The construction industry is filled with risks and uncertainties.
Different issues can arise at all times, so every business looks for ways to anticipate risks and minimize their impact.
Vigilant risk management is essential in these efforts, which means that being up to speed with industry trends and insights is key.
With that in mind, we’re going to break down 12 statistics about construction risks that every construction professional needs to know.
Want to enhance your risk management and stay ahead of the curve?
Say no more, and join us for a deep dive!
In this article...
Safety Risks Statistics
Construction has a reputation as one of the most dangerous industries in the U.S. and globally.
So, there’s no doubt about the fact that the safety and well-being of your construction workers should be a top priority.
The numbers below offer useful pointers on where to start, so let’s get to it.
In 2022, Construction Workers Accounted for 19.9% of All On-The-Job Fatal Injuries in the US
One of the key findings of an extensive report on fatal injury trends in the US was that construction workers accounted for one-fifth of all on-the-job fatalities in 2022.
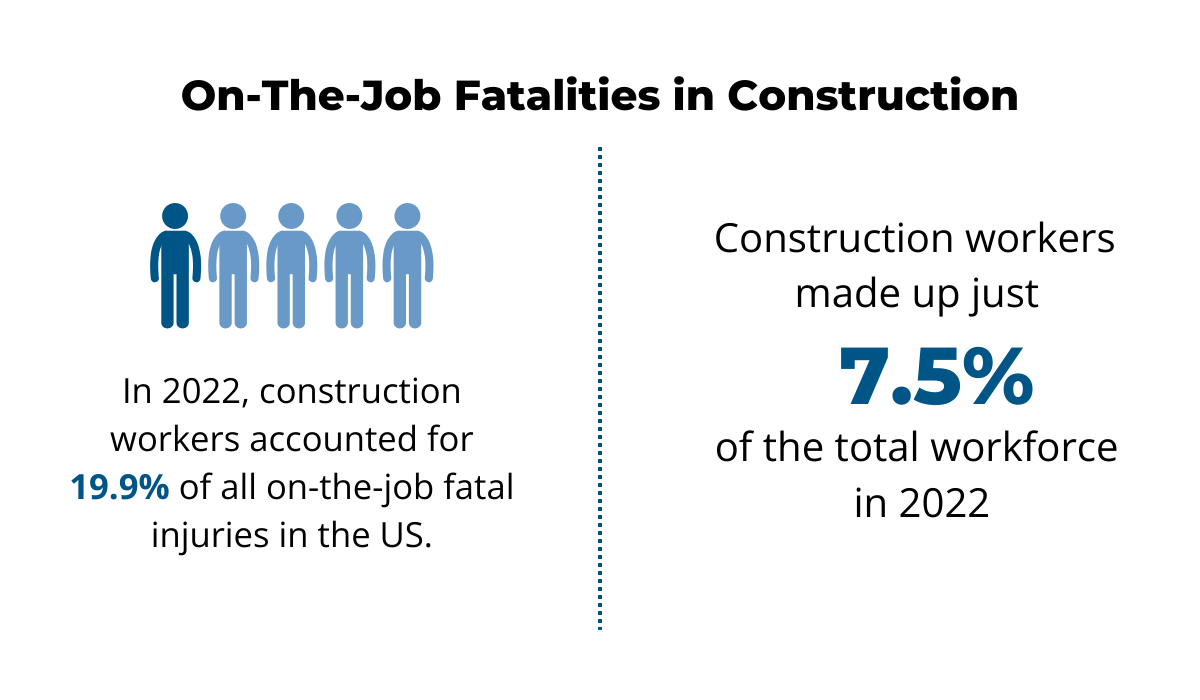
This figure is even more striking when we take into account that construction workers made up only 7.5% of the total workforce.
In other words, construction workers face a disproportionate risk of fatal injuries compared to other industries.
Yes, the construction industry has always been regarded as one of the most hazardous in the US, and this is reflected in CPWR’s numbers.
What should be worrying, however, is that the number of fatal injuries in construction increased by a staggering 39.8% between 2011 and 2022.
The takeaway is clear:
There is an urgent need for stronger safety measures and enforcement to protect construction workers on the job site to prevent that number from growing any further.
At 36.4%, Falls to a Lower Level Were the Most Common Cause of Fatal Injuries Among Construction Workers in the US in 2022
In producing their report, CPWR included data from the Census of Fatal and Occupational Injuries (CFOI), the National Vital Statistics System (NVSS), and their own Construction Fatality Map.
All the examined sources pointed to falls to a lower level as the leading cause of fatal injuries.
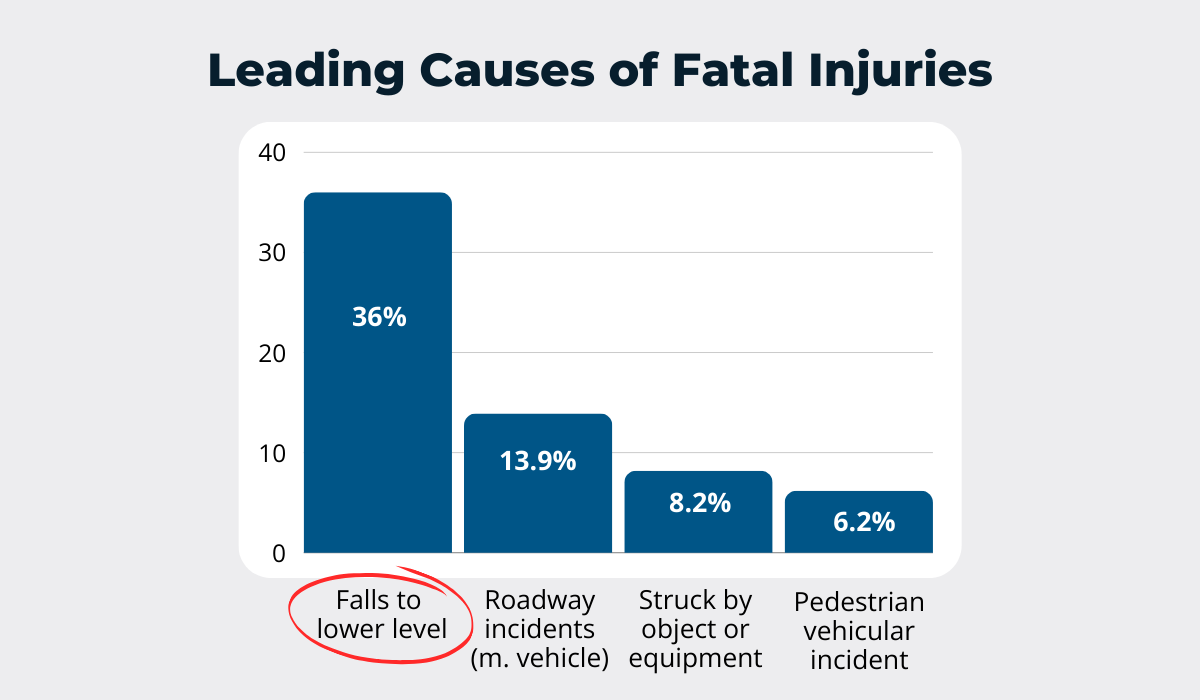
This type of injury is defined as an impact between a person who is falling and a lower surface, which can include several different scenarios:
- falling from a roof to a ground level,
- falling from a ground level into an opening or body of water, or
- falling from a collapsing structure.
