Key Takeaways:
- Choosing the right tracking technology depends on asset mobility and work environment, required tracking precision, and budget.
- Only 37% of U.S. construction companies centralize their data, creating blind spots that hinder audits and decision-making.
- Linking tags to a centralized software reduces errors and ensures real-time visibility.
- Automated tracking tools safeguard compliance by streamlining audits and improving operational control.
The asset tracking market is booming, with several reports forecasting its value will more than double by 2030.
But as businesses rush to adopt new solutions, smart asset identification is what separates real ROI from wasted budgets.
This guide outlines five essential best practices to help you build a system that delivers lasting value.
In this article...
Selecting the Right Tracking Technology
Choosing the right tracking technology is essential for accurate and consistent asset identification.
You just need to ensure it suits your working environment and operational needs.
Pen-and-paper logs have become outdated a long time ago, but the asset tracking market is only now gaining serious momentum.
One report estimates a 14.4% CAGR, meaning the market will more than double in value over the next six years, reaching $52.81 billion by 2030.
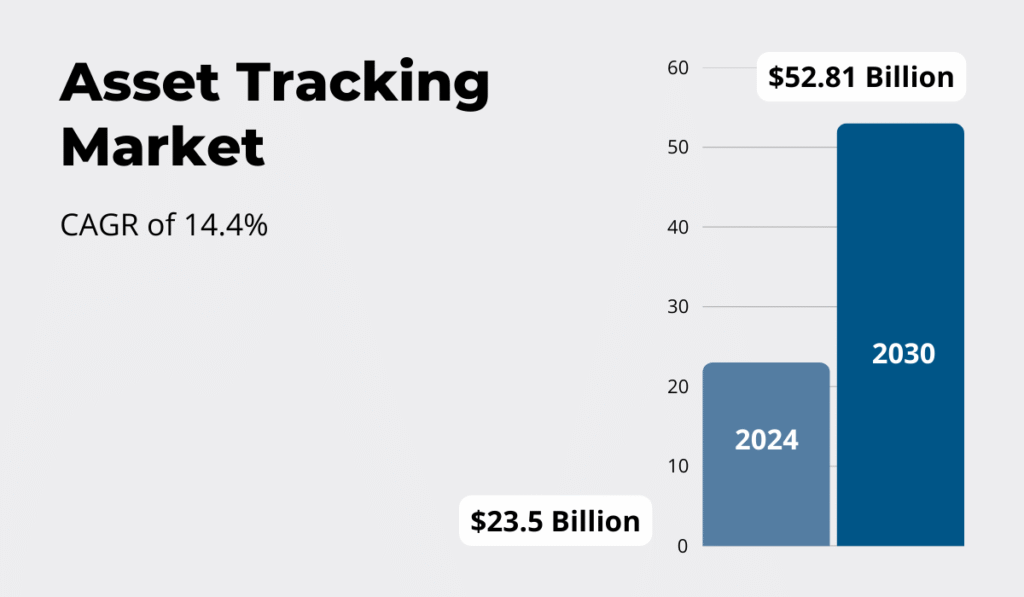
Illustration: GoCodes Asset Tracking / Data: Research and Markets
While this projection includes different tracking systems, RFID technology alone is projected to reach $41 billion by 2031, reflecting growing demand for contactless, automated solutions.
However, the best choice for your business depends entirely on your circumstances.
For example, an RFID-based asset identification system relies on radio signals, enabling out-of-sight scanning.
This means you aren’t limited by walls and similar indoor obstacles, making this technology particularly suited for warehousing, healthcare, and retail environments.
On the other hand, radio signals are prone to interference from metal and water, which can undermine RFID’s reliability on construction sites or remote field operations.
RFID also tends to be more expensive than barcodes and QR codes, which require line-of-sight but are affordable and easy to implement.
