Tracking raw material usage effectively keeps costs low and ensures the best allocation of resources. Unfortunately, not everyone knows the best way to track.
If you have questions about tracking, try implementing the Seven Steps we’ve outlined below.
We think you’ll love the raw (material) results!
In this article...
Maintain Accurate Records
First, ensure that you maintain detailed records of all your raw material purchases and usage. To do this:
- Log purchase orders and invoices.
- Track receipts of materials delivered to the site.
- Record the issuance of materials to different departments or project areas.
Simply, upload your documentation to your GoCodes Asset Tracking account, keeping everything organized, in one easily accessed place.
Implement Inventory Management Software
Use the GoCodes Asset Tracking’ Inventory Management feature to keep track of raw materials’ usage on the go.
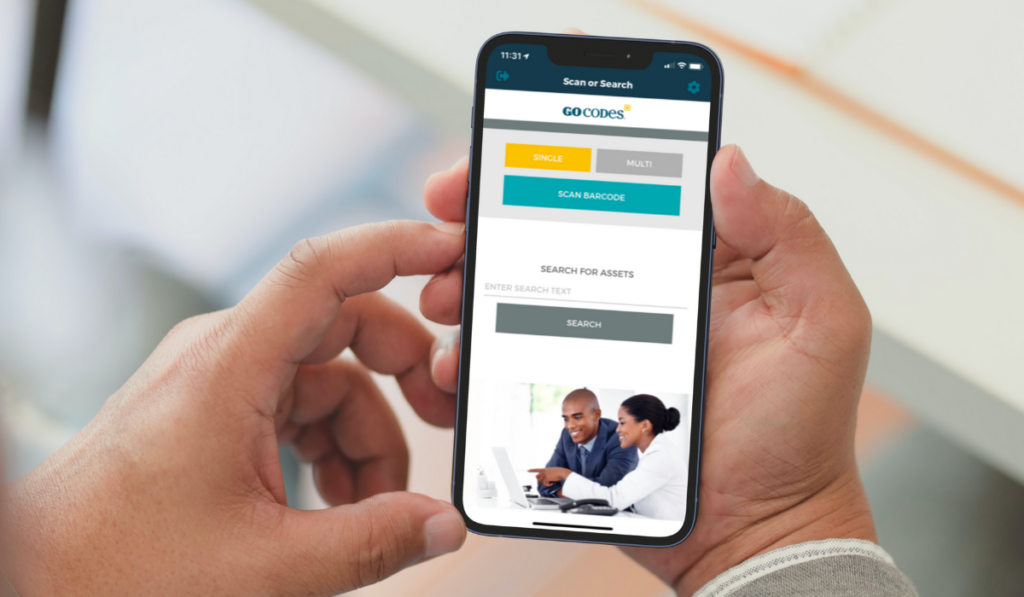
Automate the tracking of raw material usage, receive real-time updates, and generate comprehensive reports so that you and your team have clear, accurate, up-to-date raw material information at your fingertips.
Conduct Regular Audits
Perform regular physical audits of your raw material inventory.
Regular physical audits are vital to enable you to:
- Identify discrepancies between recorded and actual inventory levels.
- Detect any wastage, theft, or damage.
- Ensure accurate reporting and material usage tracking.
Use a Bill of Materials (BOM)
A BOM is a detailed list of all materials required for a project and will help you to:
- Estimate the total material requirements for the project.
- Track the consumption of each item against the planned usage.
- Identify any variances or deviations from the plan.
Now you’ll know what material you ordered, what you’ve used, and what you should have left for each project.
Monitor Material Usage Rates
Consider your material usage rates to understand patterns and trends, so that you can better anticipate your future raw material needs.
For example, if you see that your business typically uses 100 sheets of drywall per week and it’s the beginning of November, you might decide to purchase 800 sheets of drywall to take you through to the end of the year.
You can monitor material usage rates with the following:
- Compare your actual usage against the project plan or BOM to see whether your project plans are typically accurate.
- Adjust future material orders based on your past consumption rates.
- Implement steps to optimize material usage and reduce waste.
Share Information
Ensure your employees can instantly access up-to-date information about your stock inventory so that they can use that information to communicate schedules to customers or initiate reorders if stock is low.
This way, your employees can help with raw material management for a more streamlined process.
To achieve good information sharing:
- Regularly update employees on material consumption.
- Hold periodic meetings to discuss material requirements and any issues that you may have.
- Use GoCodes Asset Tracking to share real-time data on material usage.

Create Custom Reports
Create custom reports on material usage to facilitate good material decision-making.
Reports should include information such as:
- Total materials ordered and received.
- Materials issued to the project and their respective quantities.
- Remaining inventory levels and any discrepancies noted during audits.
Conclusion
By following these steps, you’ll efficiently track your raw material usage for business results that will warm your heart this Valentine’s.