Key Takeaways:
- PM checklists standardize procedures, reduce errors, and improve workplace safety.
- Different checklist types (pass/fail, step-by-step, and time-based) suit different assets and maintenance tasks.
- A strong checklist blends OEM guidelines, technician insights, and historical asset data.
- Digital tools simplify checklist distribution, scheduling, and updates across teams.
One missing step in a maintenance routine can cost a company tens of thousands—or even a worker’s hand.
Why leave that to chance when a preventive maintenance checklist can prevent it?
Whether you’re managing excavators on a jobsite, forklifts in a warehouse, or any other type of asset, a simple checklist can be the difference between smooth maintenance and a costly disaster.
Let’s see why you need one and how to create a PM checklist that actually works.
In this article...
Why You Need a Preventive Maintenance Checklist
A preventive maintenance (PM) checklist ensures that every maintenance task is done the right way, every time.
It brings consistency to your team’s work, reduces human error, and makes sure nothing critical is missed.
Like safety procedures, for example.
OSHA requires Lockout/Tagout (LOTO) procedures before servicing equipment.
But without a checklist, even experienced crews can skip steps, especially during shift changes or in a rush.
In one tragic 2019 case, a worker lost their hand because two crews failed to lock out a baler during maintenance, and the machine turned on mid-task.

Source: OSHA
The company was fined, and the worker paid a much steeper price.
A checklist prevents this kind of oversight by clearly outlining every step of the task, including preparing the equipment for servicing.
Safety aside, PM checklists also help with record-keeping.
A good PM checklist provides proof that maintenance was done, and that’s a big help for:
- Warranty coverage
- Insurance claims
- Compliance audits
- Dealer conversations
Tyler Smith, Product Manager of Articulated Haulers at Volvo Construction Equipment, agrees:
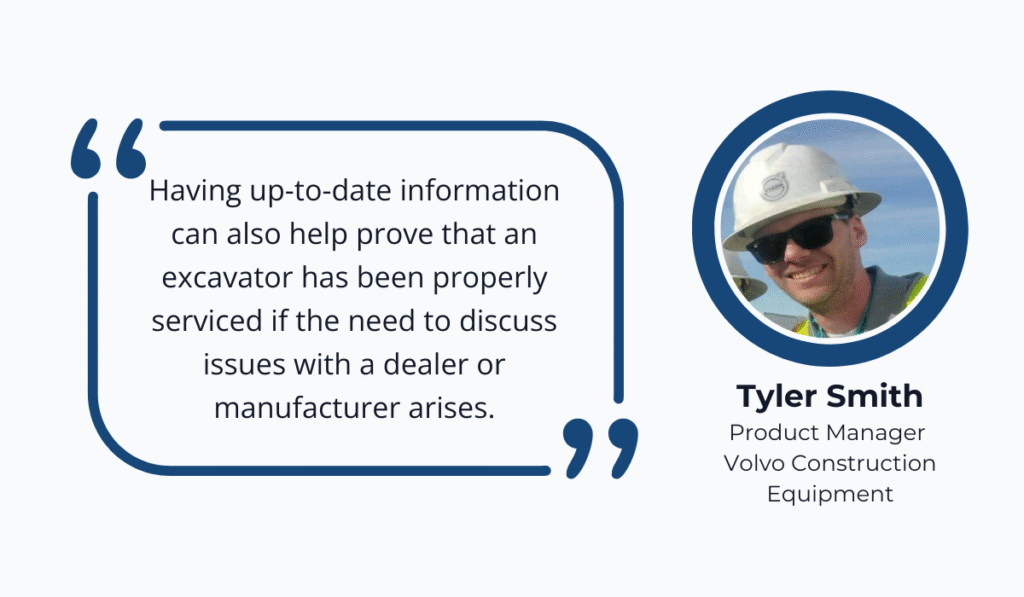
Illustration: GoCodes Asset Tracking / Quote: CONEXPO-CON/AGG
Beyond these checklist benefits, preventive maintenance in general keeps your equipment healthy, extends its lifespan, and, consequently, reduces costly equipment breakdowns.
