Today, advanced asset tracking technologies provide construction companies with more comprehensive insights about their vehicles, heavy machinery, equipment, and tools than ever before.
When the power of software is conjoined with trackers, tags, and sensors on your equipment, you can track the GPS location, usage, operating conditions, performance, costs, and much more about your construction assets.
Moreover, asset tracking solutions allow you to analyze all this data, gain invaluable insights, and use them to improve your operations, increase productivity, and reduce costs.
However, in the sea of information, sometimes it’s hard to see specific ways in which decision-makers can leverage asset tracking data to achieve the most significant efficiency gains and cost savings for their construction business.
So, here are eight ways to do just that.
In this article...
Optimize Asset Utilization
Whatever type(s) of asset tracking you’re using or intending to use, the insights gained by looking at the data allow you to optimize the utilization of your construction assets, thus improving productivity and reducing costs.
More specifically, you can leverage this data to make better informed, data-driven business decisions.
You can figure out how to best allocate and manage your assets, from large heavy equipment to the smallest tools and precision instruments.
For example, you might own construction vehicles and heavy equipment with GPS trackers.
These trackers allow you to not only see where your valuable assets are but also collect a mountain of data about their utilization.
This data is then interpreted by an asset tracking solution, which enables contractors to track vehicles, heavy equipment, and other assets in one single platform.
These systems provide the GPS location, utilization, and maintenance data for your assets, which can bring benefits such as:
- better allocation and scheduling of equipment and tools across jobsites
- less equipment downtime
- lower maintenance and repair costs
- improved asset lifecycle management
As you can see, tracking solutions can be used to gain insights and make informed decisions to optimize the utilization of your construction assets.
It’s a good idea to try them out if you are looking for ways to reap maximum benefits from your vehicle fleet and equipment.
Hold Your Employees Accountable
Naturally, the data from asset tracking can speak volumes about the ways in which equipment and tools are used.
That data can be leveraged to hold employees accountable for the construction company’s assets.
For example, when GPS tracking and equipment sensors work together, the data collected from tracking heavy equipment and vehicles will show when, where, and how your operators and drivers are using the assets assigned to them.
In the case of construction vehicles, reviewing this data can reveal unsafe driving practices like harsh acceleration, frequent breaking, speeding, slow driving, and frequent stopping.
Then, you can take action to correct such behavior by providing instructions and training to promote safe and responsible driving practices and increase profitability through driver accountability, as discussed in an article by Construction Pros.
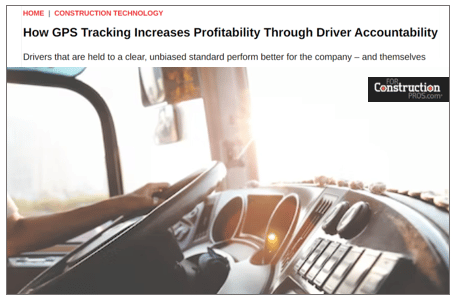
In fact, when drivers and operators know that the location, usage, and operating conditions of their vehicles and heavy equipment are being monitored, irresponsible and unproductive behaviors often go down automatically.
The same is true when dealing with theft or negligent behavior involving other smaller assets, such as hand and power tools, safety equipment, and other items.
When these assets are tracked, employees know they will be held accountable for the tools and equipment assigned to them and will therefore take better care of it.
For example, this can be easily and affordably done by attaching GPS-enabled QR code tags to your tools and equipment and scanning them into the central inventory list in your asset tracking app, such as GoCodes Asset Tracking.

GoCodes Asset Tracking allows you to establish a check-in/check-out system and scan the QR code tags with any enabled device, such as a smartphone or tablet, to check assets in and out.
This tracking system lets managers know who is using tools and equipment at any time, automatically ensuring higher worker accountability.
Whatever construction assets are tracked, the collected data can be leveraged in different ways to hold employees more accountable for the assets they’re using.
Enforce Contracts for Rented Equipment
Construction companies typically use a mix of owned and rented equipment to complete their projects, meaning they rent equipment from others, but can also rent out their equipment to others.
In either case, asset tracking data will keep both parties (owner and renter) accountable, helping ensure that the equipment is used according to the terms of the rental agreement.
For example, if the equipment should, under the rental contract, stay within a specific construction site or geographical area, GPS tracking allows you and the other party to verify compliance with such contract clauses.
