Key Takeaways:
- Fleet professionals waste an average of three days per week on administrative tasks.
- Fleet management software can collect real-time vehicle health information.
- Geofencing minimizes the time spent on routine, time-consuming activities.
Managing a fleet is no easy task.
There is so much coordination, oversight, and planning involved, which often places a heavy burden on fleet operators and managers.
But what if there were a way to lighten the load and allow more time for high-level strategic activities?
Fleet management software can do just that.
It automates repetitive, time-consuming tasks and streamlines workflows, helping you ensure operations run more efficiently and preventing staff from becoming overwhelmed.
Let’s explore exactly how.
In this article...
Automating Data Collection
Unlike traditional fleet management, which relies on manual entry for fuel logs, mileage, and other key data, fleet management software automates these data-gathering processes.
How?
By integrating with vehicle telematics.
Telematics devices connect to a vehicle’s OBD-II port or CAN bus (Controller Area Network) system, providing real-time access to internal sensors and diagnostic systems.
From there, data points such as fuel levels, odometer readings, and speed are continuously transmitted from the vehicle to a centralized dashboard, like the one you see below.
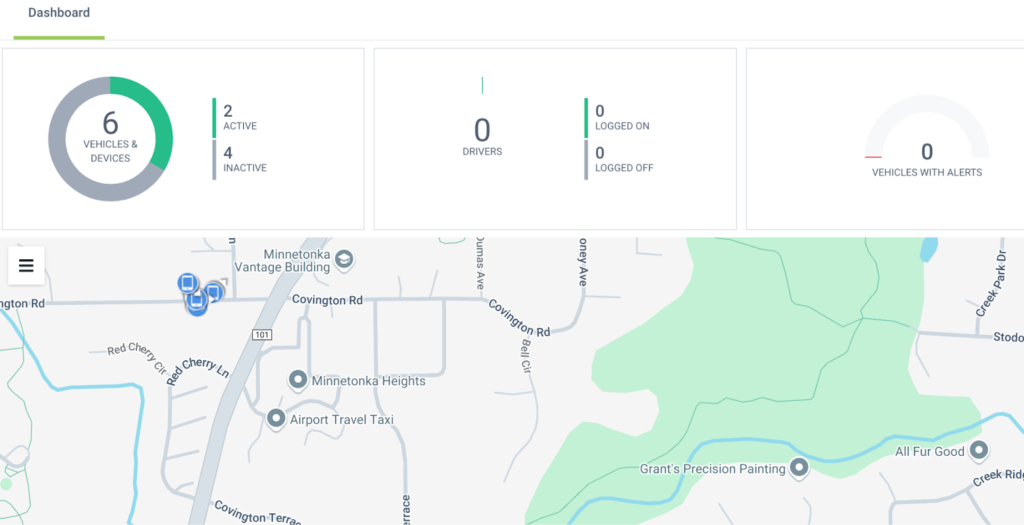
Source: GoCodes Asset Tracking
This results in faster, error-free data collection that saves time and forms a reliable foundation for well-informed decision-making.
A report from Motive shows just how necessary this kind of automation is.
As it turns out, fleet managers estimate employees waste an average of five hours per day on repetitive administrative tasks—amounting to three full days in a standard workweek.
However, this inefficiency is understandable given that 60% of them still rely on spreadsheets, and 52% use paper documents to manage their fleets.

Illustration: GoCodes Asset Tracking / Data: Motive
These outdated methods make it really challenging to track the vital information needed for effective fleet management.
After all, fleet operations are inherently complex, generating vast amounts of data.