From a financial standpoint, regular preventive maintenance is far more cost-effective than emergency repairs.
Terri Ghio, former president of FactoryEye North America, gives an example:
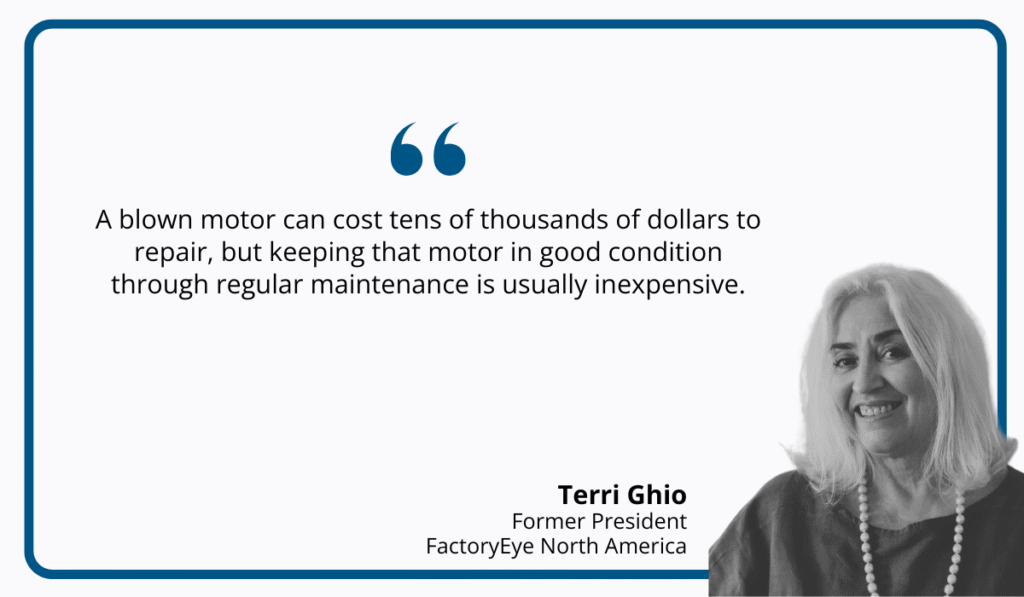
Illustration: GoCodes Asset Tracking / Quote: Pet Food Processing
Moreover, when assets break down, you’re not just facing repair costs.
Unplanned downtime also means idle workers, lost productivity, and missed deadlines.
Unfortunately, this is far too common.
Especially in industrial settings, where over two-thirds of businesses experience unplanned outages at least once a month, costing the average company nearly $125,000 per hour.
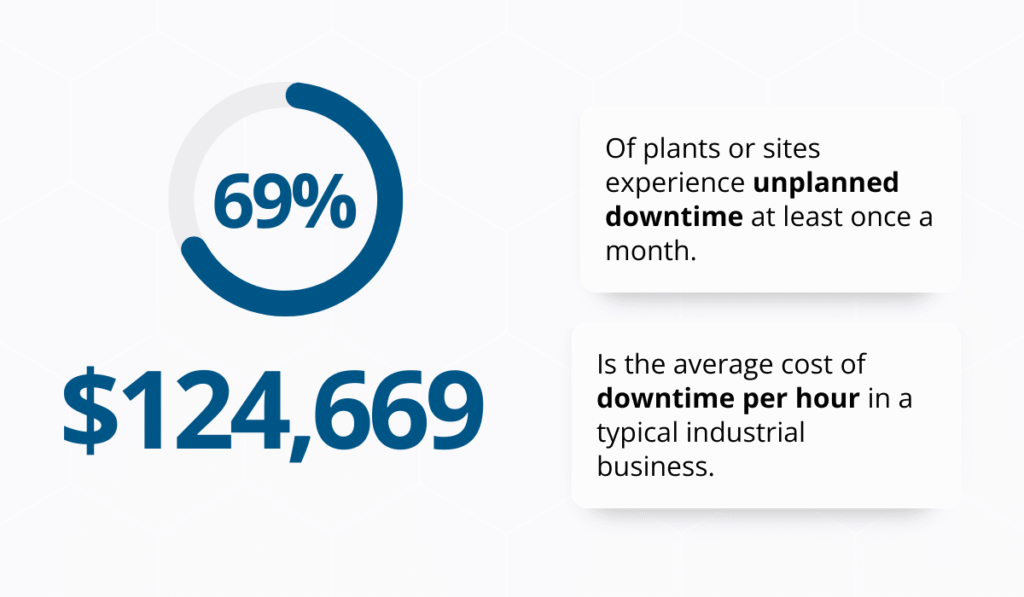
Illustration: GoCodes Asset Tracking / Data: ABB
Preventive maintenance helps you avoid all of it.
