Key Takeaways:
- Check-in/out software boosts efficiency and prevents asset loss.
- 81% of construction businesses use mobile platforms to aid their projects.
- QR code scanning simplifies and speeds up check-in/out processes.
- Real-time GPS tracking increases asset recovery rates significantly.
Struggling to keep track of your company’s tools and dealing with asset loss or inefficiencies?
Managing various assets across locations is tough enough, but outdated methods just multiply the headaches.
That’s where check-in/check-out software comes in.
In this full guide, we will explore why manual asset tracking is a thing of the past, and how these digital solutions can bring order and efficiency to your operations.
First, let’s get a clear picture of how check-in/check-out software functions.
In this article...
How Does Check-In/Check-Out Software Work?
In the simplest terms, check-in/check-out systems track when tools and equipment are taken out of storage and used, and when they’re available again.
But most modern systems have more useful features we’ll talk about later on, and a prime example is our check-in/check-out and asset tracking software, GoCodes Asset Tracking.
For now, take a look at the image below to see a typical workflow with this type of software.
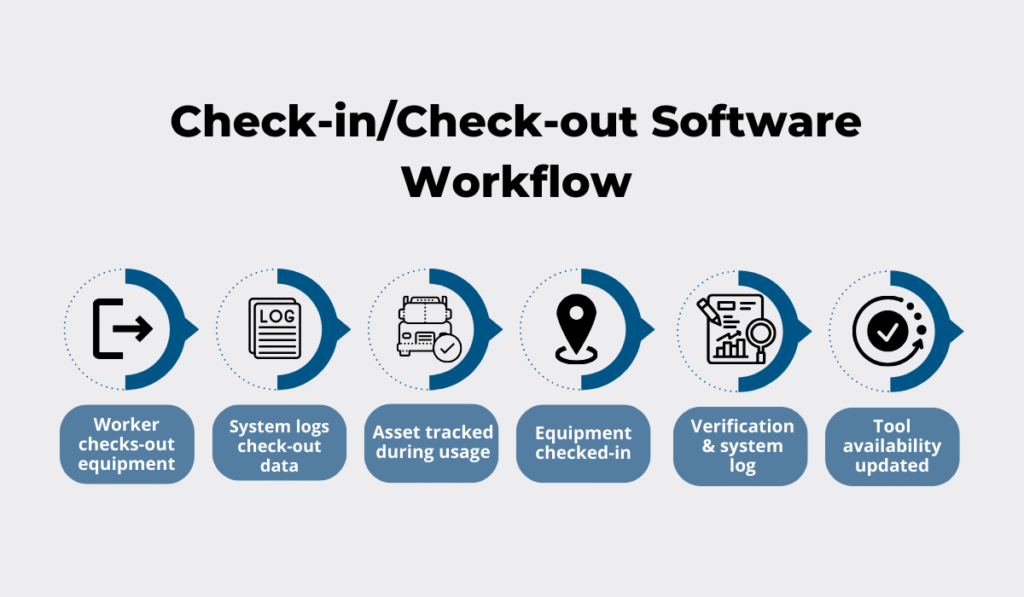
Source: GoCodes Asset Tracking
The process begins when an employee checks out a piece of equipment to use in the field.
With GoCodes Asset Tracking and our custom QR trackers, this can be done in under 5 seconds.
The system then logs key check-out data, including:
- Date
- Time
- Location
- The employee who checked out the tool
- Any manually-entered notes
Plus, the system updates the asset’s availability status in real time.
While many systems stop at this point, more advanced systems can also track other key metrics like vehicle speed and engine hours.
This way you always know where an asset is and how it’s being used.
When the worker is done, they simply check the tool back in.
The system verifies that everything is in order, logs key metrics (like which employee checked in the asset and its usage duration), and then updates the asset’s status.
This is how it looks like in GoCodes Asset Tracking.
