In construction, there is always something to spend money on, from administration, equipment and material procurement, to worker salaries, storage fees, and overhead costs.
Some would say it’s an inevitable part of doing business–after all, you have to spend money to make money.
But while operating costs may be unavoidable, you can also reduce them to remain profitable.
So, here are some tips on reducing operating costs in construction.
In this article...
Learn About Lean Construction
When they were first designed by Toyota after World War II, lean principles were intended to help companies produce quality products with less waste and improve production and business activities.
Nowadays, the methodology can be applied to numerous industries and sectors. But what is lean construction?
Lean construction (LC) is a method that helps construction companies recognize blind spots and take proactive steps to improve process efficiency and quality.
It is not a fixed set of activities companies can copy but a philosophy that encourages a holistic approach to entire business and production processes.
Simply put, lean construction stands as a framework with the following tenets:
Continuous improvement | Learning from past projects, and implementing new ways of doing things. |
Reduce waste | Ensuring there are no reworks, practicing effective scheduling to avoid downtime, and using just-in-time inventory management. In short, waste reduction applies both to physical waste, and time and work potential. |
Happy clients | All processes and activities should work to satisfy the end-user. |
Job satisfaction | Companies encourage workers to collaborate, share ideas, and have the freedom to solve problems. |
Basically, the principles will clearly define expectations and anticipate results while saving time and costs through efficient resource management.
Yet, according to Katie Wells, Director of Lean Construction at Brasfield & Gorrie, you also must provide practical applications to convince your team of its effectiveness.
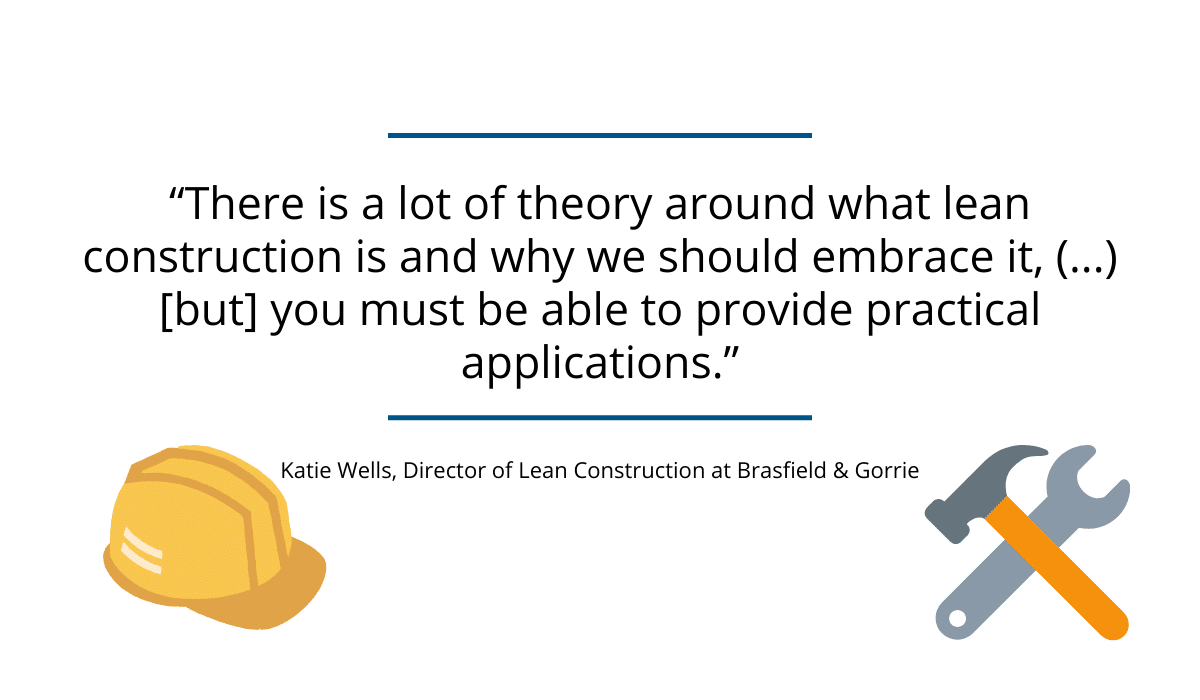
But how can you apply lean construction principles in your company?
Well, you can start small and snowball from there. For example, Southland Industries began with adjustments to the workers’ daily workflow.
One solution they implemented was using an adapted music stand to hold instructions for pipe fabrication in their Mid-Atlantic plumbing shop.