Derek Grover, Senior VP of Technology & Operations at Jim Pattison Lease, a recognized leader in the fleet leasing industry, puts things into perspective:
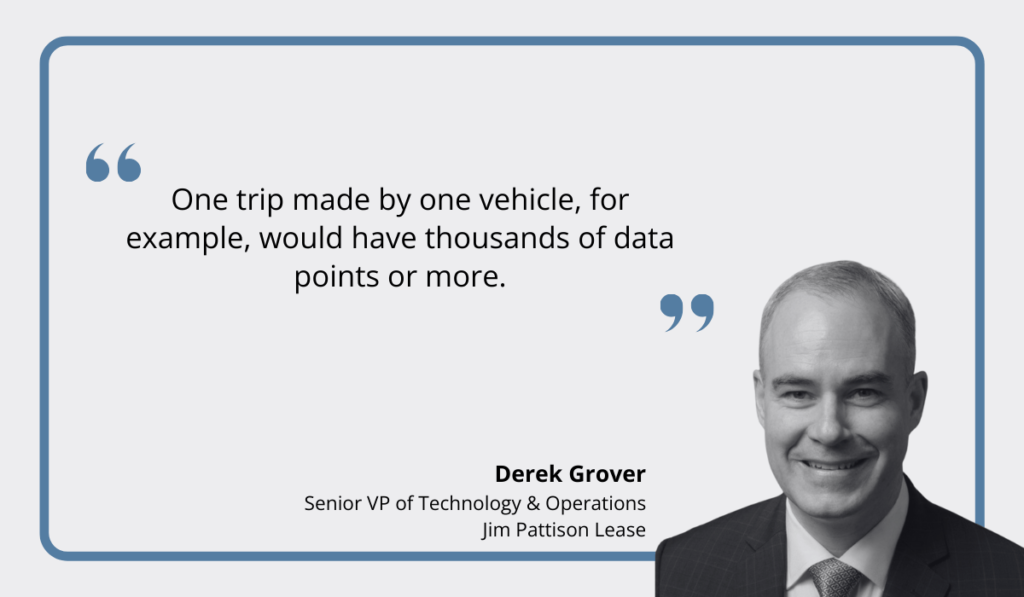
Illustration: GoCodes Asset Tracking / Quote: Autosphere
Think about it.
Manually logging fuel purchases, signs of wear and tear, and route deviations places an unreasonable burden on drivers and only increases the risk of errors.
This is where fleet management software comes in, compiling all relevant information seamlessly and accurately, leading to more efficient operations.
Just take fuel consumption management as an example.
Instead of manually logging receipts and mileage, the software can automatically track fuel usage per trip or per mile, providing a clearer view of consumption patterns.
And fuel management is only one piece of the puzzle.
With automated data collection spanning every aspect of fleet operations, the potential for improved efficiency, reduced costs, and better decision-making is too significant to ignore.
Performing Vehicle Diagnostics
Among the many types of data fleet management software can collect, real-time vehicle health information is one of the biggest game-changers.
This kind of data eliminates delays associated with physical inspections or driver-reported issues, in turn streamlining maintenance scheduling and planning.
How does it work?
It’s simple: telematics continuously monitors asset health and the software alerts you as soon as a potential issue is detected.
According to Patrick Brown, Director of Strategy at an American truck manufacturing company, Mack Trucks, things were much less efficient before such technology.
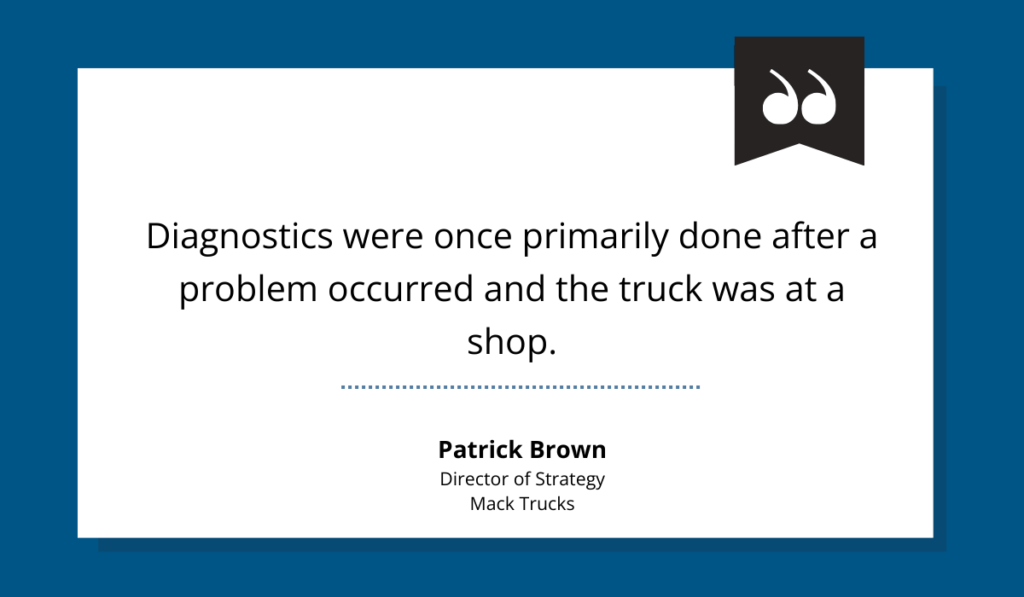
Illustration: GoCodes Asset Tracking / Quote: Fleet Owner
In other words, there was limited information about when and how an issue arose, what the asset was doing at the time, and other contextual factors.
