Do you ever feel like you’re wasting too much time keeping track of your inventory, only to still deal with issues like missing assets, inaccurate data, or sudden material shortages?
If so, the real problem might be that you haven’t found the right inventory tracking method yet.
But that changes today.
In this article, you’ll find the five best ways to track your inventory effectively.
We’ll break down each method’s pros, cons, best use cases, and practical tips for implementation.
By the end, you’ll know exactly which method fits your business best—saving you time, money, and headaches.
Let’s get started.
In this article...
Manual Inventory Audits (Cycle Counting)
Manual audits involve periodically counting and recording inventory using paper logs or spreadsheets.
This method doesn’t require any specialized software, devices, or additional tools, making it a low-cost and easy-to-implement solution.
That said, this simplicity comes at a price.
According to Paul Heitlinger, General Manager at the inventory-monitoring drones vendor, Nokia AIMS, manual inventory audits have one large downside:
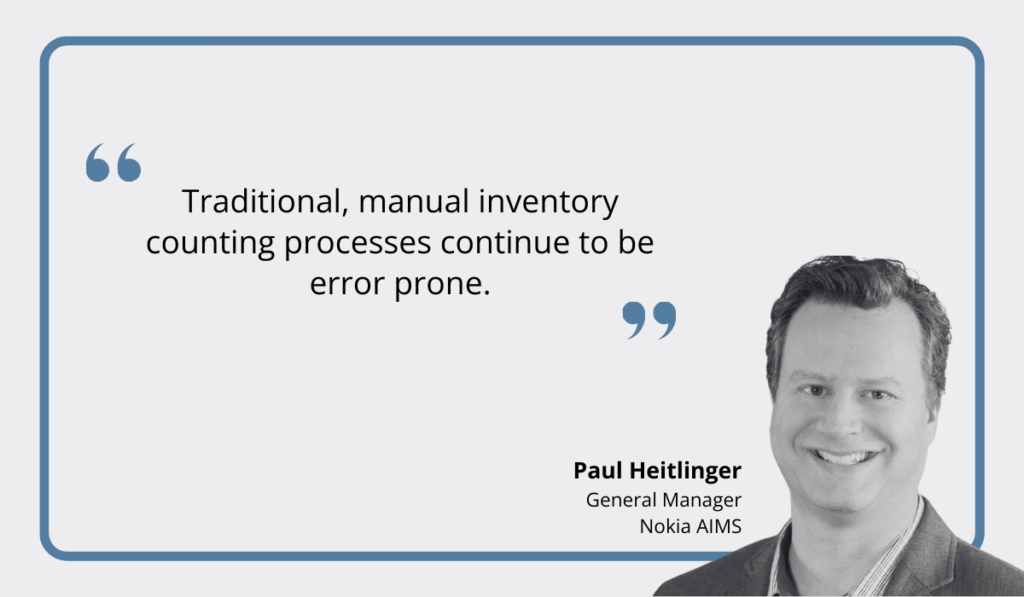
Illustration: GoCodes Asset Tracking / Quote: Supply Chain Digital
And Heitlinger is right.
If you’ve ever done a manual count, you know how easy it is to forget to log vital information, make a typo, or enter incorrect data.
These small errors can lead to large problems, from misinformed decisions and lost assets to operational inefficiencies and project delays.
Essentially, bad data leads to bad outcomes.
The 2022 Autodesk report confirms this.
As it turns out, one-third of construction professionals admit that poor decisions result from bad (inaccurate, incomplete, or duplicate) project data more than 50% of the time.
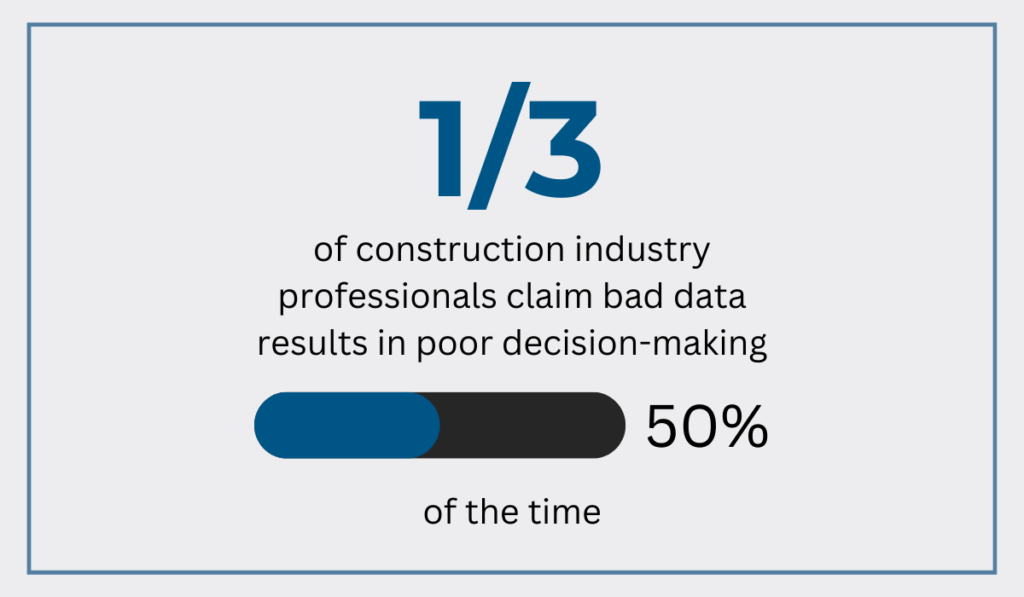
Illustration: GoCodes Asset Tracking / Data: Autodesk
This is completely unsurprising.