As Rachel Jia, Technical Marketing Manager at Dynamsoft, sums it up:
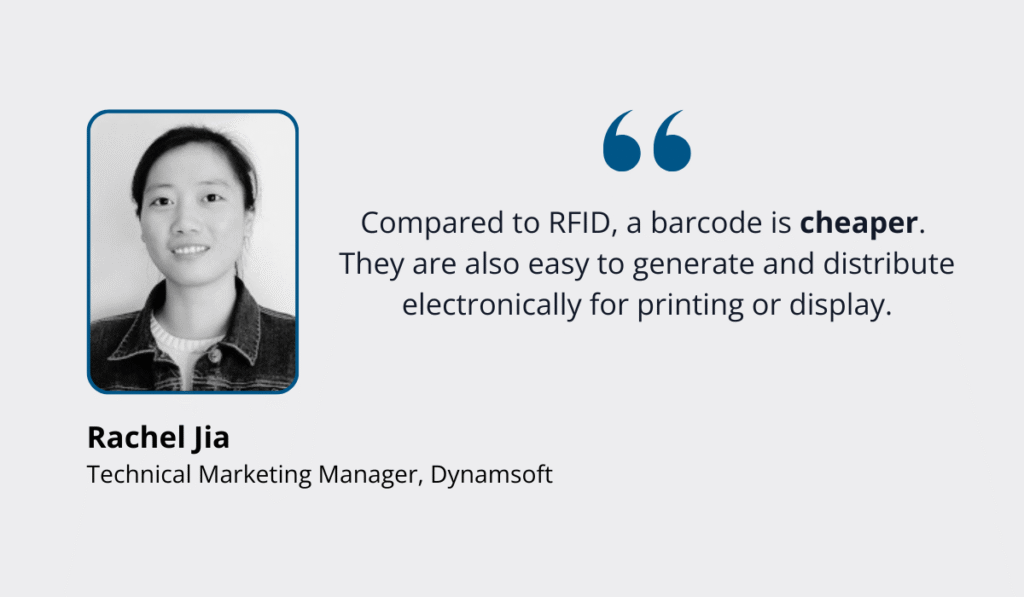
Illustration: GoCodes Asset Tracking / Quote: Camcode
So, a different method is likely to prove more cost-efficient if you don’t require advanced RFID capabilities for your particular use case.
When choosing between different tracking methods such as barcodes, QR codes, RFID, GPS, or BLE, consider the following factors:
- Asset mobility
- Tracking precision
- Environmental conditions
Here’s how these technologies compare at a glance:
Method | Asset Mobility | Environment | Precision | Cost |
---|---|---|---|---|
Barcodes | Fixed assets, inventory, small tools | Mostly indoor, possible outdoors | Very short-range, requires line of sight, limited data capacity | $ |
QR Codes | Fixed assets, inventory, small tools | Indoor/outdoor (if rugged) | Very short-range, requires line of sight, can store rich data | $ |
BLE Beacons | Mobile tools & equipment | Indoor/outdoor (if weatherproof) | Mid-range (~50m), proximity-based, no line of sight | $$ |
RFID (Passive) | Fixed assets, inventory, small tools | Indoor/sheltered outdoor | Short to mid-range (~10m), no line of sight, interference-prone | $$ |
RFID (Active) | Mobile equipment & high-value assets | Indoor/limited outdoor | Mid-range (~100m), no line of sight, can struggle in industrial outdoor settings | $$$ |
GPS Trackers | Highly mobile, outdoor assets | Outdoor only | High precision, real-time global tracking | $$$ |
Finally, make sure to assess integration capabilities and scalability for each tracking technology.
After all, the right solution won’t just meet today’s asset identification needs but grow with your business for years to come.
Creating a Naming System
There’s no effective asset identification without a carefully planned naming system.
Consistent naming conventions support faster identification and easier categorization, ensuring that key equipment is available when and where needed.
Without a clear system, crews waste valuable time hunting down tools, verifying equipment locations, or figuring out what needs servicing.
And in an industry where productivity has historically lagged behind other sectors, that’s a risk you can’t afford.
A 2018 study by Autodesk and FMI found that over one-third of construction work hours are spent on non-productive activities.
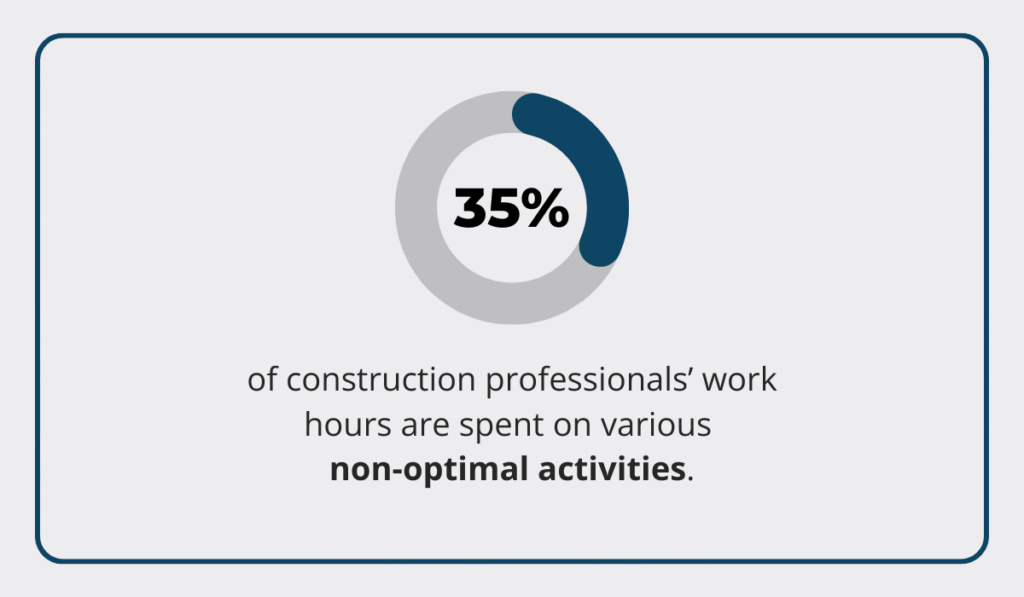
Illustration: GoCodes Asset Tracking / Data: Autodesk & FMI
This includes everything from rework and administrative delays to simply searching for information or misplaced tools.
