Companies often view safety inspections as a hassle, despite such checks improving the safety of the worksite and their employees.
This article will explain the benefit of construction site safety for companies, suggest some ideas for better safety plans, and advise on writing detailed safety reports.
If you take the safety of your employees seriously, this article will help you demonstrate it!
In this article...
What Are Construction Safety Inspections
Safety inspections on your construction site help you understand whether you follow the federal and local state regulations.
Regulations ensure the safety of the workers, which should be the company’s top priority.
Though very important, safety checks are rarely seen as a priority, even though the number of construction-related deaths is staggering.
One out of five worker deaths in 2019 were related to construction. No wonder the law wants to protect construction site employees as much as possible!
The safety inspections on the site consist of a person checking many aspects of the workplace, usually using a checklist, and trying to find any possible safety risks.
These risks entail:
- inadequate protective equipment
- faulty tools
- assets used for something other than their purpose
- insufficient fall protection
- irregularities in other vital parts of the construction site operations.
Such checks aim to discover safety hazards and report them to the employer responsible for eliminating them in order to create a safer working environment.
Safety inspections help employers discover potential hazards and remove them before they cause injuries, downtime, and monetary losses.
Therefore, having a safety inspector on your work site might not be as scary as it sounds. After all, they will point out things you might have missed and help you prevent losses.
Types of Safety Inspections
Inspections come in many different forms, depending on the project’s importance, safety risks, number of workers, and various other factors that might affect the need for such checks.
They can be formal or informal.
Supervisors and safety representatives perform the former on a weekly or monthly basis, depending on the size of the site and the amount of equipment used.
On the other hand, supervisors do informal inspections whenever they are on the worksite since they need to spot any safety issue and prevent it from causing damage during operations.
For example, they can carry out daily checks to spot any unused equipment left behind on the site, incorrect tool usage, or insufficient personal protective equipment (PPE).
Both types of inspections have the same goal: finding potential issues and reporting or correcting them as soon as possible.
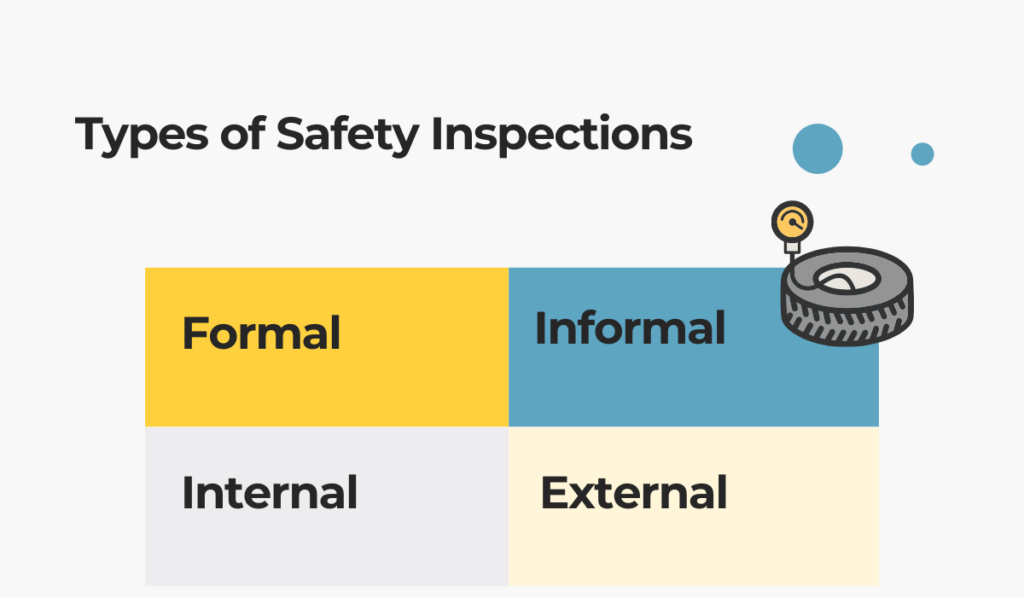
Based on the type of professional who performs the inspection, they can be internal or external.
Suppose you or the contractor want to understand how well you comply with the company and federal regulations. In that case, you can send an internal specialist or supervisor to inspect the site and find issues.
On the other hand, in cases where impartiality is important, external experts are the way to go.
For instance, you can hire an external expert to perform safety checks on your work site since this person won’t be biased and might spot aspects your employees have missed.