The CPWR’s Construction Fatality Map narratives, which draw data from ongoing OSHA fatality investigations and online media sources, also mentioned falls nearly 4,000 times.
What’s important to note is that roofs or ladders were also mentioned over 2,500 times.
This corresponds to CFOI data showing that roofers were particularly exposed to risks, suffering the highest number of fatal injuries.
In light of these findings, fall prevention and related safety measures are essential parts of successful risk mitigation.
47% of Construction Companies either Don’t Gather Any Safety Data or Don’t Use It to Improve Their Safety Program
Technology is a vital part of construction safety today, but this is not exactly the case for safety data.
Dodge Construction Network and CPWR’s 2023 research on safety management revealed that, while 62% of respondents deploy technology to improve safety, 47% don’t collect or analyze their safety data.
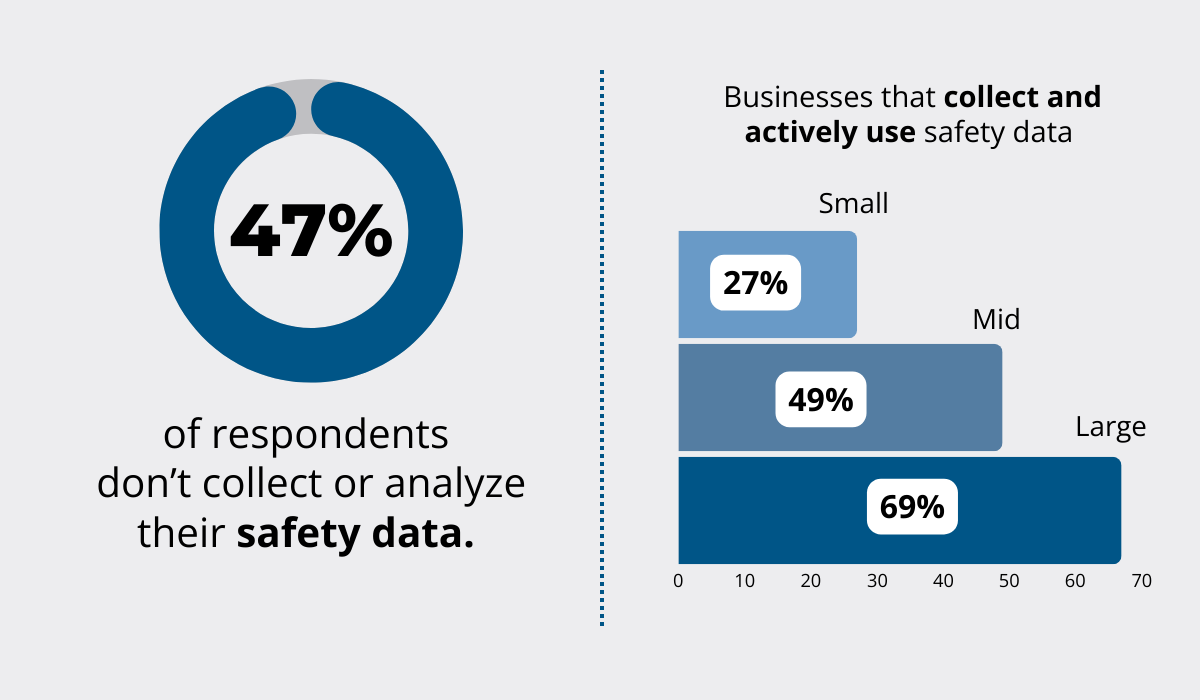
This means that only half of surveyed contractors use their safety data effectively to identify areas for improvement and develop relevant safety policies.
Furthermore, the findings suggest that the main factor in collecting and using safety data is company size.
The numbers show that larger businesses, with 100+ employees, perform far better in this area.
This discrepancy is worrying because safety data enhances decision-making and overall safety.
As Waseem Rehman, Senior Project Manager for the Saudi Arabian megaproject NEOM, points out:
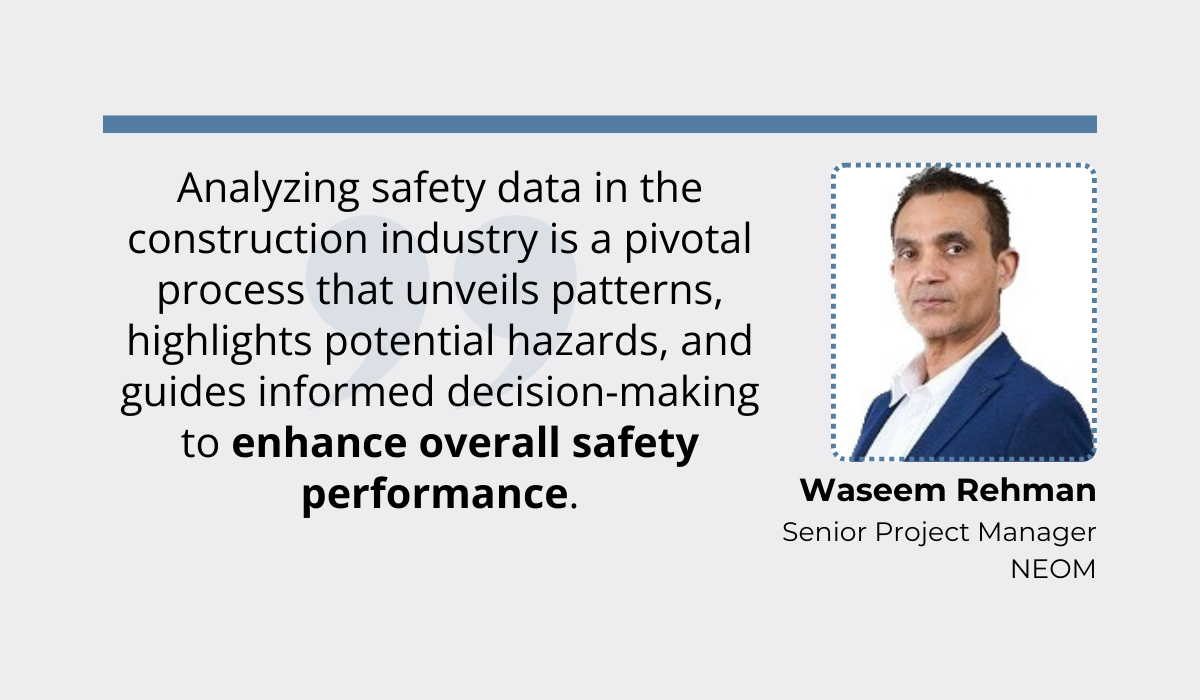
Using and analyzing safety data requires better practices and cost-effective, intuitive tools.
