Keeping track of equipment utilization increases productivity and overall efficiency, ensuring your business remains successful and competitive.
Although each company operates in a distinct setting and has different requirements, there are some dependable metrics you can always lean on to gain invaluable insights.
Determining the best usage parameters and course of action is up to you, but if you’re a business owner or an equipment manager looking for reliable guideposts, this article is for you.
In this article...
Key Takeaways:
- Tracking the utilization rate helps identify underutilized assets and optimize equipment usage for better productivity.
- Monitoring operating hours is crucial for scheduling timely maintenance and avoiding costly unplanned downtime.
- By reducing idle time, some companies save $400,000 per year.
Utilization Rate
If you want to know when, where, and how productively you use your equipment, calculating its utilization rate is the best starting point.
There’s a simple formula for capturing the equipment utilization rate (EUR), and the only thing you need are these two figures:
- Run Hours
- Available Hours
Comparing your machinery’s active run time with the number of hours that it was available gets you the utilization percentage.
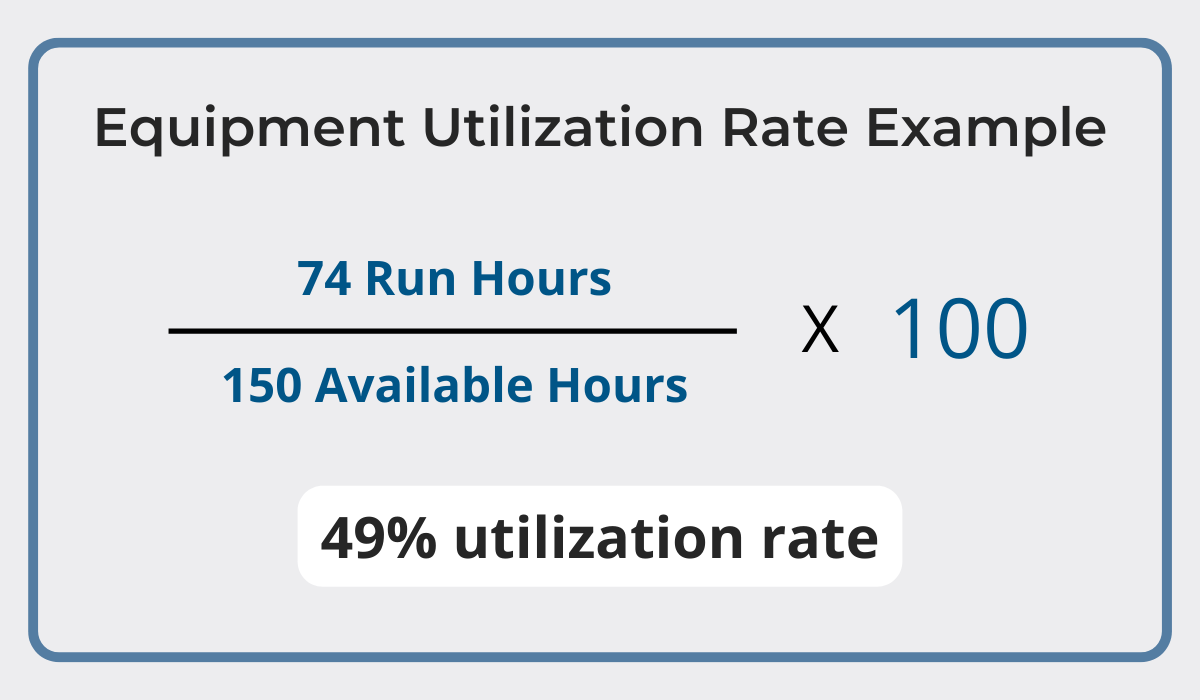
While the EUR formula itself is simple, it’s essential to remember that it’s only as good as the numbers it’s fed.
If you’re not tracking actual operating hours and available time accurately, you won’t be able to pinpoint underutilized assets.
Naturally, interpreting the numbers correctly is just as important, so let’s take a closer look at our imagined scenario.
If a piece of equipment has 49% EUR, it may lead us to conclude that it’s used poorly and nowhere near its full potential.
After all, construction companies should aim for a 100% equipment utilization rate, right?
Well, not exactly.
What constitutes a “good” equipment utilization rate varies across companies and industries.
For construction, this can also be observed in terms of job site assignments.
Companies with a lot of machinery will inevitably have some assets unassigned to projects, sitting in the yard.
This is not necessarily a bad thing if the ratio is around 70/30 for used equipment. It also supports regular equipment maintenance.
The bottom line?
Understanding the equipment utilization rate requires you to keep in mind both the industry standards and the circumstances of your company.
Operating Hours
Easily the most straightforward metric on this list, operating hours reflect the total number of hours equipment spends in use.
There are many reasons why companies pay close attention to operating hours, and benchmarking the lifespan of an asset is one of them.
