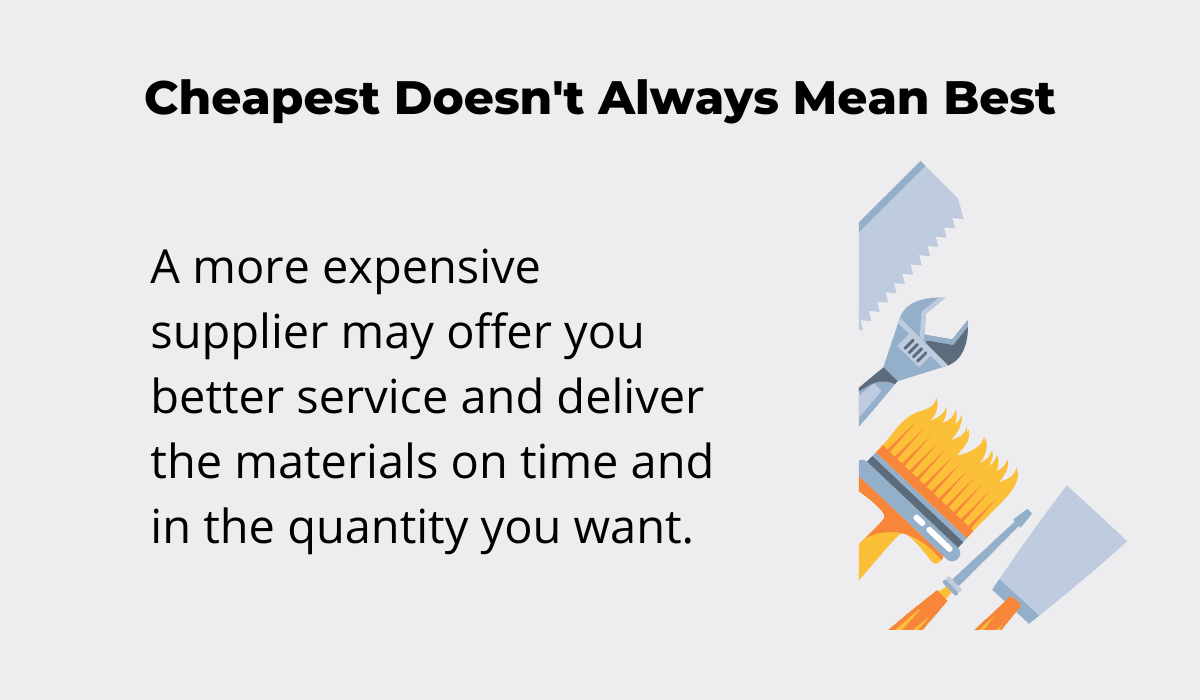
Other than choosing the cheapest supplier, there are several more factors that may lead to delays in material purchasing. The manufacturer might be short on supplies, or they might require more time to get everything ready.
To avoid such delays, try to order everything you need in advance and schedule it to arrive at least two days before you actually need it.
Another thing that can cause a material delay is miscommunication between you and your supplier. You can lose a lot of time because of a lack of clarity.
Therefore, setting clear expectations will prevent delays in manufacturing and shipping.
Delays might also occur due to the Covid-19 pandemic. The United States imports around 30% of its building materials from China, and another 20% from Canada and Mexico.