But for PM to work every time, you need a checklist that leaves nothing to chance.
Types of Preventive Maintenance Checklists
There’s no such thing as a one-size-fits-all preventive maintenance checklist.
Depending on the asset, the task at hand, and who’s performing it, you’ll need different types of checklists to keep maintenance consistent and error-free.
Here are the three most common types, along with practical examples you can use or adapt.
Pass/Fail Checklists
Pass/fail checklists are used for quick daily inspections, typically performed by machine operators before using equipment.
They help workers confirm whether essential components are in working order or not.
Each item on the list only requires a simple yes/no response.
If something fails, the next step is to flag the issue or trigger a maintenance work order.
Here’s an example of a pass/fail checklist for a warehouse conveyor system:
Record the belt speed using the built-in speed sensor. | Is the belt speed between 280–300 ft/min? | Yes/Pass, No/Fail |
Check the motor temperature with an infrared thermometer. | Is the temperature below 120°F? | Yes/Pass, No/Fail |
Listen for unusual grinding or squeaking noises during operation. | Is the conveyor running without abnormal noise? | Yes/Pass, No/Fail |
If any of the answers are “No/Fail,” notify your supervisor and submit a work order request. |
These checklists help catch small problems early, especially in fast-paced environments where full diagnostics aren’t possible during every shift.
Step-by-Step Checklists
Unlike pass/fail lists, step-by-step checklists are used for more technical tasks and are usually handled by maintenance technicians.
They function like miniature standard operating procedures (SOPs), guiding workers through every step required to complete a specific repair or maintenance job safely and correctly.
For example, for replacing a hydraulic filter on a skid steer, a step-by-step checklist would include these tasks:
Park the machine on a level surface and lower all attachments. |
Shut off the engine and engage the parking brake. |
Relieve hydraulic system pressure using the manufacturer’s recommended procedure. |
Put on protective gloves and eye protection. |
Place a drip pan under the filter location. |
Remove the old hydraulic filter. |
Apply a thin coat of clean hydraulic oil to the gasket of the new filter. |
Install the new filter by hand—do not overtighten. |
Refill the hydraulic fluid if needed, based on fluid loss. |
Start the engine and let it run for a few minutes. |
Inspect the new filter and the surrounding area for leaks. |
Log the task and record fluid levels in the maintenance system. |
This type of checklist helps eliminate guesswork, especially when tasks are performed by different people across shifts.
It ensures consistency and safety while making it easier to train new team members.
Time/Usage-Based Checklists
Some checklists are based on specific intervals—either time (daily, weekly, monthly) or usage (every 100, 250, or 500 operating hours).
These are often recommended by manufacturers to prevent wear, reduce downtime, and extend equipment life.
For example, John Deere provides detailed preventive maintenance intervals for their excavators.
Here’s how those tasks evolve over time:

Source: HVI
Each maintenance interval requires a different checklist to ensure the right tasks are performed at the right time.
That’s why it’s important to create separate checklists for each interval rather than relying on a single, catch-all list.