Another example is building an invisible perimeter—geofence—around your jobsite, which is a feature offered by many asset-tracking software.
With it, you get alerts if a GPS-tracked asset leaves the designated area.
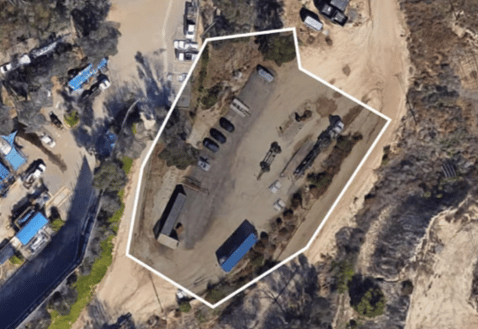
Of course, this feature and GPS tracking, in general, can be used to prevent unauthorized use or theft.
It provides a transparent record of equipment usage, which is important for insurance and regulatory/safety compliance of rental equipment.
Overall, asset tracking data can be used to keep the equipment owner and renter accountable and help you optimize the utilization of owned and rented equipment.
Avoid Client Disputes
Because asset tracking provides an accurate digital record of the location and usage of assets, construction companies can leverage data from asset tracking to avoid and resolve client disputes.
For example, Francis Plumbing & Heating were able to resolve a conflict with their client by showing them the GPS tracking report that proved the client was not overbilled, as they believed.
In the words of manager Kay Kinder, they showed the client that the truck was on-site at the time they were billed for (and even longer) and, as a result:
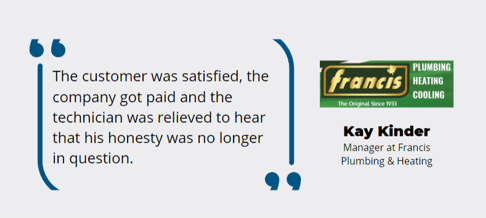
This is just one example of how asset tracking data can be used as evidence to support your arguments when dealing with a client who thinks they were wronged in some way.
Simply put, you can often leverage the asset location and usage data to find out what happened, determine who’s responsible, clear up misunderstandings, and resolve disputes with the client before they escalate.
Moreover, using tracking data can ensure more accurate job costing and billing in general, which prevents potential payment disputes down the line.
If a dispute is more serious, this same data can be used by insurance investigators, claims specialists, and lawyers on both sides to help parties reach a mutually acceptable solution in an objective and fair manner.
Overall, asset tracking solutions generate digital evidence that can be used to avoid or quickly settle client disputes.
Understand Asset Depreciation
Asset tracking data allows construction companies to gain valuable insights into the true value of their assets, enabling them to optimize asset depreciation and realize tax savings.
Depreciation represents the decline of an asset’s value over time, and the way that decline is spread over its useful life has different accounting and tax effects on your organization’s balance sheet and asset expenses in any given year.
Therefore, tracking data can be used to calculate accurate depreciation rates and better align your organization’s financial statements (with expert help, naturally) to reduce taxes.
Moreover, this data can be used to analyze the equipment lifecycle and make informed decisions about optimal asset utilization, maintenance, repair, and replacement.
In other words, to quote the Business Owner’s Playbook:
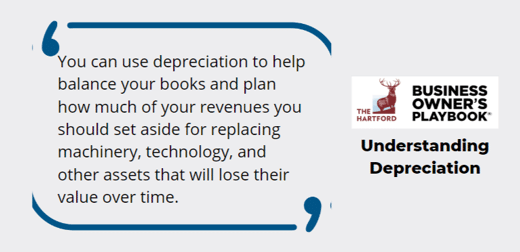
Therefore, using data to manage asset depreciation can help you improve asset procurement planning and budgeting, improve maintenance planning, and allow you to make informed decisions about asset management.
For example, tracking an asset’s loss of value over time with other factors helps you decide whether to repair or replace a piece of equipment because of wear and tear, deterioration, or obsolescence.
Overall, asset tracking data helps you understand depreciation and can be used to realize tax savings, as well as proactively manage assets to get the most out of them, both operationally and financially.
Lower Your Insurance Premiums
Given that GPS-enabled asset tracking helps construction companies prevent theft and unauthorized use, provide timely maintenance and improve driver/operator behavior, most insurance providers will take that into account and lower your insurance premiums.
Depending on the number and value of construction assets you want insured, this can quickly add up to significant savings.
