If you are a construction company owner or manager, you know that tool management can be challenging, especially if you’re handling larger projects with numerous workers and an extensive inventory of tools.
You might be familiar with the scenarios of time wasted in searching for missing tools and unexpected tool breakdowns that lead to unnecessary delays.
The common thread binding all these issues? A need for better tool control.
That is why this article will break down the details of why tool control is crucial for construction projects and provide insights into how it can be implemented into construction workflows.
In this article...
Makes Employees More Efficient
In construction, efficiency is paramount.
And when construction workers spend a portion of their time every day on activities as trivial as looking for misplaced tools, this can eat into their productivity.
For instance, if they spend only 10 minutes a day searching through the construction site for missing tools, this can amount to an estimated 43 hours each year.
That is almost two work days lost simply hunting down tools.
While larger equipment like bulldozers and cement mixers is not likely to completely vanish off the site, smaller tools such as wrenches and hammers are easier to misplace and harder to locate.
However, the process can become much more straightforward by establishing tool control through the use of tool tracking software.
It can bring a lot of benefits in terms of efficiency to the table, as summed up in the graphic below.
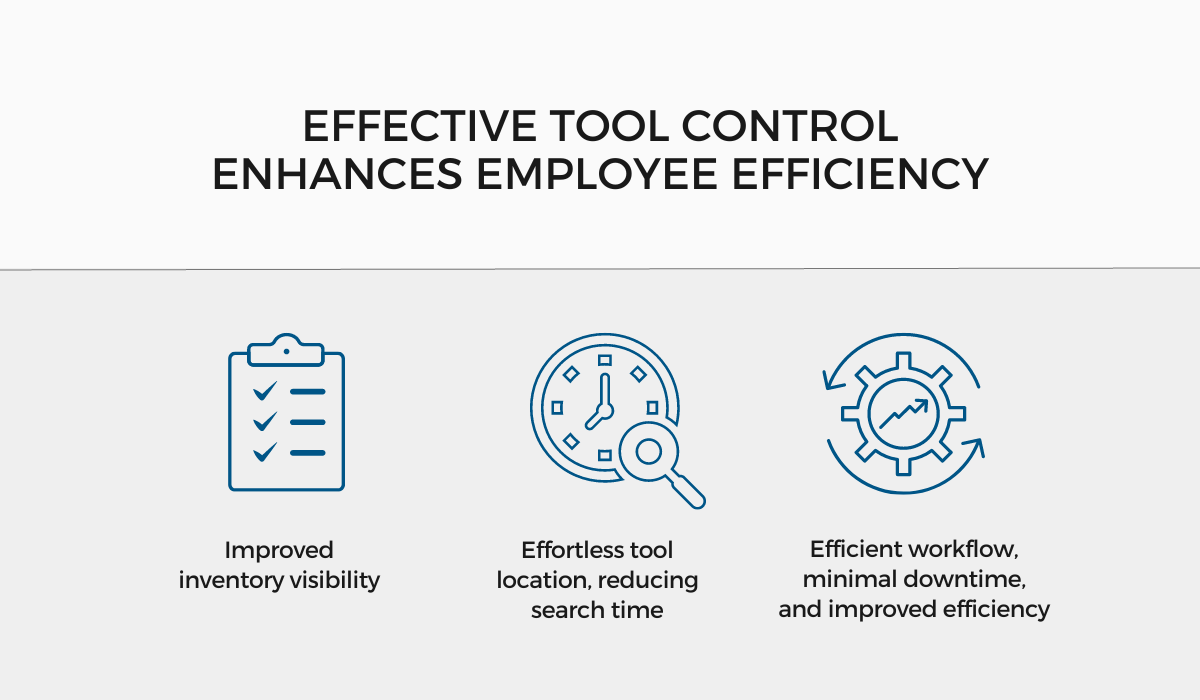
For starters, it can provide real-time inventory visibility, which allows workers to quickly determine where a specific tool is stored and also inspect its availability.
This eliminates the need to personally look for tools in the tool storage area.
Tool locations are clearly marked and logged, meaning workers can instantly find what they need and get on with their tasks.
This direct access to information reduces downtime significantly and improves efficiency.
Time is a valuable resource in the construction industry.
By implementing effective tool control measures, you can ensure that construction workers have the right tool at the right time without wasting time searching for it.
Ensures That Tool Are Calibrated
Proper calibration of tools is an important part of the company’s tool maintenance processes.
