Key Takeaways:
- Spreadsheets leave room for errors and can’t keep up with frequent updates.
- Effective inventory management solutions are mobile-friendly and interoperable.
- Real-time inventory tracking incorporates various tagging methods.
- Automated low-stock alerts are both a fail-safe and an efficiency booster.
Companies of all sizes are eager to curb inefficiencies that erode their profit margins.
However, few of them are considering revisiting their inventory tracking practices.
Inventory is the lifeblood of every construction business, ensuring optimal resource allocation and smooth implementation of projects.
In this article, we’ll tackle poor inventory management by covering six essential inventory tracking tips for enhanced efficiency and accuracy.
Want to stay ahead?
Then let’s start!
In this article...
Don’t Use Spreadsheets
Spreadsheets don’t go well with efficient and accurate inventory management.
In fact, they actively hinder it.
There are multiple reasons why this method of managing inventory is considered outdated today, including:
- Greater risk of errors
- Time-consuming input
- Lack of real-time visibility
The indications of major inefficiencies were there for a long time, with one 1998 study revealing that 90% of spreadsheets with more than 150 rows have at least one major mistake.
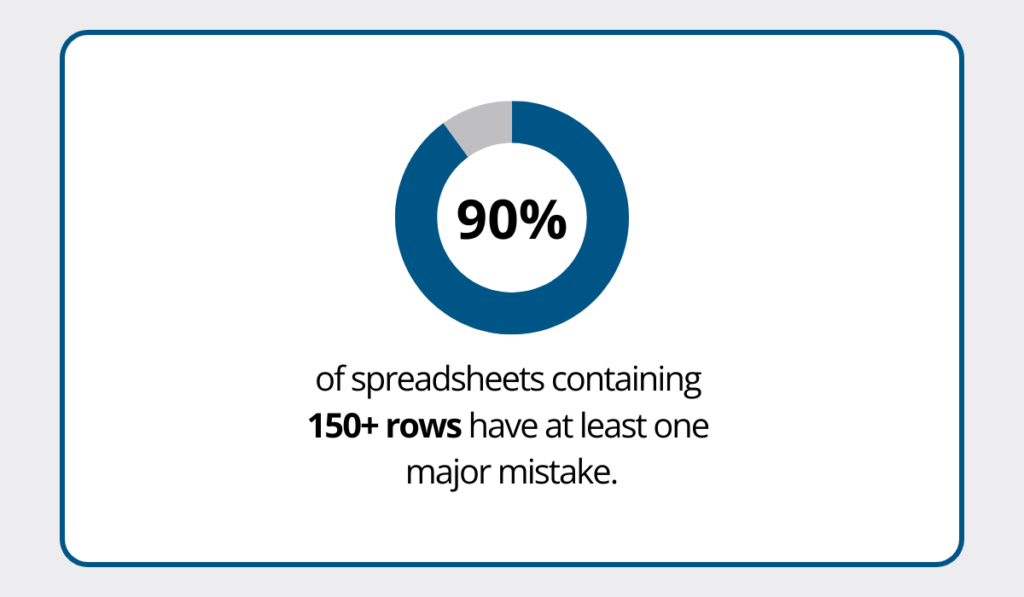
Illustration: GoCodes / Data: Journal of Organizational and End User Computing
The root cause of these inaccuracies is human error, which is imminent given that spreadsheets require plenty of manual data entry.
Despite this discouraging statistic, legacy systems like Excel spreadsheets are still around because they’re familiar, affordable, and highly versatile.
However, experts like Peter Nicholson, a Division Systems and Data Analyst at ITW Appliance Components, warn that this versatility is often a double-edged sword:
“You’ve got to start deciding what Excel should and shouldn’t handle. It can do anything, but it shouldn’t really be doing everything.”
Inventory management has its fair share of challenges no matter the industry, from mismatches between physical inventory and records to supply chain disruptions.
Since spreadsheets make it difficult to capture and track the changes in critical data, inventory issues like understocking and overstocking only get worse.
Imagine having to pause an entire construction project because multiple versions of a spreadsheet led to the site manager overlooking missing essential parts.
With all this in mind, it’s no wonder why the news of a Formula 1 team using Excel for inventory management caused quite an uproar.
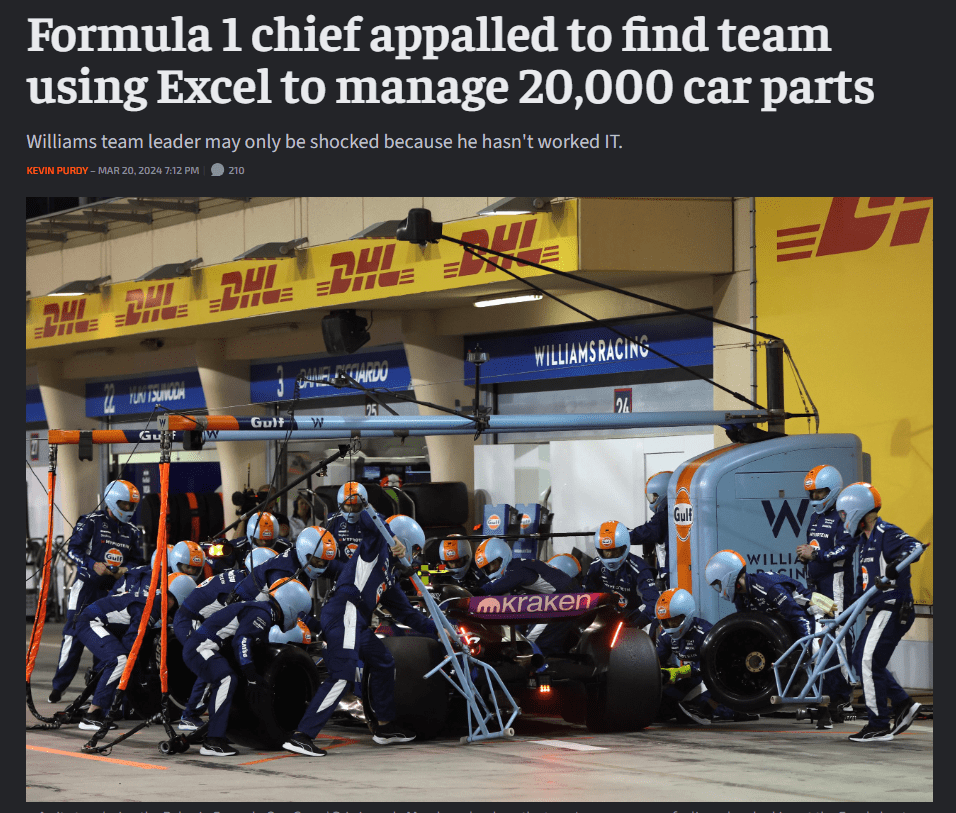
Source: Ars Technica
Besides the difficulties of managing such a sheer number of car parts using Excel, the massive list lacked data on the cost and production time of each component, as well as service logs.