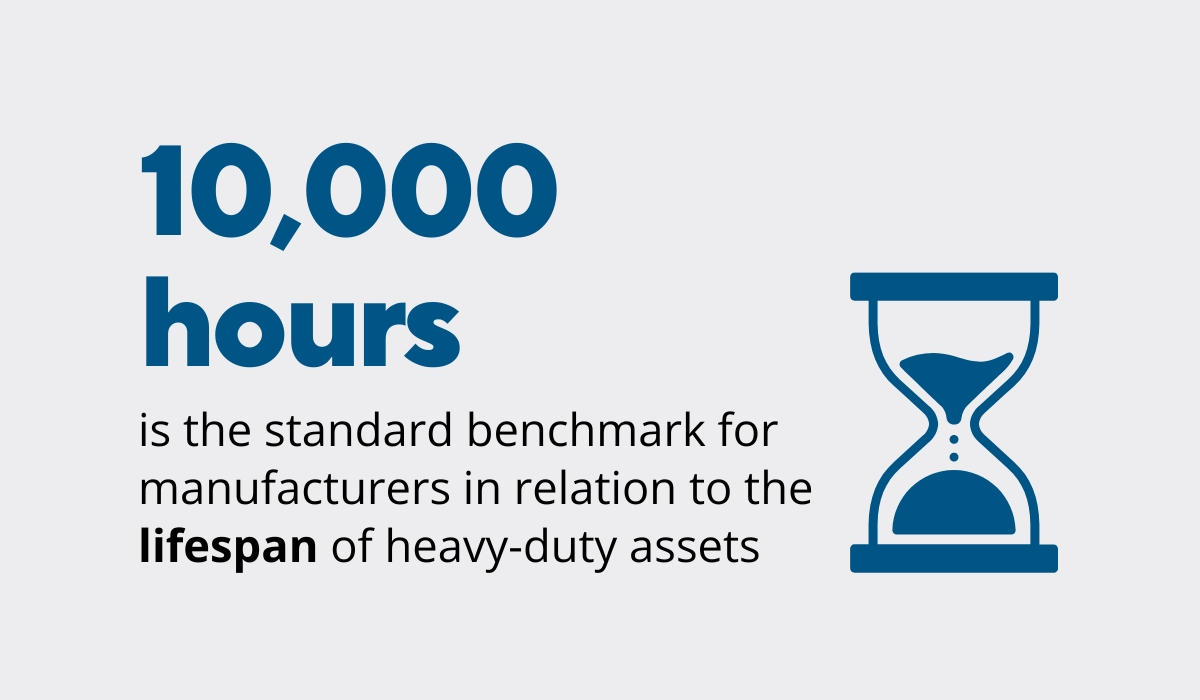
Different pieces of construction equipment have different lifespans, but one thing remains unchanged: assets lose their functionality with time and use.
Underutilized equipment tends to draw more attention, but overutilization is just as big of a problem, if not even bigger.
Regardless of whether we measure the time in years or hours, high asset utilization carries the risk of premature wear and tear, and ultimately equipment breakdown.
Companies that aren’t attentive and precise enough in logging their equipment’s operating hours risk offsetting their productivity gains by incurring extra costs through emergency repairs and unplanned downtime.
Operating hours can be calculated daily, or as a part of weekly reports, but the key is to identify potentially harmful utilization trends and schedule maintenance on time.
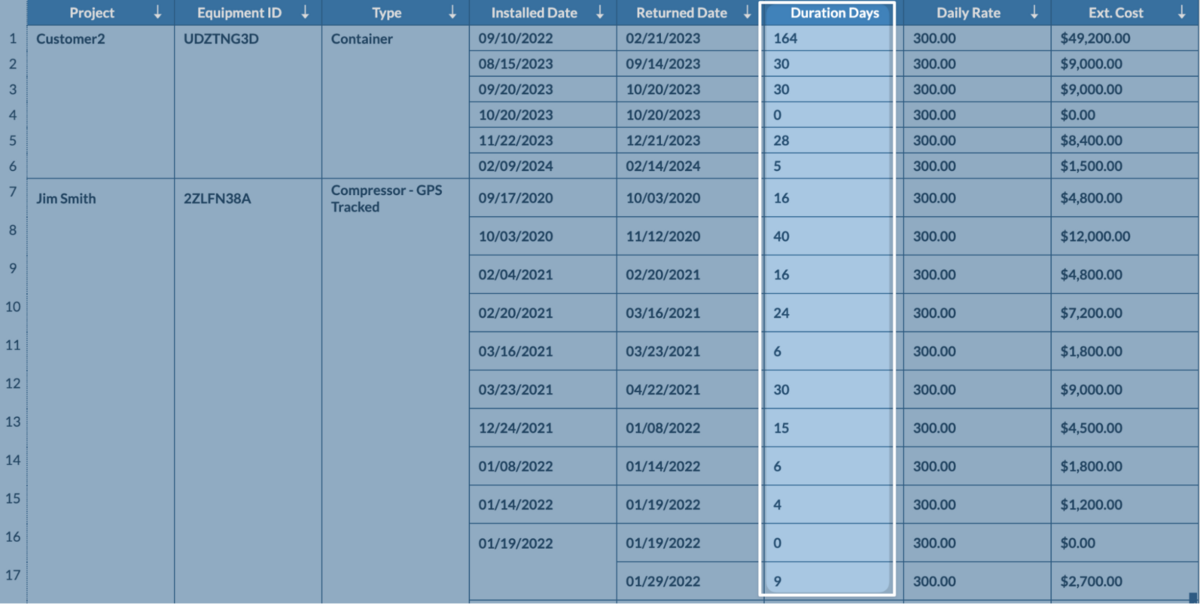
And it’s not just about avoiding catastrophic failures.