The employees’ workflow was more efficient, and they could finish their tasks much faster.
Another Southland employee also suggested using fixture carts to hold assembled sinks and toilets, which reduced job site storage, labor, and trash collection.
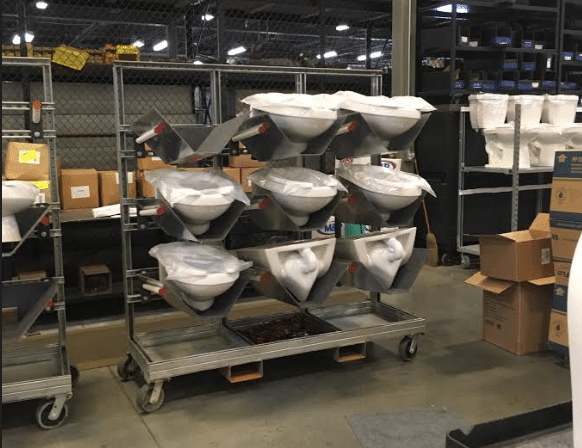
Then, you can scale these solutions to entire projects, like Arizona State University.
The institution was building a new educational facility in 2012 and decided to combine lean construction with BIM.
The superintendent created a baseline schedule for the project and then worked with subcontractors to set additional milestones and plans.
This resulted in a very aggressive schedule for the project, but it also helped the institution reduce downtime and optimize resource allocation.
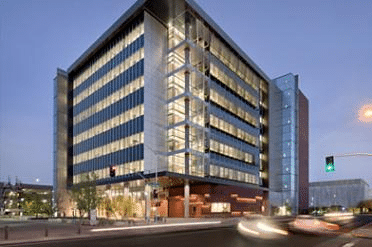
With the help of BIM, they also heavily used off-site prefabrication. In the end, the new research building was finished 16 weeks ahead of schedule, and the institution saved nearly $2 million.
Basically, how you use lean construction principles depends on your company’s shortcomings.
So get a better understanding of where you can improve processes and reduce your operating costs with lean construction.
Use Life Cycle Costing in the Planning Phase
As you’re well aware, expenses in construction go beyond the initial costs.
Therefore, it’s vital to have effective methods and tools to calculate present and future costs so you can find ways to reduce them and improve ROI.
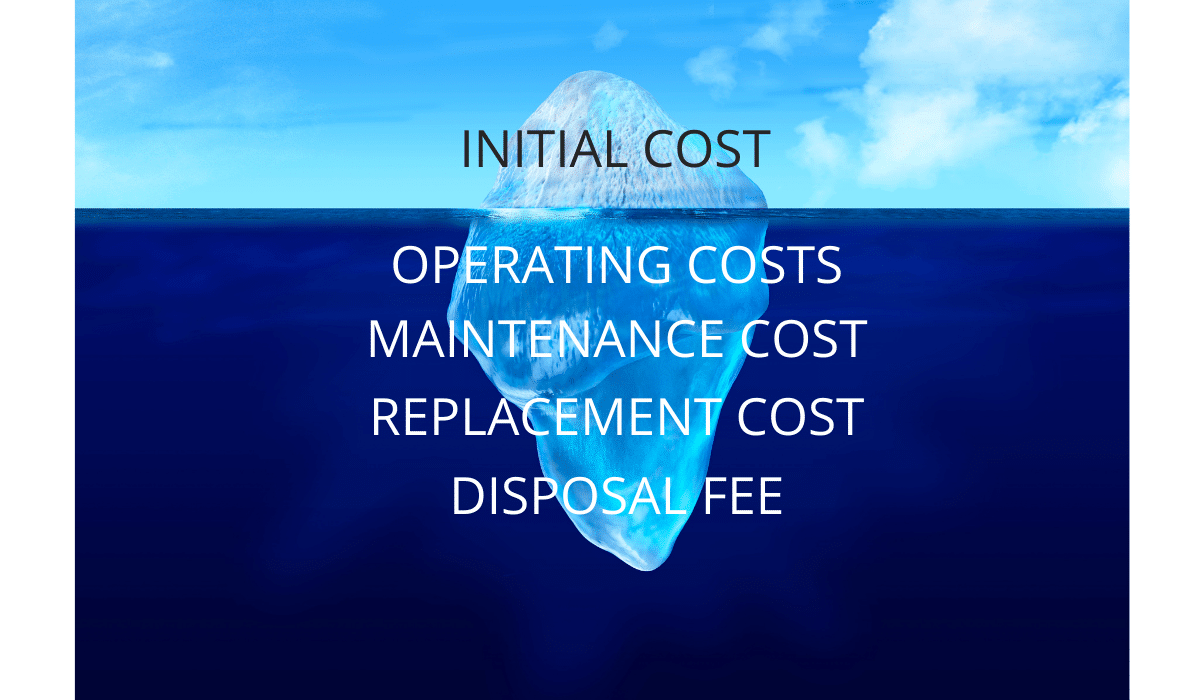
This is where life cycle cost analysis can help you.
