What if we told you there was one change you can implement to completely transform the way you handle projects?
It might sound too good to be true, but it’s really not.
This simple change that will help you upgrade your operations tremendously is using construction checklists.
These enable you and your team to stay on top of the project and complete activities one by one, while leaving a written record of them for future reference and analysis.
Wouldn’t that help you immensely?
Let’s take a closer look at what these checklists are, why you should use them, and how to create them for your construction company.
In this article...
What Is a Construction Checklist
A construction checklist is a set of tasks you need to perform as part of your construction project, or items you should check before marking a specific activity as complete.
Let’s say you want to determine whether a tool is safe for use. In that case, your checklist will state what you should check on the tool before deeming it as such.
When the tool passes this inspection, you can use it safely. If it doesn’t, you should report to the supervisor or directly to the maintenance staff as using such a tool can be dangerous.
Because of its usefulness, there is a checklist for different parts of the construction process. The most common ones are the preconstruction checklist, equipment checklist, and quality checklist.
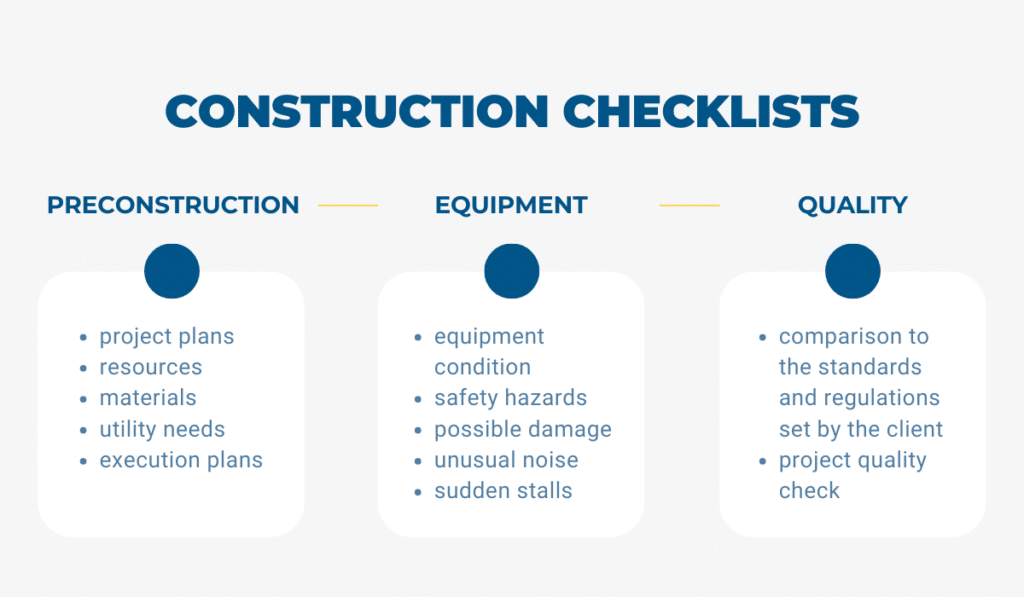
The preconstruction checklist helps you determine whether you have all the resources you need to begin the construction project in the first place. It should include the project plans, materials, utility needs, and execution plan, among others.
If you can’t tick all the items off the preconstruction checklist, don’t start working on the project. It’s a sign that you don’t have everything you need for it to be a success.
While preconstruction lists deal with the plans, materials, and resources required to finish a particular project, the equipment checklists deal with the machinery’s condition.
These are actually maintenance checklists, meaning they list aspects of the equipment you should inspect before using it, much like in our first example with the tool.
Such lists are helpful in the construction world because of all the safety concerns related to this industry. After all, approximately a hundred construction workers die at work every week, so safety needs to be a top priority.
Once you know that your equipment is safe to use, you can also check the work standard using quality checklists. They are meant to keep you on track to delivering a finished product that meets the standards and guidelines set by the client.