There are different types of maintenance programs or strategies, but more and more businesses recognize the benefits of regular tracking and data-driven decisions for achieving high productivity.
Equipment Productivity
Equipment being used is one thing, but how efficiently you use it is another. That’s where the equipment productivity comes into play.
And moving to improve the productivity rate is always worthwhile.
Construction businesses can boost their equipment productivity in several ways, taking into account multiple factors that impact overall productivity levels.
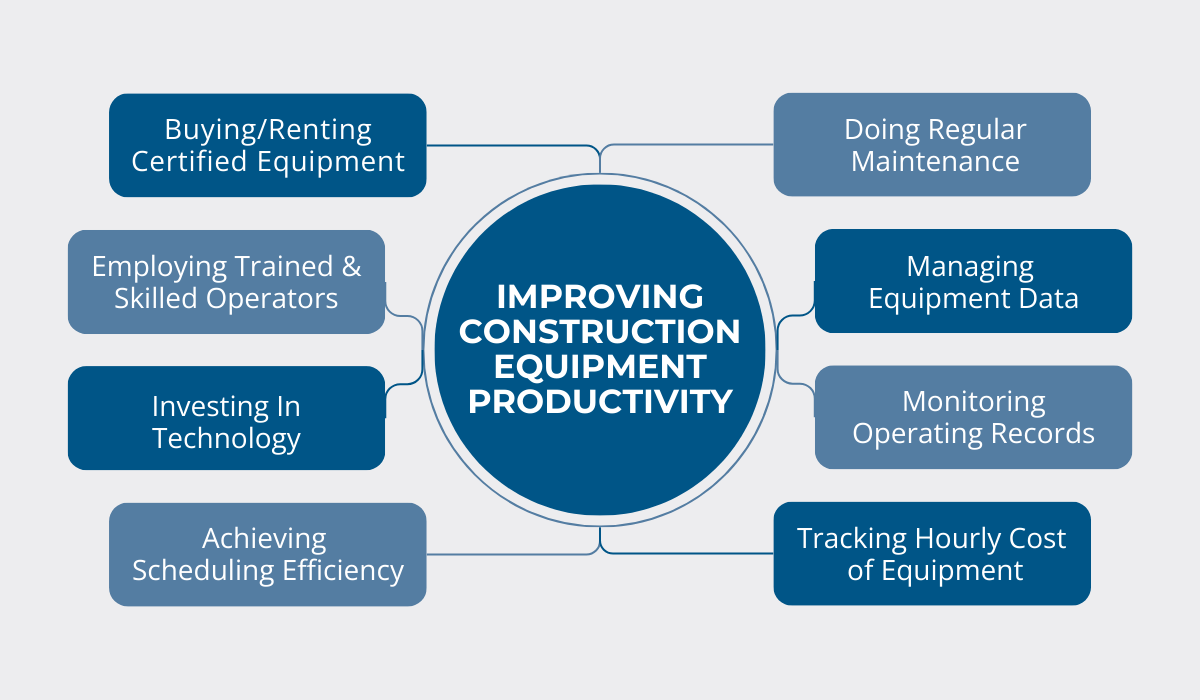
This process typically involves buying or renting high-quality equipment, maintaining it regularly, having skilled operators, etc.
Nevertheless, staying on top of equipment operating records and being efficient with scheduling should be given special attention.
Vigorous tracking allows you to capture key data, including equipment productivity rate.
Nevertheless, to make use of these insights, you need to be aware of standard productivity rates for different equipment.
A construction consulting firm, Planning Engineer, shared a helpful compilation of standard productivity rates for common earthmoving equipment, as illustrated in the tables below.
