These are exciting times for the construction industry. Last year, it was valued at $1.36 trillion in the US alone, mainly due to increased spending on private and nonresidential buildings.
But there’s more. Experts predict that the worldwide population will hit 10 billion by 2057, and as the number of people grows, so does the demand for real estate.
Add to it the fact that almost 56% of the population lives in urban areas, the prospects for the industry seem great.
But not everything is rosy. Like in every other industry, there are problems persistently impacting profit margins, productivity, and business sustainability.
You need to be aware of those issues so you can prepare yourself for any setback that may come your way. So, here are the top ten problems currently facing the construction industry that can stunt the development of construction companies.
In this article...
Poor Project Performance
Project delays are almost expected in construction.
Clients change orders, rework needs to be done, workers are unproductive, or the entire project changes its scope. Things often don’t go according to plan.
It doesn’t help that construction projects are becoming increasingly complex, while the industry has to accommodate increased regulations, competition, and labor shortages at the same time.
The coronavirus outbreak hasn’t helped the industry either.
According to the Commercial Construction Index published by the US Chamber of Commerce, a large majority of contractors have suffered project delays due to pandemic restrictions. Almost 85% expect these delays to continue throughout 2021.
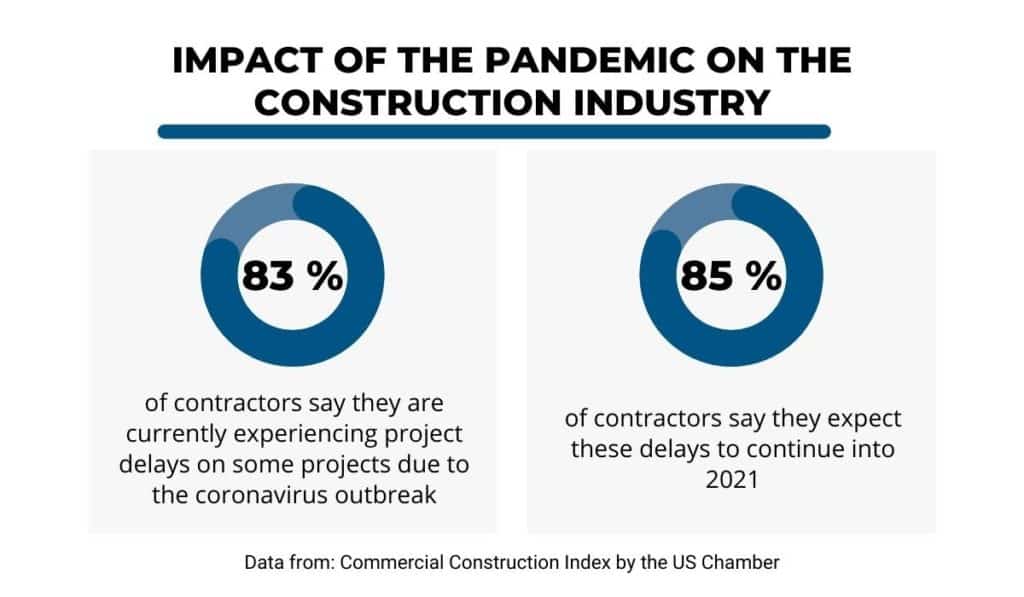
Basically, poor project performance is the result of multiple factors that the construction industry is currently facing. Unfortunately, the most common response to this challenge has been to maintain the status quo.
Slow Cash Flow
Getting paid in the construction industry is also becoming increasingly slow and difficult.
Without a relatively reliable income, companies can’t pay their bills and employees, or order necessary supplies for construction projects.
Simply put, if they can’t handle existing projects properly, they can’t grow their business either. And if the cash flow problems persist, companies will likely face business failure.
This is a reality for almost 50% of construction companies. They are not being paid on time, which causes delays in paying for labor and materials.
Consequently, they have to rely on making phone calls, sending emails, and invoicing customers continually until they receive what they’re owed.
So, how do contractors deal with cash flow problems? According to the same survey from Levelset, they usually tap into their savings.