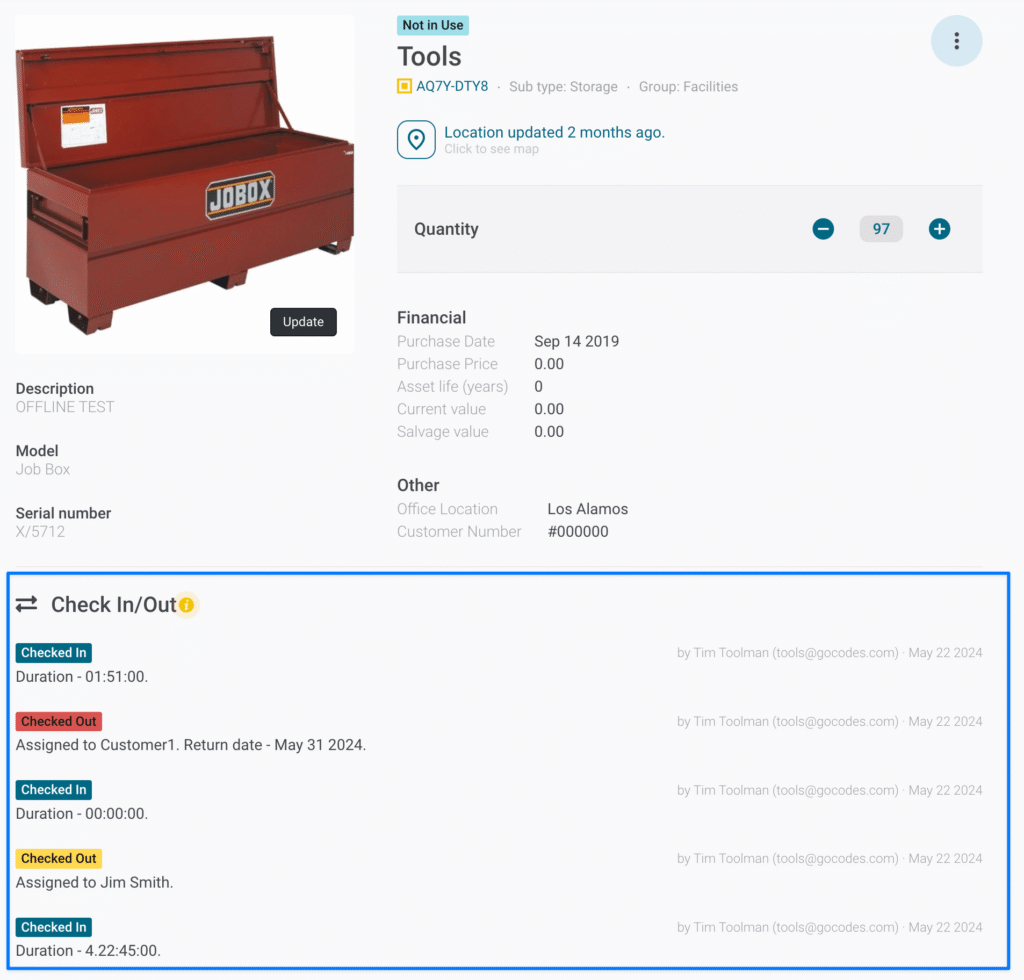
Source: GoCodes Asset Tracking
Once checked in, the tool is instantly marked as available in the system, ready to be used again.
Ultimately, check-in/check-out software replace the manual tool tracking process and provide the added benefits of real-time visibility and more efficiency.
Features to Look For
What we’ve just described is a general overview of check-in/check-out software.
Most tools will have additional capabilities that can add extra value to your operations.
Out of these features, some stand out as particularly important.
Let’s explore three key ones to look for when choosing a system.
Mobile Accessibility
Check-in/check-out systems work best when they can be used on the go, and mobile accessibility is key for this to function effectively.
After all, we want to make it as simple as possible for field teams to check tools in or out wherever they are, eliminating the need to return to a central location or carry a laptop to access a desktop app.
This is especially useful in the construction industry.
In fact, KPMG data shows that 81% of construction organizations have implemented mobile platforms either in a few or across all their projects.
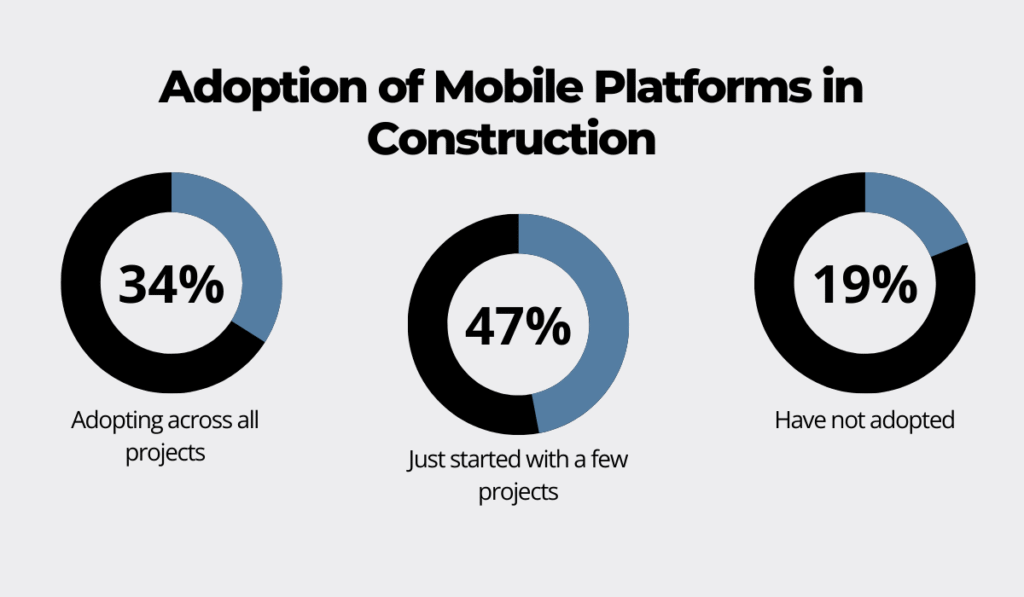
Illustration: GoCodes Asset Tracking / Data: KPMG
That means that most businesses are already capitalizing on the speed and convenience that mobile tools offer.
However, not every mobile check-in/out tool will do.
The software you choose should be specifically optimized for mobile use.