The process in itself isn’t complex, but it does turn into a challenge when you have a larger quantity of tools that need to be calibrated at different frequencies and intervals.
For example, some manufacturers require devices to be calibrated after a certain number of use cycles, a degree of wear and tear, time used, or mileage.
These specifications might vary significantly from one tool to another.
Keeping records of their next calibration dates in, for instance, Excel spreadsheets can become quite burdensome.
Plus, there is a higher possibility of human error and some tools simply being forgotten to be calibrated.
Uncalibrated tools can have far-reaching consequences in the construction industry, as shown in the following graphic.
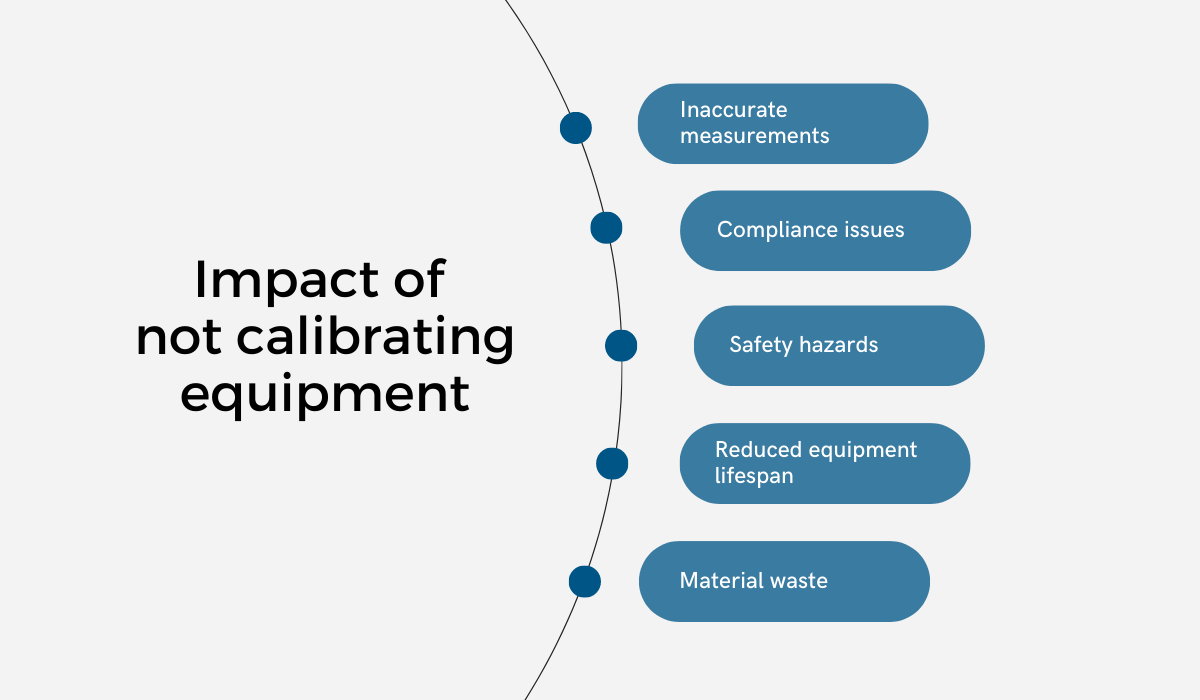
That is why it is important to have a tool control system in place that will allow you and your team to schedule the calibration of tools.
This system will record data such as the date of the last calibration, who performed it, any adjustments made, and the date of the next scheduled calibration.
At the same time, it will alert the workers every time a tool is due for calibration.
A well-established tool control mechanism does more than streamline the calibration process.
It ensures that the tools are always properly calibrated and at the level of quality required for their smooth operation.
Guarantees Proper Tool Maintenance
Every tool in your construction inventory calls for regular preventive maintenance.
The reason for this preventive maintenance is to keep the tools in top working condition, improve worker safety, minimize unexpected downtime, avoid expensive repairs, and ensure regulatory compliance.