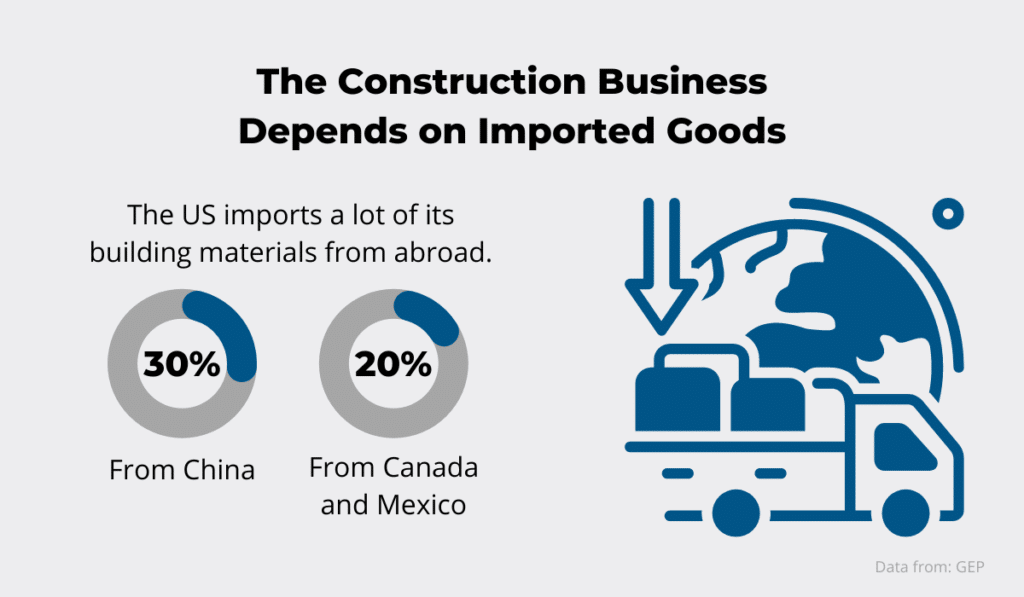
Due to supply bottlenecks and the unavailability of various required materials, the waiting time may be extended from the current 10 to 12 weeks for an extra 6 to 8 weeks.
A simple solution for this is to do your sourcing locally, if possible, or to do it a few months in advance.
So, there you have it; the material procurement process can be more challenging than you’d expect, but if you make sure you find a good reliable supplier and do a little bit of planning and calculating, you’ll be fine.
Obtaining Accurate Bill of Materials Listings
The second challenge in construction material management you’ll need to overcome is obtaining an accurate bill of materials.
Let us first explain what a bill of materials is. Simply put, it is a list of all the raw materials, components, and parts needed to build a project, the quantities in which they are needed, and their cost.
You might be thinking—“oh, so it’s just a recipe, how important can that be?”
As it turns out, quite important.
You see, errors in this document can cause significant problems. For example, inaccurate inventory can lead to production downtime, adding time to the overall product development cycle.
Missing components on a bill of materials will do the same thing, and errors in product costs will impact your overall investment return.
If you’re struggling with keeping an accurate bill of materials, you may want to consider getting some extra help. Modern enterprise resource planning software (ERP) enables construction companies to manage their projects more efficiently.
We must not forget to mention material requirements planning (MRP), an essential part of ERP.
MRP is done through specialized software that will help you calculate the materials and components needed to complete a project.
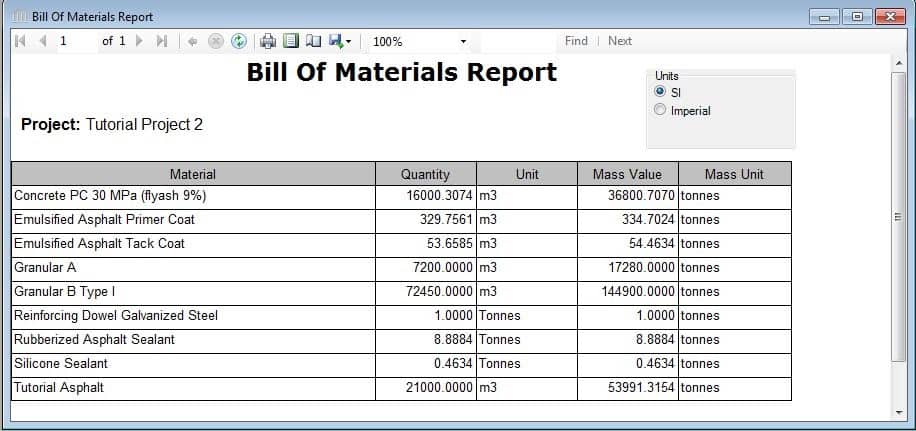
It will also help you ensure that the right inventory is available exactly when needed, at the lowest possible cost.
MRP will improve efficiency, flexibility, and profitability through three main steps: inventorying existing materials and components, identifying additional materials needed, and planning for their purchase.
In short, a bill of materials is crucial if you want to prevent errors in material purchasing and procurement. It’s best to use modern planning software for this purpose since it will make your life a lot easier.
