As the heartbeat of any construction endeavor, takeoff involves quantifying and calculating all the resources needed for a project, from raw materials like granite and lumber, right down to the last nail.
Therefore, material takeoff isn’t just a checkbox in project management, but the foundation for successful project completion.
That’s why we decided to dedicate an entire article to best practices in this indispensable stage of project planning.
Our comprehensive guide delves into specific examples, offering valuable insights and practical tips and tricks, all geared towards a singular objective—enhancing the efficiency and precision of your material takeoff process.
Read on to learn more.
In this article...
Thoroughly Review All Construction Documentation
Project documentation serves as a foundation for gaining a comprehensive understanding of the job at hand, offering valuable insights into its scope, requirements, and design specifics.
As such, it stands as an indispensable tool in the arsenal of any proficient estimator.
Construction estimators know that, without plans and blueprints, accurate takeoffs would be unattainable.
They also know that imprecise takeoffs pose significant risks for the entire project, including:
- Unplanned downtime
- Delays
- Disputes with clients
- The need for redesign
- Reputational damage
- Budget overruns
Imagine a scenario where a project calls for a specific material, yet an estimator fails to examine the specifications and excludes the item from the takeoff.
Consequently, the material is never ordered, and the oversight goes unnoticed until the construction team needs it.
At this point, there’s not much that can be done, except to hurriedly order the missing material and wait for its delivery.
This not only incurs additional costs but halts work as well—arguably two of the most undesirable outcomes in construction projects.
Such scenarios are preventable, though.
All it takes is dedicating a bit of time to review relevant information that can be found in plans, drawings, and blueprints.
Below, you can see a brief overview of various document types that can be of use to you during takeoff.
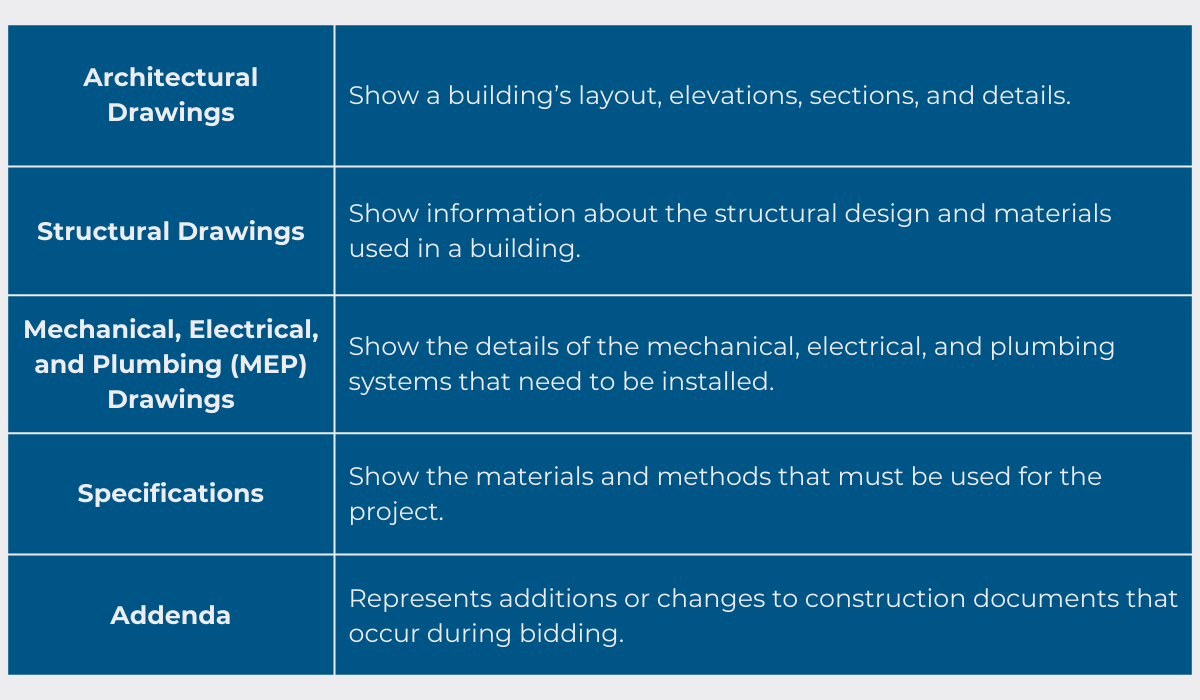
If your goal is to step up your takeoff game, prioritize a thorough analysis of these documents before quantifying materials.