In the US, the Occupational Safety and Health Administration (OSHA) performs safety inspections to ensure that the work complies with federal safety regulations.
If they find irregularities, they can issue citations, penalties, and fines.
Importance and Benefits of Safety at the Construction Site
The cost of below-standard safety in the workplace is a lot higher than most expect—penalties can reach hundreds of thousands of dollars a day per violation, while the cost of work injury reached $171 billion in 2019.
Employees who invest in the safety of their worksites and employees can improve productivity, decrease downtime, injuries, and workplace accidents while saving up on accident-related costs.
Here’s why workplace safety is essential for employers!
Worker Retention
When you invest in workplace safety, you positively affect worker satisfaction and, therefore, retention.
Workers who feel appreciated and cared for are more likely to stay with the company—it’s as simple as that.
If you show your employees that you care about their health and safety, your team will feel that you’re putting them and their well-being first.
You can do this by creating and promoting a company safety plan, enforcing safety rules, and carrying out frequent inspections to ensure that everyone is safe.
Different agencies have come to the same conclusion—if you invest in construction safety, your investment will pay off.
Some state that for each dollar you invest in promoting safety and training your workers, you get four or more dollars back in all the prevented injuries, downtimes, and equipment breakdowns.
Workers appreciate employees who invest in their health and safety and are more likely to keep working for such companies.
Reputation
Safety-related injuries can damage your reputation.
If you don’t invest in safety or neglect to inspect it often enough, accidents might happen.
An employee might get injured and suffer long-lasting consequences, disabilities. Sadly, such accidents often result in fatalities— in the previously cited report, OSHA cites 15 construction site deaths a day.
If someone gets injured or loses their life on your construction site due to the lack of safety precautions, you risk losing employees and money in penalties and fines you will have to pay.
Maybe most importantly, your reputation will take a hit.
If your reputation takes a hit, contractors will be less likely to want to work with you.
After all, who would want to be associated with a company that doesn’t put their employees’ safety first? A bad reputation equals fewer earnings for you.
Your reputation is an intangible asset that goes a long way.
If it’s negative, you’re less likely to attract qualified workers.
The highly skilled ones will get better offers—if they value their safety, they will choose to work for companies known for investing in worker health and safety.
A bad reputation caused by workplace injuries can cost you money, business partners, and employees.
Operations
If you minimize the risk of workplace accidents, your operations can go on uninterrupted.
Investing in safety at the worksite ensures that operations keep going.
For example, suppose you’re not careful enough about how safe your employees are, and an accident happens.
In that case, you will have to stop working and take care of the employee.
In addition, the supervisor will have to report the accident, and in case of more severe injuries or fatalities, authorities will investigate the circumstances.
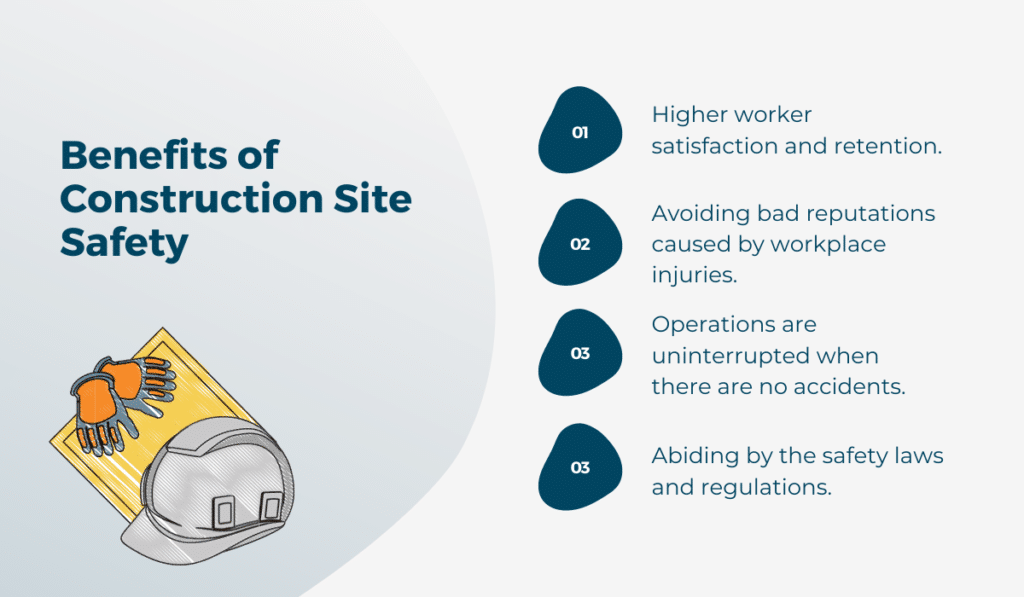
All of these points cost you time, and in the construction industry, time is money.