What these activities have in common is that they pull time and focus away from essential tasks like project execution, coordination, and overall resource management.
McKinsey’s latest report confirms that this long-standing issue worsened between 2020 and 2022, with productivity declining even further.
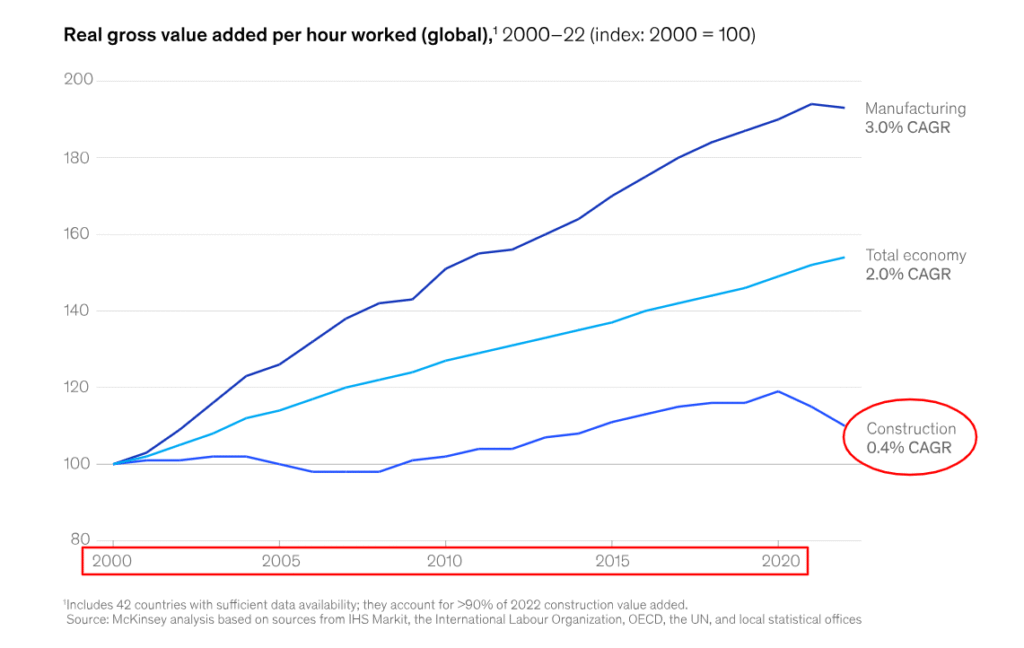
Source: McKinsey
One practical way to solve this problem is by standardizing your asset naming conventions.
Clear, consistent names help crews differentiate between similar items, locate equipment quickly, and avoid overusing high-demand assets.
Whether it’s a backup generator, a specific ladder, or a compressor in a remote yard, quick identification prevents delays and confusion.
Tom Richter, Head of Manufacturing at Nokia, underscores this point, explaining how effective tracking systems reduce both search time and replacement costs.
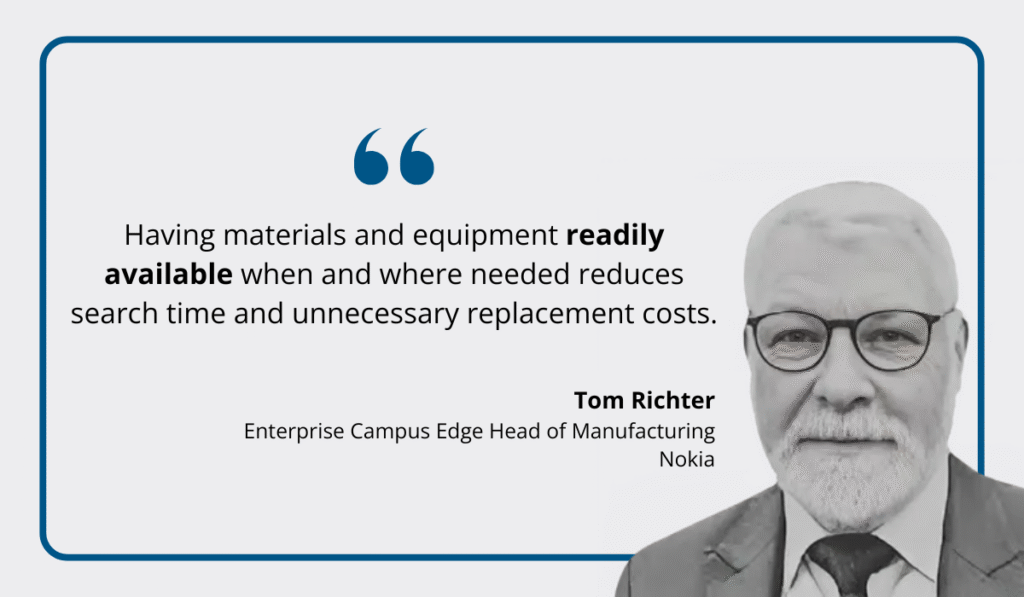
Illustration: GoCodes Asset Tracking / Quote: Manufacturing Digital
Beyond just assigning unique identifiers, it’s smart to build meaningful elements into the naming format.
