Heavy equipment maintenance and repair is a must to keep your business moving.
When equipment is down, clients are frustrated, projects lay idle, and profits are lost. Since operators must find a way to repair heavy equipment on-site—it’s not easy to roll a bulldozer down the highway to a mechanic’s shop—it’s best to have a plan in place for maintaining these assets within your own company.
The need for heavy equipment maintenance affects several industries:
- Construction
- Real estate
- Urban planning
- Food production
- Landscaping
In this post, we will explore the details of what heavy equipment maintenance involves. We will also provide you with a few suggestions on how to avoid costly repairs, and share best practices for implementing these in your organization.
In this article...
What Is Heavy Equipment Maintenance?
Heavy equipment maintenance is the process of regular inspection, cleaning, and repair of various heavy machinery parts, including hydraulics, engines, and moving parts.
The maintenance of heavy equipment is either preventative or reactive. Preventative maintenance involves regularly scheduled care of the equipment and can include oil changes, tire pressure checks, and regular cleaning.
Reactive maintenance, on the other hand, takes place when a machine fails or is not operating efficiently. It might involve much more downtime than preventative maintenance and cost more as technicians diagnose the equipment’s weaknesses.
Preventative maintenance tends to lessen the chance of reactive maintenance.
Taking the time and occasional expense to keep equipment in good shape ensures that it will work properly when necessary.
Well-maintained machines also tend to last longer than those that are not. Besides that, heavy equipment maintenance brings additional benefits to the business. Let’s see which ones.
Why Is Heavy Equipment Maintenance Important?
Proper maintenance of heavy equipment positively impacts each part of a business.
Reactive heavy equipment repair is expensive in itself, and the downtime it forces often results in reduced profits. A single asset that remains unusable for a significant period can easily create a disastrous domino effect, which includes tension with clients, delays in project completion, and reduced returns.
The chances of this occurring lessen when you invest in preventive and routine maintenance.
This might include keeping a daily record of:
- Gages
- Odometers
- Operating hours
- Minor equipment updates such as filter changes
A recent article from the University of Nebraska notes that by following a faithful schedule of preventative maintenance, owners can cut reactive repair bills by up to 25 percent.
Journaling these routine maintenance appointments with asset tracking software is accurate, efficient, and motivating.
Doing so also builds an invaluable history of the machine, which is useful in ensuring it performs at its peak.
Identifying potential problems before they suddenly appear during the workday is another benefit of regular maintenance and inspections. By instructing staff to check the oil level consistently, fuel amounts, battery performance, and tire/track conditions, you shape a culture of appreciation for company equipment and can solve small problems before they become big ones.
Besides, caring for your equipment shows that you care for your employees.
Sites on which heavy equipment is at work are inherently dangerous. Ensuring that these large and powerful machines are in good working order can help with risk management and safety objectives.
Also, consider the logistical and schedule-related nightmares associated with the replacing or filling in for a broken asset. If the heavy machinery requires an outright replacement, you need time to source an appropriate substitute.
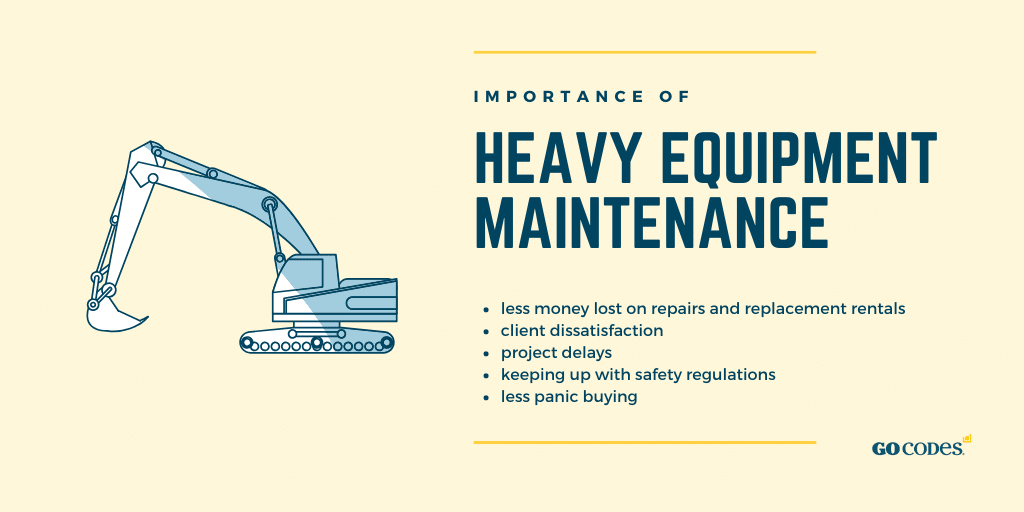
The significant cost associated with purchasing heavy machinery means that companies must avoid panic buying. Replacing a broken machine part might also require time for delivery and assembly. Also, finding financing, producing cash for the outlay, or freeing monetary assets can wreak havoc with project and company budgets.