If your inventory data is unreliable, you could easily either overorder or underorder materials, place orders too late, or inaccurately estimate costs.
The worst part?
With manual tracking, you usually won’t even realize your data is flawed until it’s too late.
One Chief Information Officer at a general contracting firm surveyed by Autodesk shared their experience:
“When we started reviewing the quality of our data, we found no fewer than 20 different spellings for the same supplier. Sometimes the first letter was capitalized, sometimes it wasn’t. We repeatedly saw variations like ‘corporation’ vs. ‘corp.’ and ‘company’ vs. ‘co.’”
So, if you choose to use manual inventory monitoring, it’s important to prevent mistakes like these and ensure your data is as accurate as possible.
One effective way to achieve this is by using standardized audit templates, like the one you see below.
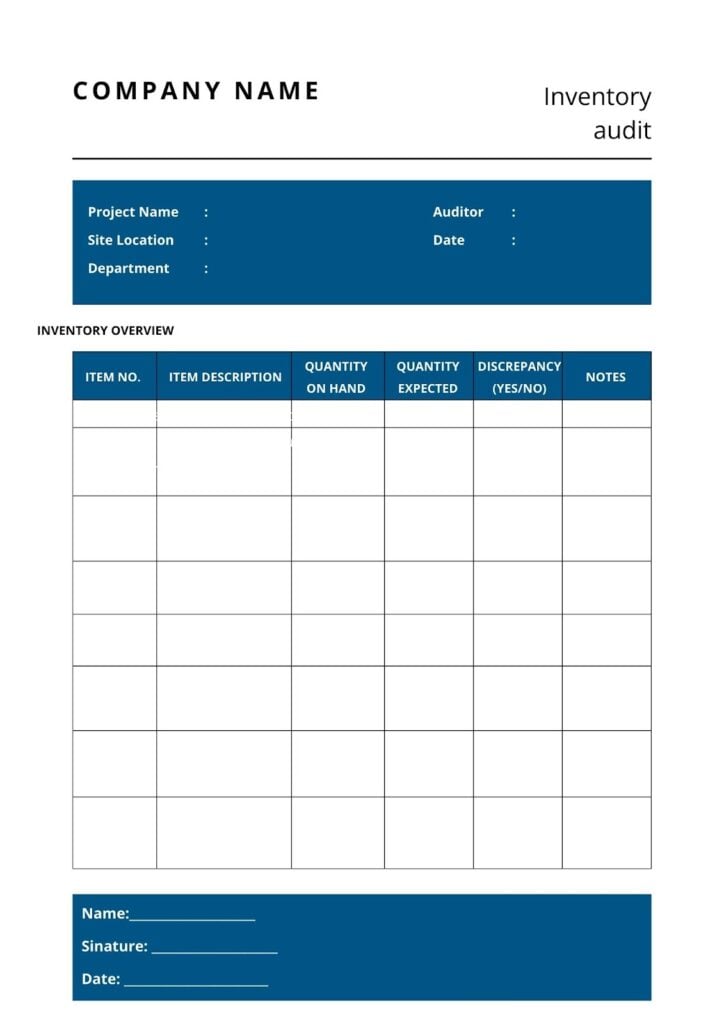
Source: GoCodes Asset Tracking
This helps create a structured process, ensuring no crucial detail goes overlooked and boosting overall data accuracy.
Ultimately, despite its limitations, manual tracking can be a cost-effective and user-friendly way to manage assets, especially for low-value items, smaller projects, and tight budgets.
For larger-scale operations, however, investing in some other solutions on this list may be more effective.
QR Code Scanning
QR code-based tracking is an excellent alternative to manual inventory management.
Here’s how it works:
You attach QR code labels (shown below) to your inventory, assigning a unique QR code to each item.