Otherwise, data-driven risk mitigation will remain a challenge for companies of all sizes.
Theft Risks Statistics
Another group of common construction risks relates to construction site theft.
Loss of valuable construction equipment can seriously impact both the financial and operational aspects of your business, so here’s what you should keep in mind.
62% of Construction Site Workers Say That Theft Has Increased in the Last Year
Out of 500 construction site workers surveyed by BauWatch, a prominent UK-based supplier of surveillance systems, six in ten reported that theft increased in 2023.
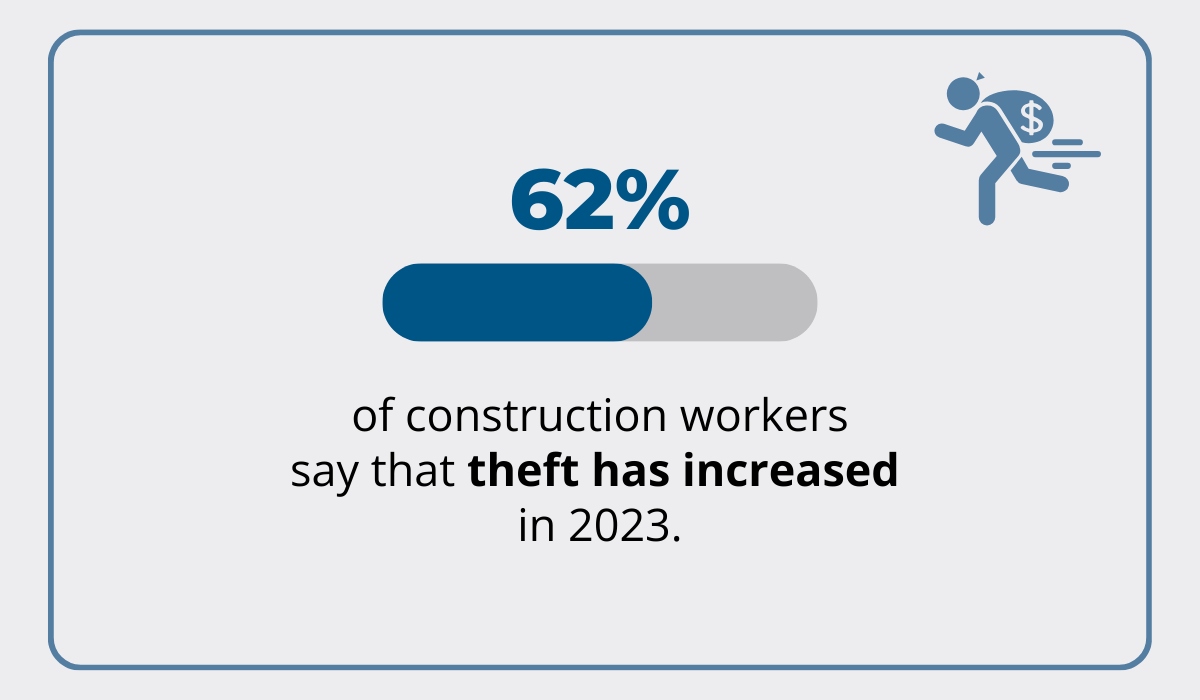
Moreover, around 70% of respondents confirmed that they had witnessed theft on-site, showing that the theft epidemic in the UK isn’t just a matter of impressions.
The thieves target different equipment, with two-thirds of cases being “minor” offenses where the costs of stolen equipment range between $650 and $5,200.
However, these costs add up over time if no measures are implemented, and BauWatch’s report identifies this as one of the key issues.
Namely, despite the widespread nature of construction crime, 34% of respondents state that security is a low priority on their job sites.
Poor security means slower response time, and can even help perpetuate crime.
The only solution for mitigating security issues is proactive and systematic risk management.
24% of Stolen Construction Goods Are Vehicles or Expensive Machinery
Stolen construction equipment ranges in size and value, but the aforementioned BauWatch report shows that nearly a quarter of stolen goods are vehicles or expensive machinery.
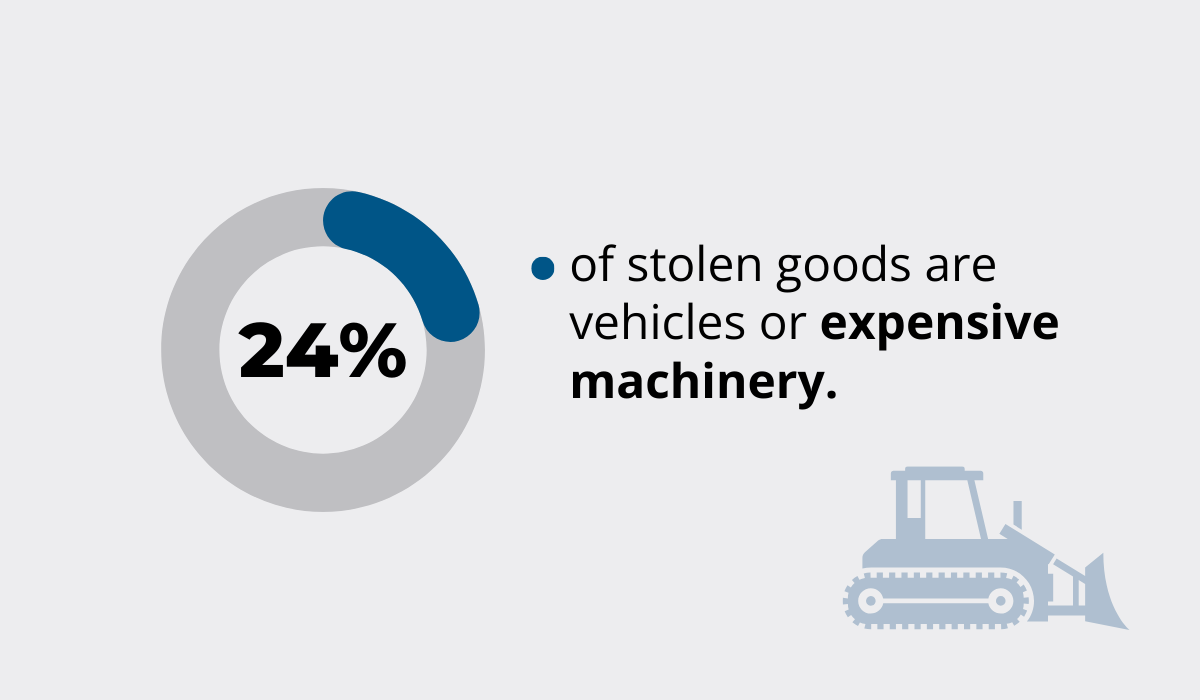
One such example happened in Maryland recently, with police recovering one million dollars in stolen construction equipment.