If a temporary replacement is in order while your equipment is repaired, you may face the same frustrating delays and potential inability to find an appropriate piece of machinery, not to mention the financial burden of paying rental fees on top of repair costs.
It’s better to invest in your heavy machinery little by little with properly spaced, high-quality preventative maintenance. Caring for these assets includes not only following minimum service schedules but also taking time to communicate with staff about machine capabilities and limitations.
And as simple as it sounds, “use only as directed” applies a great deal to heavy machinery; using equipment only for its intended purpose will avoid unusual stress on its engine and parts.
Six Tips for Heavy Equipment Maintenance
Just as you maintain your car, your home, and your body, your heavy equipment requires constant attention and care.
Here are six ways to organize the maintenance of your heavy assets so that tending to them becomes a regular and effective part of your workday.
1. Develop a Maintenance Routine
During routine maintenance, you should be checking on oil amounts, verifying fluid levels, and surveilling for small cracks or chips. Your equipment manufacturer should provide information about how often this should take place.
However, you should immediately attend to minor on-the-job events such as low fuel levels and leaking tires.
Avoiding this can lead to significant damage the longer the equipment is forced to compensate for the faulty part.
Also, knowledge is power when it comes to your machinery. Regular and preventative maintenance provides a running source of crucial data about how your heavy machinery is operating, and which practices are serving it best. Routine, preventive maintenance can minimize downtime and maximize efficiency.
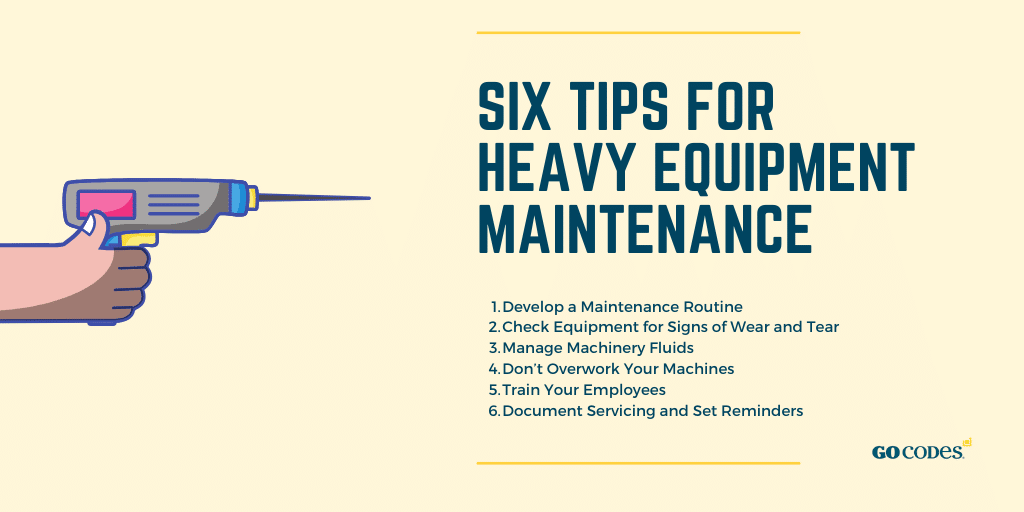
Not only is it cheaper in the long run to develop a maintenance routine, but it’s also safer. In addition to manufacturer recommendations, local, state, or federal regulations might apply to how often and in what ways your equipment is checked.
This is often due to recommendations from the Occupational Safety and Health Administration (OSHA), which states that maintenance operations are responsible for 20 percent of industrial accidents. What is worse, 15% of these accidents are fatalities.
Ensuring that your equipment is in good working order helps to avoid this.
Cleaning your heavy equipment is also an essential aspect of a maintenance routine. Sites, where heavy machinery is used, are typically covered in dirt, dust, and debris.
While cleaning your heavy equipment, pay special attention to:
- using a sturdy hose to clear out soot and dirt
- having gear on hand to clear out grease, animal debris, or hazardous materials
- wiping filters, vents, gaskets, and fans
- checking on specialized areas like brass bearings or parts made of iron, which might require pressure washing, acid treatments, or steaming
2. Check Equipment for Signs of Wear and Tear
Looking for evidence of regular minor damage to your heavy machinery and repairing it immediately helps to ward off major repairs, and keeps your asset operating at its best every day.