Here’s why insurance companies are willing to offer discounts when your fleet is equipped with GPS trackers:
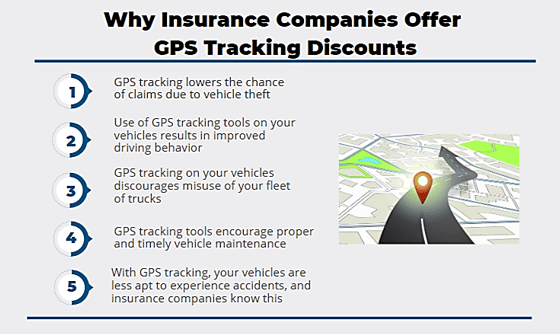
As you can see, theft prevention, better driving and operating practices, less misuse and negligence, proper maintenance, and fewer accidents are just some of the benefits that insurance providers know your GPS tracking system will provide.
Therefore, they should be asked whether they take this into account when calculating insurance premiums for the equipment.
Your business can use an asset tracking system to improve security, equipment maintenance and safety, and operating practices, and this data can be leveraged to lower your insurance premiums.
Reduce Fuel Consumption
Fuel consumption deserves special mention because of the current fuel prices and the savings that can be achieved by leveraging asset tracking data.
As we mentioned, a GPS tracking system allows construction companies to track asset locations, and, when trackers are combined with telematics solutions, managers can monitor other parameters such as fuel consumption, speed, and idle time.
The collected data can be used to devise measures to reduce fuel-wasting practices such as harsh braking and acceleration or excessive idling.
For example, construction equipment can spend a lot of time running when not in motion (idle time), with detrimental impacts on fuel consumption and engine wear, as discussed in another article by Construction Pros.
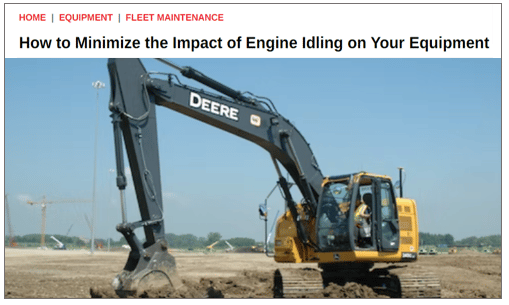
To reduce fuel consumption, construction companies can analyze asset tracking data to get insights into idle times and other wasteful practices and then take action to reduce them.
In other words, armed with asset tracking data, you’ll be ready to control fuel consumption in your construction fleet by minimizing idle time and poor driving/operating behaviors, thus generating significant fuel cost savings.
Get Fuel Tax Refunds
Although you might need professional help from an accountant or tax expert, it’s important to note you can leverage asset tracking data to get fuel tax refunds.
Simply put, gasoline and diesel fuel prices are taxed, and those funds are used for building and maintaining highways and other roads that vehicles drive on.
However, when construction companies use fuel in construction equipment that works off-road, they’re eligible for tax refunds at the federal level.
These refunds are called Fuel Tax Credit (FTC), as defined by Investopedia:
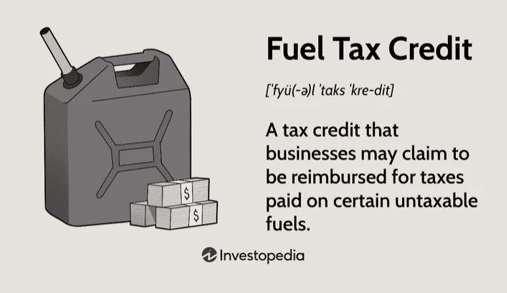
Without getting too technical, to claim the fuel tax credit, your company must provide records showing the amount of fuel used in off-road activities, the number of gallons purchased, and the supplier’s name.
And these records can be automatically created by using GPS tracking along with onboard sensors and fuel logs, meaning that asset tracking data can be leveraged to get fuel tax refunds.
Of course, this information needs to be submitted to the IRS with the tax return and needs to meet their eligibility criteria, so professional help from accountants and tax experts is usually required.
Conclusion
Finally, this is only a shortlist of how construction companies can leverage the data and insights from asset tracking to save money on equipment maintenance, insurance, fuel, and tax, achieve efficiency gains, and enhance profits.
In other words, a carefully selected combination of asset-tracking solutions can allow you to reap the benefits of optimized utilization of assets throughout their lifecycle while holding your employees and business partners accountable and avoiding client disputes.
The result is smoother operations at lower cost and higher client satisfaction.