That might include:
- Function and serial number
- Location, department, and asset type
- Manufacturer and model
For instance, using a function and a serial number means breaking the identifier into a descriptive label and a unique string, clearly distinguishing the item from others.
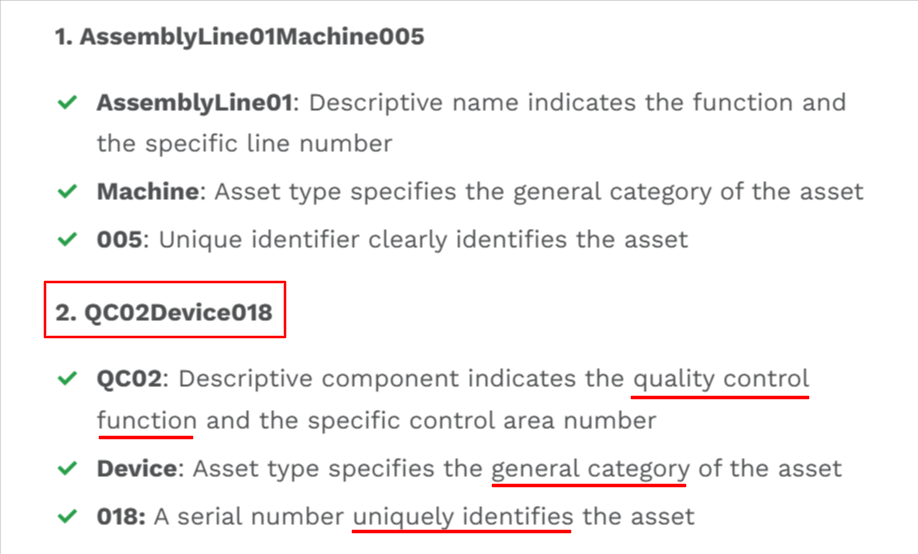
Source: Limble
Including a location can be especially helpful if you’re still using spreadsheets or basic asset lists.
For instance, a name like “Yard2_COMP05” instantly tells your team that it’s the fifth compressor located in Yard 2—no need to dig through a database.
Whatever structure you choose, the key is to keep it consistent, descriptive, and aligned with how your teams actually work.
Choosing Durable Labels
When you’re building an asset identification system, you want it to last.
Labels must remain readable over time, especially in tough field conditions where they can easily wear down, peel, or fade.
As Tyler Johnson, Grey Trunk RFID’s General Manager, puts it, it’s about ensuring your asset tags survive whatever the environment throws at them.
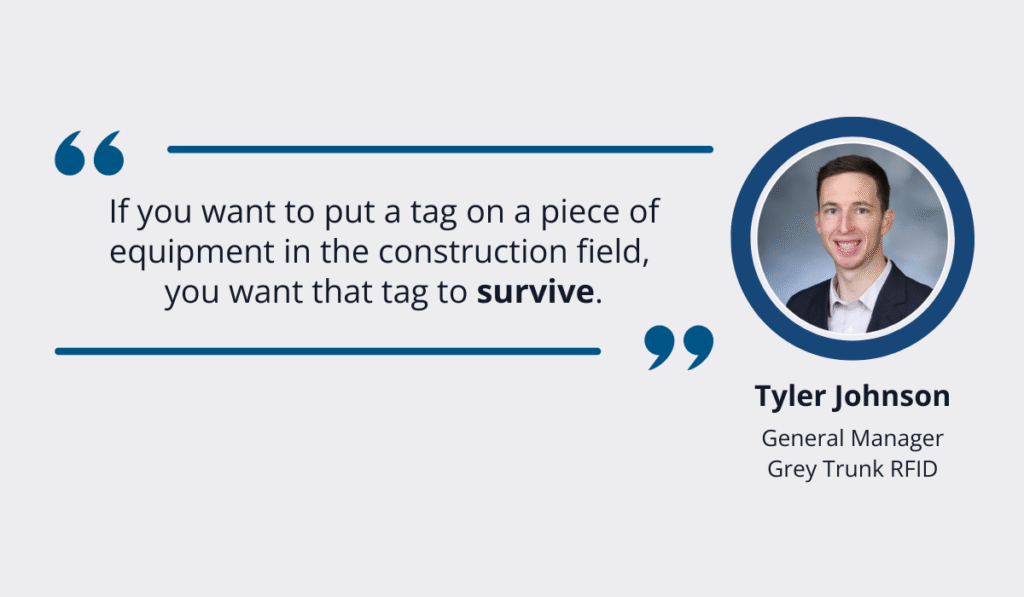
Illustration: GoCodes Asset Tracking / Quote: Grey Trunk RFID Asset Tracking on YouTube
The key is to match the label to your asset’s environment, whether it’s heat, rain, dust, chemicals, or heavy abrasion.