This means all app features should work on either desktop, mobile, or tablet devices.
On top of that, the software should offer responsive design, so the interface adapts to different screen sizes and orientations.
As seen below, menu items, images, and all functionalities should be usable and look right even on a smaller mobile screen.
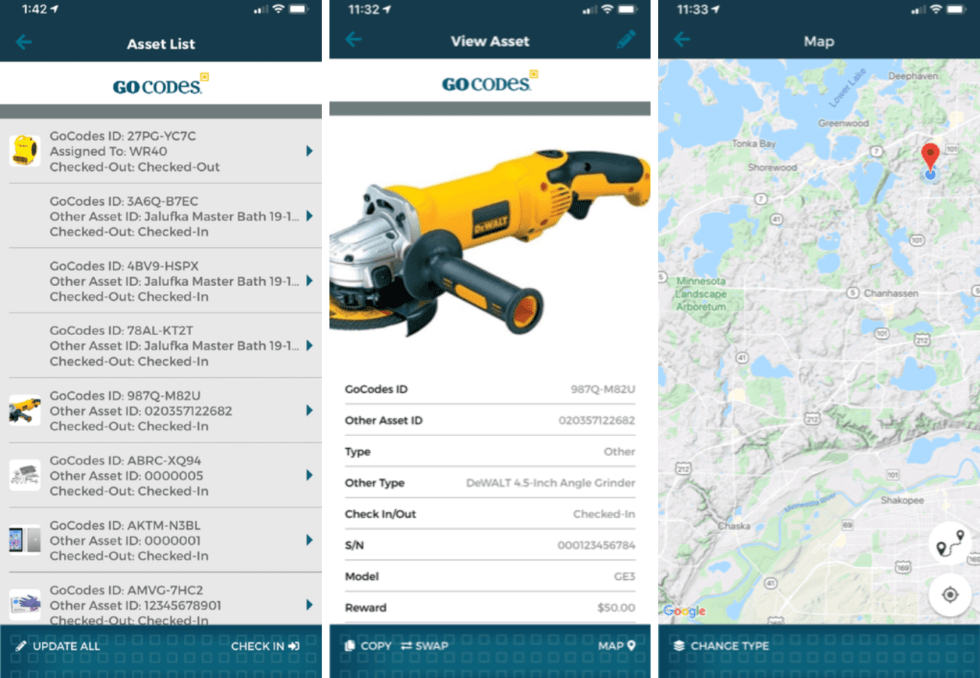
Source: GoCodes Asset Tracking
Additionally, buttons and interactive elements should be large enough for easy tapping, and the layout should be intuitive for users navigating on a touchscreen.
So, make sure that the check-in/check-out tool you select prioritizes mobile accessibility, as your team’s productivity will depend heavily on this feature.
QR Code Scanning
The second essential feature is how the system handles QR code scanning.
Having this process integrated effectively is crucial to making the check-in/out process efficient and error-free.
We focus on QR codes specifically because they offer greater benefits than typical barcodes.
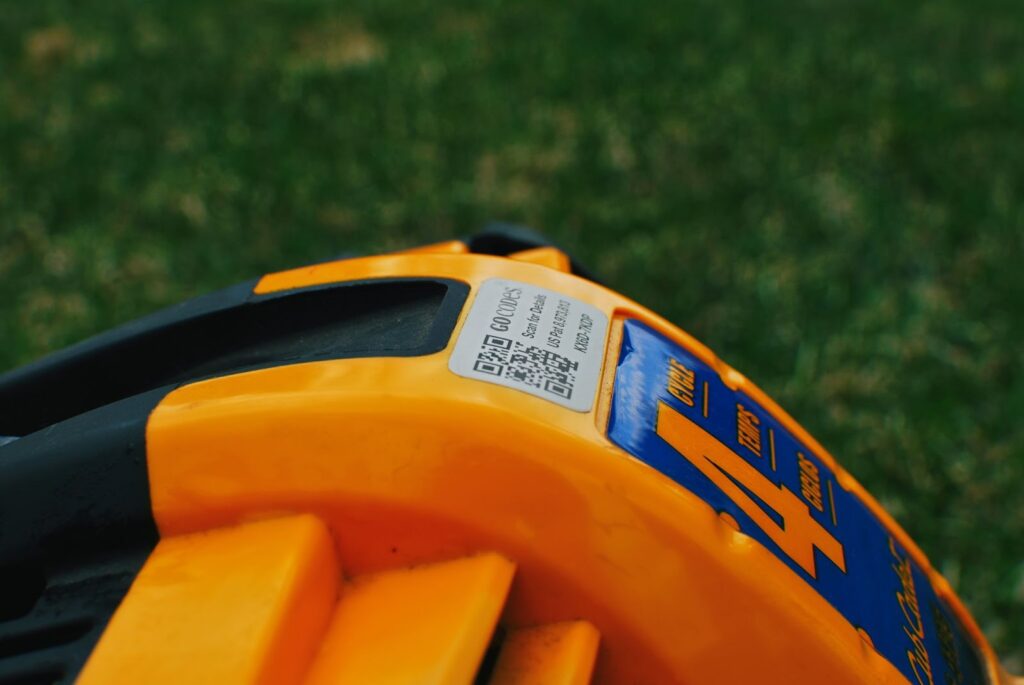
Source: GoCodes Asset Tracking
In fact, a standard QR tag has the following characteristics:
- Stores data both horizontally and vertically
- Stores a maximum of 7089 numeric characters
- Stores up to 4269 alphanumeric characters
Compare that to barcodes, which can only store data horizontally and up to 25 alphanumeric characters.
