Budgeting for overtime is a reality of managing nearly any construction project.
Since the work usually takes place outdoors, making it susceptible to supply chain issues, unexpected severe weather or unexpected labor shortages, project managers might find themselves scrambling to hit a project milestone.
While it’s impossible to know exactly when a construction project might need overtime, some pre-planning can lessen the blow when it is necessary.
Read on for some guidance on using overtime for your construction project.
In this article...
Make the Planning Phase a High Priority
Overtime in a construction project can quickly wreck even the most carefully planned budget. However, this is a challenge faced by many project managers:
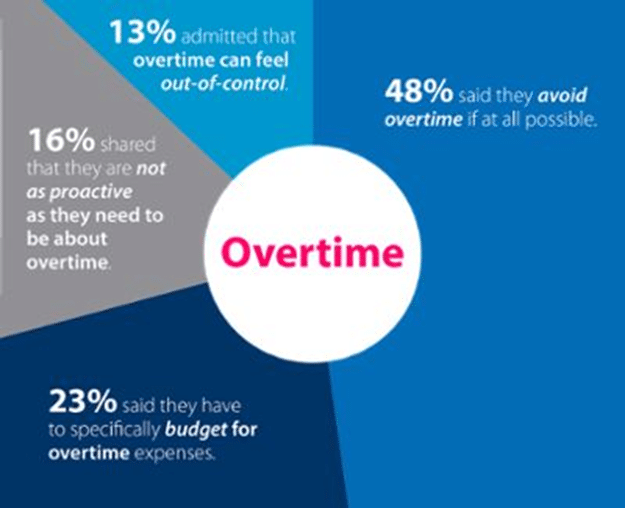
How is it possible to plan for overtime when it’s impossible to know precisely when it might be needed?
Some project managers build labor overtime into the emergency or reserve budget, and others remain alert by noting weather patterns, labor shortages, or crime in the project area.
Taking a few minutes to check on these trends can help to avoid a labor crunch later on.
It’s also useful to tap into the wisdom of others.
If you’re working on a project in an unfamiliar location, it can help to tap into your network and speak with those who have conducted construction in the neighborhood or area.
For example, if you are developing a lot in a rural area that requires sewage and electricity hookups, and the land involves several unusual elevation changes or soil characteristics, find out who might have also worked in similar conditions for advice.
What did that project manager wish he or she knew before taking on the bid?
If you learn, for example, that a colleague of yours struggled with permits and frustrating zoning codes, you can pay extra attention to such necessities before the ground is even broken.
Treading carefully with valuable information is tremendously helpful in preventing overtime.
Ensuring that you have assessed risks and potential delays as much as possible helps to avoid crews standing around, waiting for permission to begin—or, worse, falling behind on schedule.
Provide Employees With the Right Tools
When you commit to providing your workers with the right tools, that goes beyond merely getting them the forklifts, crane attachments, and wrenches that you know are necessary for completing the task.
It also involves making sure that equipment is functional, safe, and reliable.
There’s no use in owning a fleet of concrete mixers, for example, if most of them are awaiting parts or so finicky that they slow down your employees.
Sticking to a schedule of preventive maintenance and ensuring that all employees have completed proper training can help keep your equipment in top shape.
Information is important in other ways, too. Your employees expect the data and modern technological tools they require to meet your expectations and work well as a team.
The ability to communicate well helps to cut down on misunderstandings, absenteeism, or poor asset allocation. A universal asset tracking program can help.
For example, GoCodes Asset Tracking provides an app with unique QR or bar codes that provides valuable real-time information.
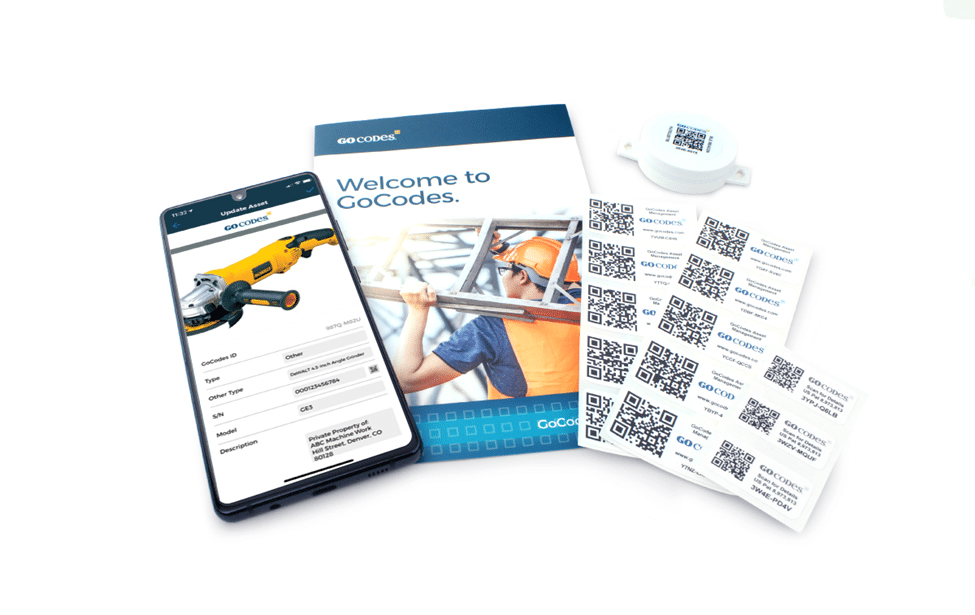
How is an asset tracking program a tool? It can bolster efficiency in the following ways:
- GPS tracking helps to locate equipment en route and track down lost items
- Unique, scannable QR codes are able to store such information as maintenance records and operator manuals
- Check-in/check-out systems increase accountability and tracking
- Cloud-based systems ensure that all data is current and available as needed
- Real-time inventory management helps avoid supply chain panic
The information you can collect with an asset tracking tool decreases the time spent searching for equipment or clarifying tasks.