For example, a small indoor generator won’t need much more than a light-duty polyester tag.
Premium polyester labels also offer good scratch and chemical resistance, making them a reliable choice for assets that don’t have prolonged exposure to the elements.
However, they, too, aren’t designed to withstand UV rays, moisture, and extreme temperatures for longer periods.
That’s where heavy-duty options like metal tags come in.
If your equipment is regularly exposed to tough conditions, anodized aluminum labels are the more resilient choice.
The video below demonstrates how anodized tags hold up under intense heat compared to premium polyester.
Source: Metalcraft on YouTube
Pretty telling, right?
Metalcraft’s durability test is a clear indicator of how material choice affects lifespan, but their specialized aerospace-grade labels also come with premium pricing.
For industries like construction, utilities, and field services, anodized aluminum tags that offer rugged, UV- and chemical-resistant performance with multiple thickness options will more than suffice.
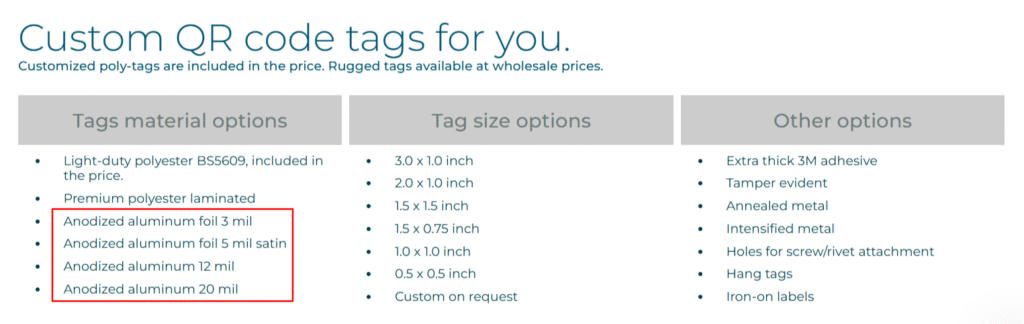
Source: GoCodes Asset Tracking
The bottom line?
Assess your working conditions, compare vendors, and choose labels built to last where it matters most.
Linking Tags with Software
Connecting physical tags to digital asset tracking software transforms simple labels into tools for real-time asset visibility and control.
It minimizes manual errors and streamlines everything from audits to maintenance scheduling.
Tagging assets without linking them to a shared software environment leaves you with disconnected data points.
Your crew might know an asset exists, but without a centralized system, they won’t know where it is, what condition it’s in, or whether it’s available for use.
Unfortunately, this is a pretty widespread issue.
An FMI study of over 2,000 U.S. construction firms found that only 37% store their data in a common environment.
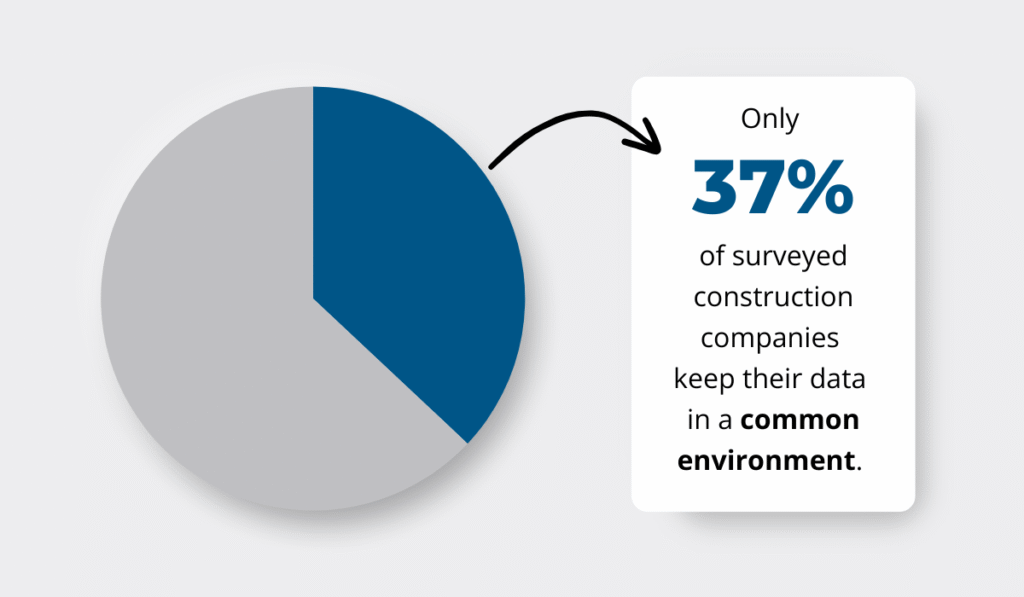
Illustration: GoCodes Asset Tracking / Data: FMI
Without a single source of truth, companies deal with duplicate entries, wasted hours searching for information, and poor asset utilization.