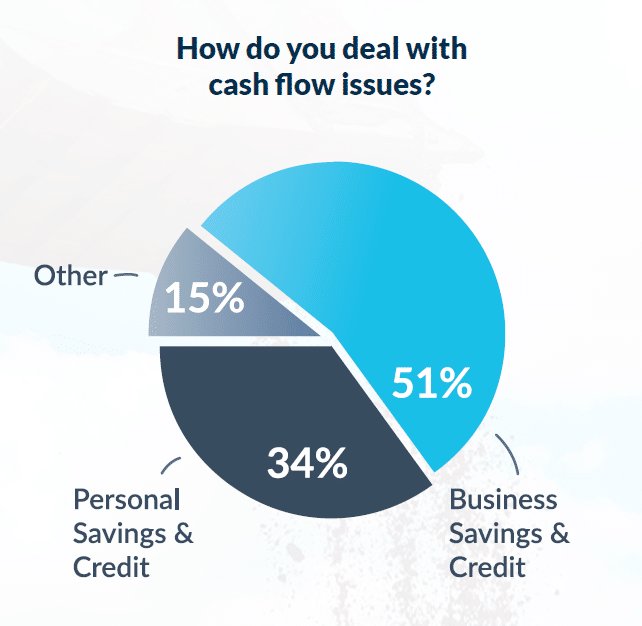
The majority rely on their business savings and credit to keep their companies afloat, but others have a different tactic.
When worst comes to worst, contractors can file a mechanic’s lien to get their money.
This is a legal document against a property that guarantees payment to the contractor that builds or improves it. They are created to protect construction professionals from going unpaid for their labor and materials.
However, most contractors avoid liens because they fear damaging the relationship with a customer or simply find the process too expensive.
As a result, most construction companies have to eat the costs. In the end, this damages their success.
Material Shortages and Rising Costs
The corona pandemic hasn’t just caused project delays. It has also impacted the supply chain.
Many countries are experiencing construction material shortages, and the situation is especially dire in the UK.
Almost 71% of contractors report an increased need for timber, steel, and lighting that they are unable to meet. Ongoing disruptions caused by Brexit have only compounded the issue.
Here are the primary material shortages:
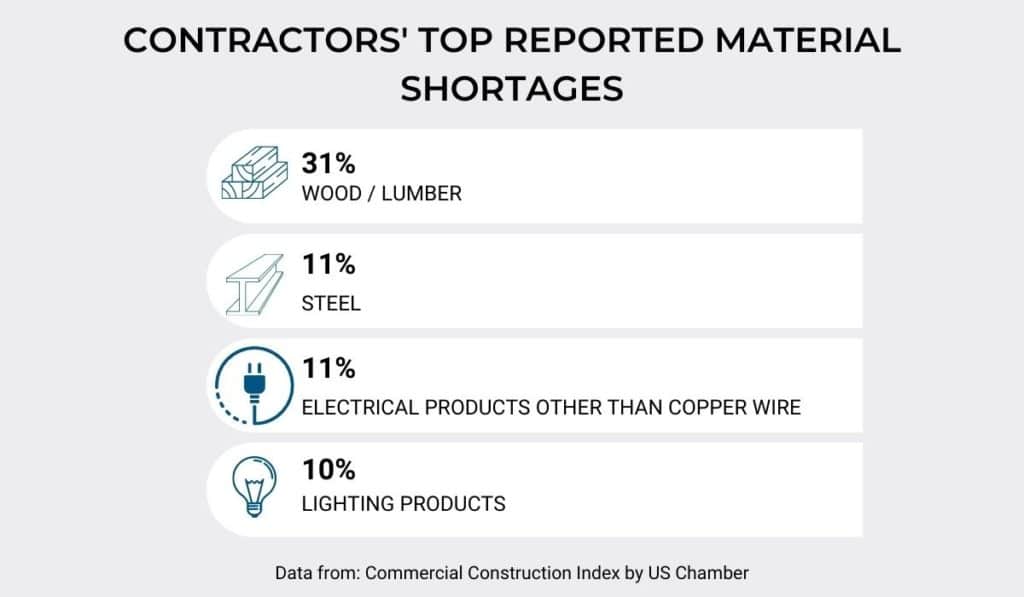
Some experts trace these shortages in material back to the rise in the number of construction and home improvement projects undertaken during the first lockdown in 2020.
On top of that, many of these goods are shipped from China. So, when the borders closed, there were many disruptions in the supply chain.
But the bad news doesn’t end there.
Because of these disruptions, prices increased for essential materials such as aluminum, steel, and timber. In addition to this, growing international trade conflicts and increased tariffs also impact construction costs.