In short, life cycle costing is a long-term, objective method that helps construction project teams measure and manage the lifetime costs of a building, construction material, or asset.
It is a robust and comprehensive assessment of ongoing costs for construction projects that enables companies to reduce overall expenses.
Furthermore, the main objective of this analysis is to provide companies with different alternatives for cost reduction while maintaining the expected quality of projects.
Essentially, when you have precise numbers to work with, you can make better decisions on where and how to spend your budget.
It also enables easy comparison between project designs to determine the best long-term value and lowest cost.
So, how do you do that?
Here is a simple formula you can use.
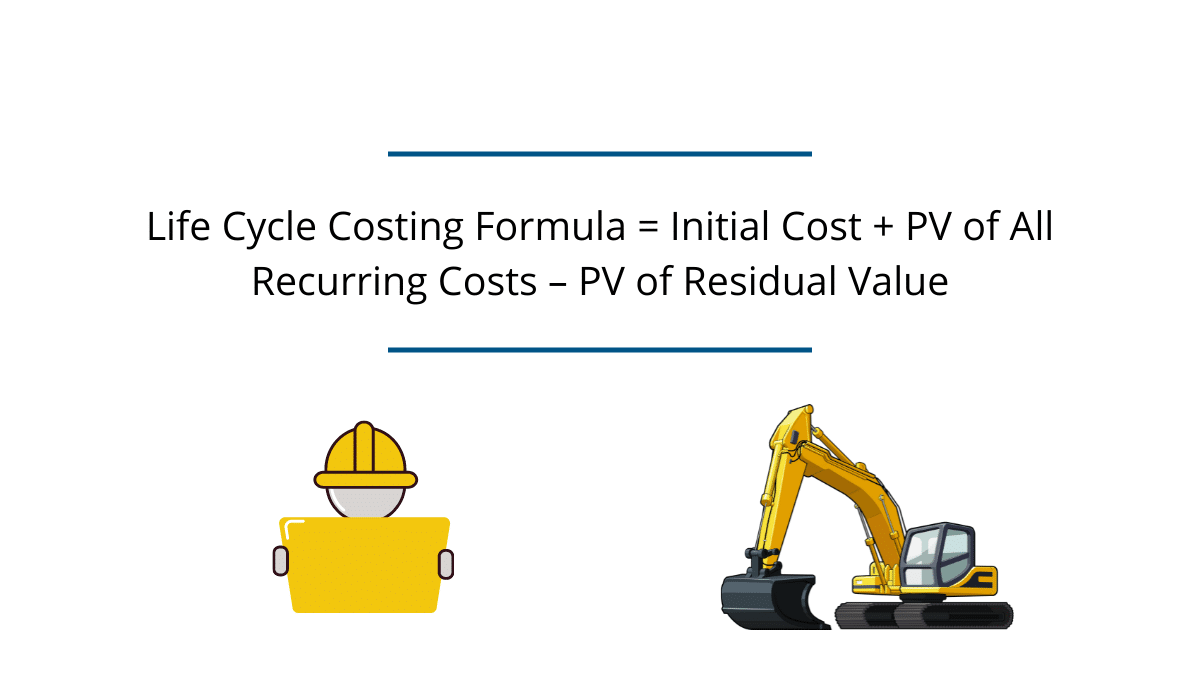
So, let’s imagine you want to buy a new forklift. The purchase price is $50 000, with recurring estimated costs for maintenance and gas going up to $5000.
Now, let’s assume you want to use the machine for 5 years with an annual depreciation rate of 20%. At the end of its lifecycle, you’ll be able to sell the forklift for $10 000.
When you put the numbers into the formula, you end up with a conservative projection of $65 000 lifetime cost for your imaginary forklift.
Keep in mind that recurring costs also include insurance, interest rate, taxes, and other expenses. Also, the residual value depends on the status of your machine.
But to make the most of these cost projections, you need to use the method at the beginning of your project planning.
Determining costs before you begin construction is the best way to find cost-effective alternatives and identify priorities.