James Vowles, the newly appointed chief of the F1 team in question, noted a range of issues, concluding that the list was unsalvageable.
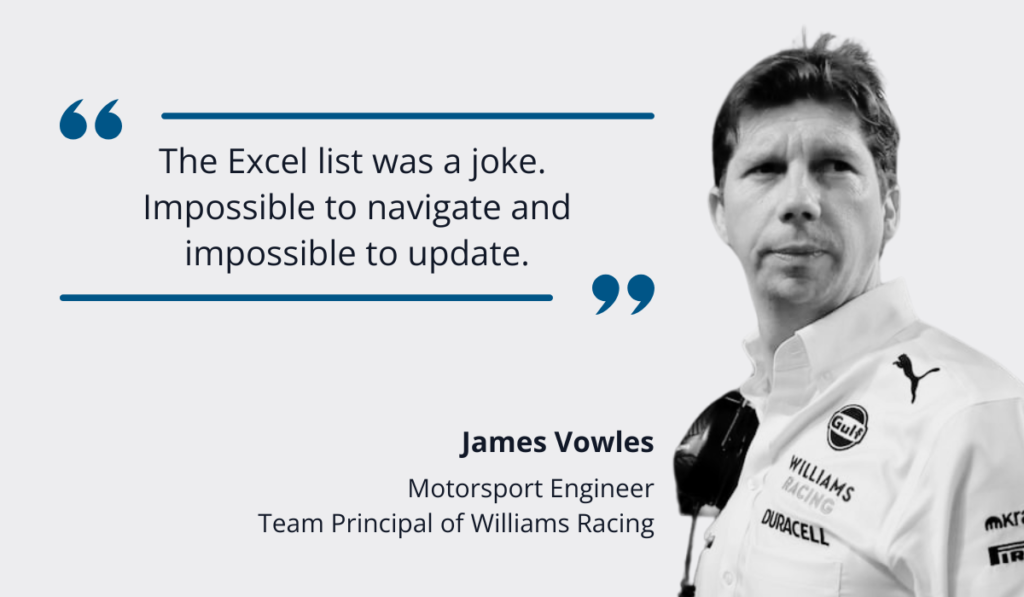
Illustration: GoCodes / Quote: The Race
Both Vowles and the F1 community reached the verdict that managing an entire car build using Excel greatly contributed to Williams Racing lagging behind its rivals.
So if the spreadsheets are out, what’s the alternative for managing inventory?
The next few sections will give you some definitive answers!
Opt for On-the-Go Inventory Management
On-the-go solutions transform inventory management by enabling real-time tracking and updates from anywhere.
Simply put, mobile-friendly inventory tracking systems or apps ensure instant insights into data from multiple locations, thereby boosting both efficiency and accuracy.
A recent survey indicates that nearly half of supply chain executives see real-time visibility as both a significant issue and a critical element of inventory management today.
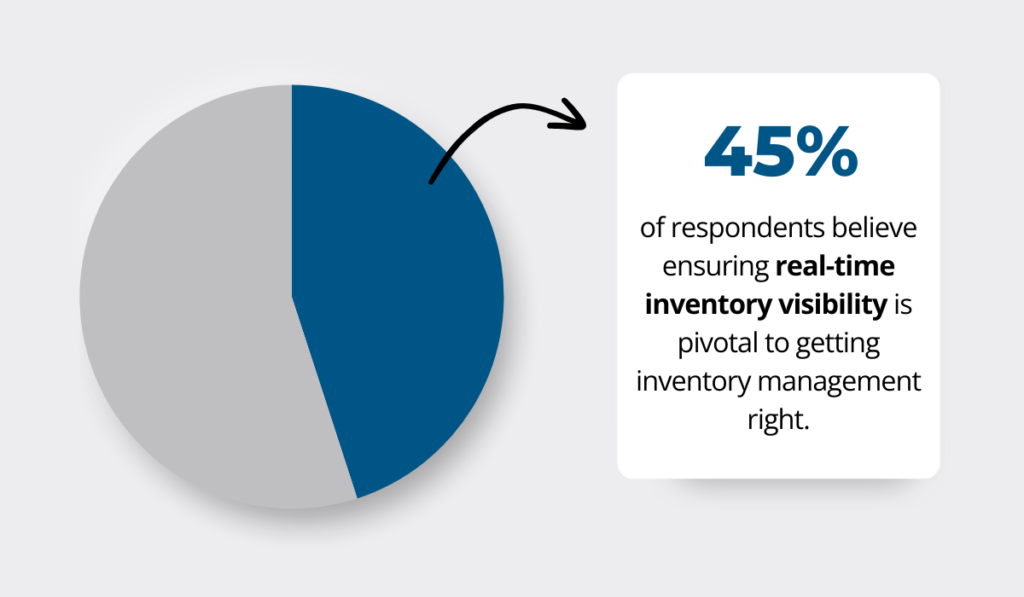
Illustration: GoCodes / Data: Standvast
Standvast’s survey focuses on e-commerce and e-tailers, but the advantages of eliminating guesswork and reducing costly mistakes appeal to various contexts.