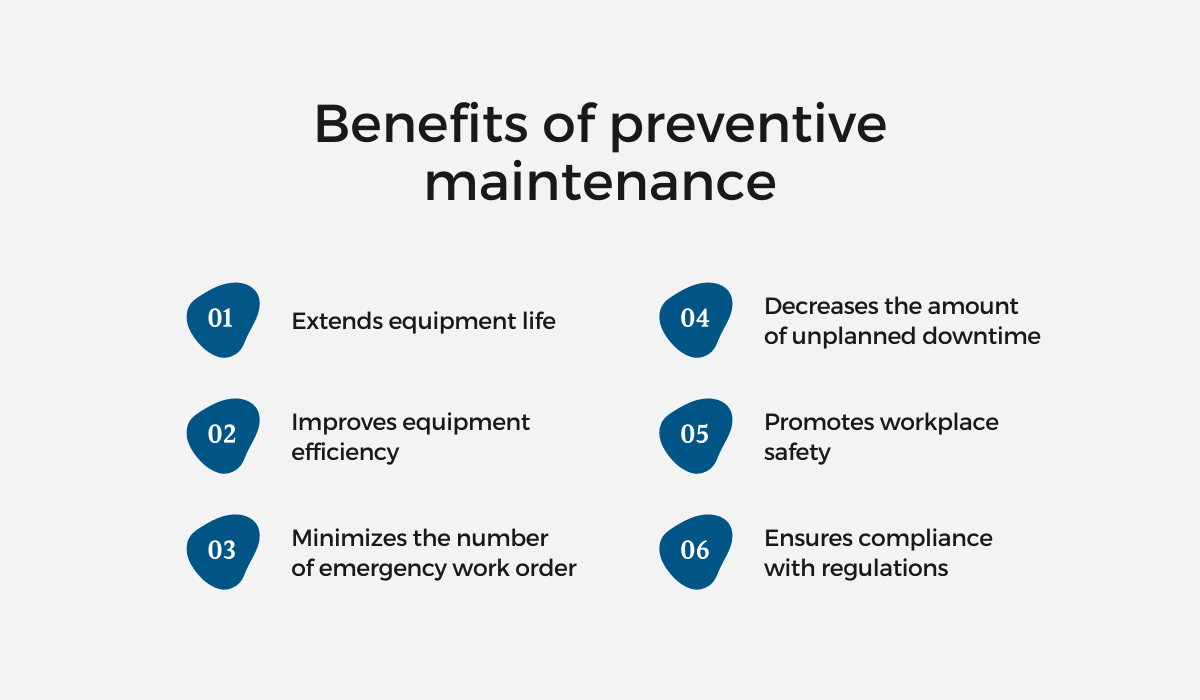
This can involve calibration, dust removal, specific cleaning procedures, parts replacement, and many more crucial tasks, as you can explore in this preventive maintenance checklist.
However, keeping tabs on every single tool to ensure that it is in good working condition and that it has undergone regular maintenance checkups and repairs can be a logistical nightmare.
A centralized tool control system, however, can flip the script and make preventive tool maintenance far more manageable.
For instance, tool tracking software enables maintenance staff to access a wealth of information about every tool, such as its manufacturer and date of purchase, manuals, warranty information, and records of major maintenance actions.
From there, you can create tasks for individual tools, assign work orders to your maintenance team, and set automatic service alerts.

Your team can then update tool data after the completion of scheduled inspections, maintenance, and repairs.
This proactive approach ensures that tools are always in optimal condition and prevents unexpected breakdowns, delays, and any associated downtime.
It also eliminates guesswork about when it is time for the next service, thereby nipping bigger issues in the bud with timely maintenance.
Improves the Safety of Employees
Maintaining a safe construction site is a challenging task, but one significant stride in this direction can be chalked up to good tool practices.
Having control over your tools considerably enhances employee safety and reduces the risk of on-site accidents.
To give you a clearer picture, let’s consider statistics.
Research from the Bureau of Labor Statistics reveals that construction workers are particularly at risk of injuries due to various falls, slips and trips, as well as different types of contact with equipment.