The haul included 13 skid steers, 2 excavators, and numerous trailers and other equipment.
Speaking on behalf of the Prince George’s County Police, Captain Craig Winegardner noted that the thief targeted smaller companies that are especially vulnerable to theft.
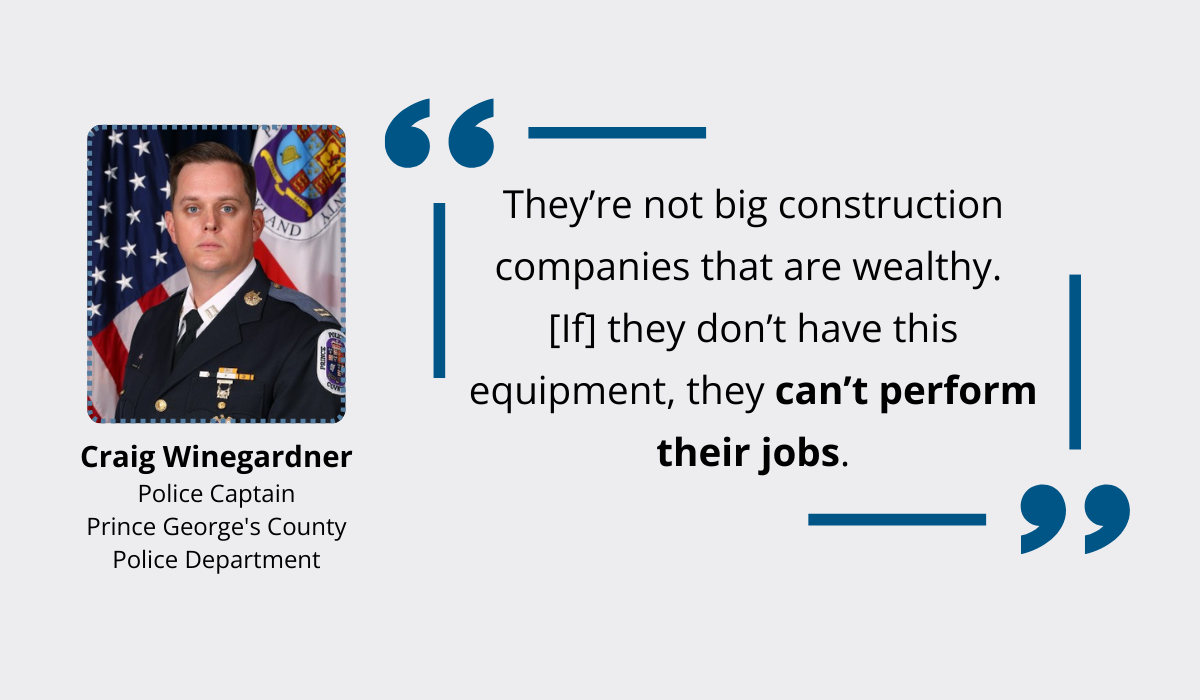
If valuable assets are stolen, the companies in question are exposed to both financial burdens and significant productivity drain.
This is especially true if the missing resources can’t be easily replaced.
What makes the story even more troubling is the fact that the lone thief didn’t employ particularly sophisticated tactics that are becoming more widespread.
The lack of on-site security made his job easy, which indicates that construction companies should consider doing more to protect their assets.
65.2% of Construction Professionals Find That Tracking Systems Are Effective at Deterring Crime on the Construction Site
In their survey on construction crime, The Chartered Institute of Building (CIOB) asked construction professionals about their experience with different theft deterrents.
Using tracking systems or unique asset identifiers proved to be an effective measure for nearly two-thirds of respondents.
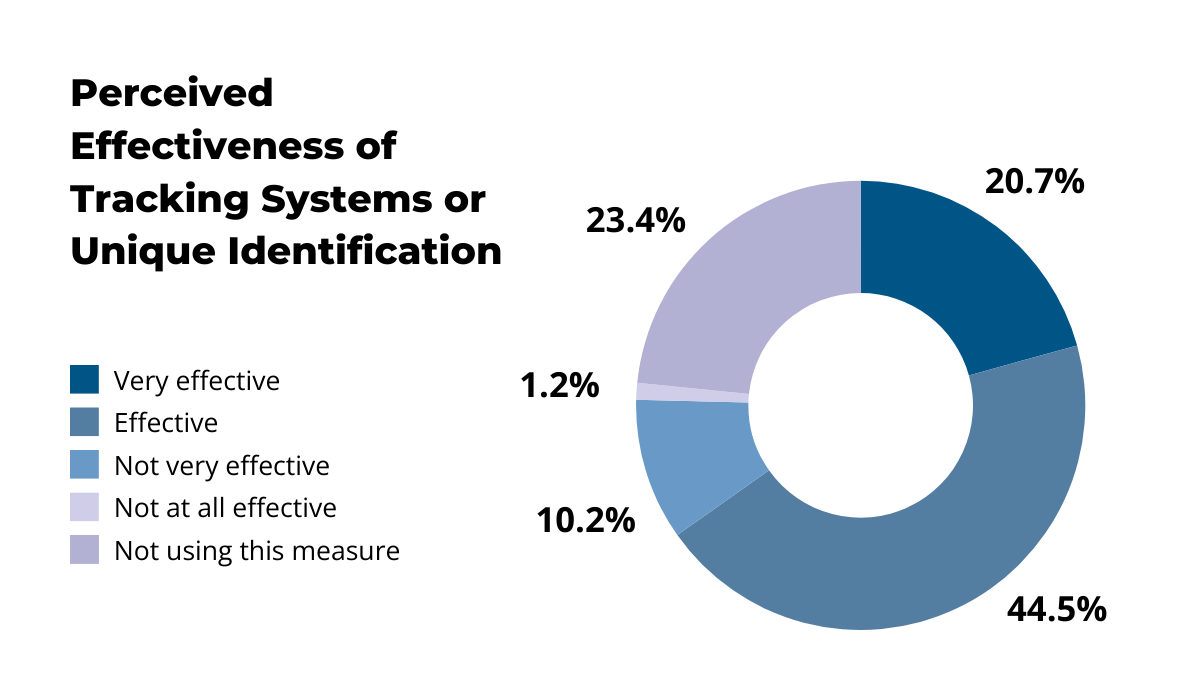
Nowadays, technology is the contractors’ fiercest ally in combating theft, but tracking solutions stand out for their ability to aid asset retrieval.