You have tight deadlines to follow, so you can’t afford to stop working, even for a couple of days.
On top of that, your team on a different construction site might need the equipment.
That means that if you don’t finish on time, an accident that happened on one worksite can cause a delay on another one.
In addition, you might need to hire more employees to finish on time.
Without workplace injuries and accidents, you are decreasing the risk of project downtime and its costs.
Regulations
You can be more confident that you are abiding by the safety laws and regulations if you invest in safety plans and training.
When your employees understand the safety standards, they are more aware of any instances when the worksite isn’t meeting them.
With proper training, you can teach employees how to spot possible safety hazards on their own and report them straight away, diminishing the risk of workplace accidents.
It’s your duty as the employer to follow what the law defines as the industry standard.
Your employees mustn’t be at risk while working for you, and it’s always the contractor and employer’s responsibility to respect regulations.
After all, if OSHA or a different authority discovers a hazard, you will pay the fines and penalties, not your employees.
To prevent that, ensure that each employee can recognize and report workplace hazards.
Following laws and regulations helps you avoid fines and injuries.
Best Practices for Construction Safety Inspections
What are some things you can do before and after safety inspections?
Regardless of whether you’re the one carrying out an internal safety check, these are tips that can help you promote workplace safety and stay organized.
Create a Safety Inspection Checklist
Whenever you want to perform a safety check, you need to inspect all factors that can pose a risk.
Doing this at the top of your head is challenging, especially if you do it daily or weekly—you might miss a certain point a time or two, and there can be some you constantly miss.
To prevent this from happening, you should create a checklist. That way, you will ensure that all relevant points are listed.
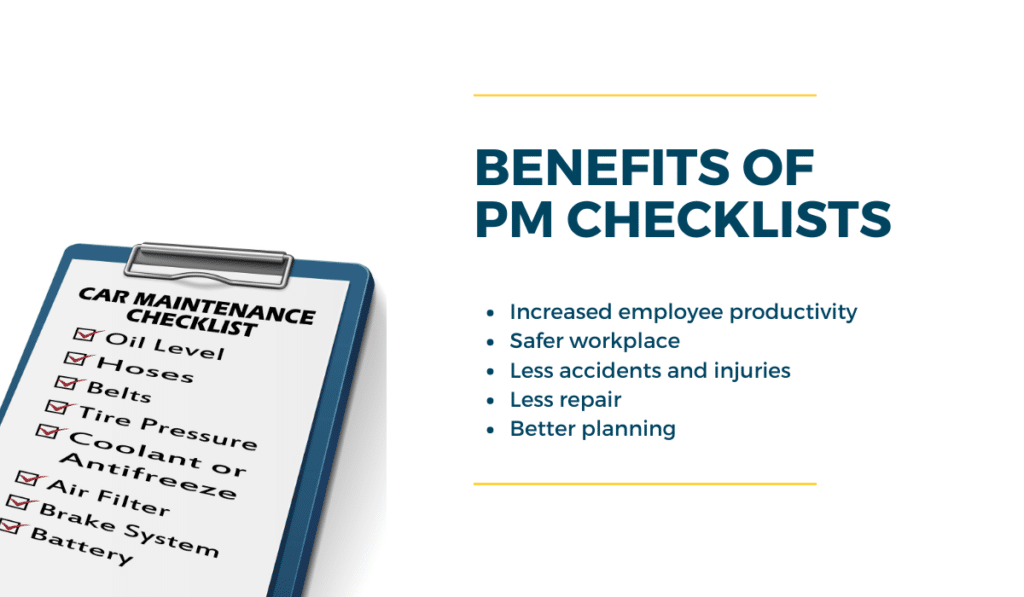
Then, the supervisor or another employee can check everything necessary, decreasing the risk of a construction site accident or injury.
Of course, when thinking of points to cover, consult employees, industry standards, and laws to create a comprehensive list that will eliminate threats.
The list should cover many different aspects found on your worksite, from protective equipment, fall protective methods, electrical concerns to scaffolding and equipment and tools.