This mostly led to reactive maintenance and slower diagnoses.
Today, that’s no longer the case, with remote monitoring and fleet management software working hand-in-hand to catch problems early and deliver precise diagnoses in moments.
This accelerates repair facility intake processes, minimizes disruptions, and improves overall operational efficiency.
Plus, proactive fleet upkeep significantly reduces the risk of future failures or repairs, even further reducing the admin workload down the line.
In fact, research shows that businesses using preventive and predictive maintenance experience almost 80% fewer equipment defects.
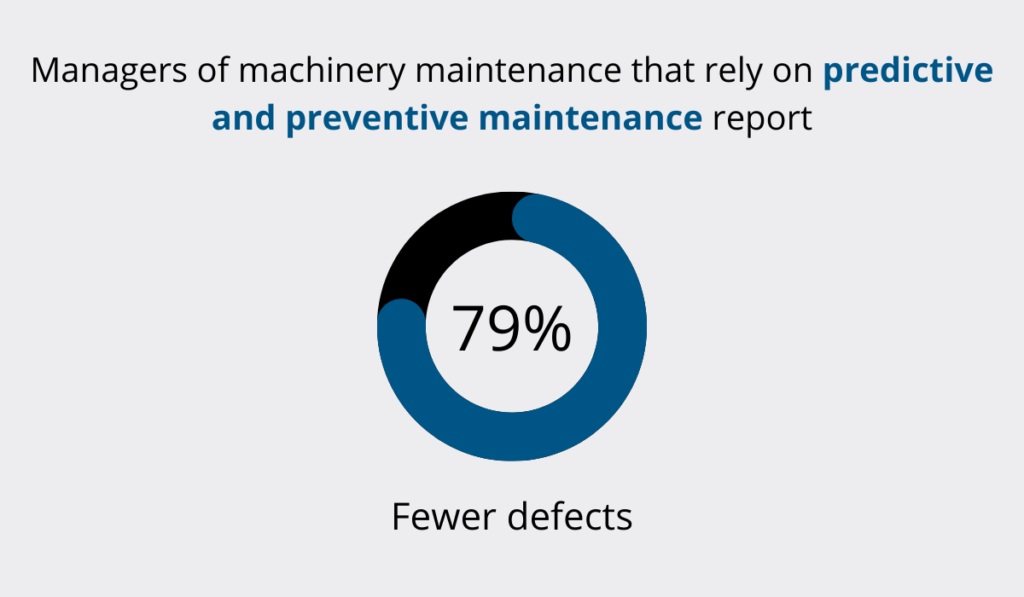
Illustration: GoCodes Asset Tracking / Data: NCBI
At Sargent Corporation, a U.S.-based earthwork construction company, they know this very well.
Thanks to the combination of telematics and fleet management software, they were able to considerably improve their workflows and boost efficiency.
Ryan Kennedy, Field Maintenance Foreman at Sargent, offers us a glimpse into their process.
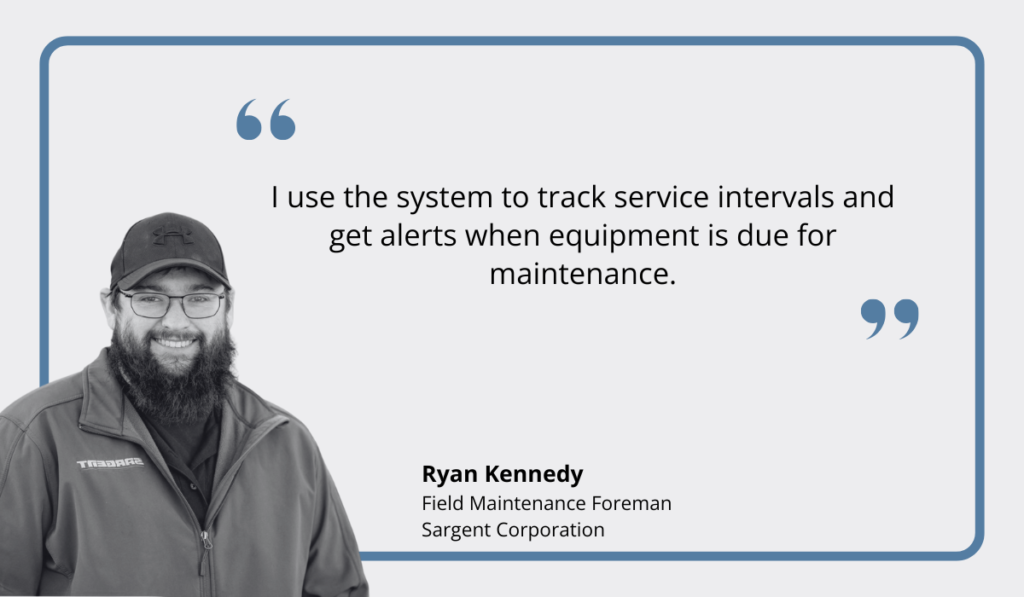
Illustration: GoCodes Asset Tracking / Quote: Construction Equipment
Each week, Kennedy prints a list of machines due for servicing, based on real-time data and location.