This means that the buyers will have to pay more to finance construction projects.
When it comes to material shortages and rising prices, the only thing remaining is to wait for the industry to catch up with the demands. Only then can we expect the costs to decline.
Labor and Skills Shortages
Hiring skilled workers has been a major problem for the construction industry since 2008. Almost two million people lost their jobs, and it took the industry over ten years to reach pre-recession employment numbers.
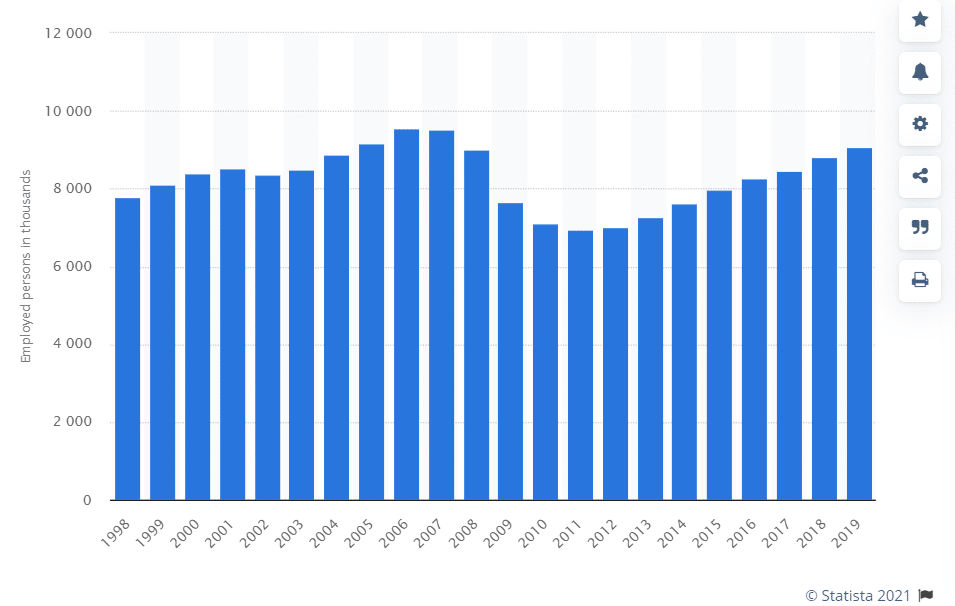
Nevertheless, even though there’s been a steady increase in the number of construction workers since then, many contractors still have significant problems hiring skilled labor.
To be precise, according to the Commercial Construction Index we’ve already referred to, over 83% of contractors have difficulties finding engineers, supervisors, and estimators.
Why is this happening?
First of all, some of the workers who had lost their jobs during the recession managed to find other employment and never returned to the construction industry.
Second, most construction workers currently in the industry are over 40 years old, with 37% being close to retirement age. Young workers (20-30 years old) make up only 12% of the construction workforce.
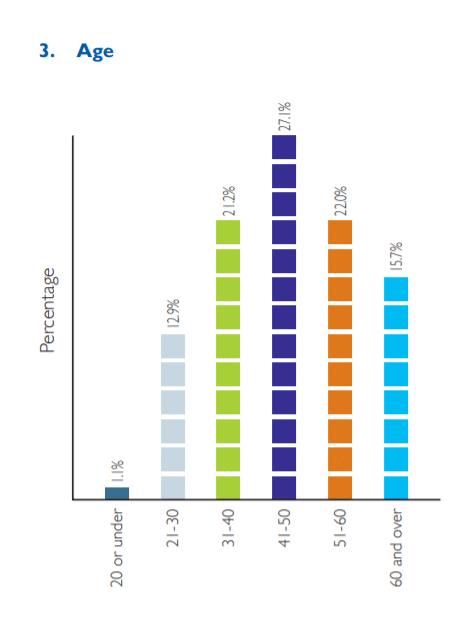
Therefore, the construction industry is overrun with older workers. The reason for this is that many young people perceive construction as difficult and dangerous.
Other reasons include potential differences in work ethic, job expectations, and attitudes which make construction less appealing to young generations.
The lack of skilled workers can severely impact a company’s ability to fulfill its contracts. It also means that the industry is lagging without fresh perspectives and innovation from younger generations.
In the end, the future of construction largely depends on attracting new and younger talent to meet the increasing construction demands and challenges.