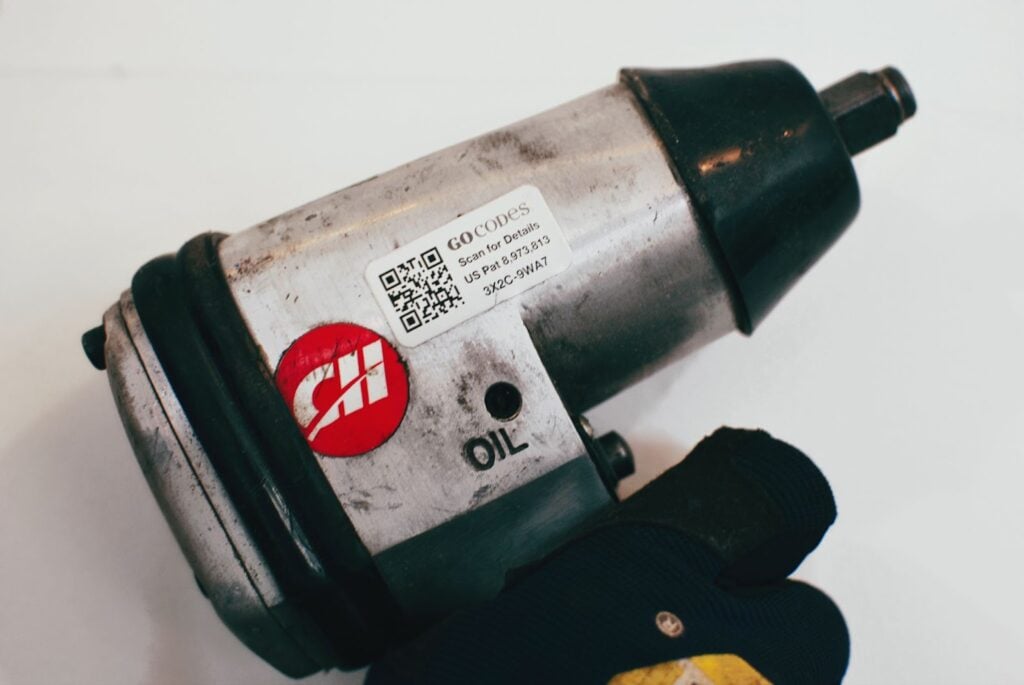
Source: GoCodes Asset Tracking
Employees then simply scan the QR code using a mobile device (smartphone or tablet with a camera) to access key asset information, such as:
- Product name
- Product ID
- Quantity in stock
- Warehouse location
- Supplier details
- Warranty information
This technology allows users to view and update inventory information on the go, which makes it easier to keep your records accurate, complete, and up-to-date.
As a result, you can significantly boost your operational efficiency and cut unnecessary costs.
Just ask J&M Keystone, Inc., a San Diego restoration contractor.
Thanks to GoCodes Asset Tracking’ QR code-based tracking, they were able to minimize instances of lost assets and reduce related expenses.
Lee Sherman, their former Operations Manager, explains how much money was wasted before implementing the system:
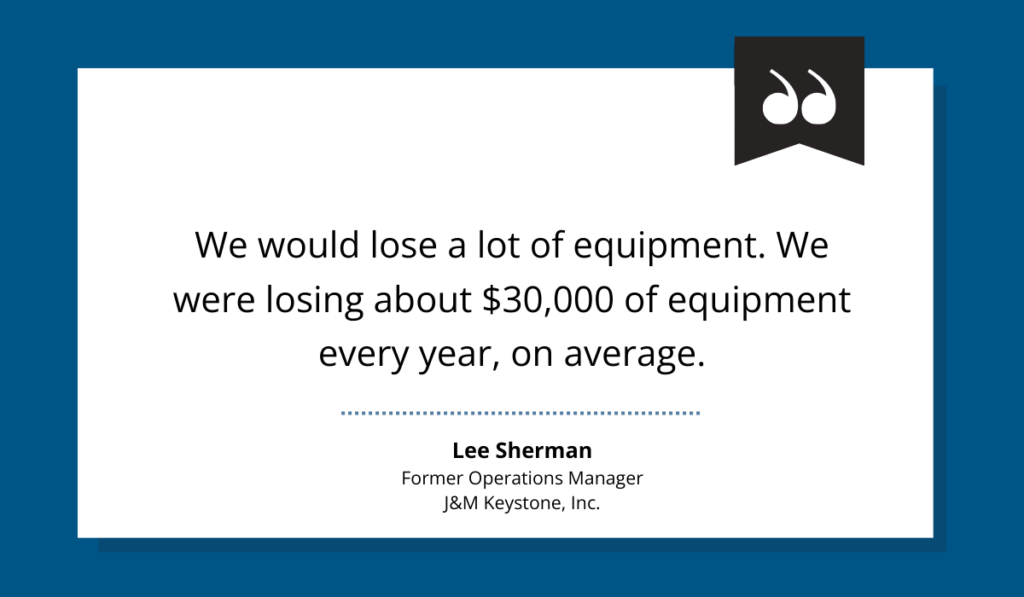
Source: GoCodes Asset Tracking
He goes on to say that before, valuable assets would be left by workers on job sites, never to be found again.
However, with GoCodes Asset Tracking, the items’ location would be recorded with each scan so they could easily look up the latest whereabouts in the system and retrieve them.
The results?
A dramatic reduction in equipment loss, says Sherman:
“Through that, we’ve got our equipment loss down, probably closer to $1,500 per year.”
This is something spreadsheets and paper logs simply cannot do.
However, for QR tracking to be effective, it’s important to choose the right labels for your environment.
For example, if you work in construction, be sure your labels can withstand dust, moisture, and rough handling so that they don’t get damaged and unreadable over time.
If you opt for GoCodes Asset Tracking’s inventory tracking solution like J&M Keystone did, you’ll have plenty of options to choose from, from light poly-duty labels to rugged hang tags.

Source: GoCodes Asset Tracking
We provide labels and tags for every need!
Overall, QR code tracking is incredibly versatile and can be used for anything, from construction materials and small tools to heavy machinery.
It’s simple yet powerful, efficient yet cost-effective—a smart choice for modern inventory management.
RFID Technology
Just like QR codes, radio-frequency identification (RFID) tracking follows this principle: tag the asset, scan the tag, and update or view the records.