Preventive Maintenance Checklist Examples
To give you a clearer picture of what preventive maintenance checklists look like in practice, we’ve included two real-world examples.
The first checklist, created by Forms Direct, is a comprehensive inspection sheet for vehicles or heavy equipment.
It’s designed to help technicians perform systematic checks across all major systems—engine, steering, brakes, suspension, tires, hydraulics, and safety equipment.
Each item can be marked as needing repair (X), okay (✔), or not applicable (NA), with space for additional notes and consumables used.
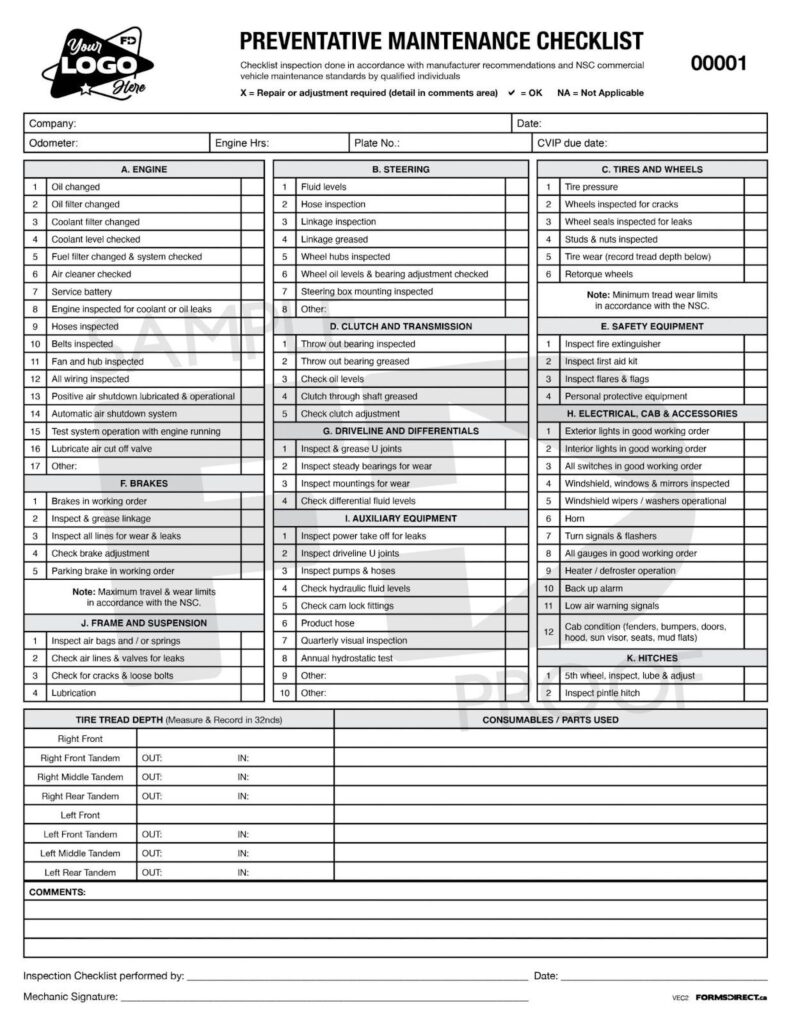
Source: Forms Direct
This format is especially useful in fleet management, where detailed tracking of each component’s condition is critical for both compliance and safety.
The second checklist focuses on generator maintenance.