Inadequate Risk Management
A common pitfall for contractors is managing risk in their construction project management. Often, they focus on long-term risks and try to push short-term issues under the rug.
As risks in construction become greater and their mitigation more expensive, even these minor issues can significantly impact the project’s budget and schedule.
Here are some common risks in construction:
Design risks | Design errors Requests for late changes Failure to follow with the contract |
External risks | Introduction of new stakeholders Law and regulations change Tax change Public protest Natural disasters Equipment and tool theft |
Environmental risks | Incomplete environmental analysis New alternatives to minimize environmental impact |
Organizational risks | Frequent staff turnover Inexperienced workforce Delayed deliveries Safety issues Material shortages |
Project management risks | Failure to comply with quality requirements Scheduling conflicts Project team conflicts Poorly defined scope |
Administrative risks | Expired permits Disagreements in construction documents |
Construction risks | Property cost increase Technology changes Unknown site conditions |
Managing risk is all about identifying problems and finding solutions. Remember that you can’t prevent every issue from happening, but having contingency plans in place can seriously benefit your project’s performance.
Poor Communication
What is the main thing that takes a project from start to finish? The answer: the team.
Every construction project has a lot of different people with different opinions, objectives, and motivations. As they work together, they need to find common ground to achieve their project goals.
But when people on the team can’t communicate properly, projects can get derailed. For example, subcontractors can’t start their tasks if they don’t know when they’ll be needed on the construction site.
Small problems can quickly snowball if members of the project team don’t communicate effectively. With large teams, effective communication is even more critical.
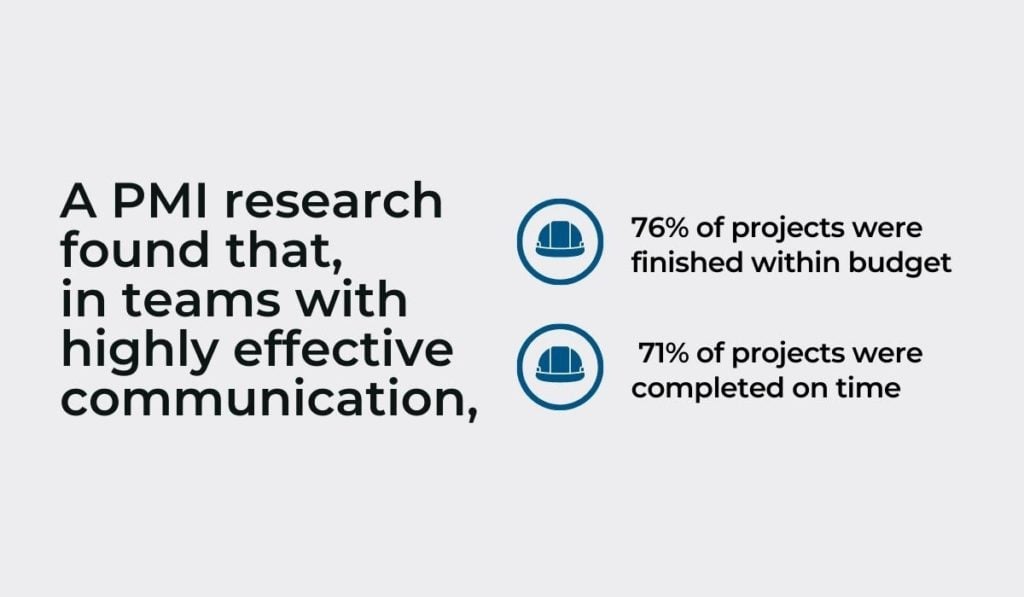
In fact, research conducted by the Project Management Institute (PMI) showed that, in teams with highly effective communication, 76% of projects were finished within budget, and 71% were completed on time.
In contrast, poor communication often leads to costly rework, schedule conflicts, and disputes.
Project status and feedback are the lifeblood of every project. Only by fostering open communication, can you transform a project from a destined failure to success.
Inadequate Productivity Levels
Walking through most major world capitals, you might think that the building has never been more productive. But you’d also be wrong.
According to research, the construction industry has been struggling with productivity for decades. Not just in the last ten years, but since 1945.
Other industries, like retail and agriculture, have seen tremendous jumps in productivity since then, reaching annual growth of 3.6%, while construction averaged only 1%.
What prevents construction from increasing its productivity?