However, RFID technology is slightly more advanced. It can read tags from a distance, doesn’t require a direct line of sight, and can scan multiple tags at once.
This makes inventory tracking even faster, smarter, and more automated.
Kevin Beasley, CIO at the ERP software developer, VAI, provides some specific figures:
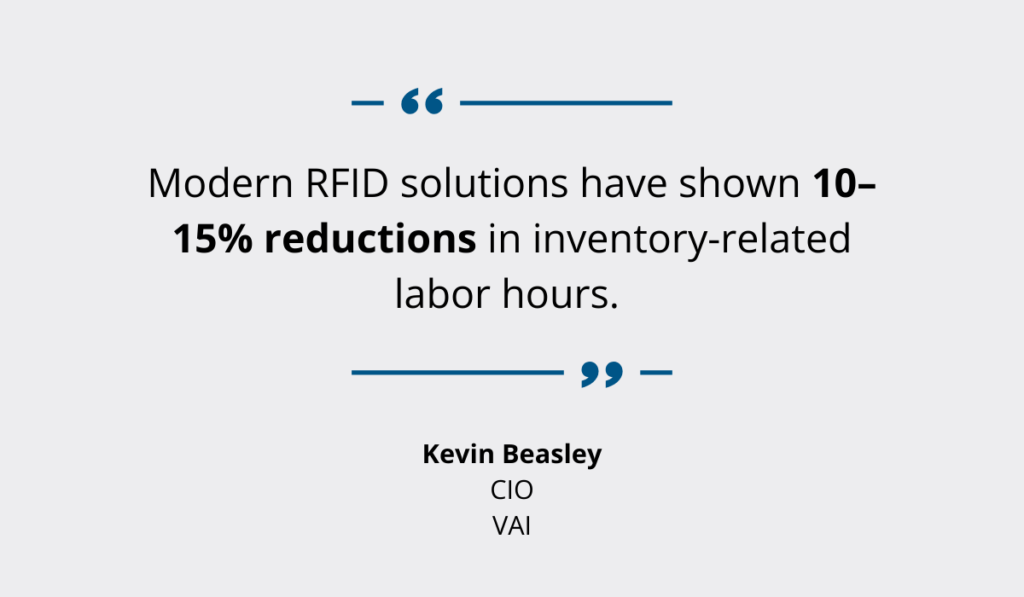
Illustration: GoCodes Asset Tracking / Quote: Supply & Demand Chain Executive
He adds that RFID reduces annual inventory fluctuations and boosts inventory precision by more than 25%.
Navayuga Engineering Company (NECL), an engineering and infrastructure firm, experienced these benefits firsthand.
By implementing an RFID-based tracking system, they were able to streamline truck movement and congestion at checkpoints, significantly improving their efficiency and inventory management.
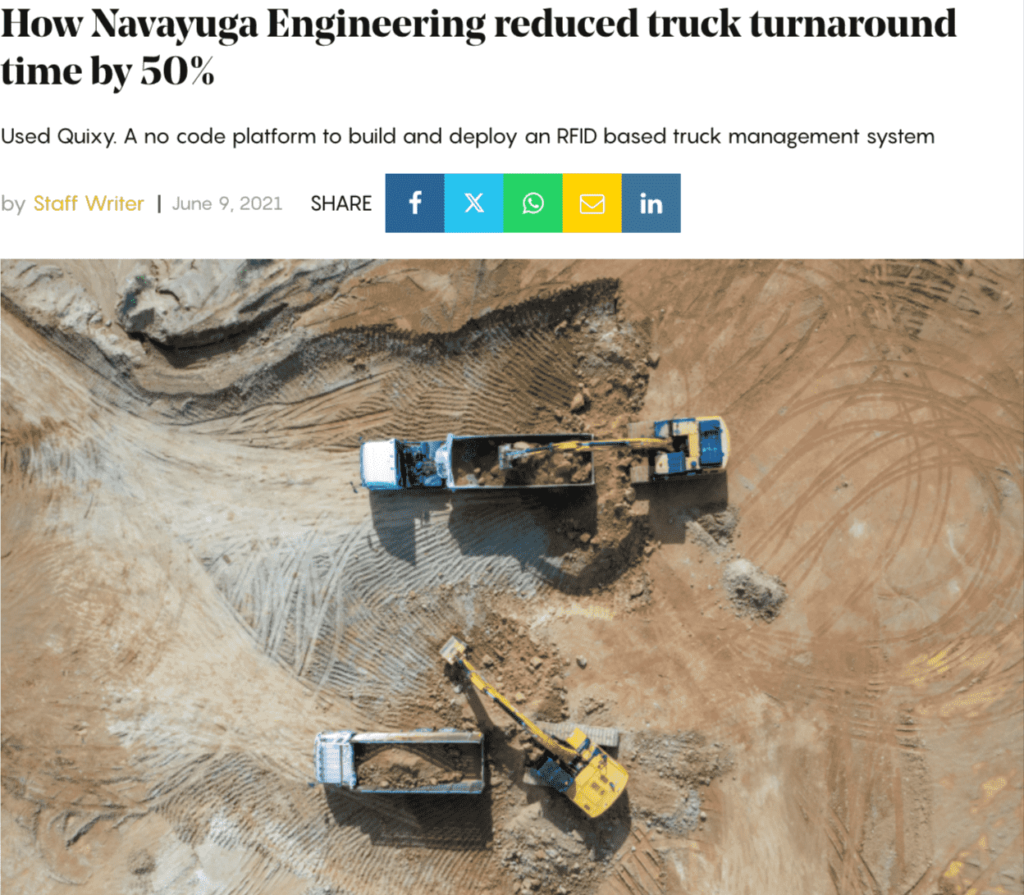
Source: Construction Week Online
Here’s how:
While executing a large infrastructure project for the government, NECL had to transport stones from a quarry several kilometers away—multiple trips, dozens of trucks, every single day.