Adjusting to Project Scope Changes
Even if you’ve planned your project perfectly, down to the last detail, there will always be instances where you will need to make changes.
Some things simply can’t be avoided; accidents, weather changes, the unavailability of supplies, etc.
We’ve already mentioned that materials can always be delayed and that changes in quantity can occur.
You won’t always be able to immediately source all of these materials. And if you do, you’ll likely need to pay a higher price which will cause budget overruns for your project.
If you have a good relationship with your suppliers, this might be less of a problem, but it’s still an unplanned cost.
Therefore, it’s a good idea to always plan some alternatives, just in case.
To start with, try to prepare for any scenario while negotiating and make sure as much as possible is covered in the contract.
A verbal agreement is not good enough; make sure to document everything.
Communication, coordination, and planning are vital, and all changes must be put in writing.
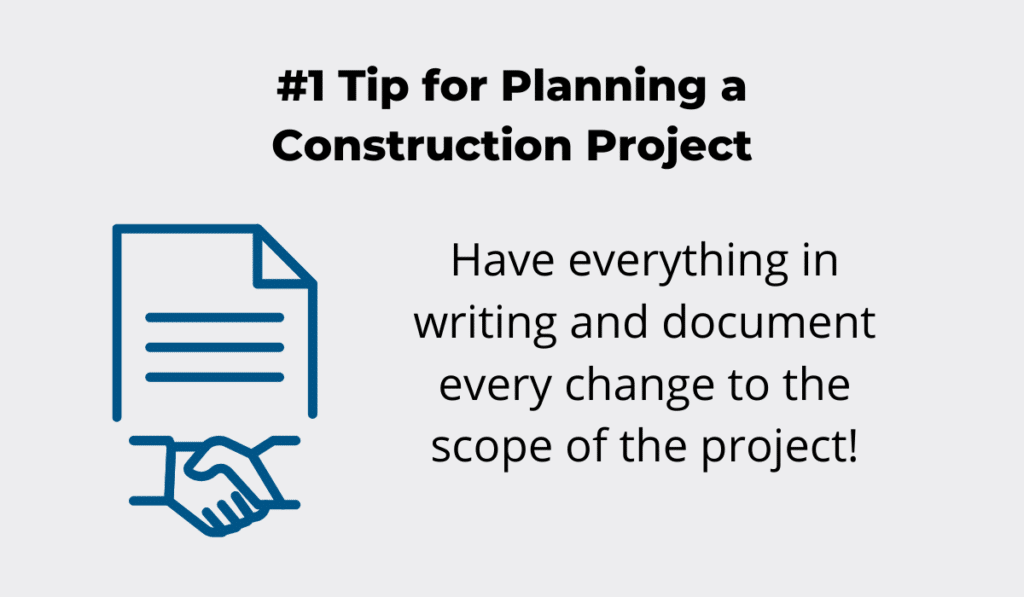
This way, you’ll have proof of an agreement which will help you avoid any further problems. You may think that documenting every single change is too much, but keeping a record will provide a foundation for effective planning.
Remember, prevention is better than a cure.
Again, this is where your project management software plays a key part. It’s not only helpful in obtaining the list of materials, but it can also be valuable for managing project scope changes.
Of course, your whole team should be informed about the changes, so make sure to use a tool that the entire team can use.
Simply put, without a plan to manage scope changes, your whole project will suffer.
Think of it this way; why is the Tower of Pisa leaning? Because its foundation is weak. The same goes for material management; always plan ahead and consider the possible scope of the changes before they even happen.
And document everything!
Setting Up Sufficient Storage Space
The next challenge in material management often gets neglected. We’re talking about setting up sufficient storage space.
On a construction site, a storage space provides protection and control for materials that are to be kept during the building process.
In other words, you need to protect your valuable materials from damage and theft.
When possible, don’t leave your materials out in the open. Still, if you must, try using close-boarded fences, and organizing patrols.
When it comes to setting up your storage space, several things need to be considered. The most important ones are the location and size of the storage area.
Both should be carefully planned because you don’t want to end up with more materials on-site than your storage space allows for.
Ensure that the storage area is near your construction site to minimize transportation costs and save some time.
Storing materials in different places makes it difficult to track them, so try to keep everything in one place. If this isn’t possible, make sure you can move the materials as needed.