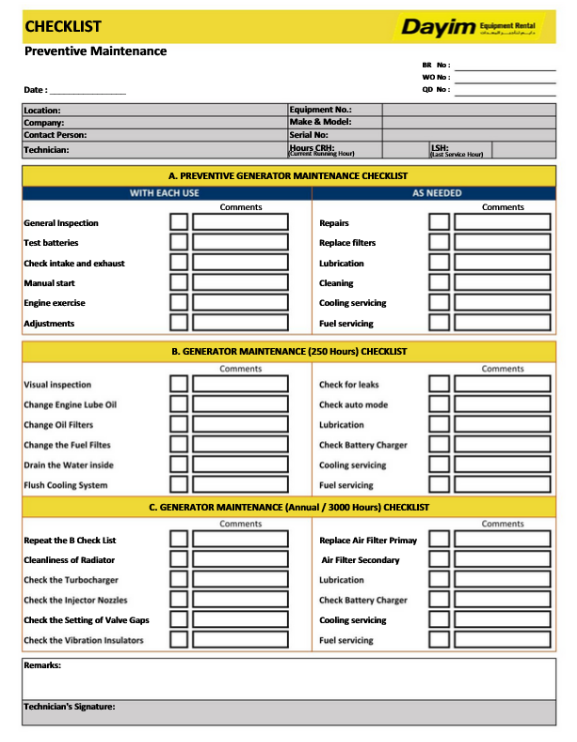
Source: Calameo
As you can see, it’s divided into sections based on maintenance intervals—tasks to be done with each use, every 250 hours, and annually (or every 3,000 hours).
The checklist includes routine actions like oil and filter changes, battery checks, and cooling system servicing.
There’s also space for comments and technician signatures, helping teams stay accountable and track service history over time.
How to Prepare a Good Preventive Maintenance Checklist
Before we wrap up, here’s a simple guide to building a preventive maintenance checklist that fits both your equipment and your team’s day-to-day operations.
Start by deciding which assets actually need a preventive maintenance checklist.
Not every tool or piece of equipment requires one, especially if it’s inexpensive, rarely used, or low risk.
Instead, focus on high-value or high-risk assets that are critical to operations or more likely to fail.
Next, turn to your OEM manuals.
They contain detailed service intervals and maintenance procedures based on extensive testing, as Tyler Smith from Volvo points out:
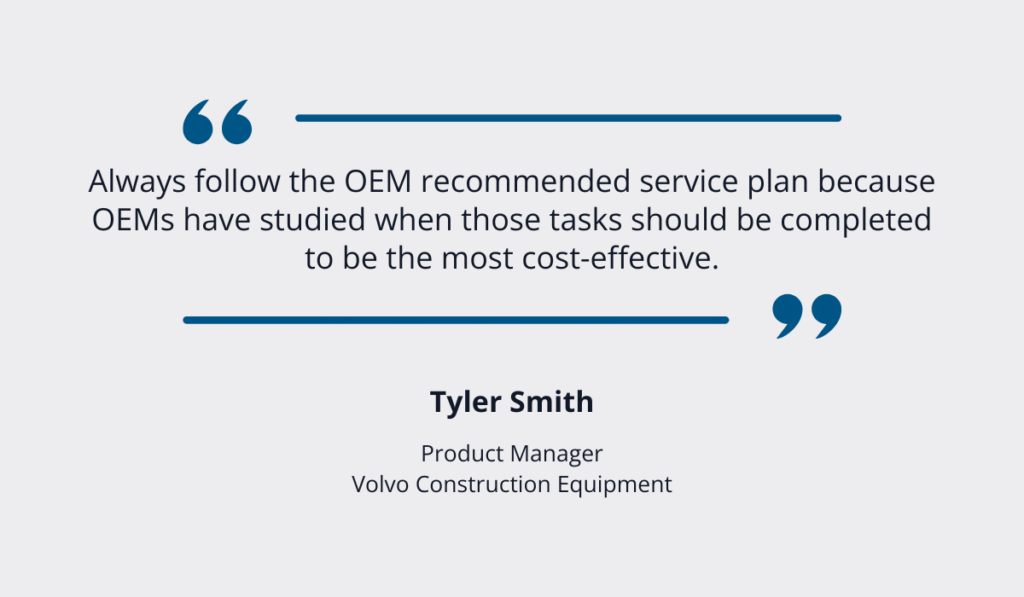
Illustration: GoCodes Asset Tracking / Quote: CONEXPO-CON/AGG
But remember that OEMs don’t know your job site.