Now, although this may seem obvious enough, we still need to emphasize the importance of knowing how to read and interpret construction plans.
Takeoff is not the time for guesswork.
If plans appear confusing to you or something seems amiss, never hesitate to seek clarification from the architect or other stakeholders.
Remember, these files constitute the bedrock of your assessment, and any lack of clarity may compromise the quality of your work.
Therefore, commit to understanding and interpreting construction documents accurately and meticulously to ensure successful project outcomes.
Double-Check the Accuracy of Measurements
On a related note, it’s also advisable to double-check the accuracy of measurements for all project components in order to minimize errors.
Unfortunately, in the world of construction, a single mistake during the early stages of construction planning can set off a cascade of issues down the line if left unaddressed.
Inaccurate measurements can easily lead to imprecise takeoffs, resulting in various complications that impact the client’s satisfaction, the project’s profitability, the integrity of the structure, as well as the safety of the workers.
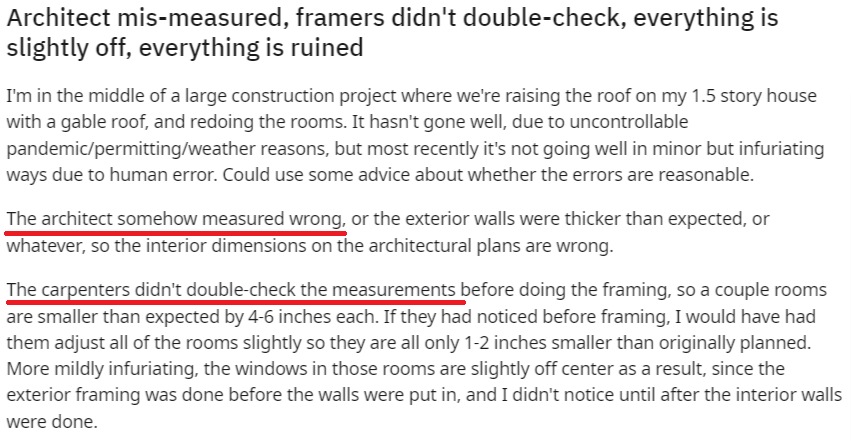
In short, bad data translates to bad outcomes, for everyone involved.
So, don’t look at this step in the takeoff process as a waste of time.
On the contrary, it’s far more time-efficient to thoroughly verify all information in the documents now, rather than leaving it to chance and facing repercussions later.
George Nicola, interior designer at TALLBOX Property, echoes this sentiment, too.
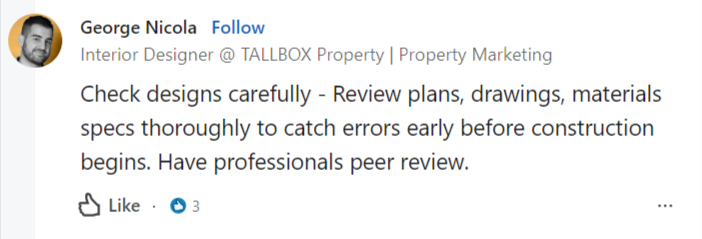
He also raises another good point, and that’s the importance of cross-verifying measurements with others, whether they are peers, designers, or other stakeholders.
The more sets of eyes review the plans, the greater the likelihood of identifying these costly errors, if they exist.
At the end of the day, collaboration is a pivotal factor in construction, not only for error detection but also for the overall success of projects.
This is precisely the focal point of our next section, so let’s dive in.
Collaborate with Project Stakeholders
Construction material takeoff is fundamentally a collaborative effort, so there’s really no room for silo thinking during this process.
Without effective collaboration, it becomes challenging to stay on top of changes in the plans, which, in turn, prevents you from doing your job efficiently.
Say a developer wants to switch from vinyl windows to fiberglass ones at the last moment but fails to notify you.
The consequence?
The oversight leads to an omission in the takeoff, and the windows remain unaccounted for in the procurement process.
According to Sameer Merchant, chief technology officer at Wheel, lack of transparency has always been a big issue for material takeoffs.