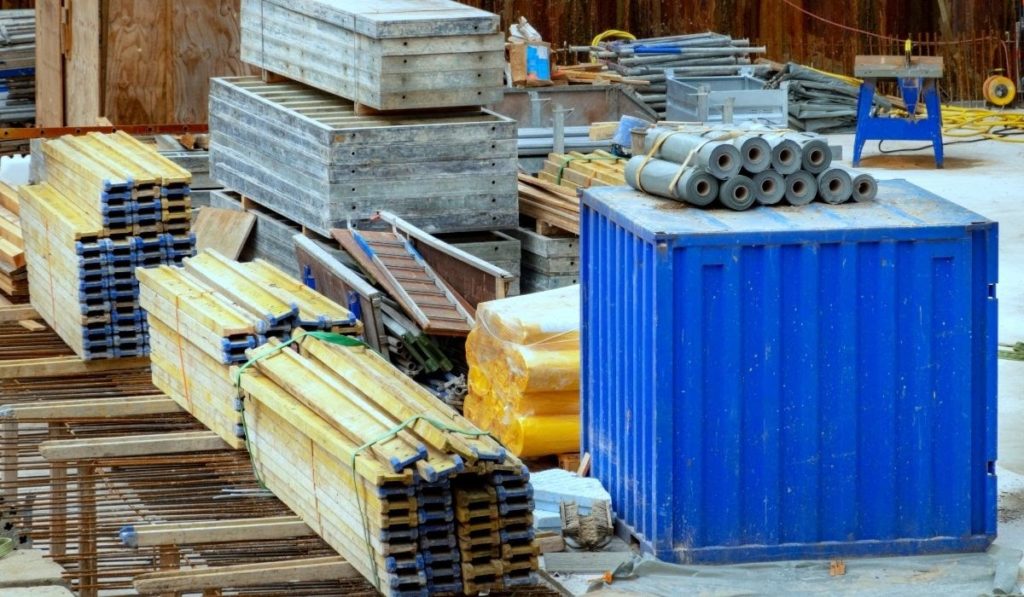
But what if you simply can’t provide enough storage space? The best solution for this scenario is to carefully plan delivery times and quantities.
In this way, you will reduce the need for storage. Of course, this can’t be done without a good and reliable supplier.
Nowadays, most suppliers offer self-pickup options to pick up the materials by yourself, making sure you don’t depend on a delivery company. You never know, they can deliver your goods to the wrong address or deliver the wrong materials.
Self-pick-up is a safer option; you can simply pick up the materials when you need to use them and, in that way, save storage space.
Storing your materials can be a real challenge. If you don’t have enough space, don’t worry, you can always plan delivery times and quantities to reduce storage needs.
Maintaining Accurate Inventory Counts
Another challenging thing related to material management is maintaining accurate inventory counts.
We all know that keeping inventory is very useful and makes purchasing and storing your materials more accessible.
However, in 2018, 52% of project rework in the US was due to poor inventory management. The cost of this was 31.3 billion dollars.
Inaccurate inventory tracking continues to cause problems in the construction industry. Obviously, this is a painful process for most companies.
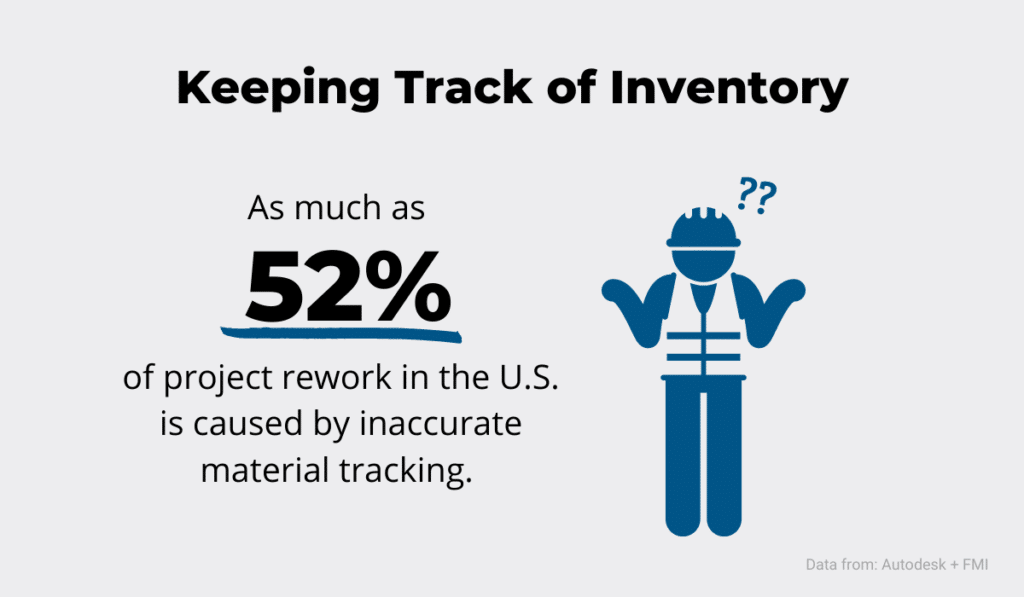
But it doesn’t need to be. The solution is the usage of tracking systems.