This limited capacity restricts the amount of information that can be encoded, whereas QR codes can hold significantly more data, including website URLs, essential product details, and much more.
This makes them far more versatile for asset tracking.
So, a great check-in/check-out system should allow users to quickly scan these codes with the camera on a mobile device or tablet, as shown below.
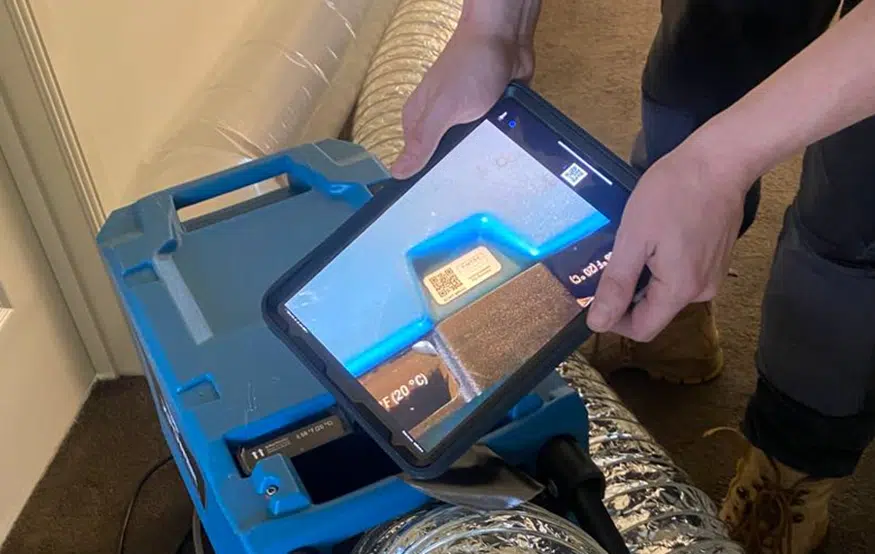
Source: GoCodes Asset Tracking
There should be no need for additional scanner equipment, and the entire process should be done almost instantly.
The system should then access and seamlessly display all the data stored in the code.
With that, you essentially eliminate tedious manual asset check-in/out processes, and minimize the risk of equipment being incorrectly tracked and managed.
Real-Time Location Tracking
While location tracking might seem like an unnecessary feature if you’re looking for just a simple check-in/check-out tool, don’t underestimate its benefits.
Take BLE (Bluetooth Low Energy) beacons, for example.
These small, battery-powered devices, shown in the image below, can be attached to assets and transmit signals that are picked up by smartphones or gateways.
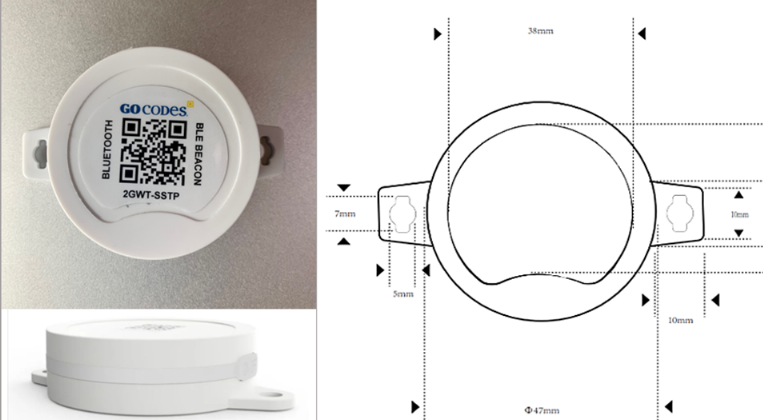
Source: GoCodes Asset Tracking
This enables the check-in/check-out system to determine the proximity of an asset to a specific location.
For example, you could set up zones within a warehouse and receive alerts when a tool enters or leaves a designated area.
The data tracked by BLE beacons includes:
- Identity of the beacon/asset
- Distance of the beacon from the smartphone
- Environmental information like temperature and acceleration
Then there’s GPS tracking, which goes even further.
Instead of tracking proximity within a limited range like BLE beacons, GPS uses satellites to pinpoint the precise location of an asset anywhere in the world.
With most modern software, you can know exactly where your tools are on a detailed map with satellite view.