Consider this: Mobile inventory management systems enhance visibility by giving your entire team access to a centralized record of all inventory items from virtually anywhere.
Everyone can update locations and stock levels based on the latest field data, and initiate reorder requests in just a few clicks.
For instance, if a crew is running low on essential materials like concrete or rebar, they can instantly alert the office from even the remotest jobsite, thereby avoiding expensive delays.
Of course, while inventory management tools have some universal qualities, different industries have different needs.
Inventory management tools like Zoho Inventory cater to retail by focusing on warehouse management and order processing features, as shown in the overview below.
Source: Zoho Inventory on Youtube
The mobile app makes it easy to handle stocks between multiple warehouses, track orders to ensure they’re shipped and delivered to the right destinations, and manage all invoices.
All in all, Zoho Inventory is equipped to manage large quantities of items and increase customer satisfaction.
Statistics show that on-the-go solutions are just as important in construction, with over 85% of companies prioritizing mobile-friendly construction software.
Real-time insights benefit construction project managers by giving them a more accurate picture of resource allocation while directly improving coordination and efficiency in the field.
Our comprehensive asset management tool GoCodes provides total field visibility thanks to its cloud-based software, seamless check-in/check-out system, and extensive automation and reporting features.
The user-friendly software is tailored for the construction industry, putting location, quantity, and usage data on all inventory items right at your fingertips.
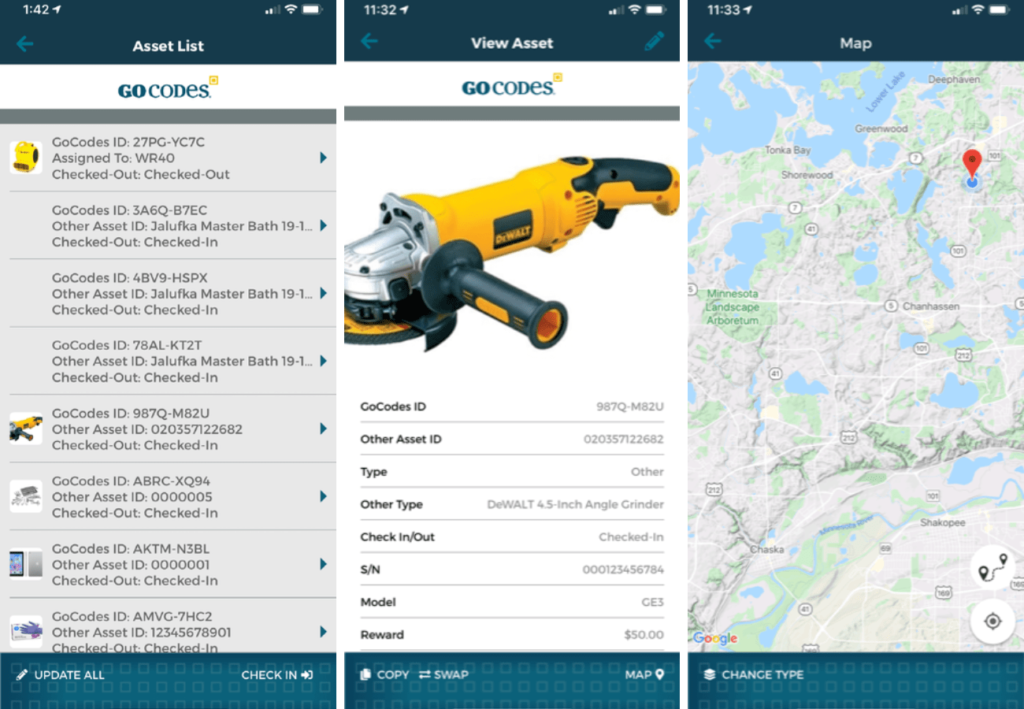
Source: GoCodes
Using tools like GoCodes for on-the-go inventory management ensures each asset and building component are right where they need to be, enhancing overall efficiency.
Get to Know Different Inventory Tagging Methods
Businesses looking for an efficiency boost need to become familiar with different inventory tagging methods.
The concept is simple:
Physical tags or labels are assigned to each item to enable quick and precise inventory tracking.
Tagging streamlines inventory management across different industries, which is one of the reasons why the global inventory tag market is expected to reach $8.49 billion by 2032.