Because once the construction starts, things can quickly go wrong, and you can’t make major changes without accumulating additional costs.
It all comes down to effective planning and managing project costs by using the best available tools. Life cycle cost analysis will result in better quality projects and lower operational spending.
Shop Around for Materials
Here’s a simple question. Do you compare prices from different vendors when buying new construction material?
Many contractors regularly do that and have experienced significant cost savings for material procurement.
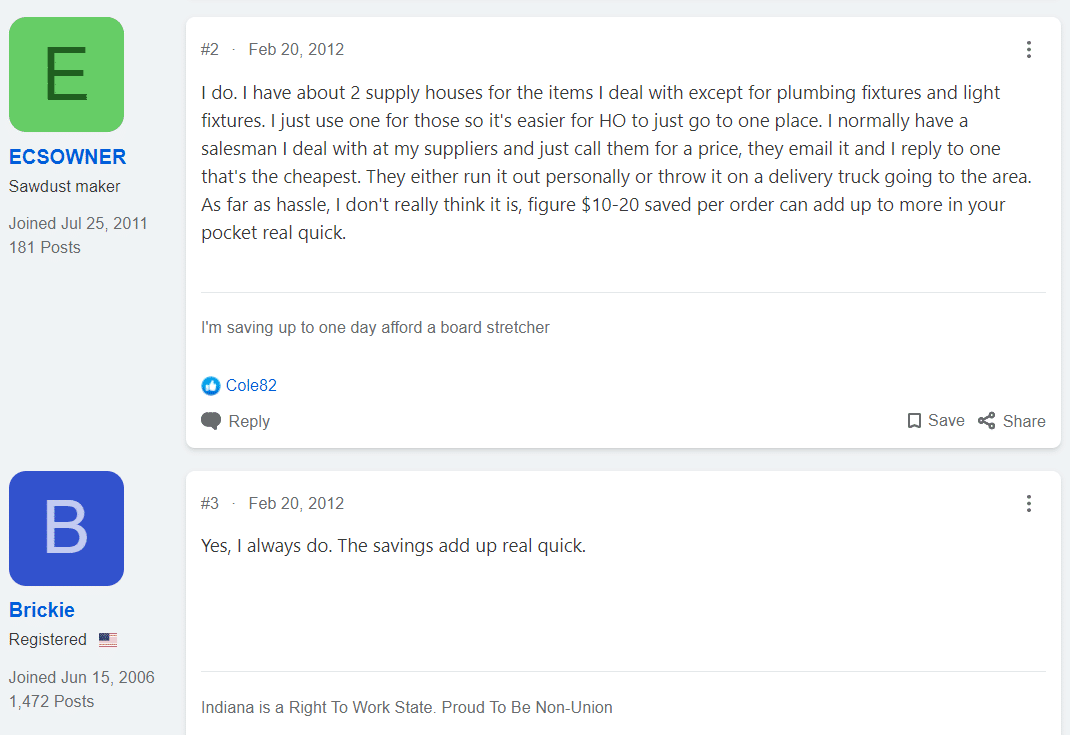
Obviously, some contractors argue that shopping around takes a lot of time, and they’d rather stick with the people they know and trust.
Yet, they might be failing to recognize that material prices can differ drastically from one supplier to another.
Or a new supplier might have more appealing benefits, such as free delivery or a bigger discount for bulk purchases.
What’s more, you don’t have to waste time calling up different suppliers on the phone.
Some contractors use online resources like SpecBid to find local suppliers, compare prices and find the best option for their needs.
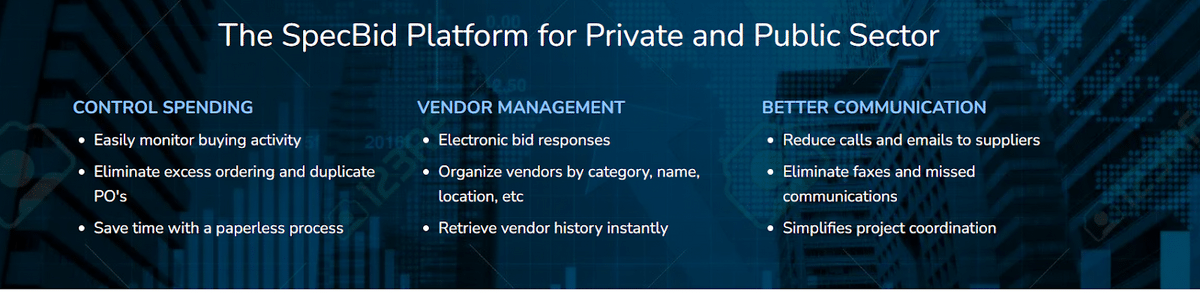
Another thing to look out for is seasonal bargains. Suppliers are eager to get rid of their stock during different periods in the year, so they’re heavily discounting certain materials.