That’s why you need to go beyond the manual when organizing preventive maintenance.
So, talk to your technicians.
They know the quirks, usage patterns, and real-world issues better than anyone.
If you want to take it a step further, use your historical data.
If you’re using an asset management system like GoCodes Asset Tracking, you already have a goldmine of past service logs and part replacements at your fingertips for every single asset.
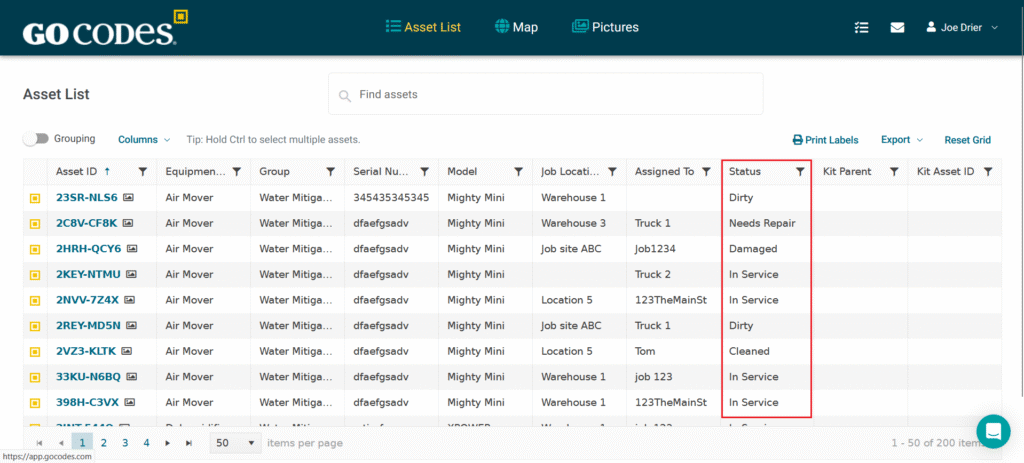
Source: GoCodes Asset Tracking
That kind of data helps you identify trends, like recurring failures or assets that need more attention than the OEM suggests.
Now, it’s time to build your checklist.
Pull together everything:
- OEM recommendations
- Technician insights
- Real-world usage
- Historical data
Then, create detailed, asset-specific checklists that reflect how and where your equipment is actually used.
Once your checklist is ready, use digital tools to distribute and manage checklists and PM tasks.
With GoCodes Asset Tracking, you can attach checklists to individual assets by simply adding a document like below:
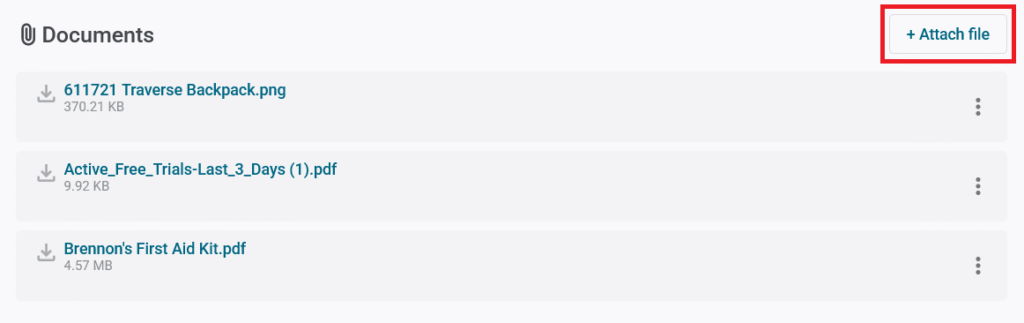
Source: GoCodes Asset Tracking
You can also schedule preventive tasks and give your technicians instant access in the field.