BULLDOZER | Productivity Rate m3/hour |
---|---|
Excavating only & haul in pile by 75 Horsepower (75) Dozer, 15 meters haul |
|
*If the Dozer is 200 HP | Multiply productivity by 2.3 |
*If the Dozer is 700 HP | Multiply productivity by 13.44 |
It should also be noted that the advent of new tech, and improved equipment design, have led to higher productivity rates over time.
As such, these numbers create only a baseline for comparison.
EXCAVATOR | Productivity Rate m3/hour |
---|---|
Small excavators (1-5 tons) | 10 to 20 m3/hour |
Medium excavators (6-10 tons) | 20 to 40 m3/hour |
Large excavators (11-50 tons) | 40 to 100 m3/hour |
Heavy-duty excavators (50+ tons) | 100 m3/hour |
Remember: there are additional factors that impact equipment productivity rate, from material types and operator experience to equipment modifications and attachments.
Location Tracking
Location tracking grants you the means to identify various process inefficiencies and bottlenecks in a hassle-free way, optimizing logistics and improving your overall operations.
You might finally reduce idle time, the universal bane of the construction industry, and clear the way for the effective deployment of assets across multiple sites.
Asset tracking comes in many flavors, but tracking GPS locations in real time with telematics grants you the most powerful insight due to its 24/7 visibility across the globe.
One such complete solution is our very own asset-tracking software GoCodes Asset Tracking.
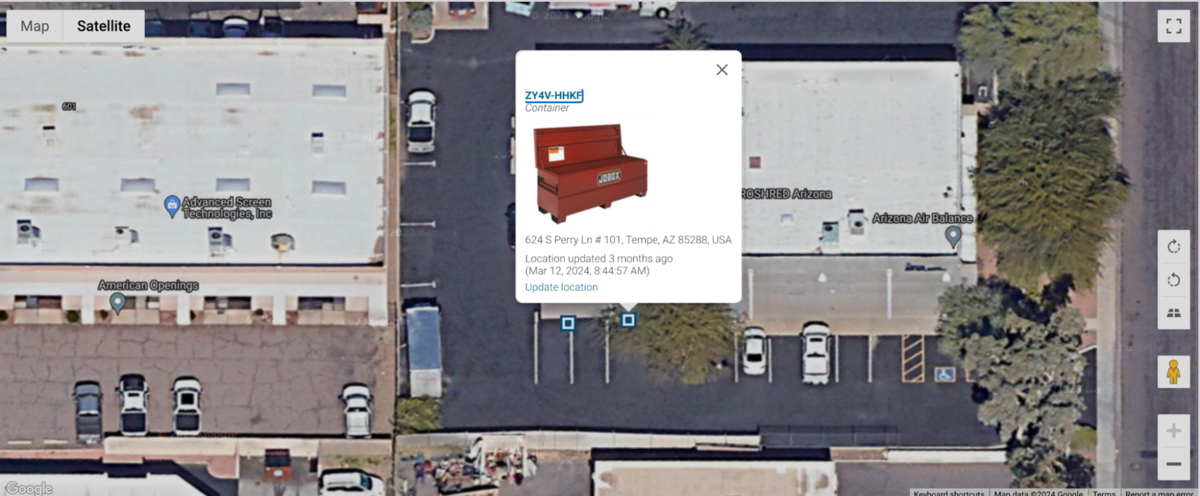
In a nutshell, GoCodes Asset Tracking leverages real-time GPS tracking and advanced technologies like geofencing to easily pinpoint an asset’s location, also creating immediate alerts in case of unauthorized use or potential theft.
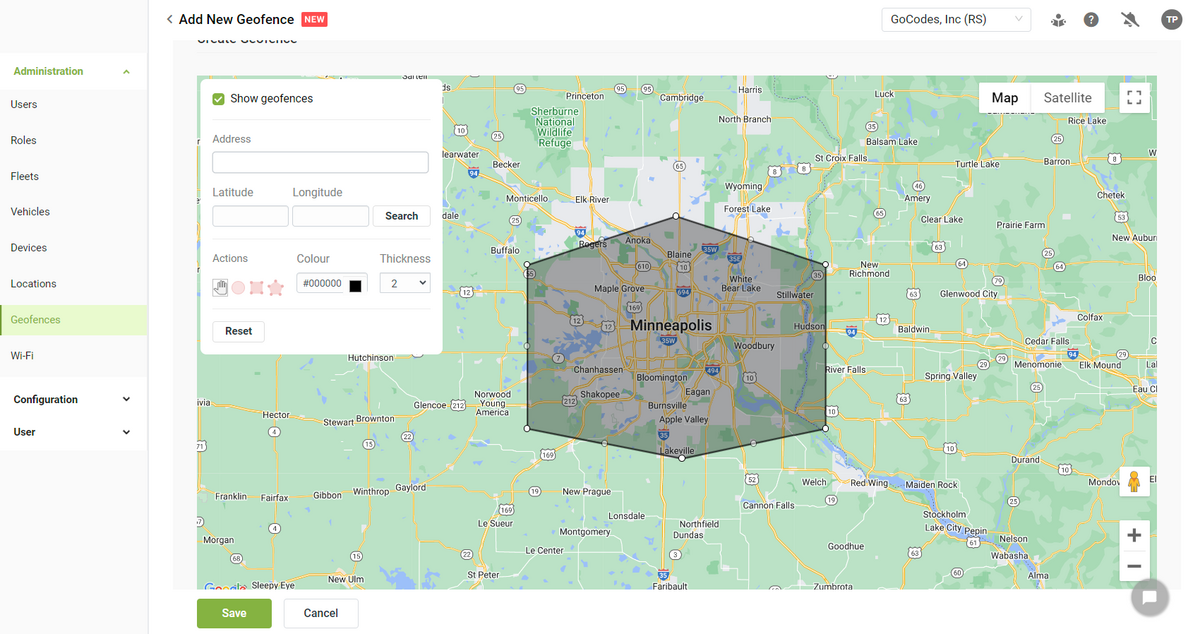
Keeping track of specific usage trends adds another layer of benefits, propelling operational efficiency and equipment utilization further.