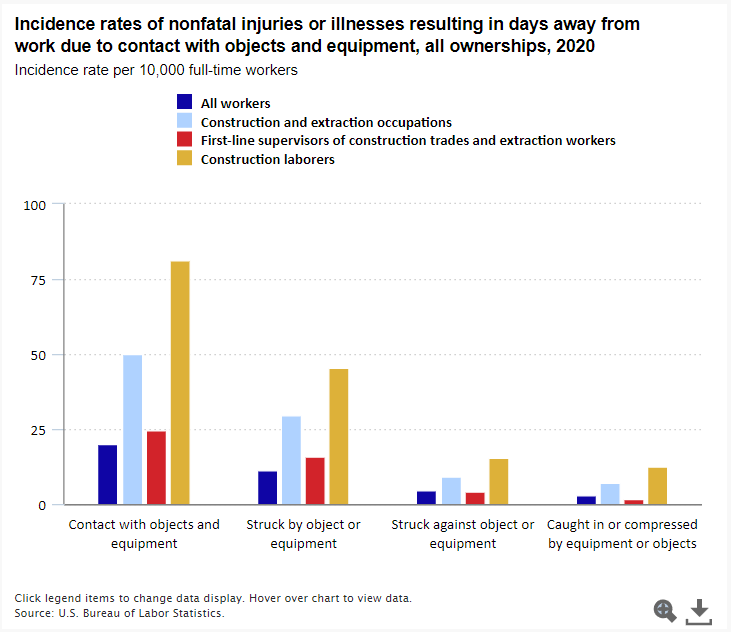
Adding to this, another research points out that 61% of workplace injuries caused by electricity happen right in the construction sector.
The culprits here could be anything from malfunctioning tools to a simple misuse of tools by employees.
These facts position construction not just as a high-risk industry but as one of the most dangerous industries around.
Given these stakes, good tool control is absolutely essential to maintaining a safe construction site for employees.
Here are the key facets to focus on:
- Keeping a clean construction site
- Setting up regular maintenance schedules
- Ensuring only trained personnel handle specific tools
- Using a tool tracking software
Without careful tool control, construction sites can become cluttered and unorganized, and tools may not be properly maintained.
This can lead to multiple safety risks, from tripping and falling hazards to more severe accidents caused by malfunctioning tools.
Another crucial aspect of tool control is ensuring only qualified personnel use certain tools.
This means keeping an eye on who has the right training for specific tools and avoiding those tools landing in unqualified hands.
By implementing these practices, construction companies can make significant leaps in improving the safety of their employees on construction sites.
Reduces the Total Cost of Ownership
Tools are one of the most substantial investments construction business owners have to make.
While purchasing high-grade tools is certainly a priority, effective tool control plays a pivotal role in maximizing the long-term value and returns from these investments.
This practice is a strategic way to optimize operational costs and enhance tool profitability.
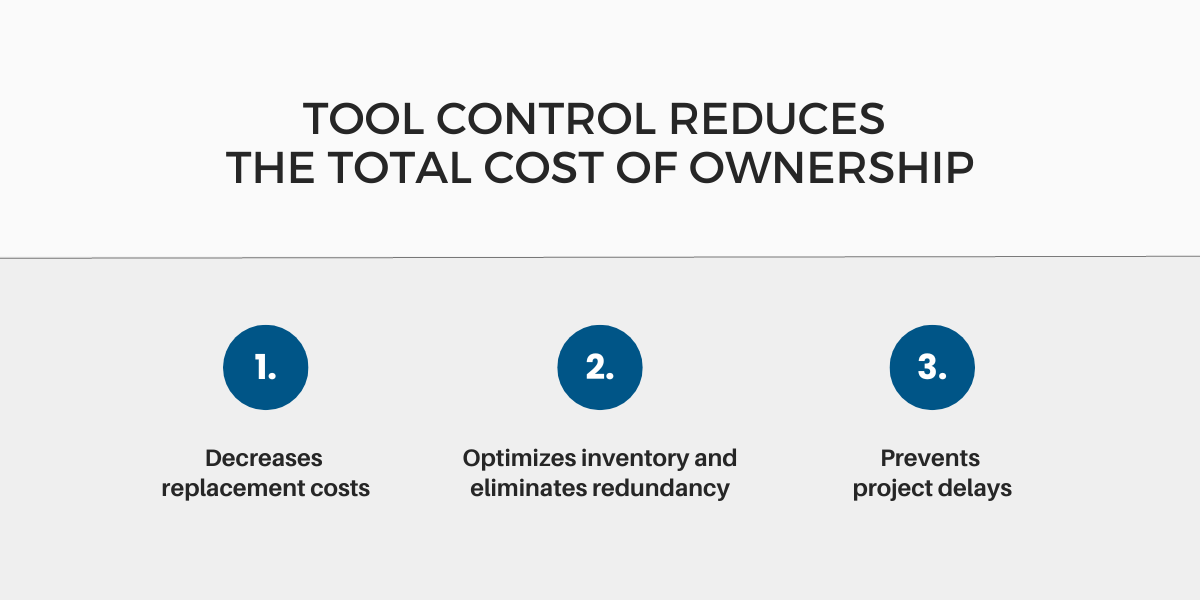
To begin with, tool control reduces replacement costs.