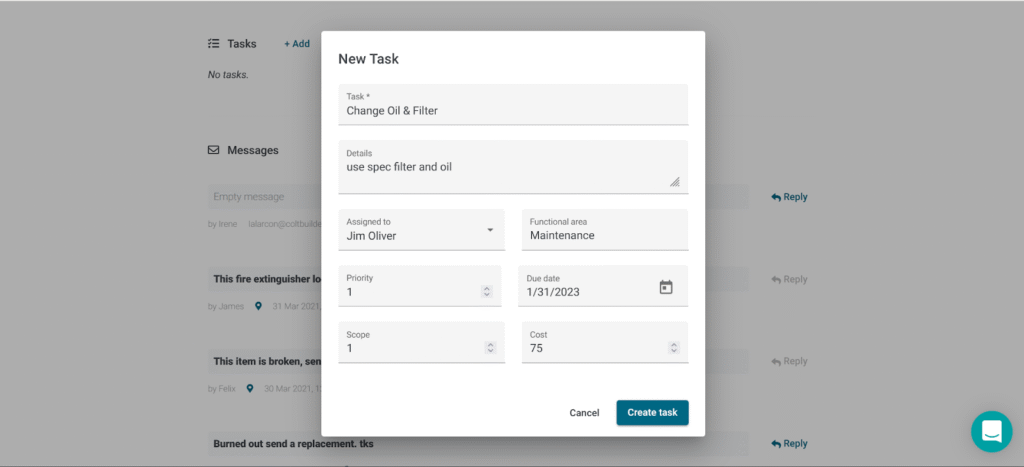
Source: GoCodes Asset Tracking
Even better, maintenance tasks can be repeated in just a couple of clicks.
That means no more attaching the same checklist again and again—just hit “repeat” and you’re good to go.
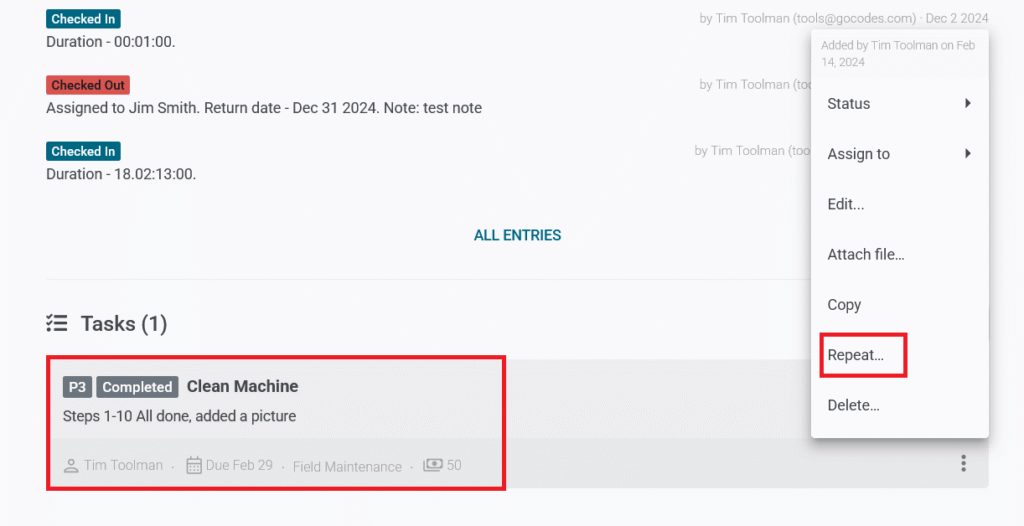
Source: GoCodes Asset Tracking
Finally, keep your checklists alive.
Update them regularly based on new data and feedback from your team.
If something’s not working or if maintenance tasks aren’t improving performance, adjust as needed.
Conclusion
One missing maintenance step can cost a fortune—or a worker’s safety.
That’s why preventive maintenance checklists matter.
They reduce human error, extend equipment life, and prevent costly downtime.
They’re also simple to create, especially if you already track your asset data with a robust asset management system.
Just connect the dots—OEM guidelines, technician input, and service history—and turn that into smart, repeatable PM checklists.
Start building your checklists today and turn your maintenance from reactive to rock-solid preventive.