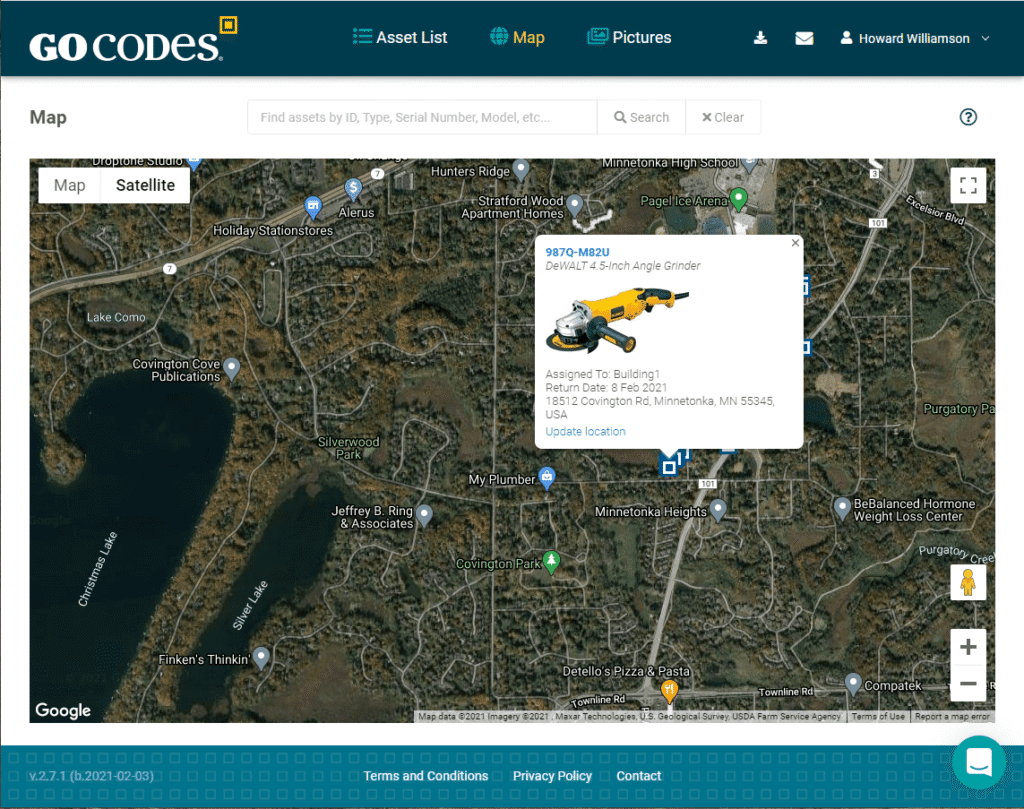
Source: GoCodes Asset Tracking
Real-time tracking is particularly useful when you need to quickly locate a piece of equipment, such as if it goes missing from a job site.
It helps save valuable time and can prevent costly project delays.
This is especially useful for large, multi-site operations, where tracking assets across different locations can be challenging.
Benefits of Check-In/Check-Out Software
Check-in/check-out systems come with a wide range of benefits.
These benefits are especially important in construction and heavy equipment industries, where smooth workflows can mean the difference between staying on schedule and costly delays.
In the following sections, we will look at how these tools drive greater efficiency, reduce asset losses, and streamline equipment maintenance.
Saves Time on the Job Site
A significant advantage of using a digital solution for asset tracking is the time savings it offers in managing and tracking equipment.
Oded Ran, CEO & Co-founder of Clue, a construction management software company, paints a very common picture of what these tools help avoid.
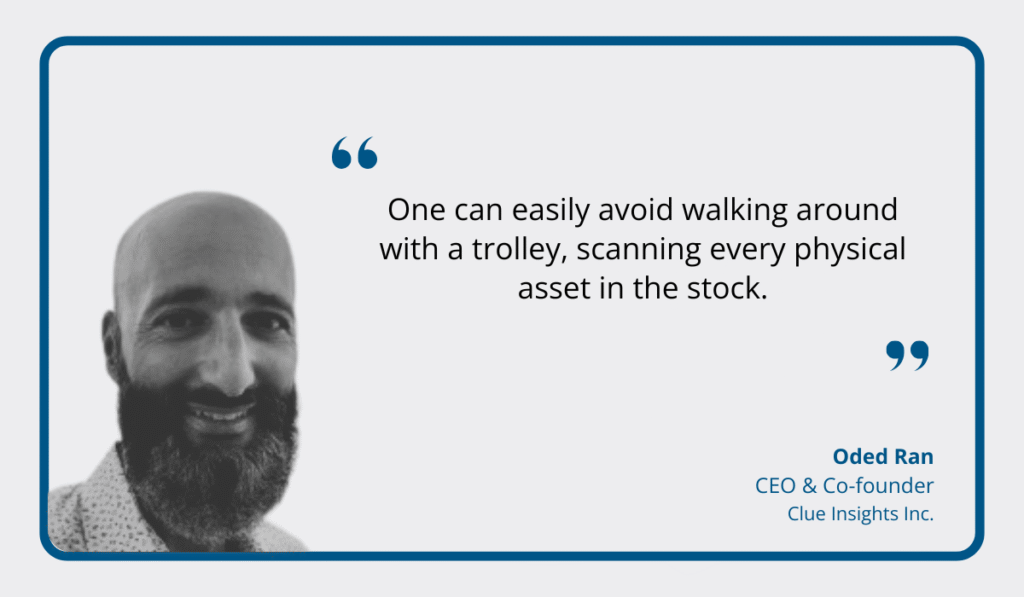
Illustration: GoCodes Asset Tracking / Quote: Clue
If workers waste time searching for missing tools or asking around to find out who last used a particular piece of equipment, productivity suffers.