When an asset tracking system is used as a tool, equipment receives better care, and your team can communicate instantaneously.
Accomplishing more during a shift helps to build a buffer against the need for overtime.
Cross-Train Your Employees
A cross-trained workforce is less bored, more motivated, and able to take on more responsibility.
Cross-training employees shows that you believe in your employees and provides your team with the opportunities to develop new skills, find areas of interest, and suggest new ways of working.
It benefits your company in many other ways, too:
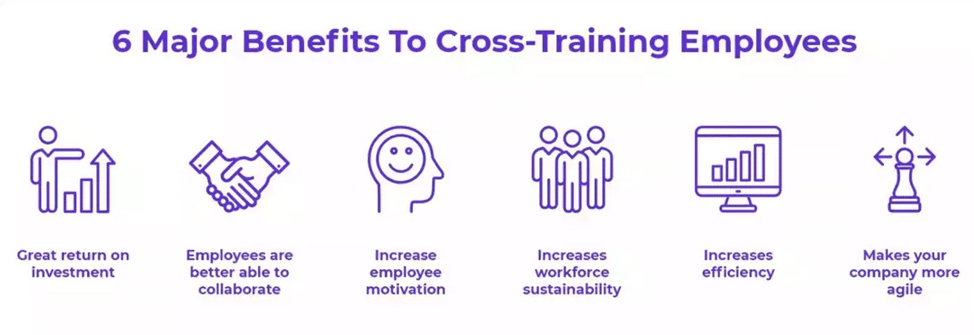
In construction, cross-training can be integrated into many formal training programs.
Certain pieces of complex equipment require permits or specialized training; by offering to assist employees with the costs associated with this, your investment will return many times over in the form of a capable workforce and avoidance of overtime.
Cross-training enables schedule rotation, skill-sharing, and continual new challenges for employees.
You are more able to promote and select teams from within without bringing in third-party contractors, and building training teams can improve relationships across the company.
In addition, providing a window into what the company does as a whole tends to increase understanding, empathy, and innovation.
When employees are cross-trained, they tend to trust and rely upon one another more.
A cross-trained team is more insulated against absenteeism and better able to adjust so that all critical tasks are covered.
While many companies were forced to cross-train on the fly during the COVID-19 pandemic, instituting a structured framework now that the crisis is over will help your company become more efficient and provide a reliable way of protecting itself against continuing staffing shortages and construction skill gaps.
Manage Your Team’s Schedule
When your team’s schedule is unreliable and constantly subject to change in a way that creates tension, it’s best to take the time to look at management techniques.
Schedules that are a constant jumble can force your team to work overtime in order to stay on track.

As you can see, the negative consequences of constant and avoidable overtime in the construction industry often have a domino effect that can sink a project or even an entire company.
Committing to proper schedule management is an important step in ensuring a healthy workforce and reliable budget.
Taking a look at project milestones and periods of heavy work is the first step in good scheduling.
By planning ahead and avoiding reliance on the same employees in the same role, you can avoid burnout, prepare your workforce for periods of increased stress, and plan for extra hands if necessary.
Other ways to manage your employees’ schedule efficiently include speaking to seasoned employees and foremen to gather information about which workers fit best in certain roles and shifts.
You can set up a group chat or another employee communication system to encourage a timely flow of information.
Next, rather than building a schedule around a project, look first at your employees’ skills and when they are available.
Ask your employees to alert you to life events they might know of ahead of time, and build trust by paying attention to such requests.
Provide a definite and workable system for swapping shifts and requesting time off.
Finally, ensure the schedule is provided in a reasonable amount of time and that it can be accessed easily.
This way, your site will be running smoothly and your workforce will feel respected.
Not only will you avoid overtime, but you will also build a crew that knows their time and work-life balance are respected.