For instance, a UK-based surveying company Survey Solutions suffered a brazen theft recently, with thieves taking an expensive piece of equipment all the way to Warsaw, Poland.
Luckily, the stolen total station was equipped with a system that tracked the instrument’s movement in real time, aiding in its successful recovery.
So, what can other businesses do in terms of deterring theft from the construction site?
Well, they can consider investing in asset tracking solutions, such as our GoCodes Asset Tracking.
GoCodes Asset Tracking offers advanced features like geofencing, which triggers instant loss alerts as soon as the asset moves outside its designated boundaries.

You can deploy a geofence in minutes, setting it up in a way that gives you the biggest strategic advantage.
For example, setting up geofences at entry and exit points or around storage areas enables you to closely monitor access to sites, which doubles as one of the survey’s key recommendations.
Ultimately, the goal is to keep a watchful eye over the most valuable assets, and these systems excel at it.
Labor Shortage Risks Statistics
Labor shortages remain a long-standing problem in the construction industry, impacting successful project completion.
The following statistics highlight the risks from different angles.
In 2023, 61% of Construction Companies Said That Worker Shortages Were to Blame for Their Project Delays
If there aren’t enough workers to take on projects, you’re bound to face delays.
This is confirmed by the 2023 survey conducted by the Associated General Contractors of America (AGC) and Autodesk.
It revealed that a staggering 61% of construction companies identified labor shortages as a major factor behind project delays.
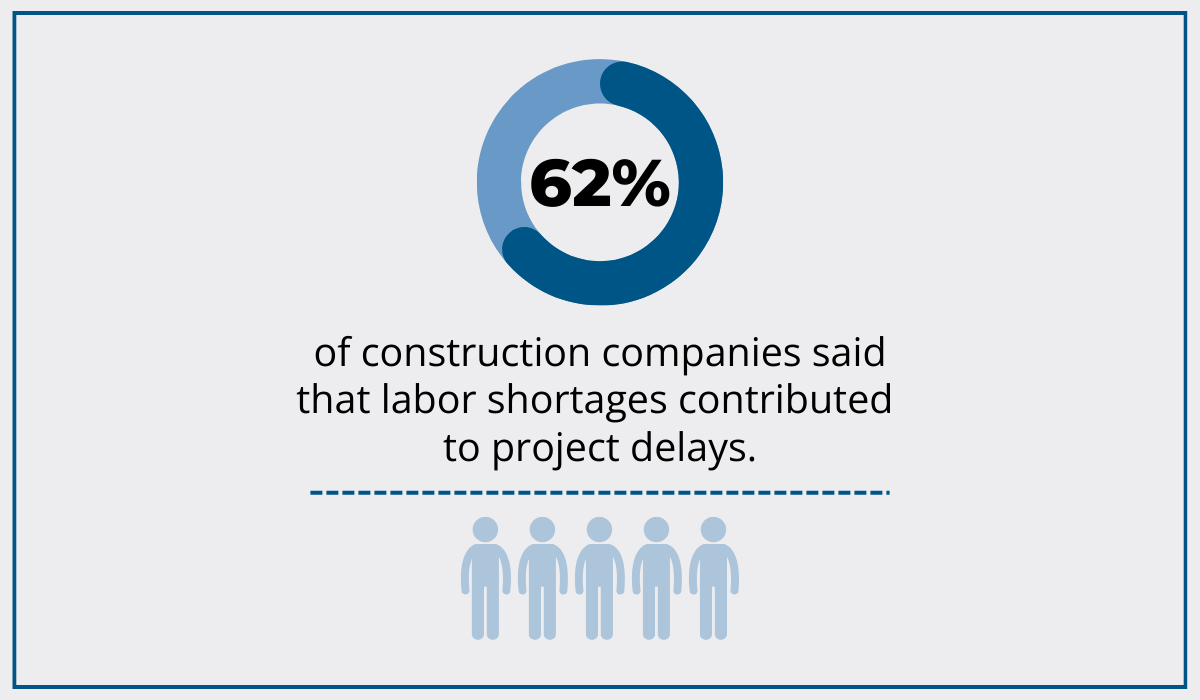
Of course, labor shortages are hardly the only reason for delays, which is why a slightly higher percentage of businesses also cited supply chain challenges.
However, companies have less control over supply chain disruptions.
So, it’s no wonder that many are turning to areas they can influence more directly, and coming up with different strategies to attract and/or retain workers.
The report lists several such measures, including:
- Raising base pay rates (81%)
- Providing incentives and bonuses (44%)
- Improving benefits packages (26%)
- Adopting digital hiring strategies (63%)
One thing’s for certain: coping with labor shortages and related challenges already requires creative and proactive measures.
The Share of Builders Reporting Shortages in 2024 Was 52% For Labor Directly Employed
Another report on the construction labor market, authored by the Home Builders Institute (HBI), reveals that 52% of builders reported shortages of directly employed labor.