These checklists should clearly state what the client wants from the finished product so you can compare your work to it.
The point of any kind of construction checklist is for you to check whether your work meets previously set standards.
Why You Should Use a Construction Checklist
Using construction checklists helps you be more productive, safe, and uniform in your work, and measure your results.
It sounds like a huge promise, but getting there is relatively easy once you have your checklists in place.
Firstly, the maintenance checklists help your team stay consistent during every service session or a quick check. Your team won’t miss a single step because they have the same list to follow during these inspections. Moreover, since they will always follow the same steps, their work will be uniform.
Furthermore, the level of expertise won’t matter if all employees use the same list. That way, you can get the most out of all your workers, instead of relying solely on those with the most experience. This, in turn, makes the entire team more productive.
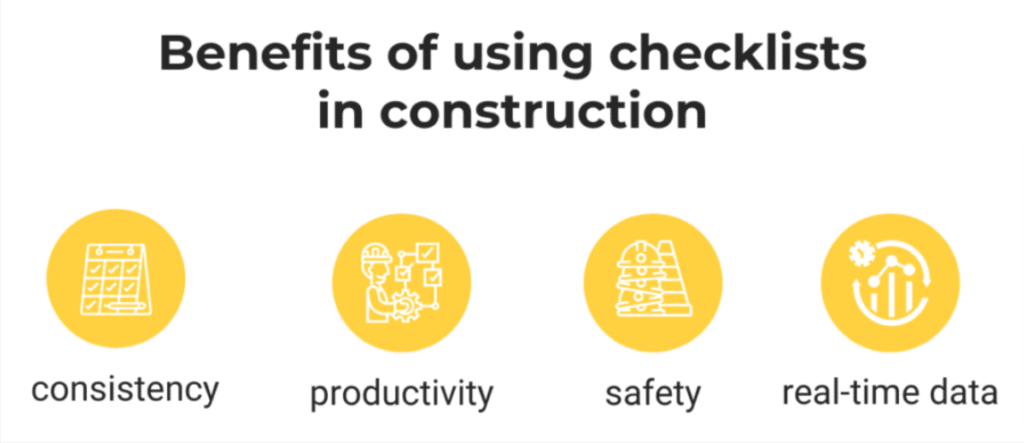
It’s not just your maintenance team that becomes more efficient—it’s the team in the field, as well. Since the equipment is safe to use and thoroughly checked, your employees can work without interruptions, as the risk of downtime is virtually eliminated.
When your workers use lists to check whether the equipment has an issue, they also ensure safety at the worksite. If employees go through the points on the list and the equipment passes each one, there are no safety hazards to using the machinery.
Conversely, if they discover an issue, your service team can immediately fix it, thus ensuring that no one operates a piece of machinery with a defect.
Checklists also give you access to real-time data about your equipment and project. With time, you’ll have enough records to be able to pull information from them and spot trends. These trends will help you improve your workflow and therefore be more efficient.
Tips for Creating a Construction Checklist
If you want to reap all the benefits we’ve discussed, it’s time to devise your own checklists.
There are many templates on the internet, and while you can use them, you should always strive to either adapt the templates to your company’s needs or create your checklists from scratch.
Otherwise, you’ll be following someone else’s guidelines, and they might not align with yours.
Here’s how you can create the perfect, detailed construction checklist.
1. Assess Your Needs
The first step towards your construction checklist is determining project requirements.
Every project is unique, so there’s no one-size-fits-all when it comes to the tasks involved.
Just think about it: how did your last project differ from the one before? Even if they were similar, there were at least a couple of divergences that made a difference.
Instead of using the same checklist for every activity, you’ll have to create one for each project or, at least, for each type of project. This is why it’s imperative to understand the project’s scope, i.e., its features and functions.
Remember, the activities and resources you put down on paper have to apply to the project at hand. Otherwise, you’re wasting your employees’ time with a checklist that does more damage than good.