Before RFID, each trip required manual documentation of truck, driver, and load details, followed by verification at various checkpoints, causing bottlenecks and limiting daily trips.
With RFID this all changed.
Truck details, timestamps, and inventory data were now automatically captured upon loading, significantly boosting overall operational efficiency.
Subhash Chinta, their former Project Controls Engineer, shared the results:
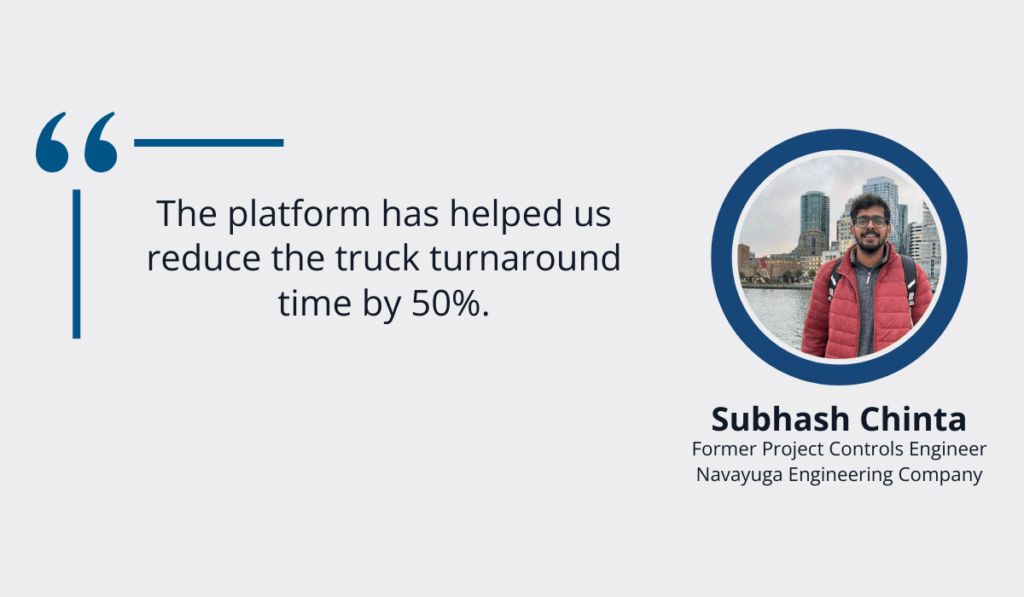
Illustration: GoCodes Asset Tracking / Quote: Quixy
Now, you must be wondering: can this tech work for tracking smaller items like tools or materials?
The answer is yes, but there’s a catch.
RFID requires specialized readers and tags, as well as ongoing maintenance, which can get quite costly.
Therefore, before implementation, it’s best to do the math first and assess whether the investment makes financial sense for your organization.
Generally, RFID is most effective for tracking high-value assets that move frequently.
Cloud-Based Asset Management Software
No matter what type of asset tags you choose—QR codes or RFID—you’ll need to pair them with asset management software.
With cloud-based solutions, all essential information is stored in one central location, accessible from anywhere, anytime, by anyone with permission and internet access—like in the example below:
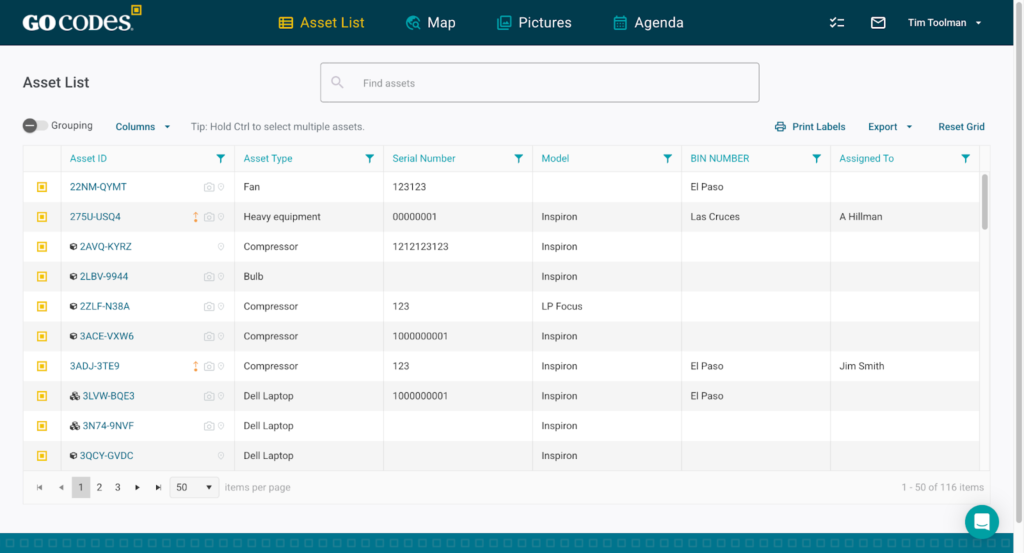
Source: GoCodes Asset Tracking
No more driving to the office computer or calling around just to check where something is, who’s using it, or how much stock is left.