Some tools sit idle because no one realizes they’re available, while others get overused and wear out prematurely.
The solution?
Adopt a dedicated asset management platform and build a centralized, cloud-based asset database.
Thad Lutgens, Director of IT and equipment at LPR Construction, explains that software is at the heart of their equipment management.
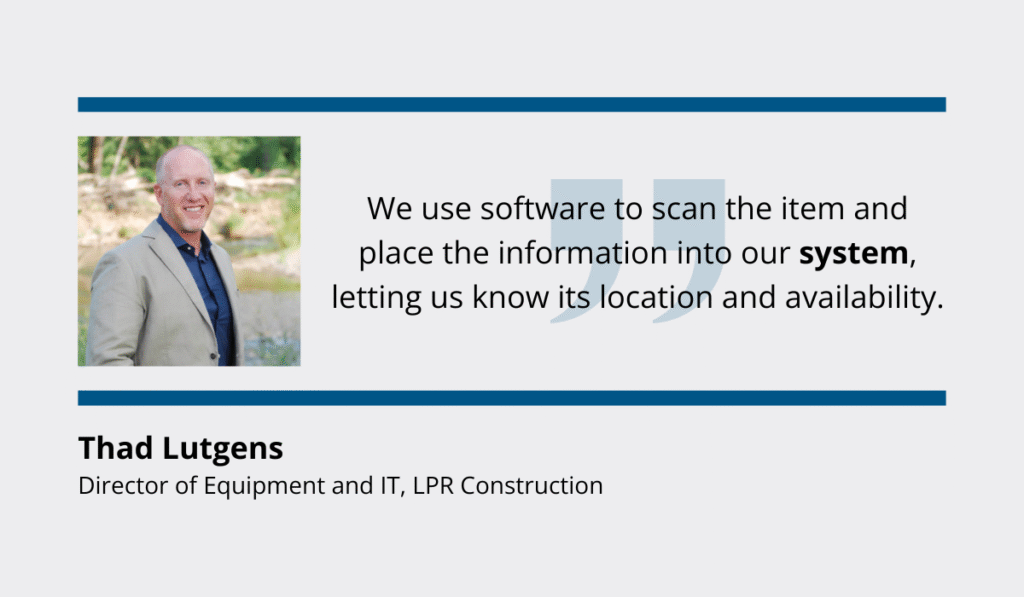
Illustration: GoCodes Asset Tracking / Quote: For Construction Pros
At LPR, every asset is checked in and out and linked to a central system via tags and GPS trackers.
Each record holds essential information like:
- Asset ID number
- Asset name and description
- Model and serial number
- Date of purchase
- Maintenance status
You can also expand it further, with corresponding asset photos, manuals, warranties, and more.
Cloud-based asset management solutions like GoCodes Asset Tracking make it easy to create such a system and access updated records from any device.
Whether you need a quick overview of all your assets or want to locate a specific item, it’s just a click away.
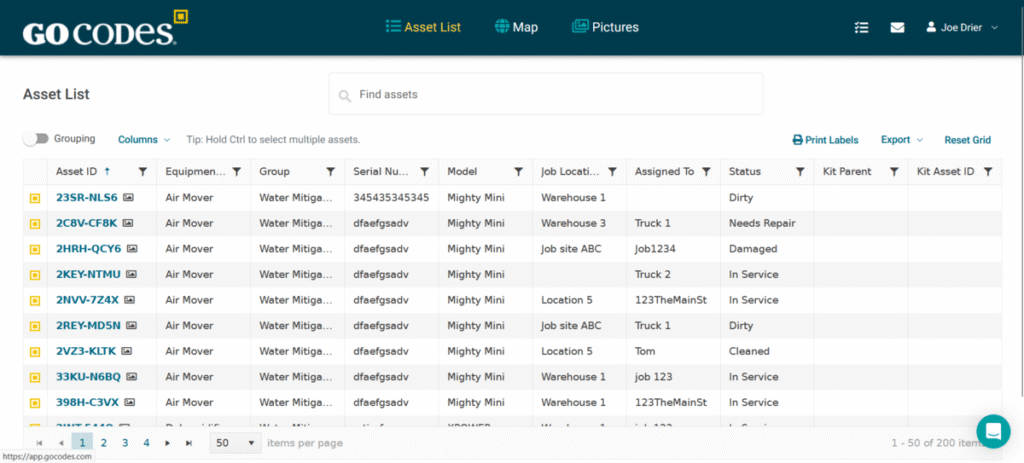
Source: GoCodes Asset Tracking
These solutions speed up processes like inventory audits, maintenance scheduling, and asset transfers, while ensuring your team makes decisions based on accurate, real-time information.