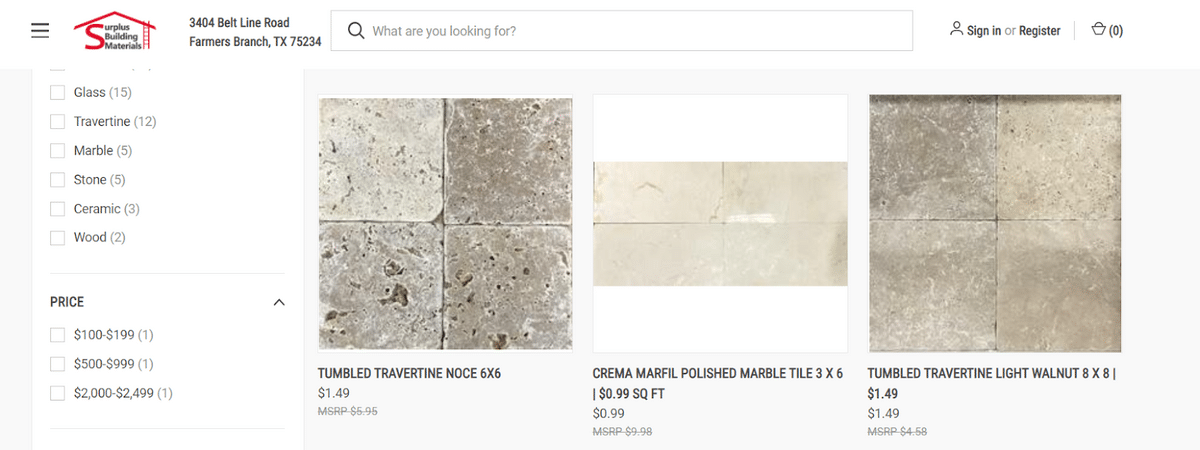
But here’s the thing. Even if you’ve been working with a supplier for years, looking around at what others offer doesn’t mean you should stop doing business with your trusted supplier.
Sometimes, simply mentioning what their competition is doing might spur them to give you a better deal.
Suppliers don’t want to lose their loyal customers, so they might be lenient in reducing their prices.
They might even offer big discounts or free delivery, but you need to do your research and ask.
Basically, to get the best prices and reduce operating costs, it might be wise to look into many different vendors.
Include Environmental Delays in Your Project Estimates
It seems like Mother Nature is actively working against the construction industry when it comes to finishing projects on time and within budget.
Every season has its own obstacles that can slow down task completion and impact the progress of the project.
In winter, you might be dealing with freezing ground that makes excavating and laying down concrete difficult, if not impossible.
Then, during the summer and spring months, you might face high winds and frequent rain.
Cranes could easily get blown over if the wind is strong enough, and other minor objects can be picked up in the air and strike people on site.
Finally, in some places, extreme heat can make construction work unsafe for the workers.
In a nutshell, bad weather can produce serious delays in construction projects.
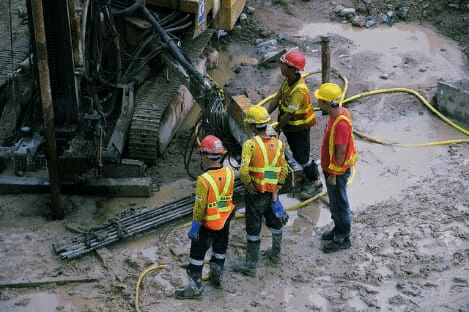
For instance, recent research has shown exactly how extreme weather conditions impact construction projects.
Namely, the most contributing factors to project delays were temperature, humidity, wind, and rain.
Even a 1°C rise in temperature above 28°C can negatively impact worker productivity by 57% while also having detrimental effects on their health.
Working outside in high temperatures often leads to heatstroke and other heat-related illnesses.