It’s all right at your fingertips.
But that’s just the beginning.
This kind of software comes with some powerful features that can streamline your inventory management even further.
For example, with low stock notifications, you never have to worry about running out of critical supplies again.
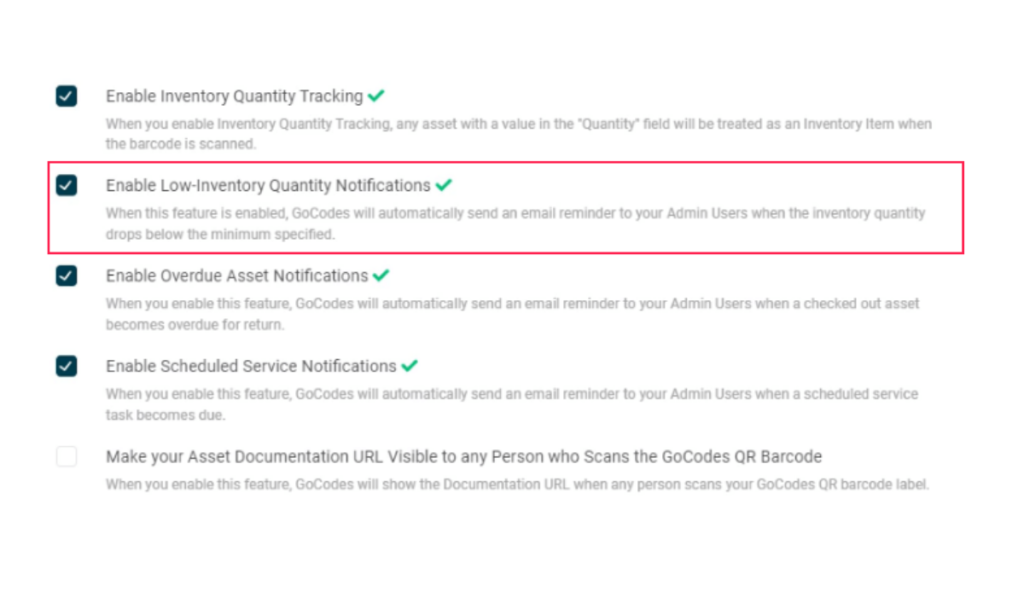
Source: GoCodes Asset Tracking
Simply set a minimum quantity, and the system will alert you when it’s time to reorder.
How convenient is that?
Moreover, analytics and reporting tools provide deeper insights into how effectively the inventory is used.
You can access reports on asset utilization, costs, allocation, and more, and share them with your team with just a few clicks.
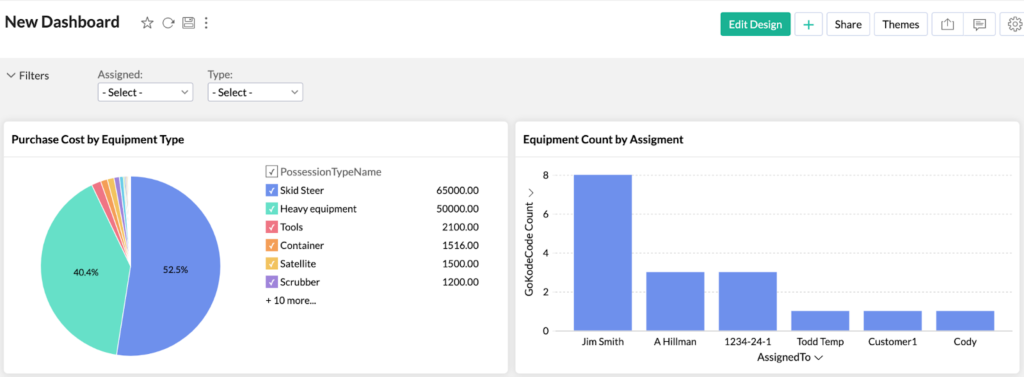
Source: GoCodes Asset Tracking
It’s a great way to improve your decision-making and communication.
However, be sure the software you choose is actually usable before implementing it. Otherwise, you’ll never get the team’s buy-in.
The 2024 Autodesk survey has already shown that 42% of construction organizations cite a lack of digital skills among employees as the biggest barrier to digital adoption.
Additionally, there’s also a reluctance to change, cited by 28% of organizations.