Being able to fully understand your equipment’s movement while capturing a wealth of data, such as vehicle speed, fuel consumption, and travel time, creates the basis for major improvements, which brings us to our next metric.
Fuel Usage
Tracking the exact amount of fuel consumed by each piece of equipment is something to be vigilant about.
Fuel consumption and related wear on equipment add up very quickly, and the surging costs of diesel, which powers over three-fourths of all heavy construction equipment, are not helping the situation one bit.
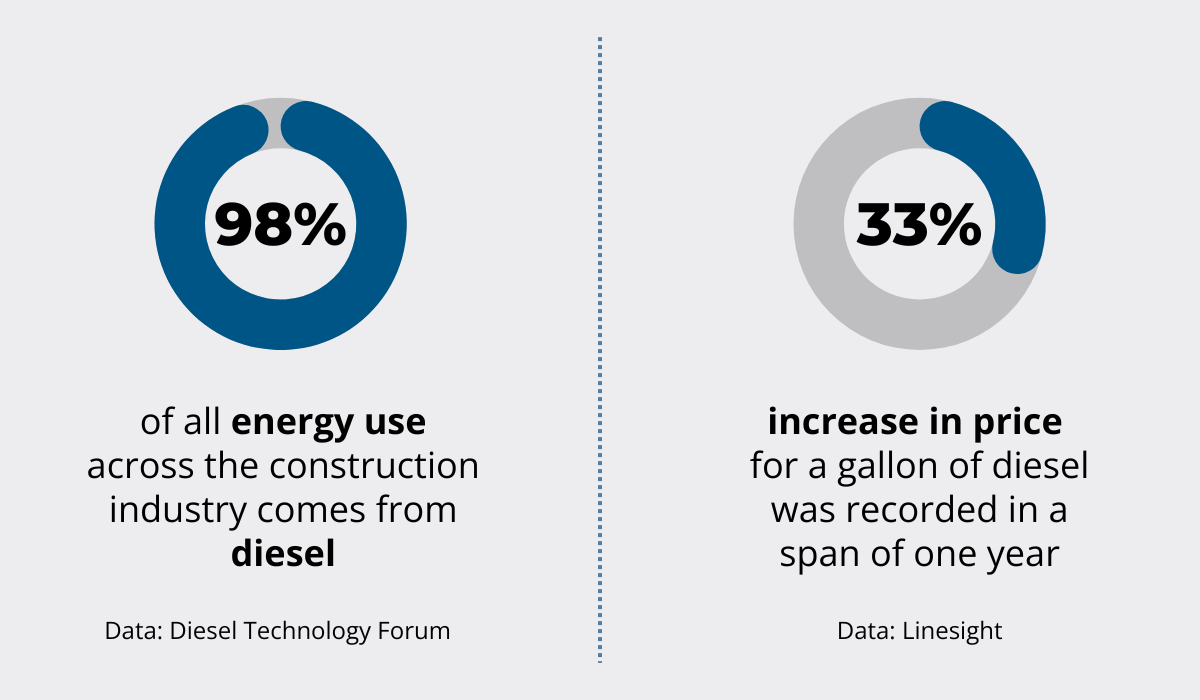
Together, DTF’s findings on diesel prevalence and Linesight’s 2022 Report indicate just how easily fuel prices can impact companies’ financial health.
However, the detrimental effects of inefficient fuel usage are complicated further by the construction industry’s substantial carbon footprint.
The efforts to reduce fuel waste are spurred on by both the prices and stricter regulations regarding CO2 emissions.
Karli Anderson, an executive of a construction materials company, Summit Materials, concurs.