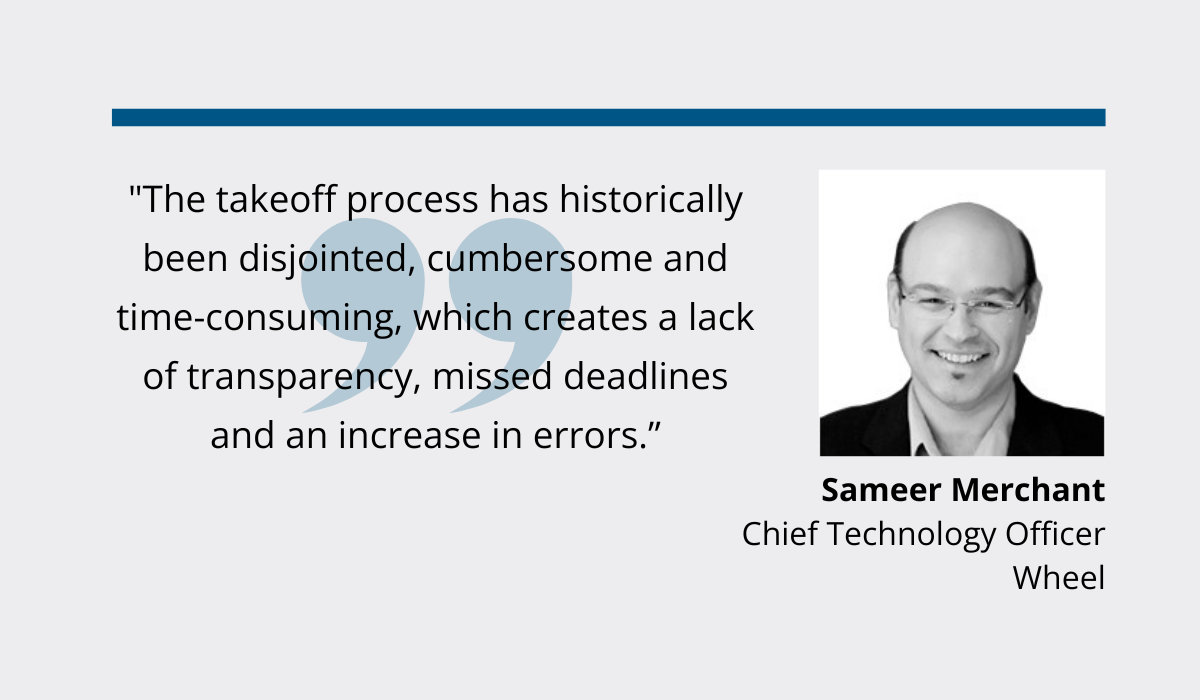
Given the inherent complexity of construction projects, it’s often difficult to keep up with all the alterations in designs and plans, or even to clarify any ambiguities, which results in inaccuracies during takeoffs.
To address this challenge, maintaining regular and efficient communication with fellow project team members is imperative.
Fortunately, contemporary tools make this task more accessible than ever.
Thanks to technological advancements, a myriad of digital collaborative solutions tailored for construction professionals now exist.
These systems enable you to communicate with stakeholders, share relevant data, collaboratively comment on drawings, make corrections, and more—all in real time.
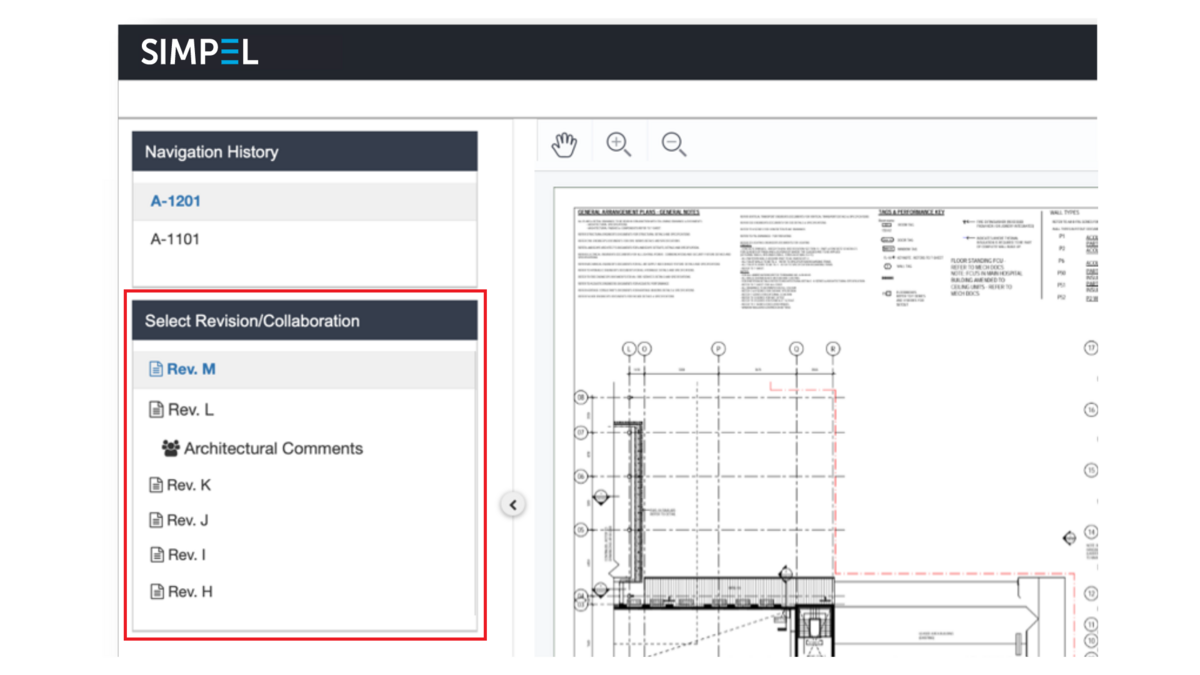
This ensures constant connectivity with everyone involved in the project, so you can be confident that the data used for your estimations is always up-to-date.