Same goes for manually logging information on paper.
Compare that with a single app that can be used to identify the location or status of equipment instantly.
This eliminates wasted time spent searching or making inquiries, allowing workers to focus on their tasks.
With the right system, you can even have a clean daily agenda list, as shown below.
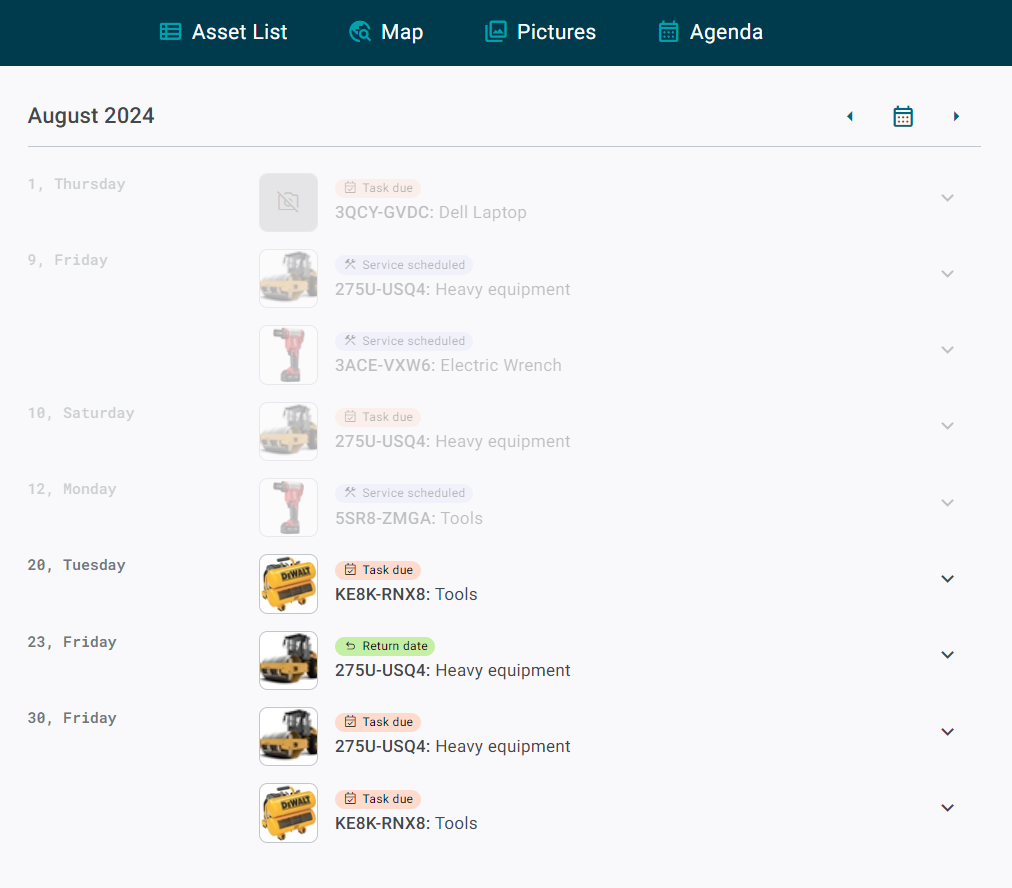
Source: GoCodes Asset Tracking
With this list, you’ll have a full overview of what equipment is checked in and out, whether a tool is scheduled for a task due, or is scheduled to be returned.
Plus, as we’ll discuss shortly, you can even use the same system to view scheduled service maintenance.
In short, a digital check-in/check-out system streamlines equipment management, freeing up valuable time and boosting overall efficiency on the job site.
Reduces Asset Loss
Asset loss is a big concern in the construction industry, and is one of the key areas where check-in/check-out solutions can help.
Data from the National Equipment Register (now Verisk) estimates that the value of equipment stolen annually in the US is up to a billion dollars.