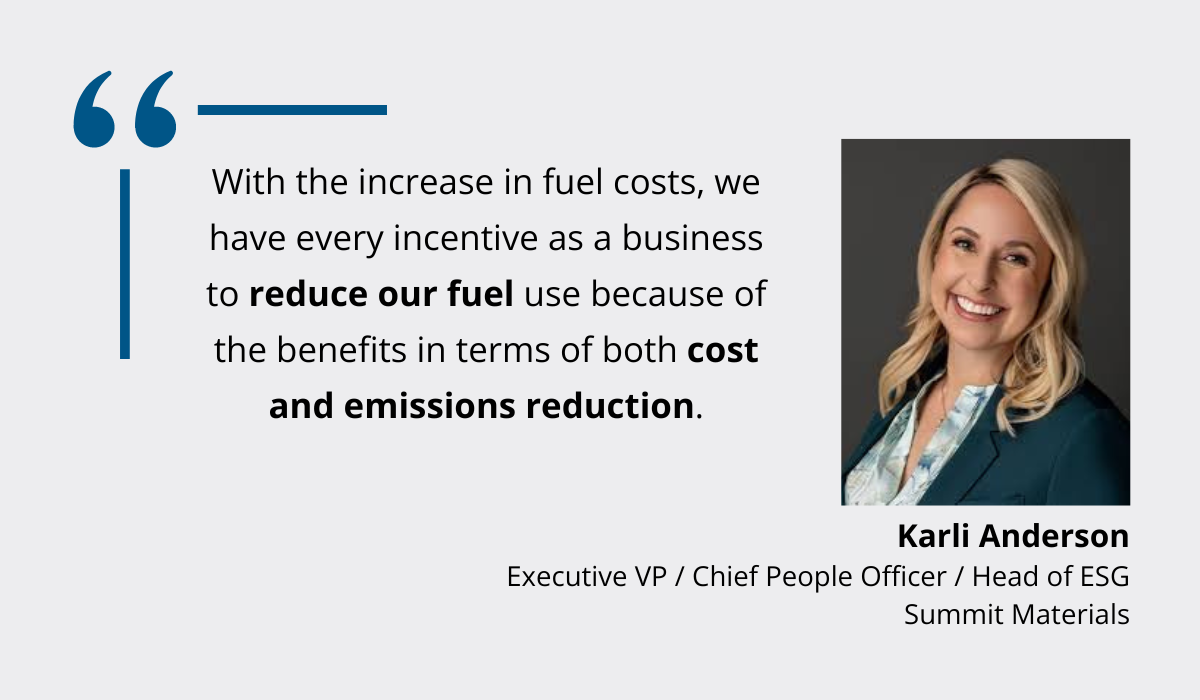
For Summit Materials, identifying opportunities for cost savings and environmental impact was made easier with technology.
Namely, relying on real-time fuel consumption data resulted in the company “saving approximately $1.8 million per year on fuel costs.”
Fuel usage and mileage metrics can also help pinpoint equipment damage well before these serious issues become fully apparent.
We’ll cover these maintenance issues in greater detail in the final section of this article, but first, let’s take a look at idle time.
Idle Time
Idle time metric refers to the amount of time the equipment is not in use while on-site.
Leaving the engine running while a related task is being completed or something is being loaded is not an uncommon sight in construction.
John Bartz, Director of Product Assurance and Regulation at Volvo Construction Equipment, explains that some conditions mandate idling, but they encourage minimal idling in the company.
The reasons for this extend beyond the costs of fuel and paint a pretty compelling picture.
Here’s a quick list of why to avoid idling:
- Creates extra wear and tear
- Incurs additional maintenance costs
- Adds hours, impacting equipment’s resale or trade-in value
Craig McGinnis, Senior Smart Quarry Manager at Komatsu America, emphasizes one of the most common scenarios.