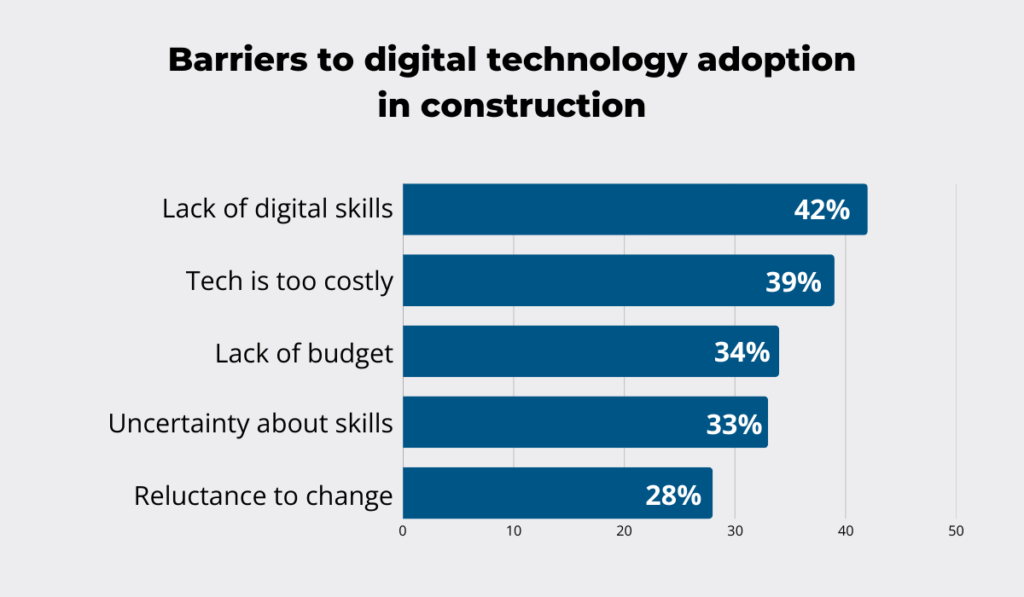
Illustration: GoCodes Asset Tracking / Data: Autodesk
That’s why choosing a user-friendly system is so important.
Your new solution needs to be simple and intuitive enough so that even your less tech-savvy workers can be comfortable working with it.
So, how do you find the right one?
Start by checking online reviews and see what others in your industry are saying.
If the feedback is positive, like the one you see below, that’s a great sign.
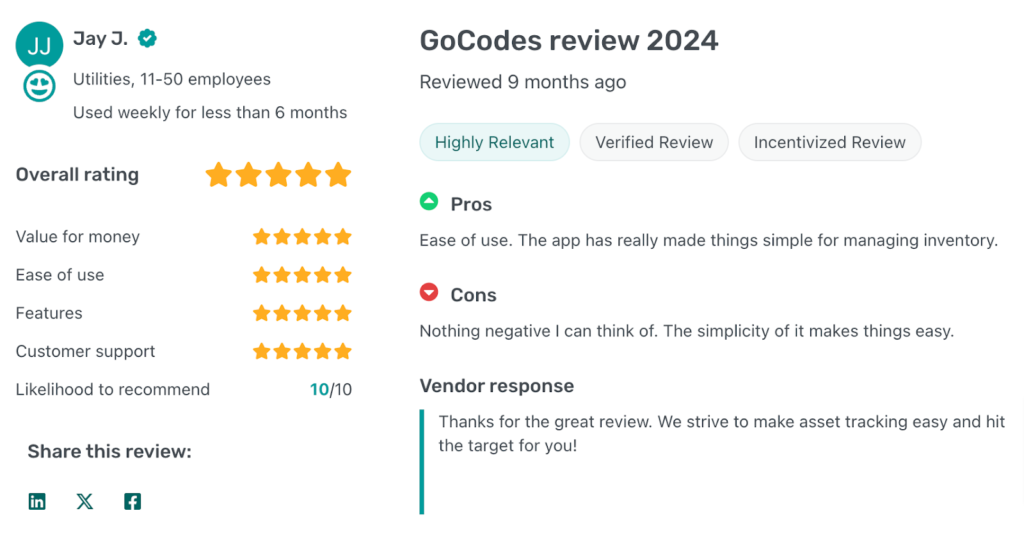
Source: GetApp
From there, find out if the vendor offers a free trial so that you can explore all the features yourself before making the final decision.
After all, nothing beats firsthand experience.
IoT-Based Inventory Tracking
The final method on our list is also the most advanced: IoT, or the Internet of Things.
This technology connects traditionally non-communicative devices to the Internet, allowing for remote monitoring and data collection.
Not too long ago, smart features like Wi-Fi connectivity were limited to phones, tablets, and laptops but now, almost any item can become a “smart device”.
In other words, IoT enables your inventory to be “online” and, in a sense, communicate with you and your team.
Below, you’ll see this advanced technology in action, automatically updating inventory quantities.
Source: IoT Design on YouTube
One of the greatest advantages of IoT is that, beyond tracking locations and quantities, it provides insights into inventory conditions that were previously unavailable.
For instance, some IoT-enabled sensors monitor environmental factors like temperature and humidity, ensuring your assets are not just tracked, but also used effectively.
A great real-world example comes from Costain, a UK-based construction company that uses concrete sensors to track temperature and strength as concrete sets.