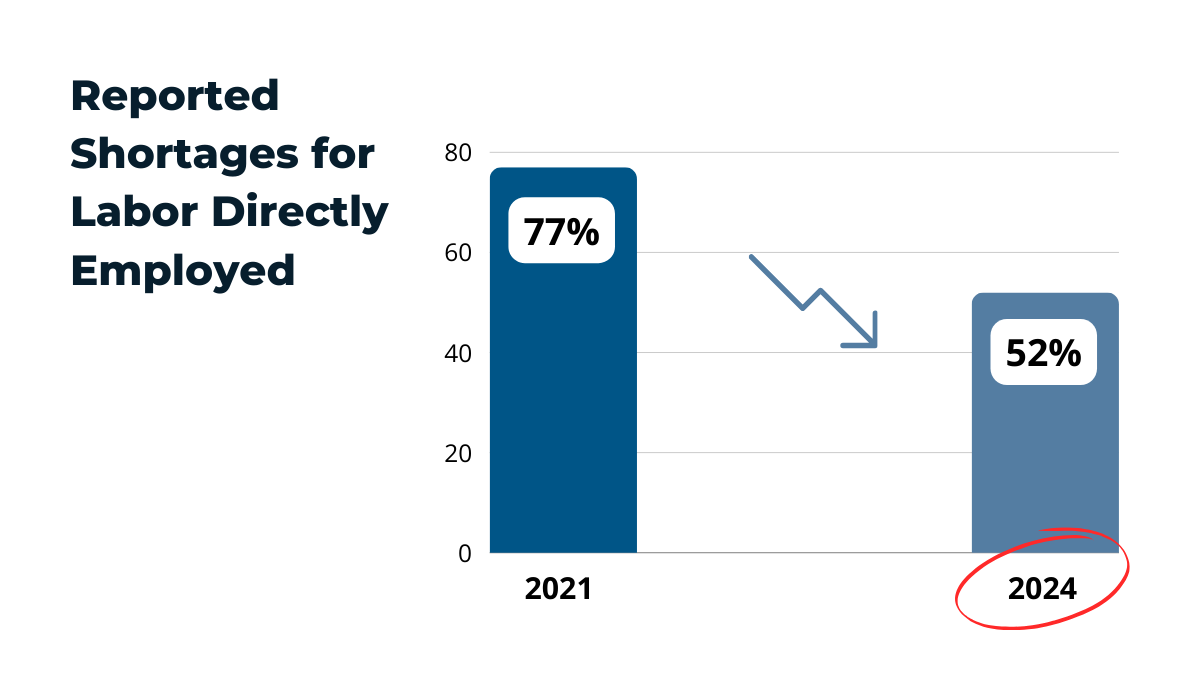
It’s important to note that this is the lowest labor shortage rate in five years, especially compared to a record high of 77% in 2021.
Despite this improvement, though, the shortages remain significant from a historical perspective.
Interestingly enough, subcontractor shortages were consistently more widespread in the past, especially compared to direct labor.
However, the reported shortages in February 2024 stood at 52% for direct labor and 51% for subcontractors, making the gap between the two virtually nonexistent.
This goes to show that companies can’t rely on subcontractors to fill labor shortages either.
Instead, the solution lies in optimizing the existing workforce by investing in cross-training, reskilling, and other professional development initiatives.
In fact, the previously mentioned AGC report shows that 41% percent of businesses are already investing in training programs for new hires and existing workers.
By addressing the growing skills gap, companies look to strategically enhance productivity and maintain their agility as a way of tackling ongoing challenges.
The Number of Women Employed in the Construction Industry Increased to Over 1.28 Million in 2022
The same HBI report reveals that the number of women employed in the construction industry reached 1.28 million in 2022.
In other words, women currently account for 10.9% of the construction workforce.
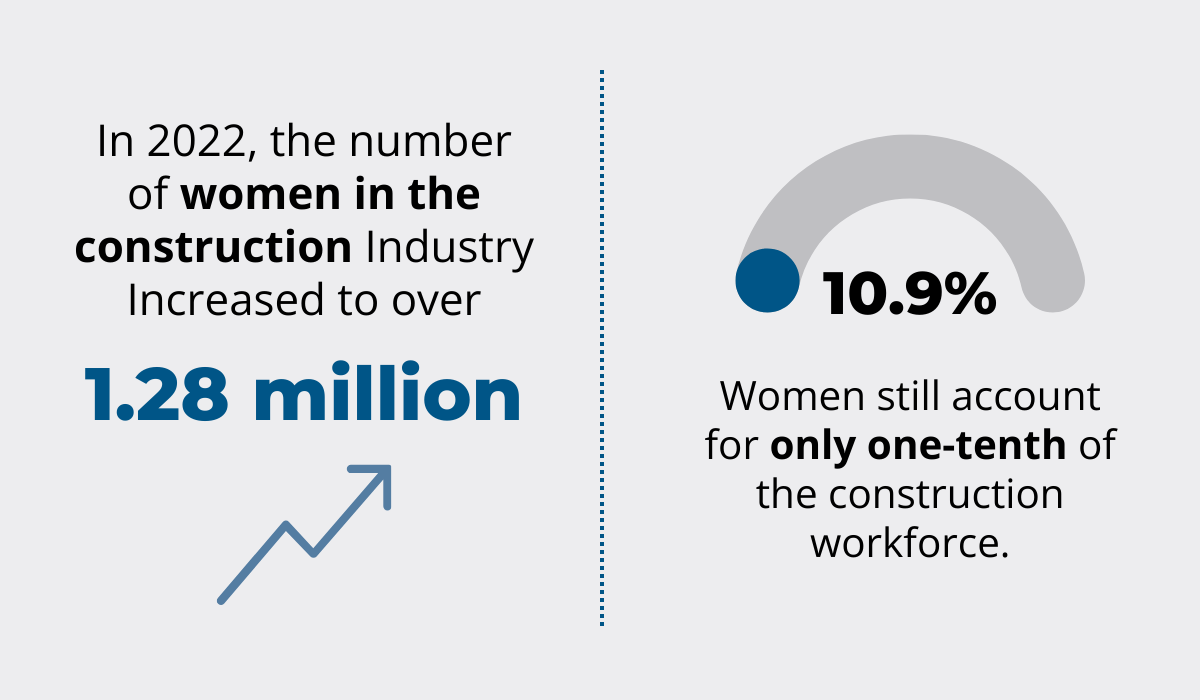
This recent boom is in sharp contrast to 2010 and the dismally low 807,000, when the Great Recession cut the female construction workforce by 30%.
Given the ongoing labor shortages, the growing pool of female workers represents an untapped potential for the future.
Currently, most women in construction occupy positions related to office, administrative support, management, business, and financial operations.
Meanwhile, only 4% of women hold occupations experiencing the greatest shortages.
As such, companies that invest in attracting female workers into high-demand occupations are sure to gain a significant advantage over the competition.
Project Delay Risks Statistics
Project delay risks often arise as a result of different construction risks, including the three groups we’ve explored so far.
As such, the failure to manage project delays usually carries grave consequences.
88% of Construction Firms Reported Experiencing Project Delays In 2021
Nearly nine out of 10 firms reported suffering project delays in 2021.
The reasons for the delays varied, but included longer lead times or material shortages, labor shortages, and administrative delays.
Three-quarters (75%) of respondents cited materials shortages as the primary cause of delays, reflecting the context of the pandemic.