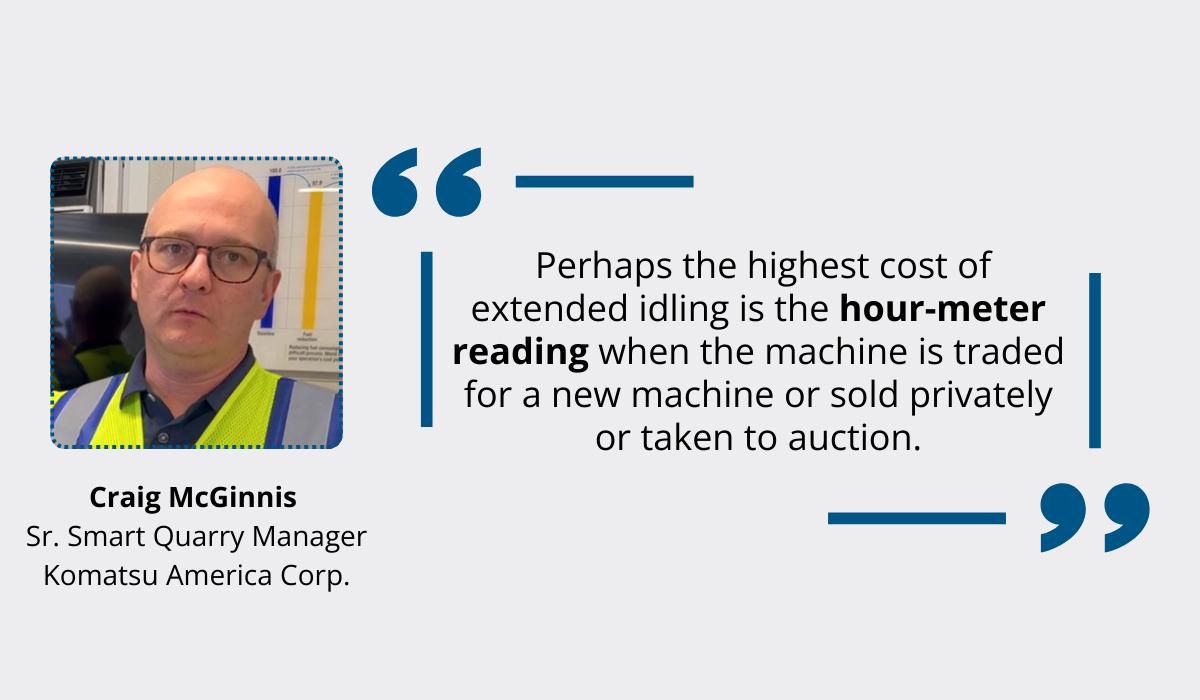
McGinnis notes that careless idling drastically devalues equipment because the extra hours spent idling show up in the hours’ log, creating the impression that a piece of machinery is more worn out than it is in reality.
Maximizing efficiency on-site goes a long way. The better the initial planning and efficiency of operations, the less time there is for the assets to stay idle during their active hours.
Also, since there is a natural tendency to keep the machinery running, it’s important to educate operators on the reasons and strategies for avoiding idling.
Equipment Manager at Emil Anderson Construction, James Boydell notes that the practice adopted by his company dictates turning off engines after 3 minutes of idle time.
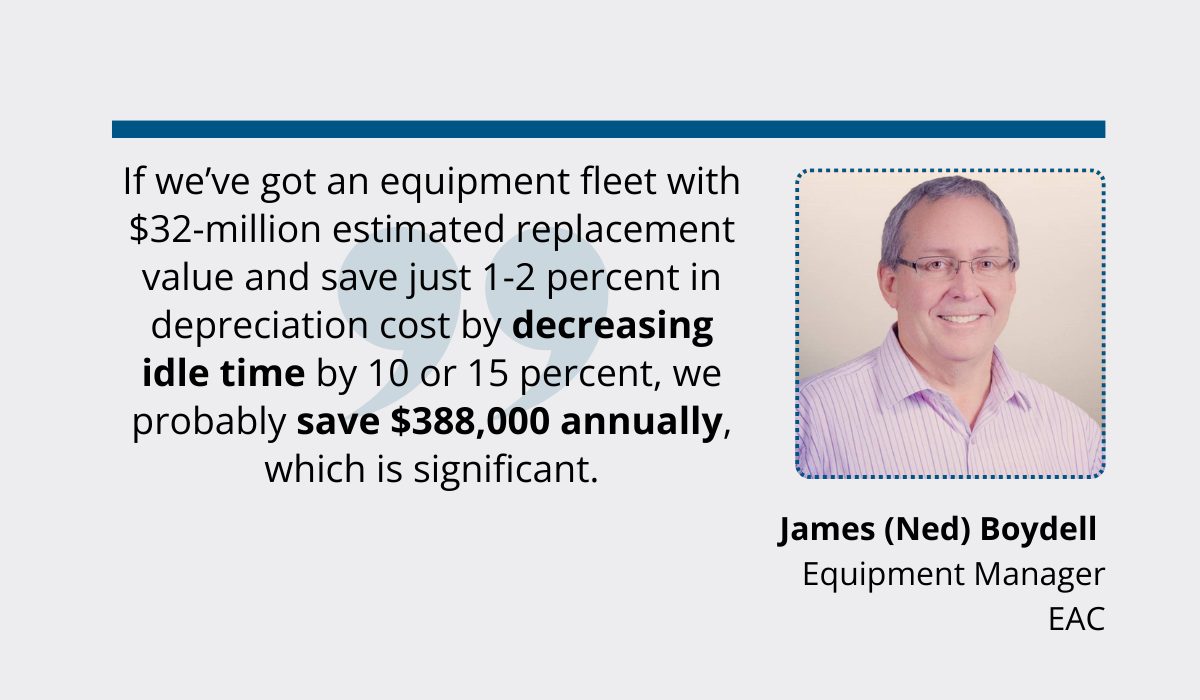
As Boydell writes, the effect of decreased idle time is evident in the annual savings of close to $400,000, creating a strong incentive to track this aspect of equipment utilization as well.