In the grand scheme of things, material takeoffs aren’t a solitary endeavor.
So why not embrace the tools that allow you to leverage the expertise of other project team members and ensure accurate and timely results?
Update Takeoff Documents Regularly
As corrections and modifications unfold throughout the project planning phase, it’s important for you to simultaneously keep your takeoff documents fresh.
In other words, if there are alterations in project requirements or shifts in the scope of work, you should ensure that material quantities match these changes.
After all, quantity takeoffs serve as a reference guide for many different decision-makers involved in the construction process, so regularly reviewing and updating quantities based on project progress will result in:
- More accurate cost estimations
- More efficient resource allocation
- Optimal quality of the structure
- More effective risk management
Given that revisions are inevitable in practically any project, it’s best to establish a proactive workflow beforehand to stay ahead of the changes and manage your takeoff documentation more effectively.
For starters, consider specifying a regular update frequency for your files.
This can be, for example, after every change in the design.
When updates become part of your schedule or process, you’ll be more likely to prioritize them, reducing the risk of overlooking essential information.
Implementing an efficient version control system is another good practice in this context.
In the most simple terms, this is a system that helps you keep track of all the versions of your documents.
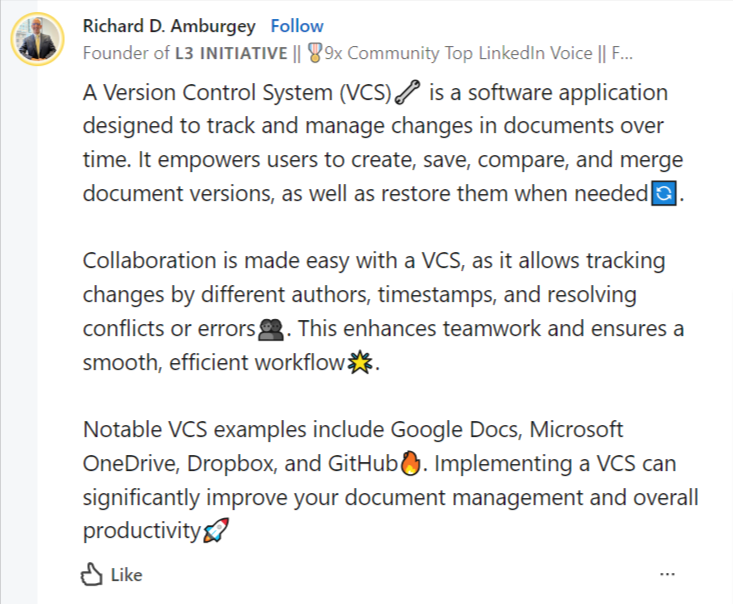
This not only provides the freshest data about the project but also preserves all original documentation as a reliable source of truth in case of disputes.
Overall, the repercussions of neglecting to update a single piece of information can be extremely detrimental to project outcomes.
Therefore, be prepared, keep an eye out for alterations, and have a robust system in place to promptly record and manage them.
Use Digital Takeoff Tools
If you want to expedite, streamline, and enhance the accuracy of your takeoffs, consider utilizing digital takeoff solutions.
Specifically designed for this purpose, they automatically analyze the plans you input and then calculate the required material quantities, all in a couple of moments.