Features like GoCodes Asset Tracking’ agenda view also provide a clear overview of upcoming tasks, making it easy to stay on top of all asset-related responsibilities.
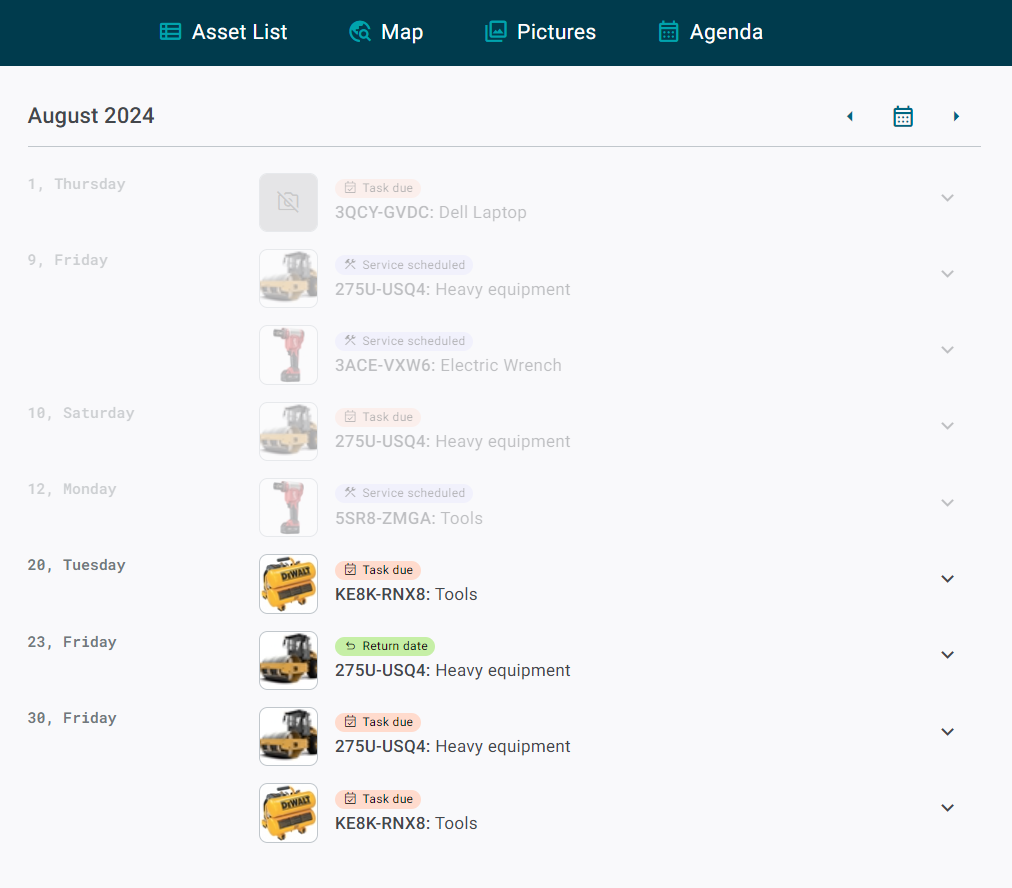
Source: GoCodes Asset Tracking
Without software, tags are just labels.
With it, they become a vital part of your business infrastructure.
Scheduling Asset Audits
Maintaining an accurate, up-to-date asset register is more than a good practice.
It’s essential for internal compliance and operational efficiency.
Regular audits play a key role in helping you ensure your asset records reflect what’s actually in the field, minimizing risks tied to outdated or missing data.
According to FE fundinfo research, over 40% of businesses report that keeping up with regulatory changes threatens their operations.

Illustration: GoCodes Asset Tracking / Data: FE fundinfo
Navigating shifting regulations is even harder when your asset data is incomplete or unreliable.
And as the report points out, compliance isn’t the only concern—asset managers must also balance costs and keep the business ready for new projects.