For each point, you need to check if the condition exists, if it’s properly used, and its state.
Creating a comprehensive safety inspection checklist can help you find and eliminate potential hazards.
Make Plans
Planning makes the safety inspection go easier and quicker.
Before a safety inspection, you need to know the risks and understand how to remove them.
In fact, you should always be aware of potential hazards and how to solve them, regardless of safety checks.
You must figure out how to collect the data on the site, for which you can use carefully developed checklists. Once you know that, you can determine what to do with the information.
Decide how to share the findings with others and who needs to see them.
If the results are concerning, should you set up an urgent meeting to discuss possible solutions?
Finally, determine whether you need to shut the site down until the issues are resolved or not.
When beginning to work on the site, identify hazards and consider ways of minimizing or removing them.
That way, you can eliminate most issues before they even get a chance to pose a threat to your employees.
Planning hazard solutions and actions helps you prevent worksite issues.
Inquire About Actions Taken
Inquire about the actions taken after each inspection to ensure safety.
Even if you’re not the one who has performed the safety inspection at the worksite, follow-up is a step you shouldn’t miss.
Why? It’s not enough to just get a list of things you’re doing wrong, put it away in some drawer, and be done with it.
You need to address the issues you, your supervisor, or third-party auditors discover during the check, otherwise you’re leaving safety hazards unattended and endangering your employees.
Maybe you’ve had a meeting with your team to go through inspection results and concluded that none of the points pose a severe threat.
Regardless, you shouldn’t turn a blind eye to an unsafe aspect of the workplace because it can quickly become a real danger.
If an accident happens after you become aware of the issue, the fines and penalties will be even higher, and so will the degree of responsibility.
Following up on inspections ensures that workplace safety threats no longer exist.
Analyze
Analyze what caused the safety hazard to improve the conditions in the workplace long-term.
You shouldn’t stop working on your safety process after successfully removing the threats found during the inspection.
Instead, put some effort into determining why these issues even occurred.
Such analysis can help you get to the bottom of the issue at the construction site and help you prevent similar threats from emerging in the future.
Suppose someone noticed that your employee isn’t using equipment properly.
Let’s say you’ve immediately removed the worker from the site and organized extensive training to ensure they know how to operate the equipment safely.
However, that is not enough.
You have to ask yourself why this person didn’t have this knowledge before to understand the issue.
For example, maybe your trainers skipped a step, or the employee didn’t attend the training, but nobody followed up on it.
If you get to the bottom of why each safety hazard appeared, you will successfully remove current and prevent future threats.
Involve Managers
When you include management in the safety process, you stress its importance.
Your managers should be involved in safety inspections as much as possible—they can even perform checks, discuss the results, and help you analyze root causes.
This step will make them understand just how vital construction site safety is to you and the company.
Such involvement from your side will also show the workers that you care. Most of them believe that managers have no interest in what is happening on the site and have more critical issues.
However, if they understand that even top management is involved in construction site security, your employees will feel that the company cares about their wellbeing.
This feeling will affect their engagement at work.
The project managers should also come to the worksite, inspect it, remind workers of the safety code, and report any irregularities.
Also, you need to clarify to the employees that they can report any hazards to management, thus fostering a relationship.
Involve your managers in the safety process to ensure everyone understands its value to the company.
Train the Team
Training allows your employees to prevent, notice, and report safety hazards.
Most companies invest in safety training during the onboarding process and occasional refreshment training on more complicated things, and they think it’s enough.
However, 55% of employees disagree and say they want to receive more training.
It’s no surprise that employees feel that way about safety training, considering how many injuries or fatalities happen in this industry.
After all, education helps them prevent accidents and notice a safety hazard before it damages equipment or harms employees.
Because of this, OSHA considers training one of the four pillars of health and safety compliance, further accentuating its importance.