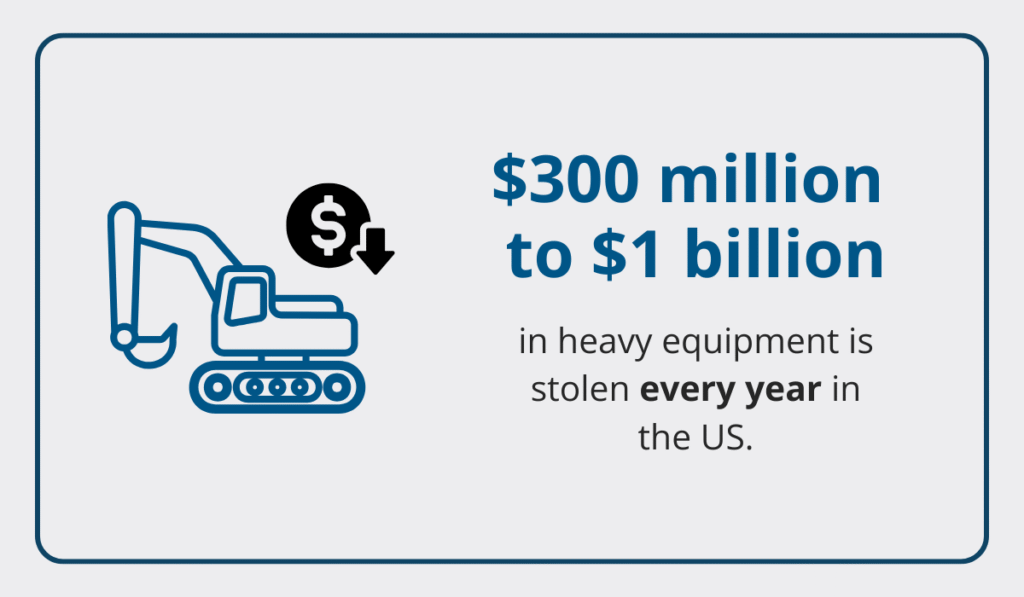
Illustration: GoCodes Asset Tracking / Data: NER
What’s more, multiple online sources claim that only 10 to 25% of stolen equipment is ever recovered.
These are concerning numbers, and one effective way to mitigate losses is by always knowing where your assets are.
In this case, even the most basic check-in/out tools can help.
For example, if a piece of equipment isn’t checked in on time, your software will provide visibility into this, allowing you to take immediate action.
You’ll also have information on who last checked out the asset, which significantly increases accountability and deters theft and misuse.
When real-time GPS tracking is available, you can pinpoint the exact location of missing equipment, dramatically improving the chances of recovery.
It’s no wonder, then, that companies around the world are capitalizing on the visibility provided by this type of software.
Take a look at the forecast from Juniper Research.
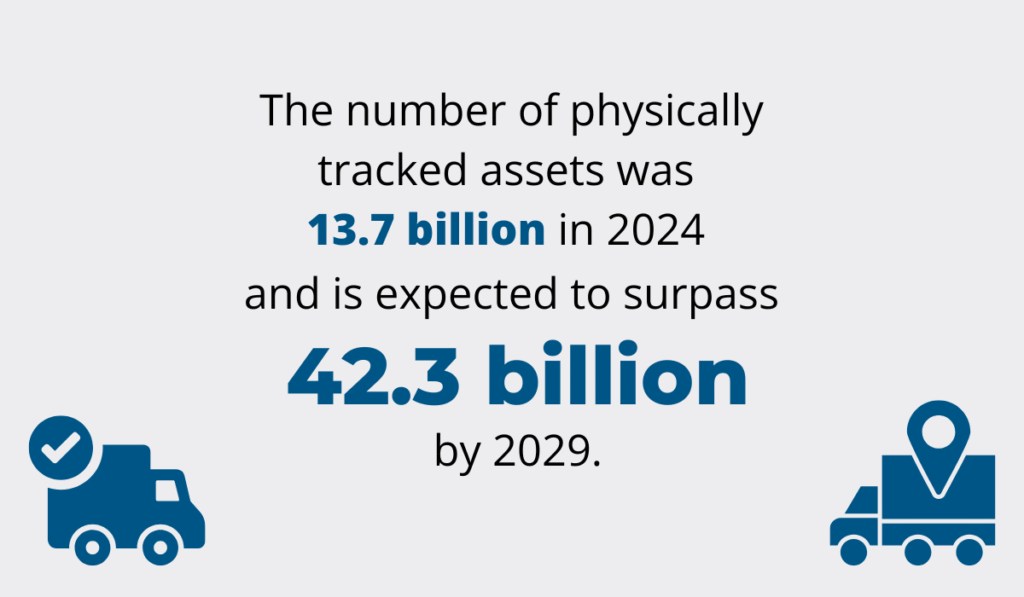
Illustration: GoCodes Asset Tracking / Data: Juniper Research
As you can see, there’s currently a substantial number of assets being tracked with software, and the entire asset tracking market is expected to growth by 208% by 2029.
In other words, as more businesses adopt these technologies, we should see a marked reduction in asset loss due to improved visibility and control over equipment.
This highlights the importance of considering this type of software for your business to protect your investments and prevent costly delays.
Streamlines Asset Maintenance
The added visibility from check-in/check-out software extends beyond simple tracking and offers significant benefits for maintenance teams as well.
That’s because this type of software allows anyone to instantly access the status and condition of any asset.
Consider the following image, showing just some of the data that can be accessed for a piece of equipment—in this case, a DeWalt compressor.
Here, you can see the “Asset Service” section, which shows when the compressor was last serviced, along with any notes or issues recorded during that service.