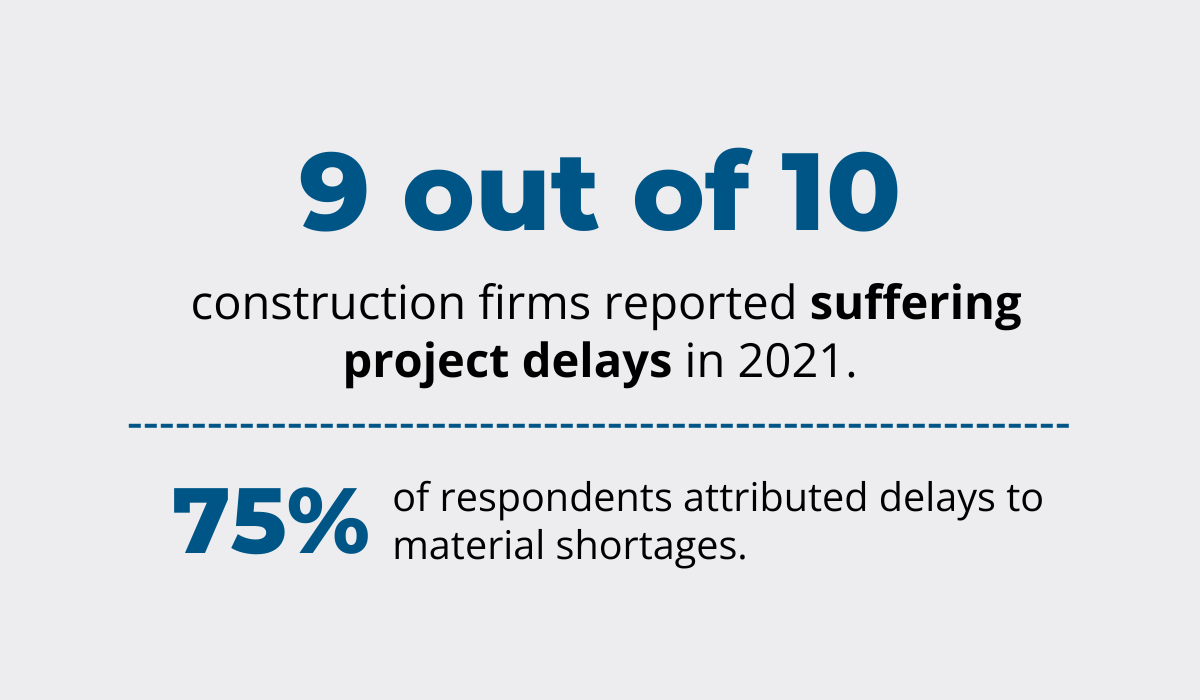
What’s more, the resulting uncertainties made many of the construction firms skeptical about their ability to make a full recovery in the upcoming months, if ever.
Consequently, the new normal of dealing with uncertainty and the constant risk of delays, led to agility becoming—and staying—a top priority for businesses today.
In 2022, Construction Jobs Were Delayed 46.8 Days on Average
According to proprietary data of Buildertrend’s customers, construction jobs were delayed 46.8 days on average in 2022.
This delay doesn’t seem as significant until we put things into perspective by comparing these numbers with 2021.
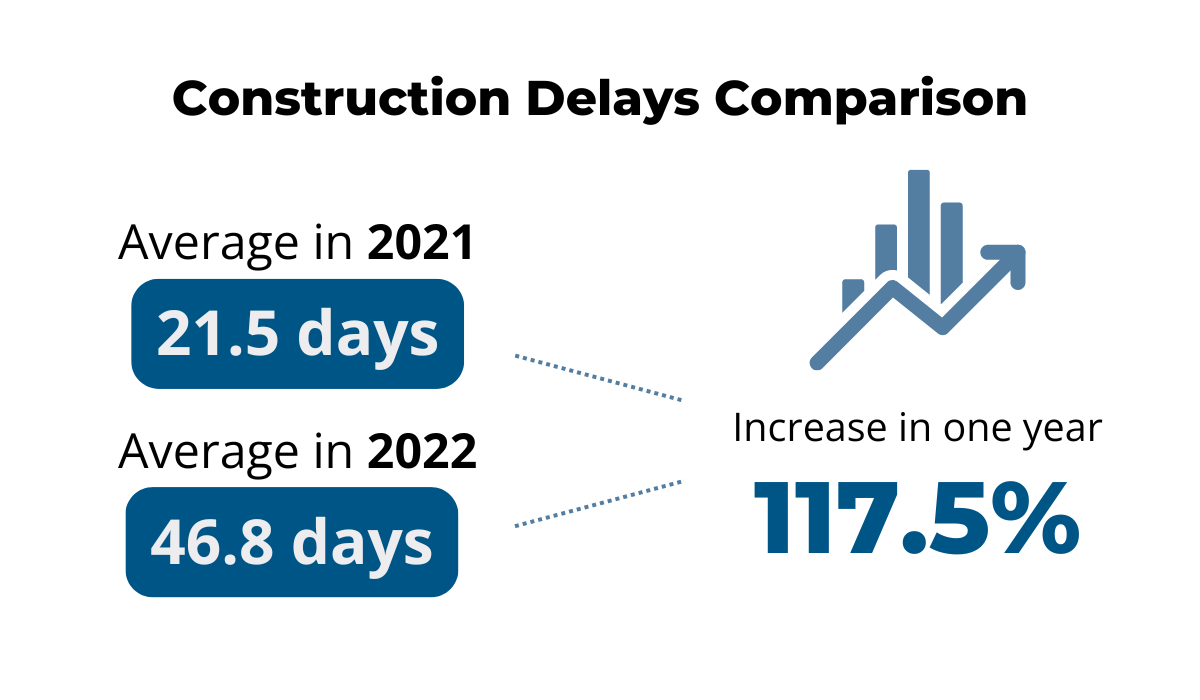
As the report states, the 117.5% increase year-over-year came as a result of different challenges that hit the industry in the aftermath of the COVID-19 pandemic.
Supply chain disruptions, in particular, created huge construction delays.
Buildertrend analyzed which materials created the most significant delays by comparing the 2019 and 2022 numbers, as seen in the table below:
MATERIAL | AVERAGE DELAY | INCREASE (2019) |
---|---|---|
Siding | 17 days | 183.3% |
Windows | 13 days | 333.3% |
Doors | 12 days | 200% |
Framing | 10 days | 233.3% |
Roofing | 9 days | 200% |
So, how can construction companies overcome supply chain issues?
Handling supply chain disruptions is crucial for ensuring efficient material management.