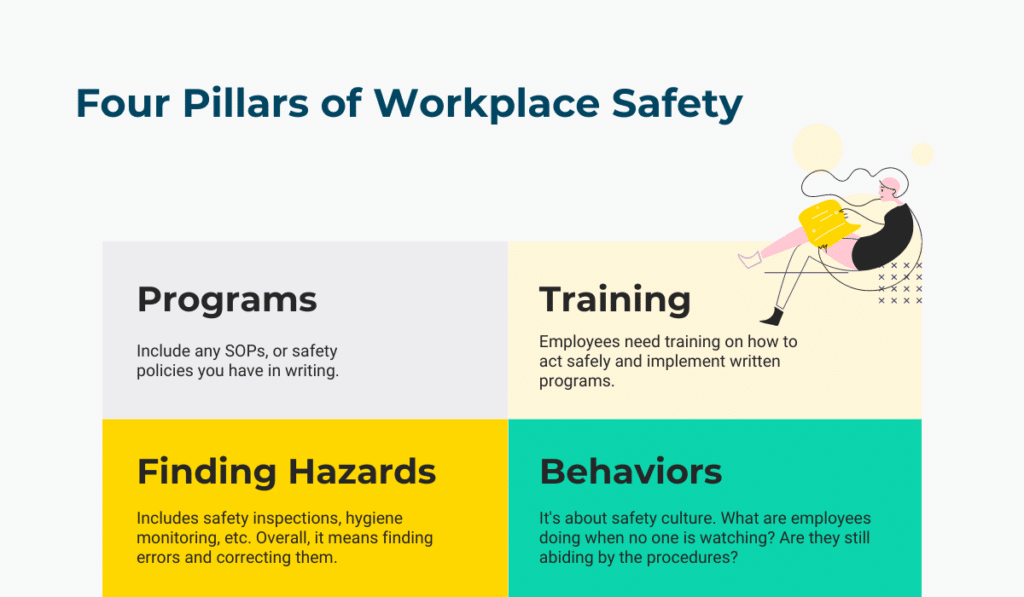
The employees should receive initial detailed training on safety and additional, frequent refreshment training.
The materials on safety, operating equipment, wearing PPE, and similar safety issues should be on hand at all times, allowing them to have a look whenever they need to.
Provide sufficient safety training to all employees and give them access to safety materials.
How to Write Excellent Internal Safety Inspection Reports
If you’re the one performing an internal safety inspection at one of your construction sites, you want to ensure your report is as thorough as possible.
Quality reports will help your team understand the exact issue on the site, allowing them to come to a solution faster.
To hone your report writing skills, consider following one of these pieces of advice.
Provide Details
Make your reports as detailed as possible to ensure you’ve covered everything.
When writing reports, you have to be sure that you’ve named every potential hazard you’ve seen during the inspection.
There may be many, but try to think of why they’re posing a threat to the employees’ safety and how they can fix the issue.
The more details you give, the easier it will be for employees to understand where the threat lies and remove it.
You should attach photos of the unsafe aspects of the workplace to your reports to ensure everyone understands precisely what you have found.
If you’ve found more issues, classify each one according to the degree of hazard, which will allow the team to prioritize better.
When doing this, you can explain why something is very hazardous while something else isn’t as urgent.
There is a chance someone else wouldn’t have considered that same aspect an issue, so it’s always helpful to write down how you came to the conclusion that it poses a threat.
For your report to be good, you need to add details and explain your findings.
Document Observations ASAP
Document your findings while on the worksite to be sure you mention everything.
When you’re doing safety inspections, each potential hazard is essential.
Because of this, you might feel that there’s no way you’d forget it. After all, every finding poses a threat to employee safety and seems just as important as the others.
However, unless you write them all down and take pictures, it’s easy to forget about them.
In addition, you can’t predict how many threats you will find and what will happen after the inspection.
Therefore, it’s more convenient and reliable to document the issues as soon as possible, preferably during the review itself. Equipment management tools like GoCodes Asset Tracking allow you to add details about each item, such as:
- inspection type
- inspection findings
- service history
- next service date
- images
- user manuals or other documentation
- Warranty expiration, etc.
Using software like GoCodes Asset Tracking, you’ll have real-time observations backed up by photos you will add to the report, and you will be sure you haven’t forgotten anything. Plus, you have the ability to generate custom reports on your equipment.