The initial investment in purchasing tools is a given. Yet, repeated expenditures on replacement purchases can significantly drive up the overall cost of tools.
Implementing a structured tool control protocol paves the way for regular cleaning and servicing schedules that ensure the tools not only perform better but stand the test of time.
Tools that undergo routine maintenance are less likely to break down, thereby cutting down on the frequency and cost of replacements.
Because tools aren’t at risk of suddenly breaking down, tool control helps prevent project delays.
A construction project is only as smooth as the workflow that governs it.
If your tools are in sub-optimal condition or unavailable when needed, the ripple effect can result in project delays, cost overruns, and possibly even penalties.
In fact, 50% of unplanned downtime results from a lack of spare parts.
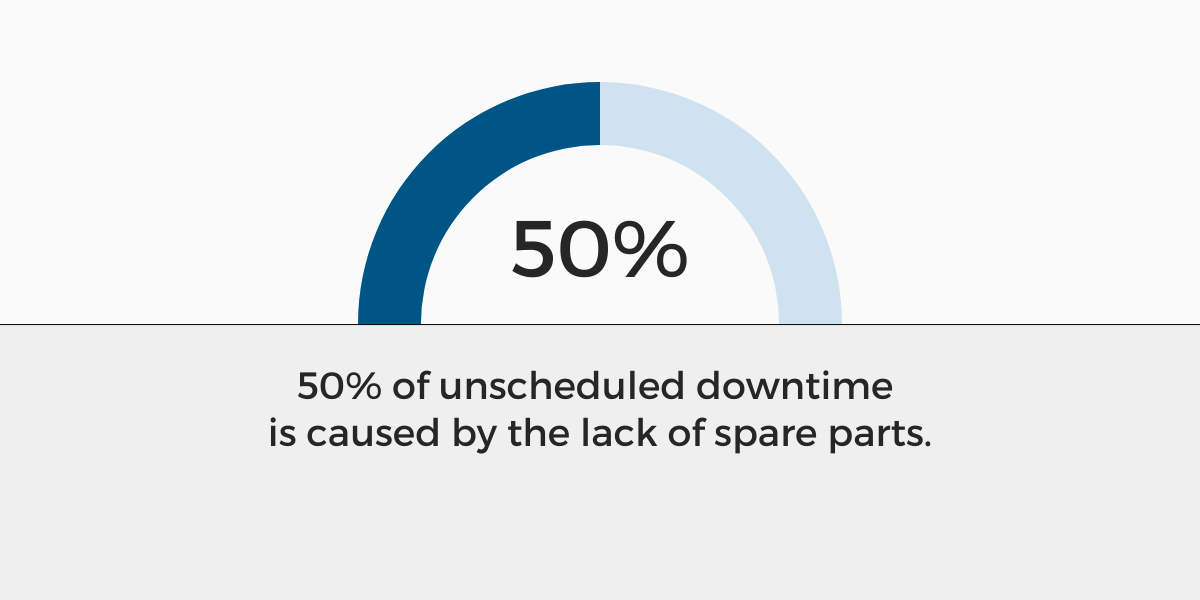
Implementing a stringent tool control system makes sure that tools are always available, helping to prevent such scenarios.
Along with ensuring tool availability, proper tool control also optimizes inventory by providing you with complete visibility.
Knowing what to procure and when is crucial. By systematically tracking the types and quantities of the tools available, you can avoid purchasing tools you already own.
Similarly, understanding which tools are rarely used can guide you toward more cost-effective decisions for future investments.
For instance, if a tool is seldom used, it might be wiser to rent it for specific projects rather than to own it.
Therefore, effective tool control is a strategic move that can result in reducing the total cost of ownership of tools.
Prevents Tools From Going Missing
Tool misplacement, loss, or theft is more than just a mild inconvenience. From project delays to spiraling costs, the implications of lost or stolen tools can be far-reaching and damaging.
In fact, theft poses a far greater risk than other mishaps such as vandalism, fire damage, or even natural disasters.