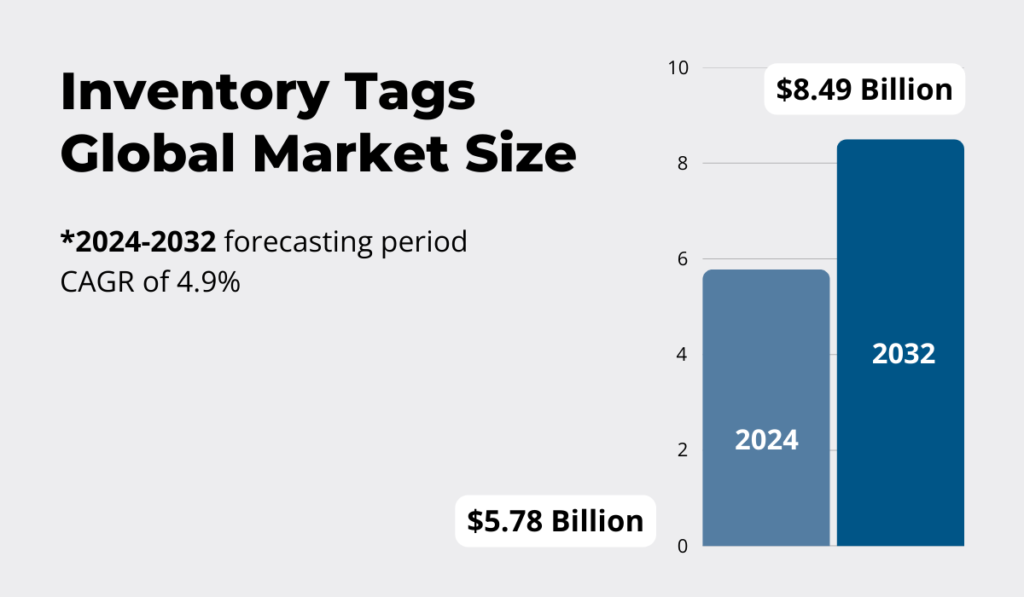
Illustration: GoCodes / Data: Fortune Business Insights
So, why are these methods so popular?
One part of it is simplicity and convenience.
Tags are a staple of reliable check-in/check-out systems—the only thing workers on-site need to do is scan the tag using either a smartphone or a handheld device.
Even if you have dozens of identical items, you can easily pinpoint the exact one you need at the moment by checking each tag’s unique identifier.
Accountability is the second part of the equation.
The most widely used tagging methods operate on the same principle of scanning unique identifiers to track and manage items.
The difference between RFID labels, barcodes, and QR codes lies in the technology used to capture data.
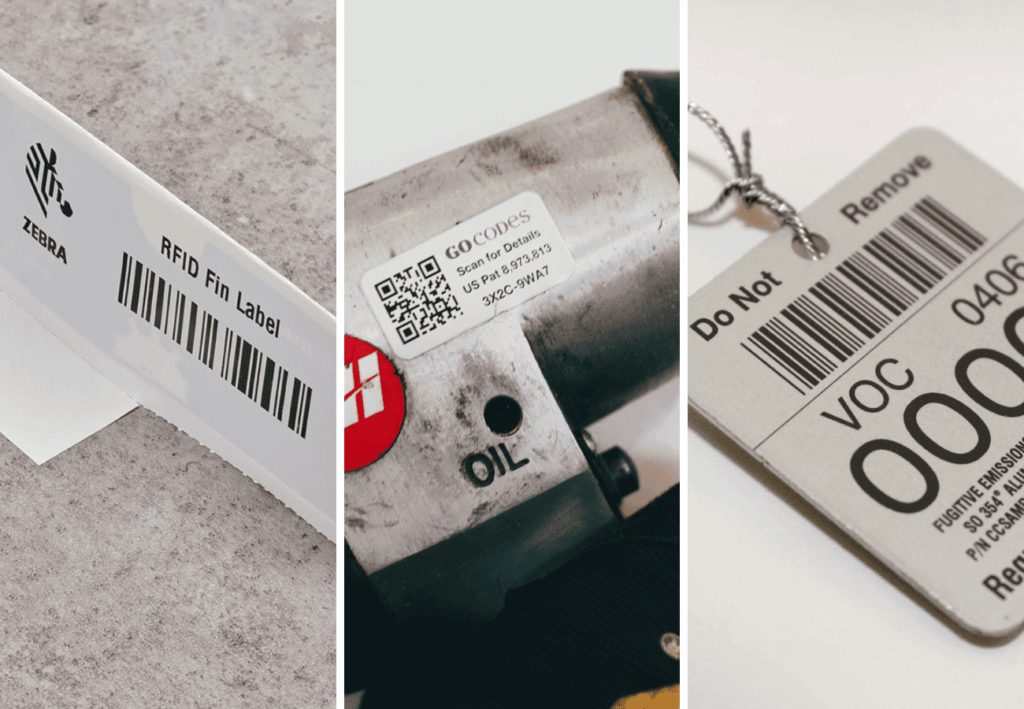
Source: GoCodes
Technology determines how successfully these solutions can be applied in different industries, and it’s also your key criteria for choosing the best fit for your business.
For instance, RFID technology enables bulk scanning even without a direct line of sight, which makes it highly suitable in large warehouses and among retailers.
One recent success story is Zebra’s RFID-enabled retail solution which helped Gramedia bookstore reduce inventory checking time by 50% and accelerate self-checkout for customers.
There are just two downsides to RFID:
- It’s often unreliable in outdoor environments.
- Its real-time tracking technology is expensive to implement.
Eric Allais, the President and CEO of PathGuide Technologies, notes that the hefty price is especially evident when comparing RFID labels with barcodes and QR codes.