Thanks to equipment tracking, you can stay on top of your inventory and always be aware of what tools and materials are available where, whether certain materials are on backorder, as well as if there’s a specific need for a certain type of equipment or material at a particular site.
For example, you can never overorder materials you already have if you track their numbers.
Tracking your inventory involves controlling your materials at every stage, from fabricating to installing.
The primary purpose of a material tracking system is to ensure that the materials you need are available on time and in the right quantity, but there are also many other benefits to it.
If you track your tools and materials, you’ll avoid losing them and reduce the time spent searching for them.
For instance, our equipment tracking software, GoCodes Asset Tracking, is a complete tracking software solution that combines cloud technology, a mobile scanning app, and our own patented QR code system that will help you track your entire inventory, at the office or in the field.
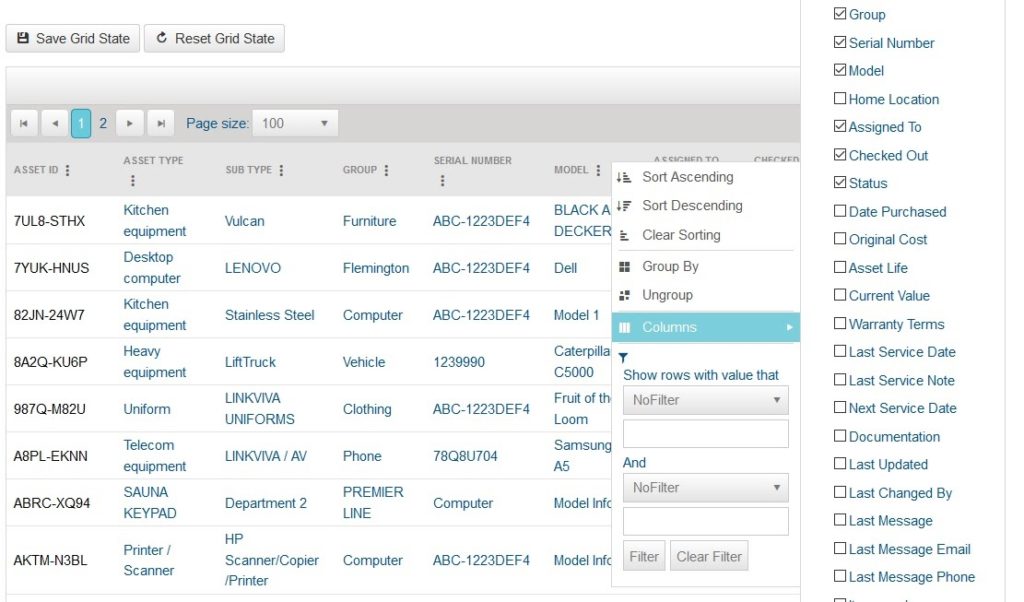
When it comes to inventory maintenance, it can make or break your project. If your inventory isn’t regularly updated and tracked, problems can occur on your construction site.
The best way to avoid this is to keep your inventory regularly and use software to do it.
Minimizing Material Waste
And this brings us to the last challenge—minimizing material waste.
Did you know that the construction industry is responsible for around a third of the world’s total waste?
Furthermore, according to the statistics, in 2018, construction companies generated 600 million tons of waste and debris in the US alone.