In simpler terms, they perform tasks that you would otherwise have to do manually, but with more efficiency.
Now, you may feel like your Excel templates are doing a good enough job, and you just might be right. For now.
Realistically, manual takeoff tools like spreadsheets can take you only so far.
While they may suffice for smaller projects, their susceptibility to human error becomes more pronounced in complex, larger projects.
And it’s not like the ramifications of these errors are insignificant.

They can significantly impact projects in terms of time and financial resources.
Therefore, if you’ve noticed inaccuracies in your recent takeoffs, it might not be a reflection of your skills, but rather the method you’re using.
In that case, incorporating digital takeoff tools into your workflow just might prove to be the ideal solution for you.
However, don’t hastily buy the first software you come across.
Conduct thorough research, compare prices and features across different options, and make use of free demos to determine the most suitable choice for your needs.
Once you’ve identified the right system, take the advice of Ryan Lanser, president of the Affordable Site Model, and invest time in learning all the ins and outs of the software.
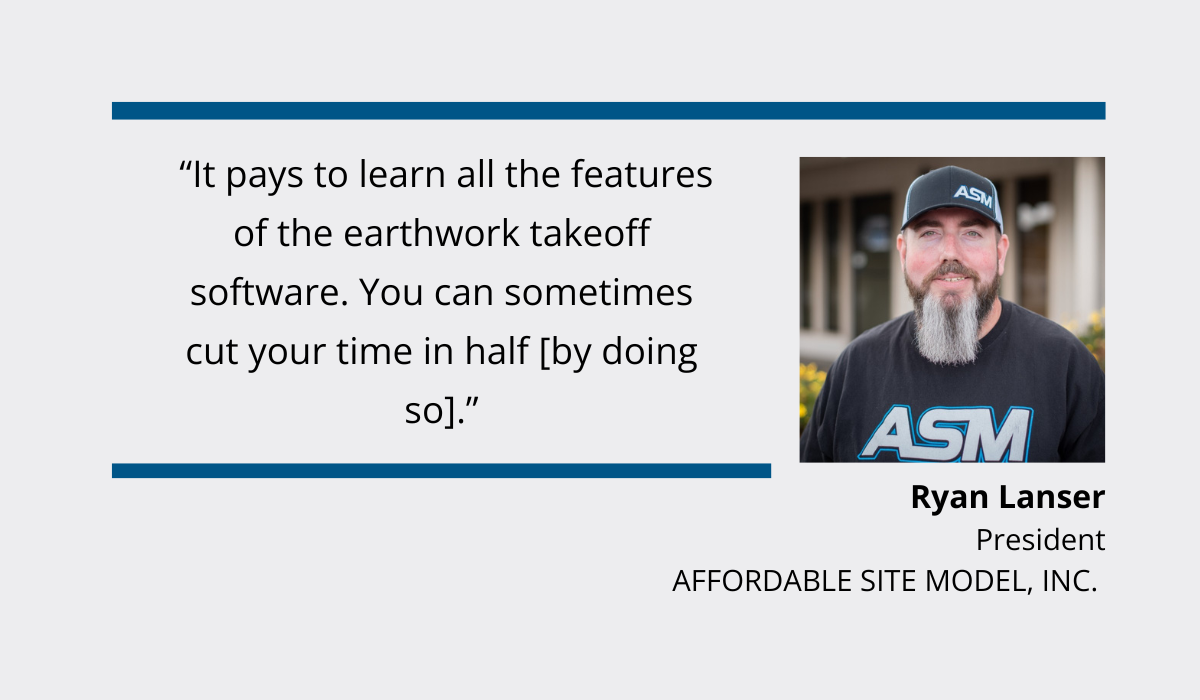
Familiarize yourself with hotkeys, templates, auto contours, and other features that can maximize the effectiveness of the system you’ve chosen.
This proactive approach ensures that you extract maximum value from your investment.
Conclusion
If this entire article could be summarized in three words, they’d be “thoroughness and precision”.
Top-notch construction estimators epitomize precisely these virtues.
They consistently strive to immerse themselves in the intricacies of every project, leaving no room for oversight.
As a result, their ability to forecast project material needs becomes akin to possessing a clairvoyant ability.
If you, too, want to reach such a level of proficiency, keep a vigilant eye on potential errors to mitigate risks, seek clarification from stakeholders when needed to prevent mistakes, and utilize the right tools to make the process easier.
With a consistent dedication to these principles, you will swiftly see improvement in both your takeoff accuracy and the overall success of the projects you are engaged in.