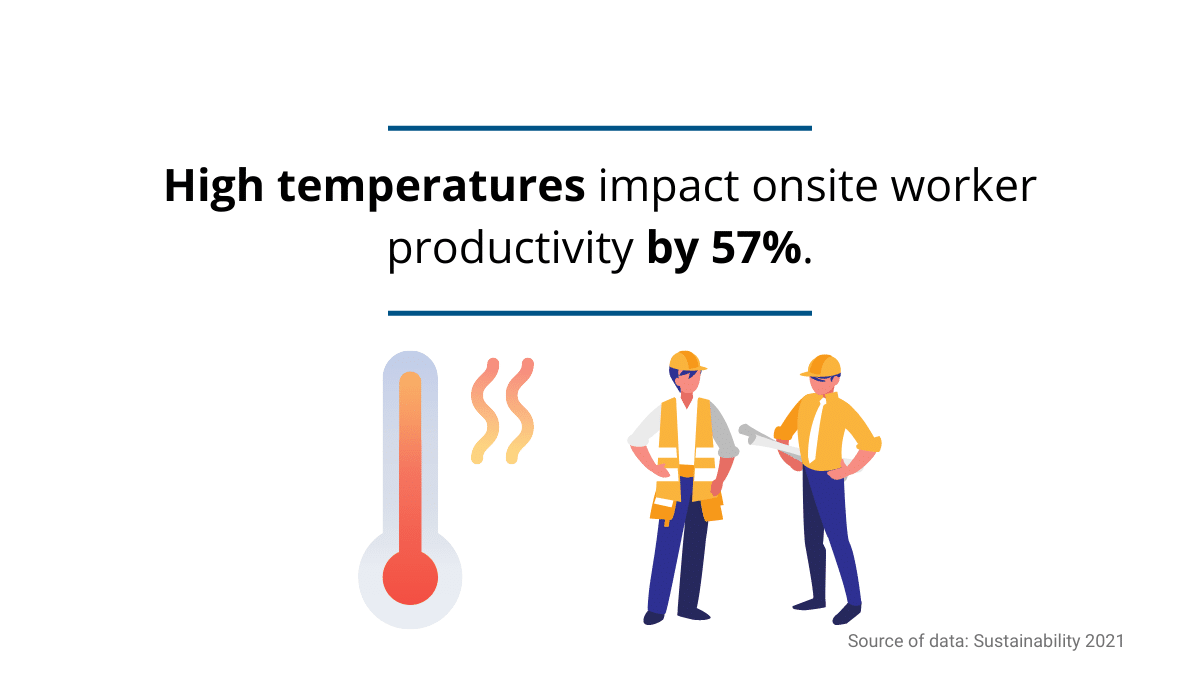
But it’s not just your workers who are affected. Weather conditions also impact how long it will take for materials to become effective.
For example, cold weather can delay mortar mixing for 3 to 5 hours because of slow hydration.
Similarly, installing drywall at 10°C or below can cause gaps, inconsistent paint, or poorly bonded boards. In turn, this could mean more rework and increased operating costs.
So what can you do to minimize operating costs due to weather?
While you can’t stop bad weather from happening, you can plan for it.
In other words, if you know the weather pattern and site conditions for the location you’re going to work in, it’ll be easier to include environmental delays in your project estimations.
This means the client will cover eventual costs caused by environmental delays, and you can have procedures to mitigate problems.
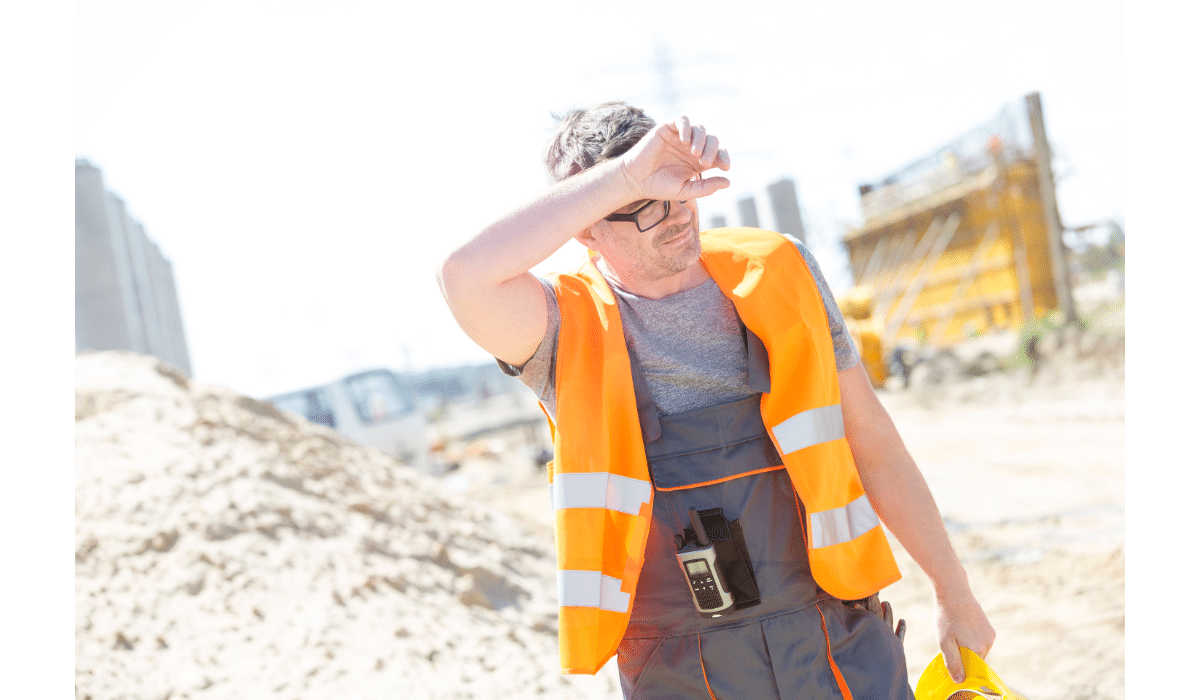
For example, if your worksite is in hot areas like Arizona (USA) or Darwin (Australia), you can anticipate possible delays due to reduced worker performance.
You’ll have to schedule workers to do more intensive outdoor tasks when temperatures are low (morning and afternoon).