Given the new, uncertain reality, companies need to plan ahead and be ready to review and adjust their construction material management processes if and when necessary.
31% of Projects Have Been Delayed Due to Construction Crime
Out of all the projects explored through BauWatch’s report, construction crime helped delay nearly one-third of them.
Of that figure, a quarter of respondents experienced delays of over four weeks, causing considerable disruption to construction timelines.
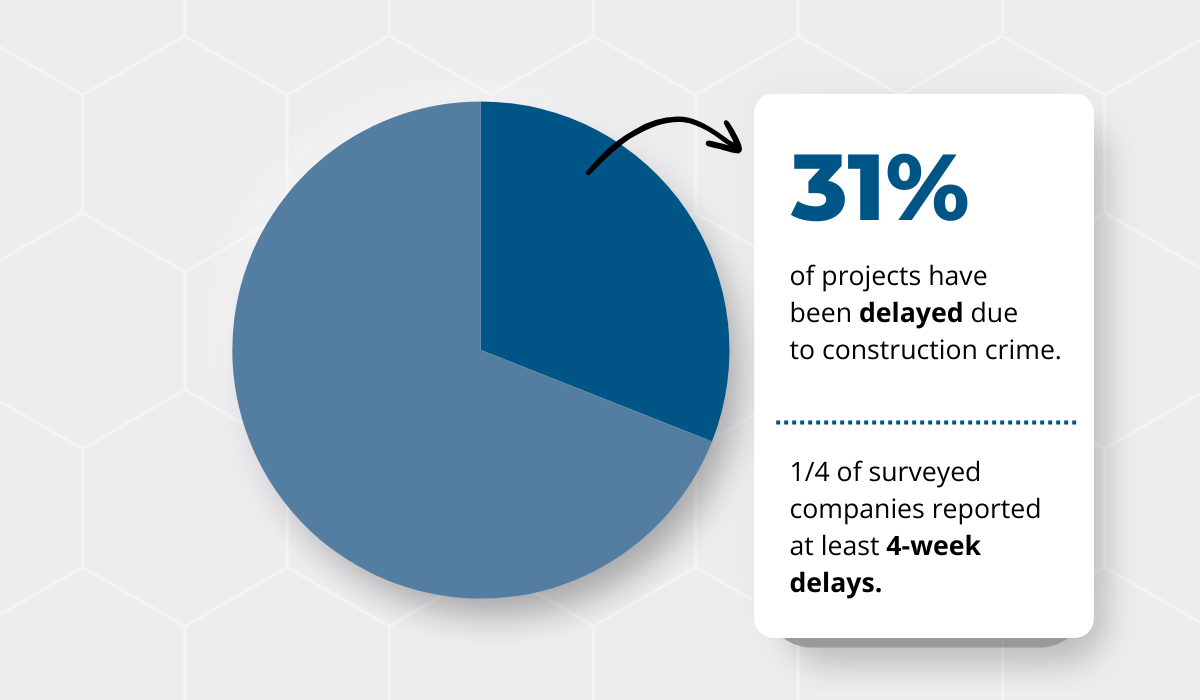
Annabel Hiatt, Senior Category Manager at the UK’s largest supplier of building materials, Travis Perkins, highlights that even the smallest incident can have devastating effects depending on the context.
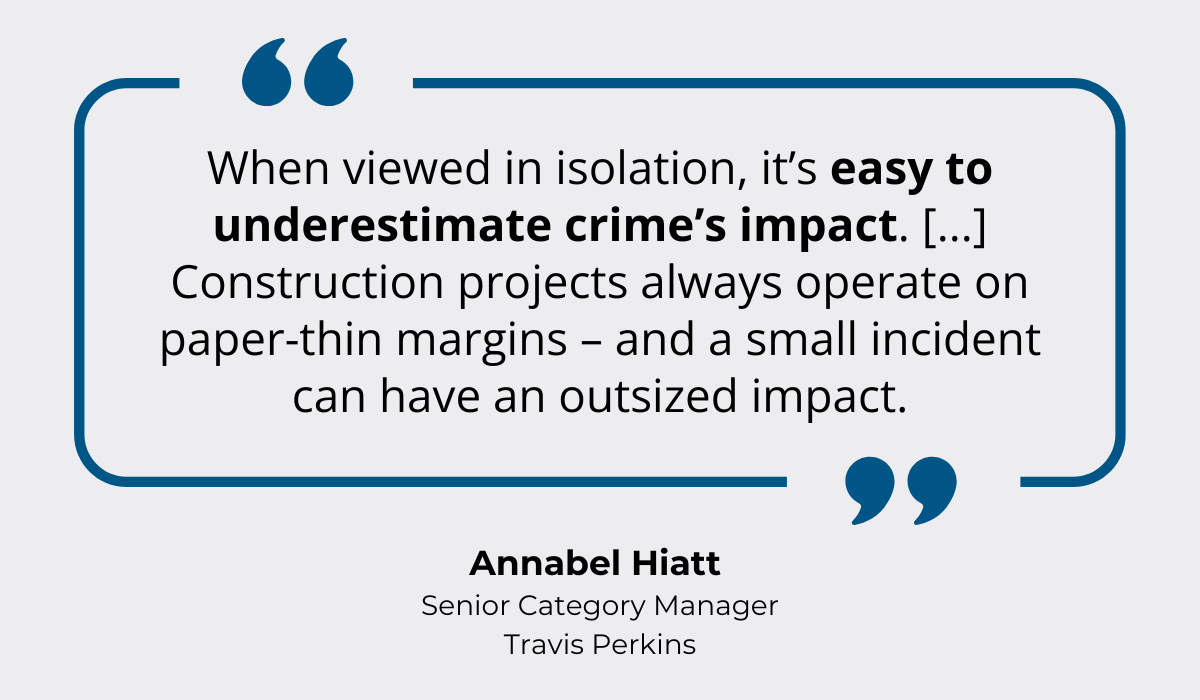
The data confirms this: in 1 of 10 cases, construction projects could not continue at all.
In the end, bolstering your security system will certainly cost money.
However, deciding to invest upfront helps mitigate immediate and additional construction theft risks, thereby cutting costs in the long run.
Conclusion
Construction risks vary in scope and nature, but they tend to shift and merge all the time.
This creates a messy setting that can be difficult to navigate. However, having a roadmap of different insights can help you in those efforts.
We trust that this statistical overview helped you pinpoint some essential concerns and chart the best route to propel your company forward.
Remember: you can’t anticipate every difficulty, but a good understanding of key construction risks will help you stay nimble and prepared for anything that may come your way!