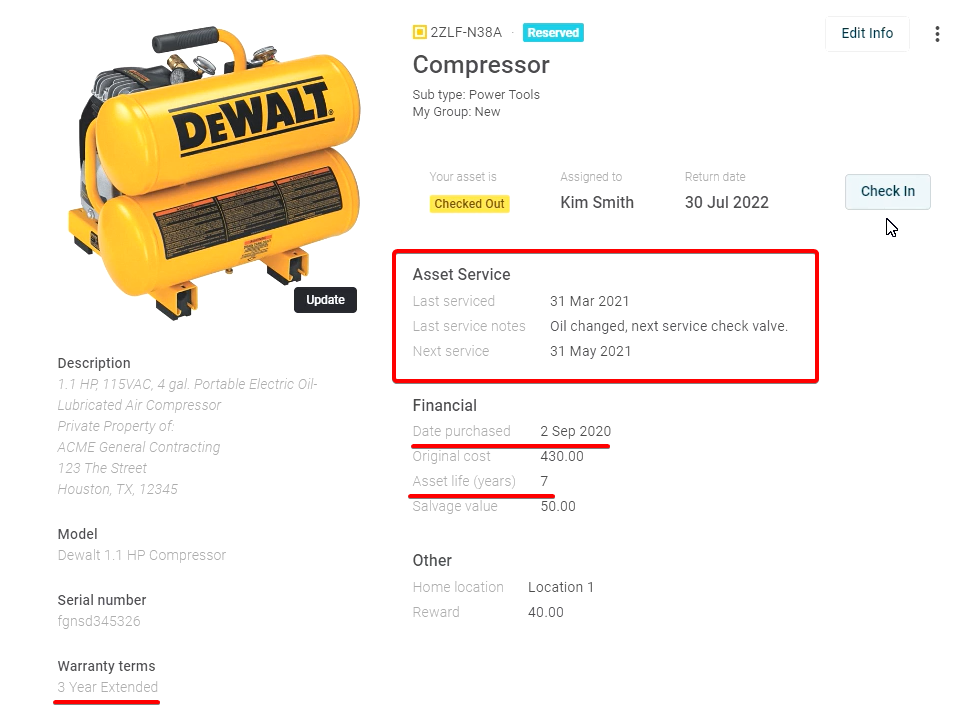
Source: GoCodes Asset Tracking
Additionally, the next scheduled service is clearly visible, enabling proactive maintenance and helping to avoid costly downtime.
What’s great about digital systems is that they can provide even more data, such as:
- The purchase date
- Estimated asset life
- Warranty terms
- Other helpful notes
This information empowers owners and maintenance teams to make informed decisions about repairs, replacements, and preventative maintenance schedules, optimizing the asset lifecycle.
Finally, with tools like GoCodes Asset Tracking, you can even assign work orders to employees and maintenance crews, such as regular maintenance tasks or specific service checks.
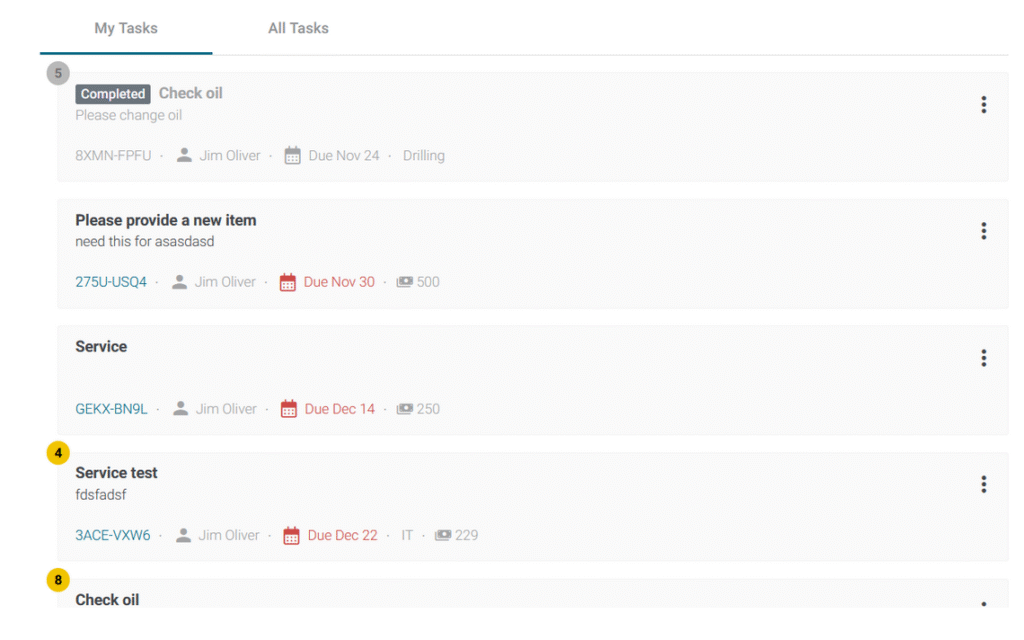
Source: GoCodes Asset Tracking
By consolidating everything in one place and streamlining task creation and assignment, communication improves, accountability is enhanced, and maintenance tasks are completed more efficiently.
This leads to better-maintained equipment, reduced downtime, and ultimately, cost savings.
Conclusion
And that sums up our guide to asset check-in/check-out software.
We’ve covered what these systems are, and how they can improve your asset management processes, prevent asset loss, and even aid in better equipment maintenance.
Plus, we’ve highlighted three essential functionalities that every great check-in/check-out tool should have.
Hopefully, you’re now better equipped to choose the right solution for your organization.
So, consider your specific needs, choose the right system, and take control of your assets.