There are various reasons, and they’re not new. The industry has been aware of them for decades, but most industry players lack the incentive to change the status quo.
The most common factors seem to be:
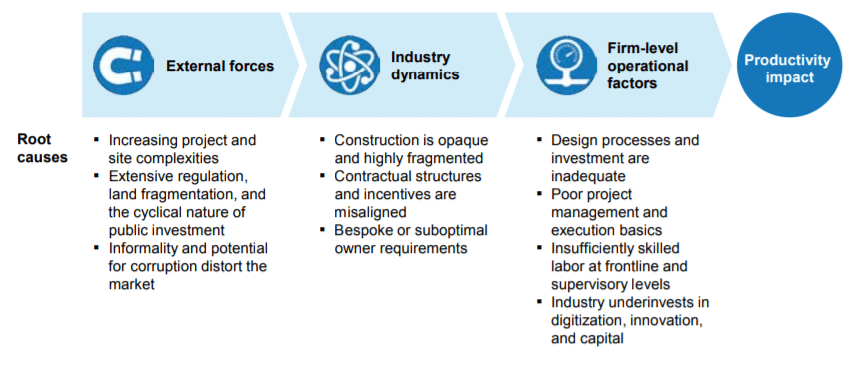
This underperformance is troubling if you consider that the construction industry contributes to 24% of the global GDP. Simply boosting productivity levels could solve so many of the world’s infrastructure and housing problems.
Yet, the industry is still not moving fast enough.
Safety Issues
Did you know that, according to the Commercial Construction Index we’ve quoted earlier, almost 64% of contractors regard worker safety as a top concern for the construction industry?
This is not without reason. For years, the construction industry has led in the number of deaths on the job site, with the number of nonfatal injuries remaining in the hundreds of thousands year after year.
This is further confirmed by the US Bureau of Labor Statistics Census of Fatal Occupational Injuries. They have reported a 6% increase in the number of deaths in the construction industry (1,066 in 2019, the highest number since 2007).
2015 | 2016 | 2017 | 2018 | 2019 | |
---|---|---|---|---|---|
Construction fatalities | 924 | 970 | 965 | 1 003 | 1 066 |
Supervisors and extraction workers | 123 | 134 | 121 | 144 | 136 |
Construction trades workers | 694 | 736 | 747 | 731 | 809 |
Extraction workers | 45 | 41 | 41 | 64 | 50 |
So, it’s no wonder that contractors are worried! But can something be done?
Injuries and deaths tend to happen because of a lack of training, safety processes, and equipment non-compliance. So, when you implement safe working practices, you protect your workers and even contribute to their productivity.
But worker safety is not just mandatory to keep the companies’ productivity rates. There are also legal reasons too.
Companies that fail to provide safety training and procedures can face strict punishments. Those can be in the form of financial penalties but also community service or jail time.
Therefore, ongoing training with a focus on safety should keep construction companies more productive but also increase their reputation and help attract new talent.
Companies that show they care about their worker’s safety can easily solve numerous problems at once.
Technology Adoption
Countless surveys have stated that the construction industry is very slow at adopting new technologies. What’s worse is that low technology adoption is the leading cause of poor project performance and low productivity.
Some recent research has shown that only 10% of companies have a dedicated budget to implement new technology for their business. These include BIM and software applications to gather data and drones and robots to increase efficiency.
What stops most companies from embracing technology?
According to the research we’ve quoted, most contractors believe that ease of use and lower costs are the main reasons for software adoption. Another reason is a verifiable return on investment.
Basically, they want to know if the investment will be worth it, so they’re very cautious about making suggestions to decision-makers.
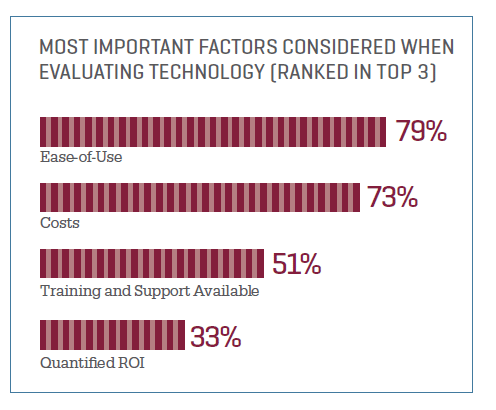
But there’s good news. As construction work becomes more complex, construction companies are starting to transform how they approach their work.