Doing so even extends the service life of the asset.
Monitor your heavy equipment for the following:
- Sputtering electronics
- Water damage
- Chips in metal
- Fatigued engine components (alternators, starters, gears)
- Fraying or cracks in belts or hoses
- Wires falling out of good repair
- Cracks from bearing loads and vibrational damage
- Contamination in belts, gauges, and circuits
Sometimes the signs that your heavy machinery requires minor repairs or a check-up aren’t visible with a simple walkaround or glance at the gauges. For example, your heavy equipment might show evidence of a problem via its exhaust. If it’s usually white or grey, a sudden change to black or shift in odor is a danger sign.
Another early indicator of a potential repair issue is low fluid levels. While this might be normal for some functions of some machines, if it happens too quickly after a top-off or routine maintenance appointment, it might indicate a coolant leak or faulty valve.
Heavy machinery is noisy, but if it makes sounds which are unusual or unnaturally loud, it’s time to check its moving parts.
Grinding, clunking, or hiss sounds are early indicators of failures in the machine’s major systems. Stay alert for changes in odors or vibration levels as well.
Avoiding any of these wear and tear warning signs can quickly become expensive, time-consuming, or even deadly, so make sure you regularly check your heavy equipment for the mentioned signs of wear and tear.
3. Manage Machinery Fluids and Ensure Regular Lubrication
Effective fluid management doesn’t just include checking fuel and coolant levels. Lubrication is a vital aspect of good heavy machinery health.
Oils and hydraulic fluids are as much a part of the machine as the levers and gears.
Without them, the equipment fails to perform at its most efficient levels, but it can also increase regular wear and tear, speeding the day when the equipment either fails or is no longer cost-effective to repair.
Checking lubricant levels should be a regular part of basic and preventative maintenance. While doing so, it’s good to ensure that the lubricant isn’t showing signs of leaks from nearby seals or hoses.
When replacing lubricants, it’s always best to use the type mentioned by the manufacturer. And while low lubricant levels are harmful, more lubricant isn’t necessarily better. Too much lubricant invites grease buildup, clogs, and decreased performance.
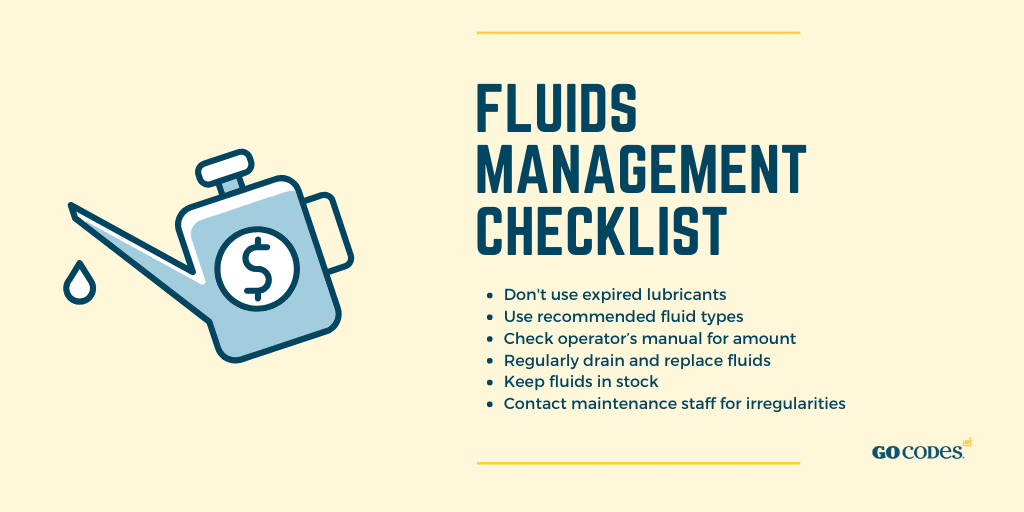
Beyond simple lubrication checks, careful fluid management can increase your heavy equipment’s performance exponentially. Analyzing the fluids within your machine can be a smart investment of time and preventative maintenance funds.
Sending samples of your machine’s liquid innards can yield a treasure trove of information about viscosity, potential sources of contamination, and amounts of pH or acid.
Regular fluid analysis can flag potential problems even earlier than common tip-offs such as odd noises or vibrations.