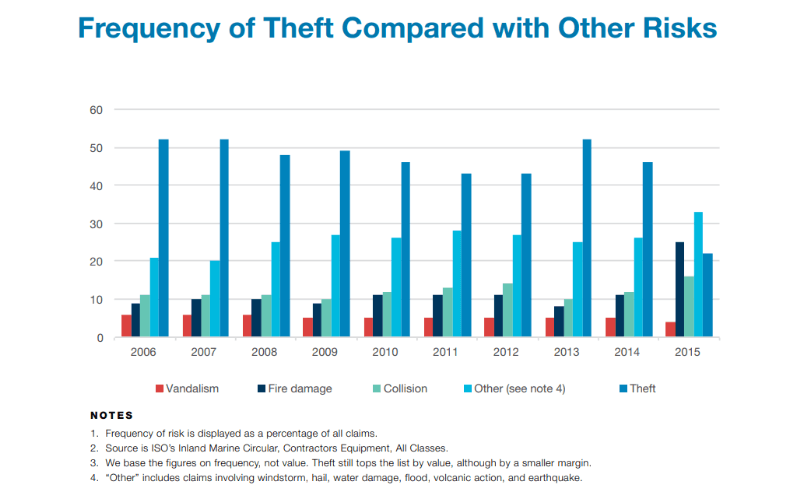
With stolen equipment costing the construction industry nearly a billion dollars annually, mitigating this risk becomes a priority.
That is where effective tool control strategies come into play.
Using GoCodes Asset Tracking as a case study, let’s explore how tool tracking software can help prevent tools from disappearing.
GoCodes Asset Tracking enables you to implement a barcode-based tool tracking system into your workflow.
The process begins with assigning unique QR code labels to individual tools.

These labels, which can be easily attached to even your smallest tools, act as a digital ID for each tool.
When these QR codes are scanned with the GoCodes Asset Tracking app, the tool’s location is updated in real time because GoCodes Asset Tracking uses the GPS location of the smartphone as the location of the tool.
This means that even if a tool gets misplaced, lost, or stolen, you will always have its last documented location available for reference.

Also, the check-in and check-out feature makes sure every tool’s last known user is recorded.
This clears the fog on where, when, and by whom the tool was last used, instilling a sense of responsibility among the workers using them.
Aside from QR code labels, other methods of tracking tools are also available, such as Bluetooth beacons.
Beacons are compact, battery-powered sensors that can easily be attached to any asset.

These beacons broadcast essential information to nearby Bluetooth-compatible devices, such as smartphones.
The result? Remote tracking that pinpoints your tool’s precise location in a 300 feet (or 100 meter) radius, which is almost the size of a football field.

As you can see, the combination of powerful tool tracking technology, an effective check-in and check-out system, and monitoring onsite tool movement reduces instances of missing tools.
And the next time a tool goes missing, you will know exactly where to find it.
Speeds up the Tool Auditing Process
In the construction industry that acts according to strict deadlines, an inefficient tool auditing process can act as a bottleneck.
It can slow the staff down and take up precious hours that could have been better used on actual construction work.
Thankfully, this doesn’t have to be the case. A solid tool control system can be a game-changing solution that can speed up the auditing process.
To understand how this can be achieved, it is essential to outline how those two interact.
Auditing is the process of taking inventory of all tools, which is in most cases a long and tiresome manual process.
However, if you switch to a method like code label tracking, you can cut down on auditing time.
When the audit is underway, your team can simply scan the QR codes attached to the tools. The software will then immediately record scanned tools, thereby simplifying the audit process.

Additionally, during an audit, managers can quickly identify the employee who is currently in charge of each tool.
For instance, say you are auditing power tools.
You can now efficiently trace their current location and the person responsible for them. No more going through piles of documents or trying to remember verbal commitments.
Everything is there at a glance.
With all tool-related information in one place, performing an official audit becomes only a matter of verifying the existing data.
This transparency considerably reduces the time an auditor would otherwise spend manually verifying the whereabouts of each tool.
Therefore, with consistent tool tracking and a centralized system, audits become less of a burden and more of a routine check.
Conclusion
Having organized, well-maintained, and properly tracked tools is more than just a nice-to-have for construction companies.
It’s essential for increasing worker efficiency, fostering an accountable work environment, reducing replacement costs, and streamlining the auditing process.
With good tool control, you will also strengthen your safety protocols, ensuring that everyone on the construction site can work in a secure environment.
Additionally, you will build a reputation of reliability and professionalism, which can lead to increased client satisfaction and more business opportunities.