Data-driven decision-making is becoming more important for contractors, which pulls numerous benefits.
Adopting cloud-based solutions helped companies improve the allocation of labor and materials, safety measures, and recruitment processes. For example, when companies use tool tracking software, it’s easier to assess the status of their equipment and maintain it.
In spite of this, one-third of contractors still rely on paper forms or spreadsheets.
Even though digitalization in the construction industry seems to be on the rise, there’s a lot of room for improvement.
Sustainability Concerns
There is increased pressure on the construction industry to comply with new environmental regulations and expectations. And it’s not unjustified.
Large amounts of CO2 are generated every year from different construction operations. Extraction, transportation, installation, and construction waste disposal contributed to 39% of global CO2 emissions.
In addition, the industry uses almost 30% of global raw materials and generates 30-40% of solid waste.
In summary, the construction industry is one of the biggest pollutants in the world.
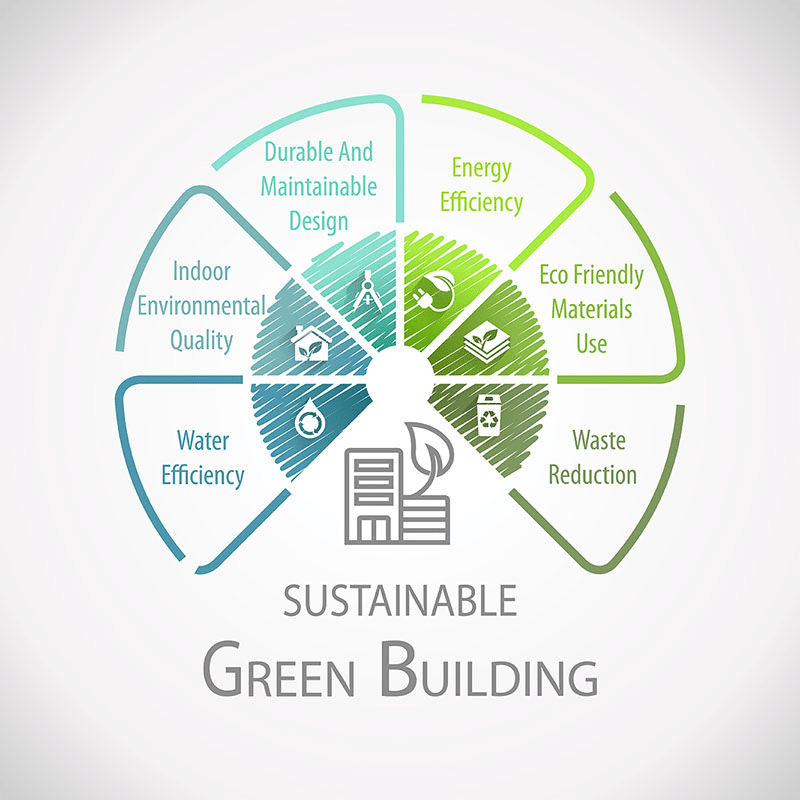
What does this mean for the construction industry?
First of all, implementing new construction materials will have the biggest impact. The new materials should be renewable and recyclable but also increase energy efficiency.
Such sustainable materials might replace the demand for steel and other materials, but they could also add costs, at least early on.
Second, a new approach to planning and design will face more traditional companies with a sharp learning curve. The industry, on the whole, is accustomed to managing its projects in specific ways, and many are not prepared for dramatic changes.
Yet, most construction companies will have no choice but to get on with the times. This is because countries like the UK are already making numerous plans to reach net-zero carbon emissions by 2050.
In fact, there’s been a demand from the UK Government for large construction companies to make climate-related reports by 2022.
In the end, sustainable construction is the future, so construction companies need to adapt as soon as possible.
Conclusion
Looking at this list, the future of the construction industry doesn’t seem bright. Yet, the industry has managed to survive numerous recessions and crises despite these challenges.
However, while the industry might be resilient, how individual companies handle these problems is an entirely different matter.
You might be looking forward to rising demands for sustainable housing and infrastructure, which could keep you employed for the foreseeable future.
But don’t overlook the challenges that are in front of you. Not being prepared is what breaks most companies.
The first step is knowing which challenges you’re facing. Then you can find adequate solutions to soften their blow and prepare yourself for growth and increased project opportunities.