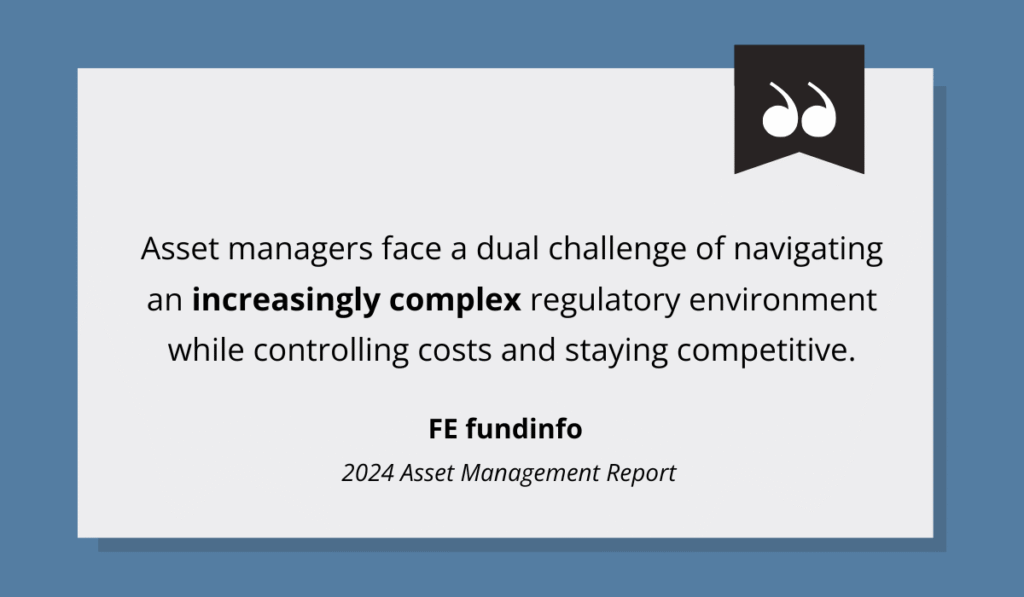
Illustration: GoCodes Asset Tracking / Quote: FE fundinfo
That’s why routine audits should be a core part of your asset strategy, with intervals tailored to asset value, mobility, and operational importance.
High-value, high-usage, or frequently moved equipment typically benefits from quarterly audits, while lower-risk and less mobile assets can be checked once or twice a year.
Regardless of timing, what matters is consistency and a clear audit process.
Automated barcode or QR code scans linked to a centralized asset database remain one of the most efficient and reliable methods.
They reduce human error and accelerate verification, especially during large-scale audits.
Discrepancies will happen—due to misplaced items, unrecorded disposals, or outdated data.
The key is to resolve them quickly and update your system immediately to maintain data integrity.
This is where mobile scanning features in digital asset tracking systems shine.
Source: GoCodes Asset Tracking
They simplify reconciling physical audits with recorded data, reduce administrative workload, and help your team respond faster to discrepancies.
Moreover, software-powered audits give managers sharper, real-time insight into their equipment’s status and performance trends, as explained by equipment manager Taylor Mitchell.
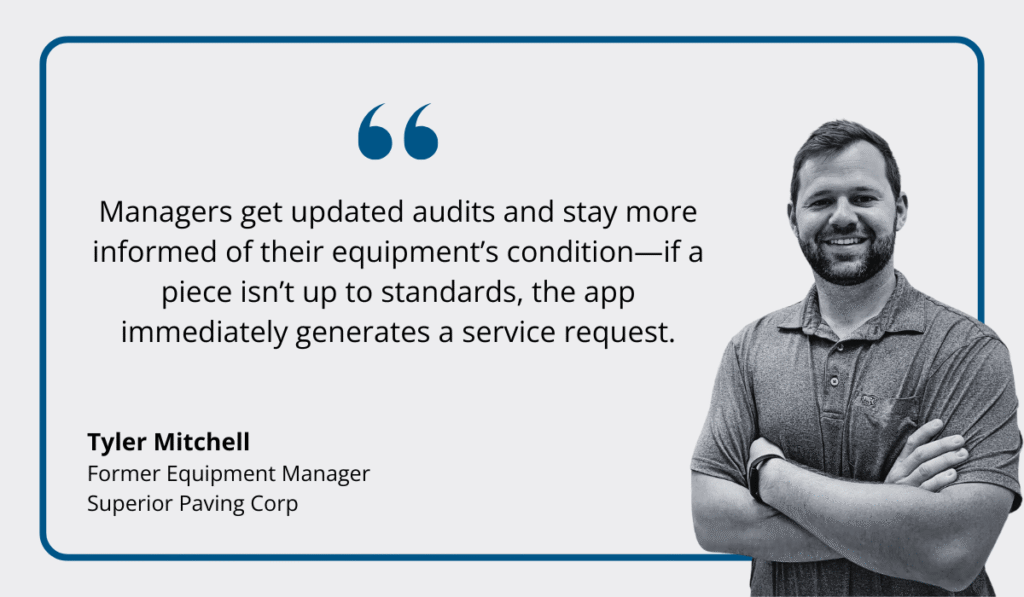
Illustration: GoCodes Asset Tracking / Quote: Construction Equipment
Ultimately, regular audits do more than help you avoid regulatory headaches.
They support smarter, faster decisions about maintenance, asset redeployment, and replacements—protecting your workflow, workforce safety, and bottom line.
Conclusion
If you want reliable asset identification, just sticking tags on your equipment won’t cut it.
Every detail matters, from selecting the right tracking technology and investing in durable labels to building a system that streamlines audits and centralizes data.
The practices we’ve outlined here will help you avoid common pitfalls and future-proof your tracking efforts.
The result?
A connected, efficient system that reduces costs, improves visibility, and keeps your construction projects on track.
Whether you’re managing a single site or hundreds of assets across multiple locations, getting asset identification right pays off—in both time saved and money earned.