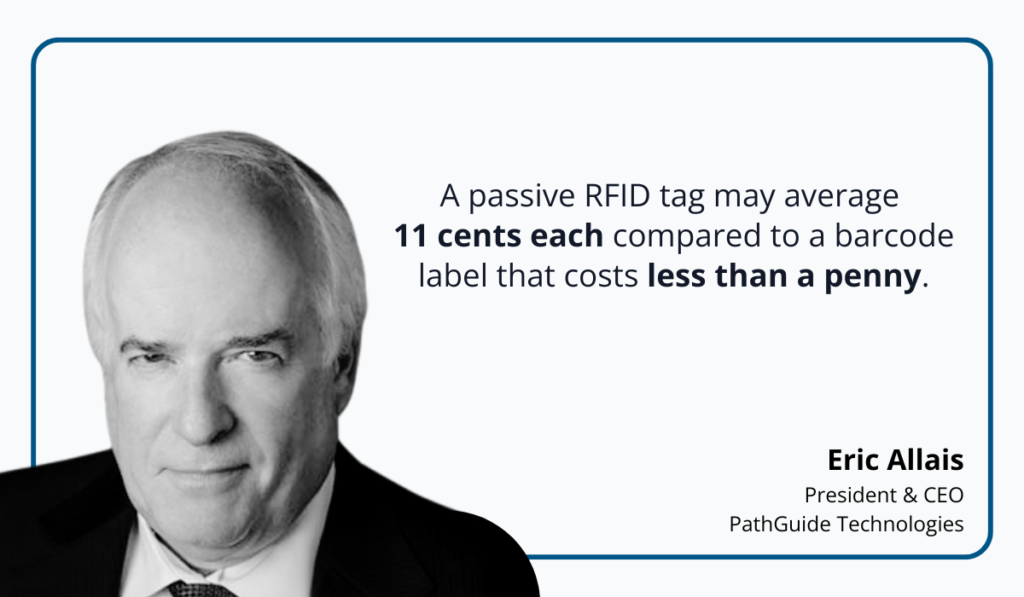
Illustration: GoCodes / Quote: Camcode
Barcodes are the most affordable tracking option of the three, suitable for a range of contexts, from retail and warehouse distribution to construction.
However, they don’t support long-range or bulk scanning and have limited data storage.
QR codes have similar scanning limitations but deliver a more advanced and cost-effective solution.
As you can see below, these tags can fit the smallest items while still supporting detailed information sharing.
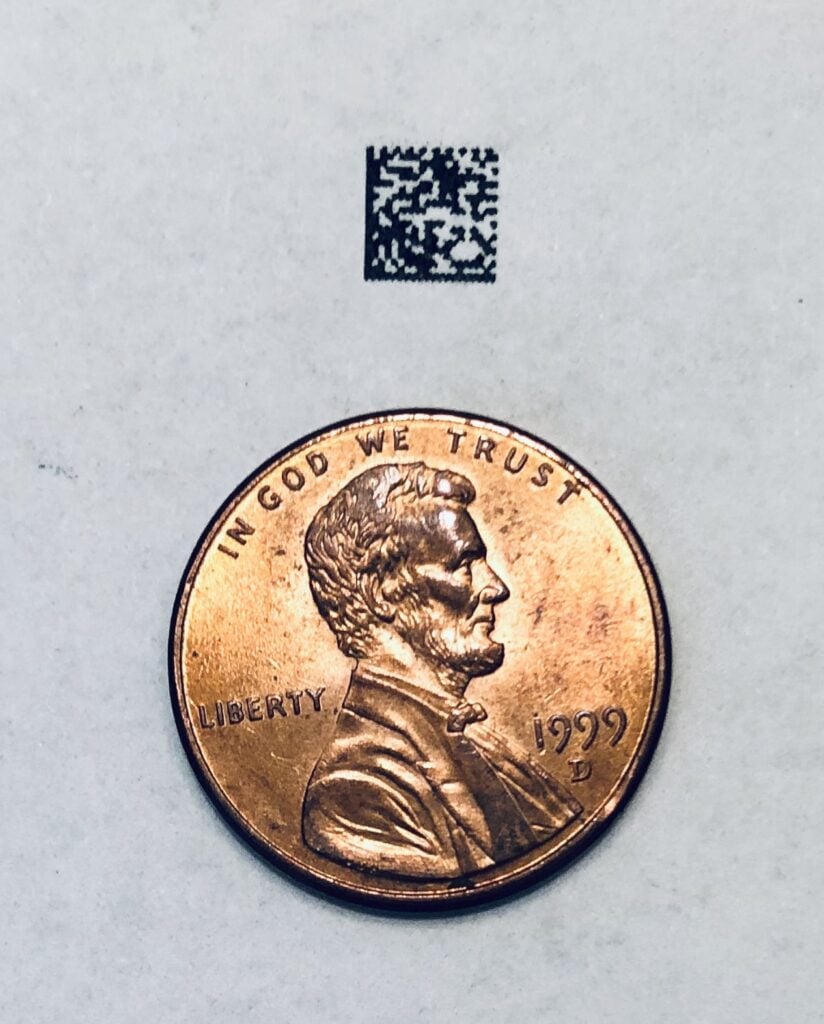
Source: GoCodes
This makes QR code tags ideal for healthcare and construction industries which demand quick access to different records, service logs, and documentation.
Ultimately, there is no ideal tagging solution, but finding the option closest to your needs will surely enhance your inventory tracking.
Optimize Inventory Layout and Storage
Keeping track of your inventory is much easier if you optimize the layout and storage system.
With mobile inventory management and an effective tagging system already in place, the next step is to adopt an effective layout.
Doing so will maximize storage space while minimizing retrieval time.
The system you opt for depends on your inventory process and industry, but there are some universal best practices for ensuring proper stock levels and efficient allocation.
Every storage space includes a variety of specialized areas, such as pallet storage zones and areas for incoming and outgoing materials.
Here is one general example of a warehouse layout designed with efficiency and precision in mind.