You can see one such sensor below:
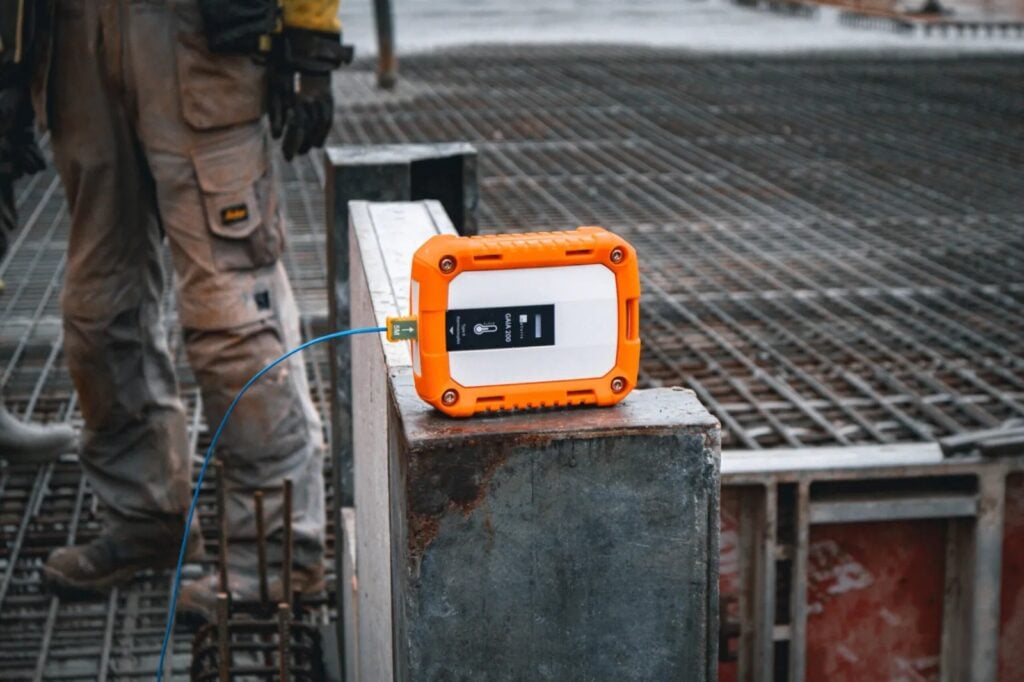
Source: Maturix
With this data, they’re able to make informed decisions about when to remove formwork, ultimately reducing striking times by an average of 33%.
Bhavika Ramrakhyani, Head of Materials at Costain, commented:
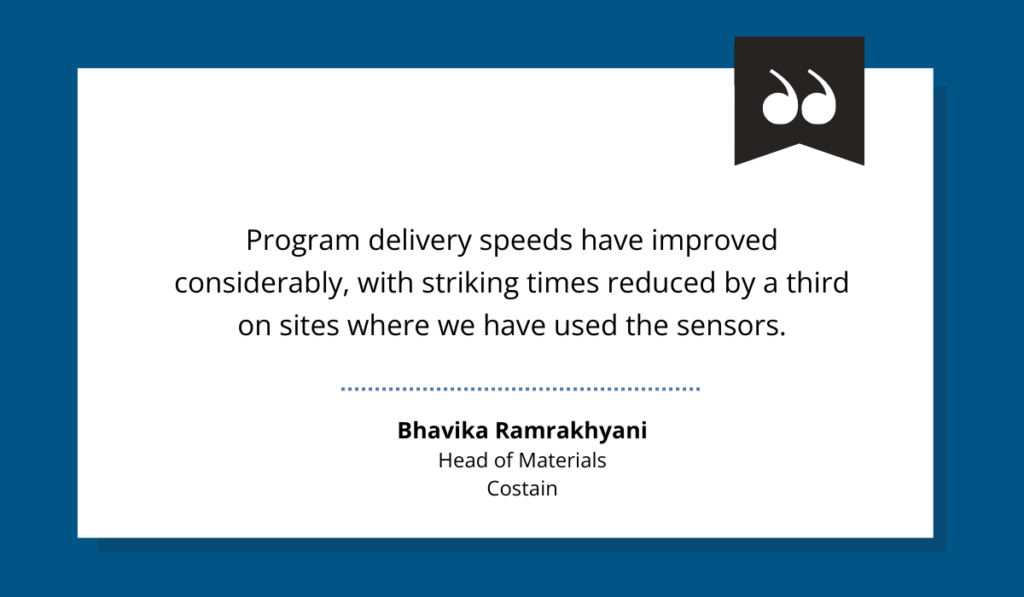
Illustration: GoCodes Asset Tracking / Quote: Costain
Additionally, this technology allows Costain to repurpose and reuse more temporary structures, reducing inventory waste and lowering its carbon footprint.
Essentially, thanks to IoT, they’re able to make the most out of their valuable inventory with ease.
Of course, no technology is perfect.
IoT can be pricey and tricky to implement, especially for smaller operations.
That’s why, just like with RFID, it’s important to evaluate whether it aligns with your budget, needs, and technical expertise.
Typically, this technology works best for projects that rely on precise monitoring or deal with sensitive materials.
Conclusion
So, there you have it!
These are the five best ways to track your valuable inventory.
But how do you figure out which one is right for you?
Easy—just weigh the pros and cons of each and see which fits your needs, goals, and budget.
If you’re running a smaller operation, there’s no need to splurge on the most high-tech, expensive system.
A simple, budget-friendly solution like QR codes might do the trick just fine.
At the end of the day, the best tool is the one that works for you.