That way, the project can still progress without jeopardizing the worker’s health, but it will be slower than working in areas with moderate temperatures.
Next, for more vulnerable materials such as concrete, it might be smart to account for physical barriers such as tarps to protect it from heavy rain.
Or plan in your estimations for modular construction which can be assembled off-site, and thus, you can avoid delays due to weather conditions.
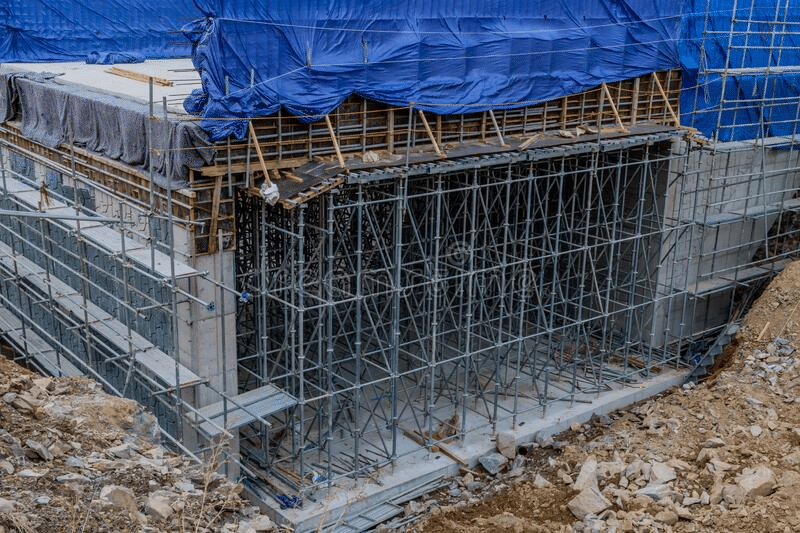
Keep in mind that construction heavily depends on weather conditions.
Still, when you’re actively anticipating possible project delays, it’ll be easier to mitigate problems when they occur and minimize operating costs.
Track Everything With Construction Technology
One of the easiest ways to reduce operating costs is to keep an accurate inventory.
Construction tools and materials often grow legs, and suddenly you’re burdened with replacement costs that can strain your budget.
Tracking everything might seem time-consuming and costly, but the benefits far outweigh the initial costs.
Monitoring and tracking your assets is essential to enable optimized workflow and transparency in asset availability.
That way, you help your workers find the tools they need faster while having historical usage data at your disposal if issues arise.