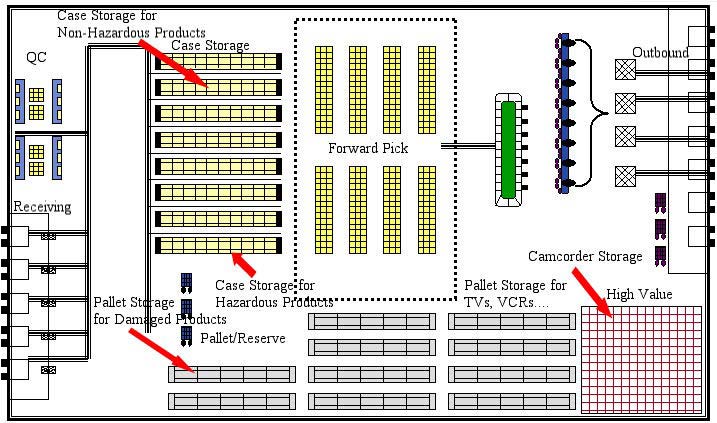
Source: SIPMM
It’s a common practice to group items by frequency of use, keeping in mind whether they are perishable or hazardous, and create dedicated spaces for high-value and high-turnover items.
When it comes to construction, maximizing storage efficiency requires combining floor-level pallet locations and stackable bins with appropriate racking and shelving units.
For instance, the cantilever racking in the image below is ideal for storing long and heavy construction materials, such as lumber, pipes, and steel beams.
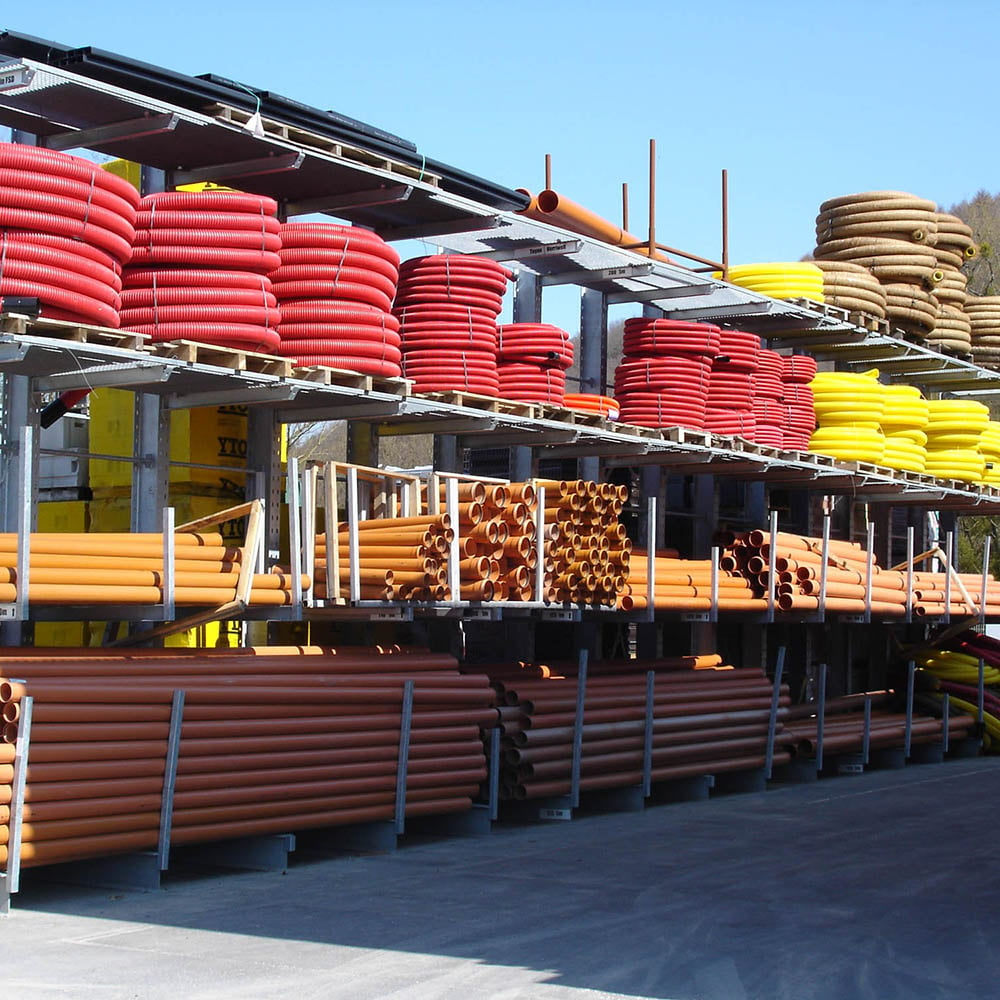
Source: OHRA
This type of racking allows easy access, reducing handling time, and can be used both indoors and outdoors.
Moreover, the detachable cantilever arms help minimize damage to both the racking and stored materials, even in the event of accidental impact.
Efficiency isn’t just about proper planning and organization—it also means ensuring safe on-site material handling.
That’s why any warehouse layout should incorporate stable shelving systems along with relevant safety regulations.
Preventing accidents and maintaining smooth operations requires regular assessments of on-site conditions and staying up to speed with current regulations.
Logistics Executive, Shankar Katla, agrees.