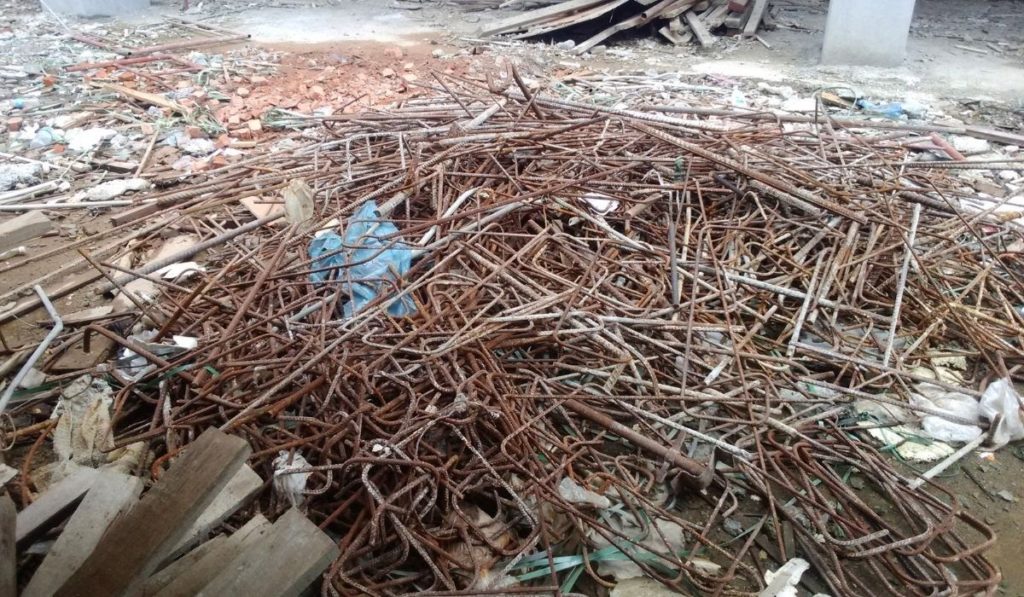
Wood, drywall, metal, concrete, plastic, glass are only some of the materials that tend to go to waste.
And it’s a real shame since around 60 – 80% of the budget goes to materials and the labor for handling those materials on a construction project.
Basically, if you waste less, you spend less.
So how can you minimize waste? Well, for starters, try to avoid creating any in the first place. For example, you can take exact measurements before purchasing materials to avoid any leftovers.
Another thing you can do is educate your staff on the importance of minimizing waste and train them to implement greener practices in their waste management.
However, sometimes waste can’t be avoided no matter how hard you try.
In those cases, the best thing you can do is reuse as many materials as possible. This can often be done if materials are in good condition.
This way, you will reduce the consumption of raw materials, minimize landfill waste, and reduce fossil fuel emission.
For example, in 2005, a Dutch architecture firm named Superuse constructed the world’s first contemporary house made mostly of waste construction materials. The only exceptions were a few interior walls and isolated glazing.
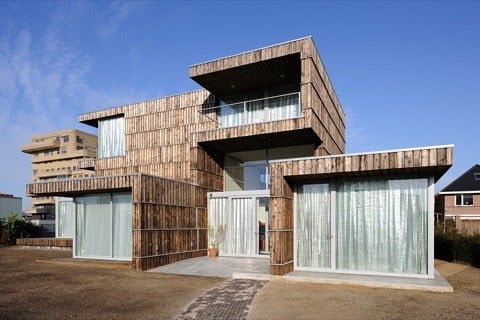
Villa Welpeloo, as it’s called, is made from the steel from defunct equipment formerly used in the textile industry and timber from old industrial cable reels, as well as other second-hand materials.
So, to sum up, while avoiding waste on a construction site is nearly impossible, good material management and reusing old materials can help you reduce its negative effect.
Conclusion
Construction materials are quite literally the building blocks of a good construction project. Without them, there can be no project, so good material management is crucial.
However, it is also challenging.
The best thing you can do is plan ahead, but it’s still entirely possible for something to go wrong.
However, by following the advice in this article, you’re much more likely to face those challenges head-on, minimize them, and manage your materials with optimal efficiency.