Best practices for working with your heavy equipment’s lubricants and fluids include:
- Avoid using expired items or those which are a mismatch for your machine
- Check with the manufacturer and operator’s manual to ensure correct fluid amounts and recommended types
- Regular draining and replacing according to intervals recommended by the manufacturer
- Keep fluids in stock, clearly labeled and in appropriate containers
- Store carefully to avoid contamination or dangerous conditions
- Rather than merely telling your staff to “check the fluids and lubricants,” identify a specific employee to do so at appropriate times
- If fluid levels change more rapidly than usual or change in appearance, viscosity, or odor, contact your maintenance staff or the manufacturer
4. Don’t Overwork Your Machines
While trying to stay on schedule or make up for lost time on a project, it’s tempting to push your staff and heavy equipment just a little harder to keep supervisors, clients, and accountants happy.
However, using machinery beyond recommended limits isn’t just dangerous and potentially out of safety regulation compliance, it can shorten the life of your equipment or contribute to a costly repair job.
Overworking machinery strains its major components, but also strains its smaller items – gears, silicone rings, and connection points.
Over time, a small weak or worn part of the equipment can trigger a more massive failure.
Performance specifications on heavy machinery can include:
- Amount of incline
- Pressure limitations
- Weight limits
- Engine capacity
- Temperature limitations
Paying attention to such guidelines as proper power modes for certain tasks is just as important as preventative maintenance. Even more importantly, ignoring the likes of temperature and pressure limitations can injure your employees.
It’s more costly to gamble with overworking your fleet and employees than to slow down, ease off, and stay within limits.
OSHA states that the weekly bill for workers’ compensation is nearly one billion dollars—and that doesn’t take into consideration project downtime, lawsuits, equipment replacement, or machinery repair.
5. Train Your Employees
Paying attention to preventative maintenance won’t mean much if your employees are not properly trained in how to use heavy equipment properly, or how to spot signs that the machine is out of alignment.
Proper employee training is a significant contributor to a company’s health and safety culture.
If your staff understands what constitutes safe behavior and why, they are more likely to follow guidelines. In addition, emphasizing that heavy equipment requires specific treatment will help employees to treat it as their own.
Incorrect operation can result in damage, injury, and unusually heavy wear and tear. Simply sending a new hire out on a job with the hope that he or she “will pick up one way or another” is a recipe for disaster.
Training on heavy equipment should be standardized, precise, and regularly updated.
Local and federal laws, encouraged by OSHA, might have strict details in place concerning employee training. Some might require specific certification and licensing.
By fulfilling these norms and ensuring that your staff is aware of best practices, proper cleaning techniques, and emergency procedures, you can keep your operators and heavy machinery healthy and efficient.
Effective employee training should include:
- Reminders to avoid distractions; for example, cell phone use should not be permitted while operating heavy machinery
- Communication about avoiding the use of such equipment while taking certain medications
- Protocol for security
- Checklists for starting and ending a shift
- Familiarity with routine maintenance as well as cleaning procedures
- Understanding all parts of the equipment (systems, limits controls, etc.)
- Testing
6. Document Servicing and Set Reminders for Future Repairs
Knowing what your heavy equipment needs, and when it needs it, is vital to its operation.
Installing a regular schedule and reminders for future equipment services can keep track of documentation for you, help you budget for preventative maintenance, and allow you better control over your personal and job site time tables.
Asset management software is a modern, efficient way to track heavy equipment maintenance. Some systems, like GoCodes Asset Tracking, allow on-the-go scheduling through an app, eliminating wasteful paperwork that can easily go astray on a construction site.
Documenting service via software allows employees across the company to access this information at any time. The data is far more securely preserved than on a whiteboard or in physical logbooks.
Details within your digital log should include:
- Which machine was serviced
- Date and time of work
- An employee involved in servicing
- Parts replaced, including technical specifications
- Notation of irregularities
- Date of next preventive maintenance
Over time, this information keeping creates a detailed history of your equipment, which is useful should you decide to sell it or need to make a warranty claim.
Documenting regular maintenance and servicing can also assure regulators that you are maintaining compliance and that you can provide maintenance workers with the information they might require to begin a major repair.
Make Heavy Equipment Maintenance a Habit
Properly maintaining heavy equipment is key to running a robust and nimble company. Understanding the full scope of heavy equipment maintenance helps to avoid downtime, slipping schedules, and costly repairs.
By taking advantage of new technology to keep yourself informed on the status of your fleet, you can save money and time while maintaining regulatory compliance and employee safety.
From upholding equipment cleanliness to ensuring employee training and accountability, you can’t afford not to pay attention to ongoing equipment maintenance.
GoCodes Asset Tracking Can Help
The GoCodes Asset Tracking asset management system can help you keep tabs on your heavy equipment and its maintenance.
We use QR code tags with a unique visual code that you can scan with your smartphone. When scanned, GoCodes Asset Tracking tags provide detailed information about equipment location, its last service date, serviced parts, and any scheduled maintenance—making heavy equipment management a breeze.
Sign up for a free trial here.