So, sit down with your team and discuss what needs to be done in detail.
Once you make a note of these different aspects of your project, you will have a better understanding of everything it entails. Then, you can start thinking about what to include in a checklist and how to make it as easy to follow as possible.
During this stage, you have to define project needs and requirements to go forward with checklist creation and implementation.
2. Break the Process Down Into Steps
The next step is analyzing and splitting a more substantial activity into smaller chunks.
Doing so might seem like a waste of time at first. You might be thinking that it’s better to have one long instruction than ten smaller ones: it’s easier to remember and focus on one thing.
After all, the results will be the same, so what’s the difference?
Melissa Gratias, a workplace productivity coach, explains that breaking down tasks makes your team more effective. She says:
“ it helps us to see large tasks as more approachable and doable, and reduces our propensity to procrastinate or defer tasks, because we simply don’t know where to begin.”
And this makes sense, doesn’t it?
Seeing that you have a complex construction project task ahead of you can be disheartening as it takes longer to achieve. And if this one task entails many different aspects in itself, it can feel neverending.
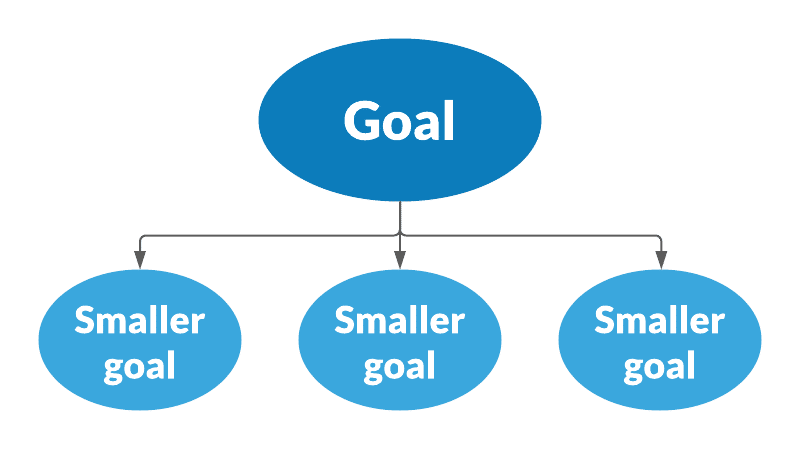
However, defining it as a list of smaller, more manageable tasks from the outset will help your team feel more productive. Whenever they complete an activity, they’ll feel the satisfaction that comes with accomplishing a goal, which will spur them on further.
That way, setting ten smaller goals instead of one larger one gives your workers the chance to get ten things done in the same, if not shorter, timespan.
So, when you create a checklist, don’t forget to break down activities into smaller ones.
3. Set Deadlines
When completing tasks, your workers should have a clear understanding of how much time they have for each one from the start.
Otherwise, you risk delays, which can cost you up to 20% of the project’s original value.
To avoid these additional costs, you should determine how long it takes to complete each task with precision. This estimation can serve as a deadline for your workers.

While deadlines are often dreaded, they help you boost productivity, according to Parkinson’s law. This law states that “work expands so as to fill the time which is available for its completion.”
In other words, you can get people to do more by giving them less time to do it. Otherwise, take their time waiting for the deadline to approach, even if they could realistically finish their task faster.
This happens because people are adaptable. When they can estimate how long it takes to complete a particular step, it’s more likely your team will finish the work in the nick of time rather than sooner.
In other words, if they receive a five-day deadline for a task that they could easily be done within only three days, they’ll still wait until the fifth day to complete it.
Therefore, giving your team a tighter, although still realistic, timeframe from the start will make them more productive as they will adapt to adhere to that deadline.
4. Assign Responsibility
Every checklist item has to have an assignee, a person in charge of the task at hand, who also communicates the results to the management.
Without this, your team will be like a ship without a captain: they’ll each do what they do best, and some will inevitably end up doing a lot more work than others. Consequently, a part of your team will experience burnout, while the other will feel insufficiently challenged at work.