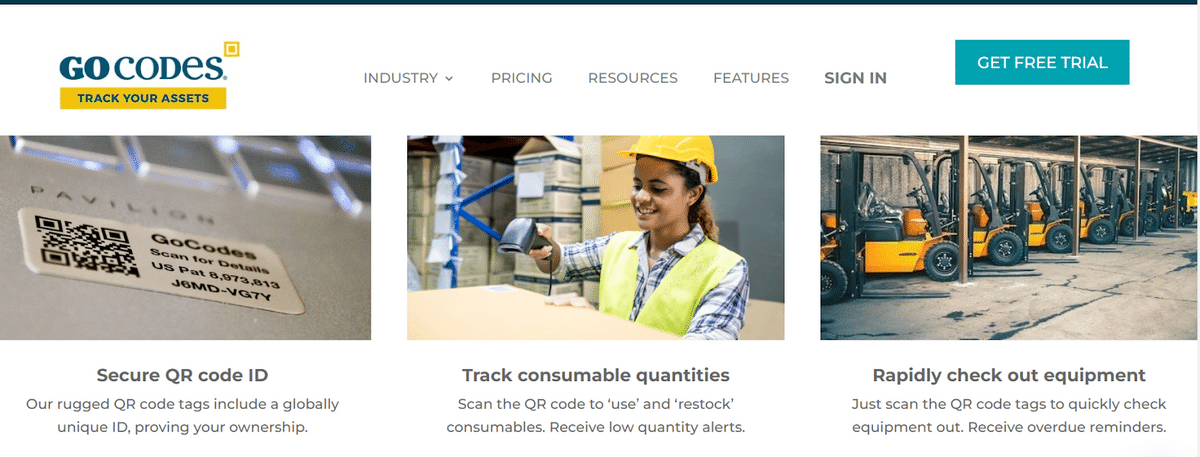
Having user-friendly and simple software like GoCodes Asset Tracking at your disposal will boost your productivity and prevent equipment misplacement or loss.
You’ll be equipped with robust tags you can place on any asset you want to track, while a scannable QR code will provide you with the latest data.
Other useful features include tracking inventory levels of your construction materials. You can also set up alerts when material quantities are too low.
But the best part is you can access updated asset information from anywhere using your computer, tablet, or smartphone.
Now, mastering resource management can be expanded to other areas. For example, using a time-tracking app to manage employees’ working hours and schedules.
This way, you’ll reduce unnecessary paperwork, improve visibility and free up workers’ time, enabling them to focus on essential tasks.
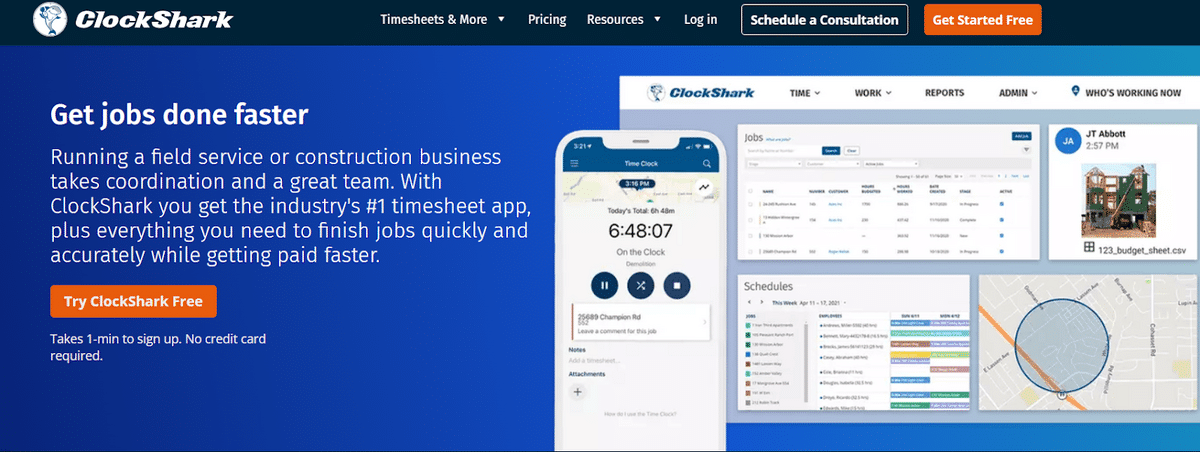
Not to mention that automation can severely reduce human error in timesheets and provide more accurate labor costs.
Or in other words, more optimized workflows and removed bottlenecks enable companies to reduce operating costs.
In the end, use the right software to create a streamlined system for successful project delivery and save money.
Conclusion:
It’s easy to say you want to reduce costs, but your efforts will be useless when you don’t have actionable methods.
Start by evaluating your current systems and see where you can make minor or bigger improvements to optimize processes and cut down expenses.
Then, spend time and resources smarter by looking for bargains, tracking quantities, and accounting for delays.
Hopefully, our tips have helped you realize how many ways there are to drastically reduce your costs.
By implementing some of them, you can start new projects with a bigger profit margin and remain in business for a long time.