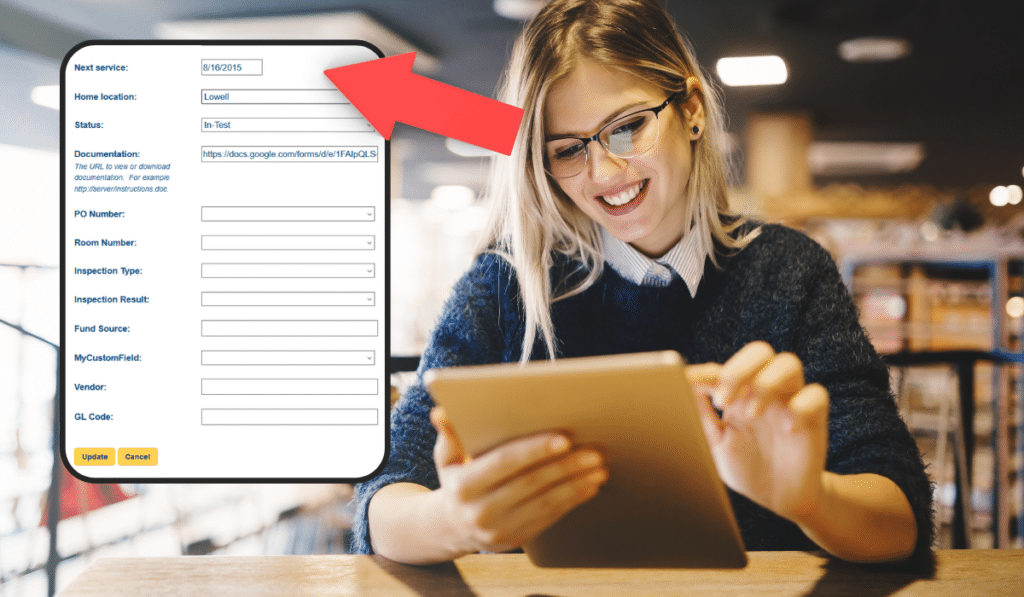
When conducting inspections, each potential hazard has to be identified, as it can cause a lot of damage to the company and the employees.
The thing you miss might cause an accident the next day. To prevent that, be diligent about making notes.
Immediately noting your findings ensures you don’t forget to mention a hazard.
Write Clearly
Be clear when mentioning each hazard to ensure their removal.
Don’t complicate your writing. Using words that others may find challenging or hard to understand won’t help the report. In fact, it will make it worse.
When you conduct a safety inspection, your main goal should be to find weak safety spots and notify the people in charge to eliminate any issues.
That’s why the report should be clear and concise—everyone has to understand what hazard you’ve found, why it’s dangerous, and how they should fix it.
It’s best to keep the report professional and straightforward to avoid misunderstandings and leave no room for misinterpretation.
While this may seem challenging for those not used to summarizing the main issues while still giving enough details, practice makes perfect.
You will get better at getting your point across effectively with every report you hand in.
Describe your findings clearly and concisely to maximize understanding.
Create a Template
Use a professional company template to ensure standards.
When writing a report, you might decide to use a template you find online. Making your own might seem like a waste of time.
However, it’s better to create a layout with your company logo, one that suits your needs, and includes all the points related directly to your company, than to use someone else’s template.
The elements that apply to another construction company might not apply to yours, even though you should have the same standards.
You can use other people’s templates and layouts as a reference, but it’s vital to add company-related specifics.
Whoever performs internal safety checks can use the template, making your reports standardized.
When your reports have the same outline, you can easily compare them and draw conclusions.
If your report looks completely different than the next person’s, it’s hard to keep up with specific points.
Also, if you add other reviews into the mix, you will waste a lot of time trying to find the same point in all of them.
Using a company template helps standardize and speed up the reporting process.
Note the Positive Aspects
Include positive findings in your report to make everyone more receptive to the negative ones.
A safety report doesn’t have to be entirely negative—you can add some positives to it.
The company and employees will be more receptive to reading a review that doesn’t show them in a wholly negative light, even if that’s not the point of safety reports.
You must report on any safety issues you find during your check, but remember that you are there to help the company improve and enforce safety standards.
Most employees and businesses dread safety reports because of the list of things they are doing wrong, starting from PPE to equipment handling.
Employees may worry about the consequences of negative feedback, while employers might feel overwhelmed with the number of hazards present at the worksite.
If you notice improvements during inspection regarding the points you’ve covered previously, compliment the employees on their work and include it in your report.
This way, you’ll make it clear that you value effort and growth and that you’re willing to reward those who follow instructions.
Positive reinforcements can go a long way if included in your safety inspection reports.
Conclusion
Construction site safety inspections help you retain workers, have a good reputation, and adhere to regulations while keeping your operations safe and running.
Before conducting internal checks, create a detailed checklist, make plans to fix issues, and follow up on previous findings.
Whenever you find a safety hazard, determine the cause to nip the problem in the bud.
Training your employees will take your safety plans to the next level—they will know how to use equipment, help others when they’re not, and report hazards to management, which should be involved every step of the way.
Follow this advice and stay safe!