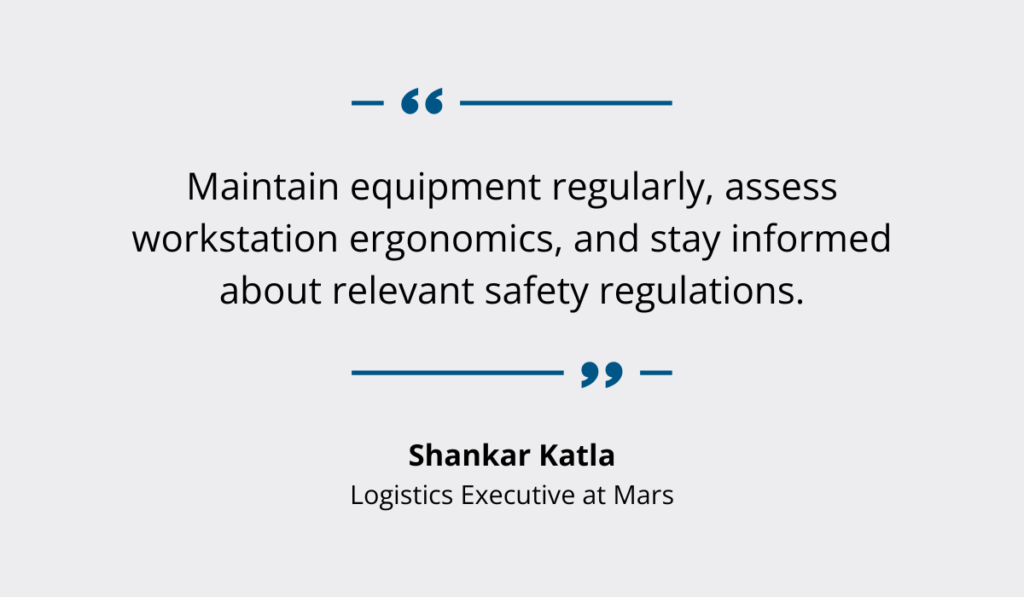
Illustration: GoCodes / Quote: LinkedIn
In the end, even the most advanced technology and automation won’t matter if you have disorganized or unsafe inventory storage.
So, design your inventory layout with care, and you’ll be one step closer to improving the overall efficiency and accuracy of your operations.
Integrate Inventory Tracking with Other Business Systems
Real-time inventory tracking won’t guarantee efficiency unless it’s integrated with your other business systems.
Companies that strive toward operational efficiency use dedicated systems for various parts of their operations, from inventory tracking and accounting to project management.
But, when these solutions aren’t compatible with one another, you miss opportunities for improvement and actively harm overall productivity.
Yooz’s 2023 research on workplace technology reveals several ways in which poorly introduced tech impacts workers’ output.
The negative effects of incompatible systems and limited integration options were highlighted by 19% of respondents.
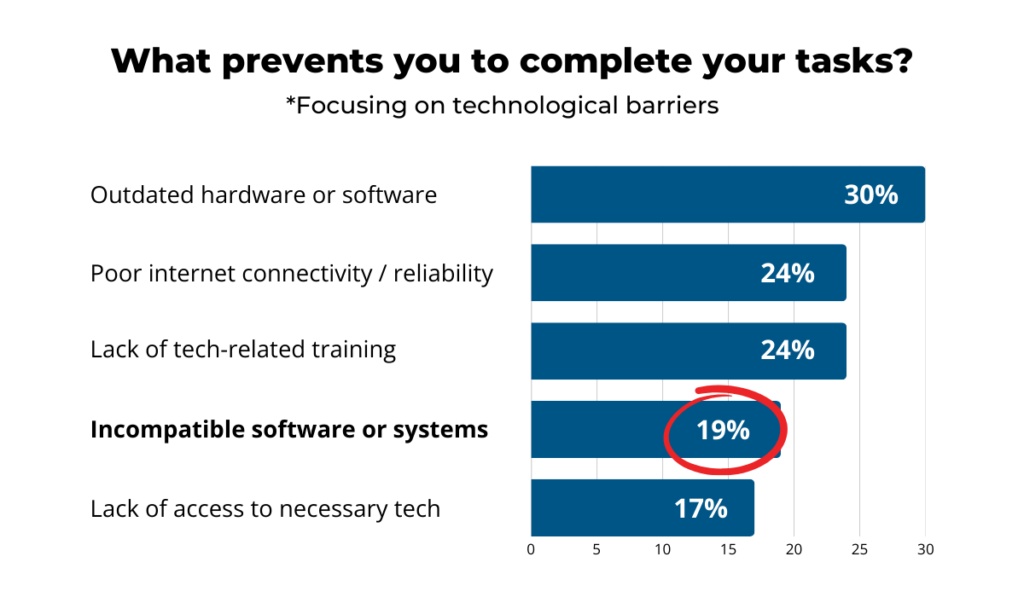
Illustration: GoCodes / Data: Yooz
Inventory management is complex, and smooth data flow between systems is essential for:
- Accurate financial reporting
- Process automation
- Better adaptability
That’s why companies prioritize integrations with these key systems:
Enterprise Resource Planning (ERP) | Improves budgeting, resource management, and overall decision-making. |
Accounting Software | Ensures inventory costs align with financial records, streamlining financial reporting and tax compliance. |
Procurement System | Automates stock replenishment to prevent over or understocking. |
Project Management Software | Aligns inventory usage with ongoing projects for smoother execution. |
As you can see, inventory management software that helps you bring together ERP, accounting, procurement, and project management under one umbrella is invaluable.
That’s why seamless integrations should be among your key criteria for choosing the right solution.
Leverage Automated Alerts and Notifications
Keeping track of inventory is much easier when you don’t have to constantly monitor stock levels yourself.
Automated alerts and notifications help businesses stay ahead by providing real-time updates on inventory levels.
These features ensure that teams can take proactive action before stock runs too low, preventing unnecessary shortages and disruptions.