Use a Time Tracking Software
Using time tracking software is a tremendous help in building a reliable and accurate schedule.
It allows real-time changes and can help employees to know when they are needed; in addition, if the schedule requires adjustments, employees can alert the appropriate team members ahead of time and avoid last-minute labor gaps.
Time tracking software helps project managers assess how well a schedule is meeting their needs.
It is also far more secure, user-friendly, and accessible than relying on paper distribution or a spreadsheet.
In addition to meeting scheduling needs, time tracking software can help with employee onboarding, provide a one-stop login for personal information, and streamline payroll integration.
Good time tracking software can also provide project managers with such information as which training programs are efficient and how employees are faring at a new site.
This data is then easily digestible in reports, which encourages analysis by stakeholders and workers alike.
This form of transparency is especially useful in proving compliance with certain regulations, such as meeting overtime pay laws:
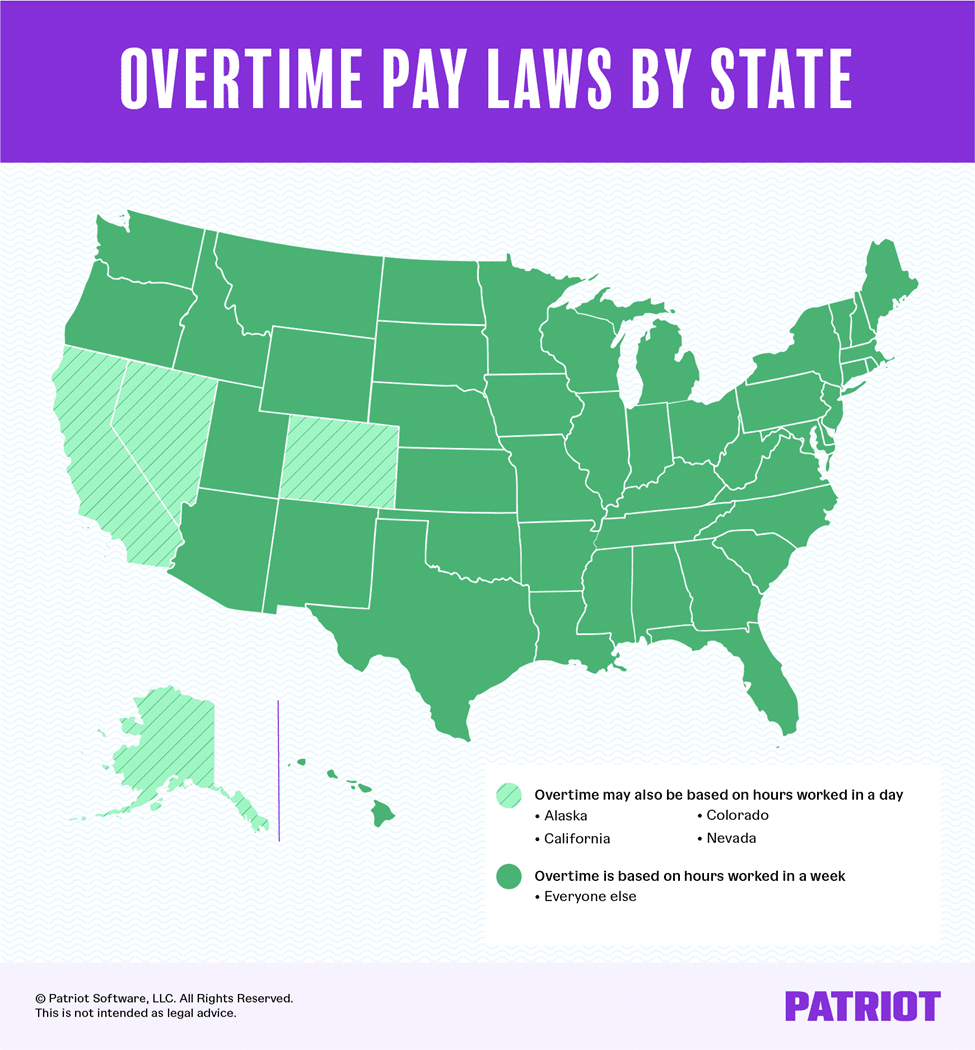
By using software to track regular and overtime pay, your company can ensure that your workforce is compensated fairly and as expected.
In addition, you can identify areas in which overtime is used more often than necessary. That means strategizing to solve the problem is more effective and grounded in data.
Conclusion
To manage overtime on your construction project, pre-planning is a must, as is relying on your contacts in the industry.
It’s also important to supply your team with the right physical and technological tools.
By cross-training employees and using good schedule management techniques, project managers can build trust, lessen overtime, and increase the flexibility of the workforce.
Finally, using time tracking software can assist in efficient schedule creation and provide transparency as well as valuable data.