Similar but different to idle time, unplanned downtime is another key metric for tracking equipment utilization.
Unplanned Downtime
If you’re experiencing unplanned downtime, your equipment is out of service due to maintenance or repairs.
Equipment downtime is the percentage of time lost from the planned operations, and you should calculate it for your company.
Ideally, unscheduled downtime shouldn’t exceed more than 10% of the total working time.
Higher figures than that indicate problems with production or maintenance.
Since unplanned downtime occurs due to process inefficiencies, tracking and minimizing it leads to elevated productivity and major cost savings.
A recent survey by industrial technology giant ABB shows just how devastating downtime can be for businesses.
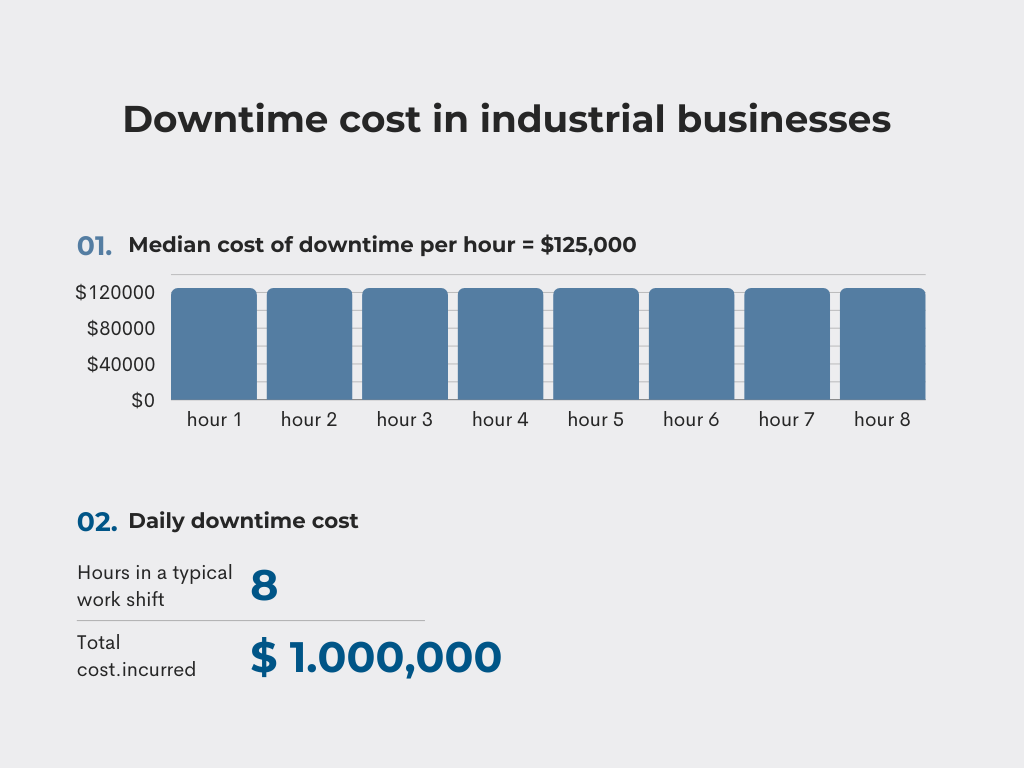
The findings also underscored the crucial role of maintenance and equipment reliability, with 92% of respondents reporting that it increased their uptime in the past year.
Similarly to the previously mentioned EUR formula, to calculate downtime you need only divide the time that the asset was down with planned operation time, and then multiply that by 100.
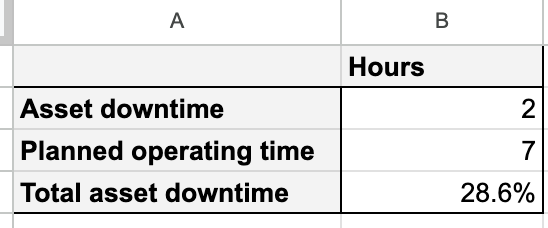
Once you’ve calculated the percentage of lost time, you can add additional insights such as downtime frequency.
The best way to counter downtime is through timely, preventive, or predictive maintenance, as opposed to waiting for more serious errors and risking the total breakdown of equipment.
Conclusion
For equipment utilization to be as effective as possible, keep track of different metrics presented throughout this article.
Companies that do so get invaluable productivity insights that maximize their overall success.
Whether you want to make your equipment more productive, or reduce fuel consumption and idling, capturing data will enable you to make smarter decisions.
The best advice we can give you is: start tracking things!