So, it’s in your best interest to assign work responsibilities to your team in a way that ensures that everyone does something they are good at, while not taking on significantly more work than others.
Julie Morgenstern, a productivity expert, stresses the importance of fair work distribution:
If you overwork your high performers, you will lose them because they start to resent the fact that they’re doing more.
On the other hand, if you’re not giving enough work to the slow workers, you’ll make them lose interest in the job, while also denying them the opportunity to improve.
Therefore, when deciding on responsibilities, take the following into account:
- the worker’s experience
- the worker’s speed
- the difficulty of the task
- the employee’s current workload
At the end of the day, it’s crucial that each employee clearly understands their assigned tasks and knows how to perform them.
5. List Tasks in the Right Order
Now that you know what to include and who to put in charge of each activity on the checklist, it’s time to decide on the correct order in which these activities should be performed.
Deciding this takes a lot of practice and experience. However, the Eisenhower Principle can come in handy here.
The former US president once stated that he has two types of problems: urgent and important. In his words,
“the urgent are not important, and the important are never urgent.”
What Eisenhower meant by this was that some of the tasks you come across will be more urgent, and as such more time-sensitive, than others. They will have to be on the top of your list.
However, they might not carry that big of importance for the project as a whole. On the other hand, the critical tasks, the ones that affect the project on a fundamental level, often won’t require such an immediate response as the urgent ones.
Nevertheless, as each carries its own set of repercussions, it’s essential to dedicate your time and attention to both types of activities.
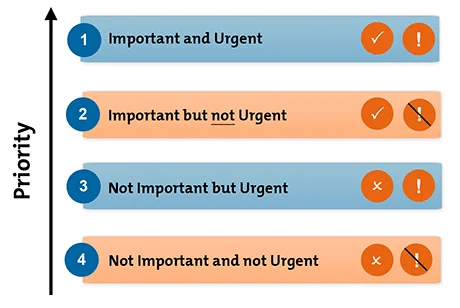
That is not to say that the two categories are mutually exclusive.
Occasionally, there will be certain tasks of great importance for your company that will also require you to deal with them as soon as possible.
The top of your list should always consist of tasks that are both important and urgent.
Without addressing them, you can’t move further down the checklists.
Next, your focus should be on the tasks that matter but are not that urgent. The things that affect the project greatly have to be finished in a timely manner for the project to succeed.
Only then can you worry about the tasks requiring immediate attention but not carrying much importance. Finally, handle the tasks that are neither important nor urgent.
6. Keep It Digital
Once you’ve compiled your checklist, It’s time to start thinking about the best way to save, use, and store your checklists.
The answer is to go digital.
While it may take you a while to implement technology and transfer all your checklists to the cloud, it will pay off.
You’ll get to centralize your data, which helps you make more informed decisions. All the checklists will be saved in the same place, allowing for easy access.
Your maintenance team will then have access to previous maintenance sessions; your project managers will be able to go over project checklists, which will help them spot problem areas and introduce improvements.
The bottom line is, with a digital solution, your employees will easily find the data they need.
On top of this, the risk of losing data from a digital checklist is minimal compared to the alternatives, as you can always check the review history and undo an accidental deleting.
It’s less feasible to undo an error in an Excel spreadsheet if someone’s already used it after you’ve made a mistake, and you can’t always protect your paper lists from getting ripped, wet, or thrown away.
If that’s not incentive enough, maybe savings will be. McKinsey’s research shows that going digital reduces construction companies’ spending by 4-6% while increasing their productivity by 14-15%.
Why not make the most out of it?
Conclusion
Creating construction checklists will help you stay on track with your project while making your team more productive in the process.
It may take some time to perfect your checklist and make sure it covers all the necessary details, but it will be worth it in the end.
What you can expect of such checklists is to get data that helps you learn, improve, and remain consistent and uniform in all projects.