It’s no surprise that low-stock alerts are a top priority for many businesses—one Reddit user discussing inventory management software even listed it as one of their biggest concerns.
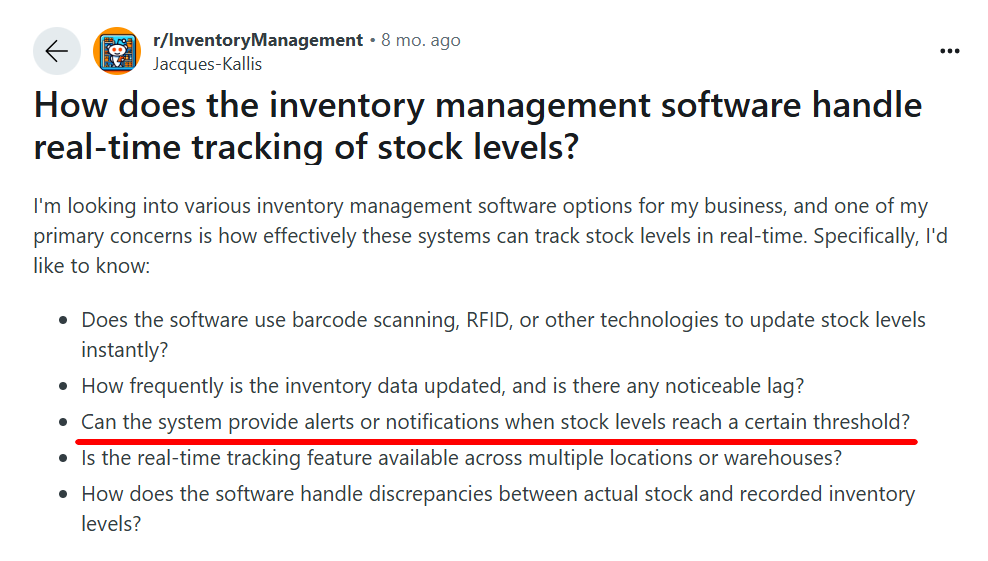
Source: Reddit
There’s more to automated alerts than simple operational benefits.
Prompt notifications instantly raise awareness of potential issues, helping you address them before they can do any serious damage.
Having this fail-safe in place is essential in industries like construction, where a slight delay or a sudden materials shortage can severely impact project timelines and create mounting costs.
Before enabling automated alerts, it’s important to set appropriate thresholds.
You don’t want to receive an alert at the last possible moment, so you need to consider what’s the optimal threshold for each of the inventory items.
Business development expert and a founder of a food and beverage startup, Sonali Saraogi Singh, points out several factors to keep in mind when making the configurations.
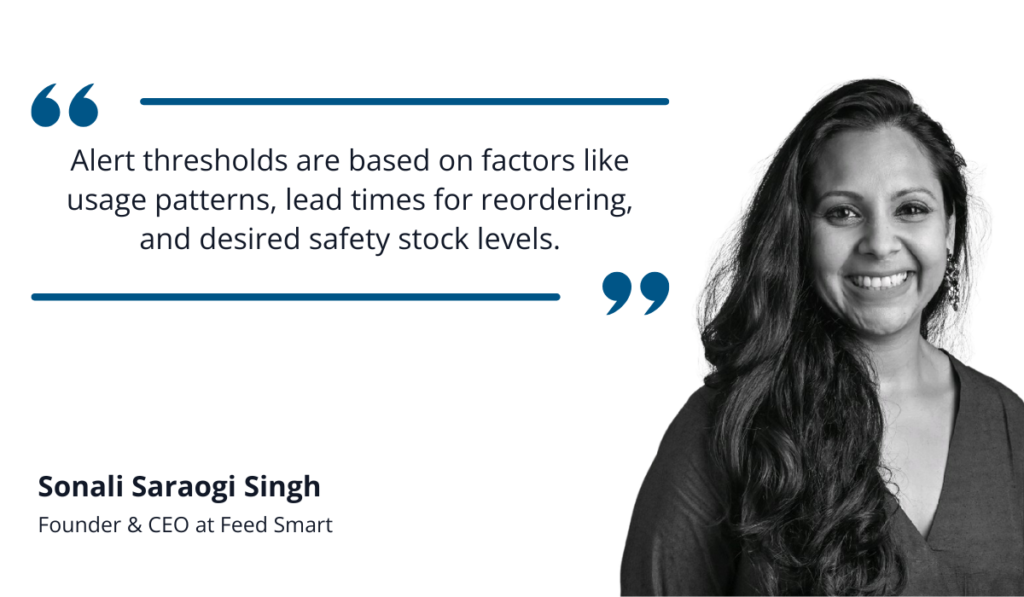
Illustration: GoCodes / Quote: LinkedIn
Once you’ve established the right thresholds, configuring alerts is a straightforward process.
Notifications are usually an optional inventory management feature.
Platforms that prioritize ease of use—such as GoCodes—make setup simple and intuitive.

Source: GoCodes
Once alerts are enabled, additional customization options become available, allowing businesses to fine-tune settings to their needs.
Turning on automated alerts is a small but impactful step.
You get to keep inventory on track and avoid costly shortages with minimal effort.
Conclusion
Mastering inventory tracking may not seem like a top priority, but ignoring it will cost you time, money, and efficiency.
Each of these six tips brings you closer to eliminating errors, preventing shortages, and keeping your projects on track.
But in the end, the key to successful inventory management lies in modern solutions.
These systems make it easier than ever to stay in control.
Now is the time to explore your options, match features to your business needs, and start implementing.
Your business and your bottom line will thank you for it.