He then groups equipment to create an efficient schedule for technicians, aiming to reduce downtime while maximizing the number of machines serviced in the shortest possible time.
This approach increases job transparency and simplifies processes while ensuring that every asset receives timely and proper care.
It’s a clear win-win.
Simplifying Data Analysis
In addition to collecting data, fleet management software also generates detailed reports on fleet and driver performance.
This saves time and effort by empowering fleet operators to cut through the noise of overwhelming data streams and uncover actionable insights that truly matter.
Yes, rich fleet data is great—but only if it leads to smarter decisions. Otherwise, it’s just a sea of useless information.
Bob Cavalli, consultant and fleet subject matter expert at Jackson Dawson, a company specializing in marketing, summarizes the issue perfectly:
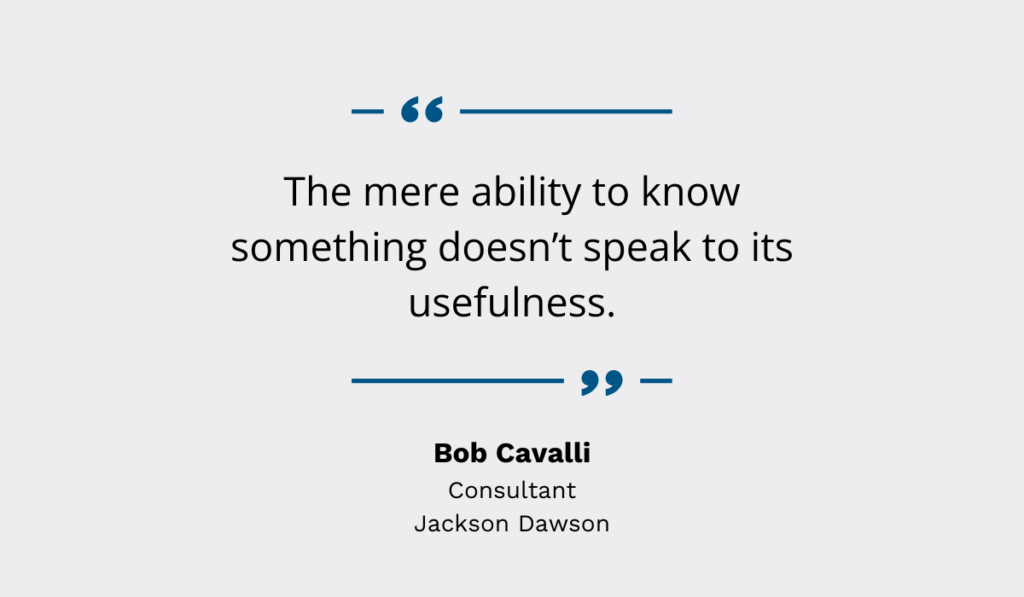
Illustration: GoCodes Asset Tracking / Quote: Automotive Fleet
But how should fleet managers filter interesting but useless information from that which actually helps improve operations?
The answer lies in fleet management software’s robust reporting features.
These tools digest an avalanche of collected data and present either detailed reports or concise summaries—whichever is needed—within seconds.
Sasha Arasteh, E-Mobility and Services Manager for Shell Fleet Solutions America, explains the importance of instant access to these reports:
“And then, using that data, coupled with the actual mapping and GPS technology that tells you where your drivers were and where all your vehicles are located, you can address other parameters, including route optimization, scheduling, and a more efficient plan of action.”
And that’s how you take your fleet to the next level without wasting time sifting through mountains of data.
Recognizing the value of strong reporting capabilities, we ensured our own asset management solution—GoCodes Asset Tracking—offers all the reports you could need.
Want to improve driver behavior and safety?
Take full advantage of our reports on harsh braking, speeding, and similar events to identify areas for improvement.
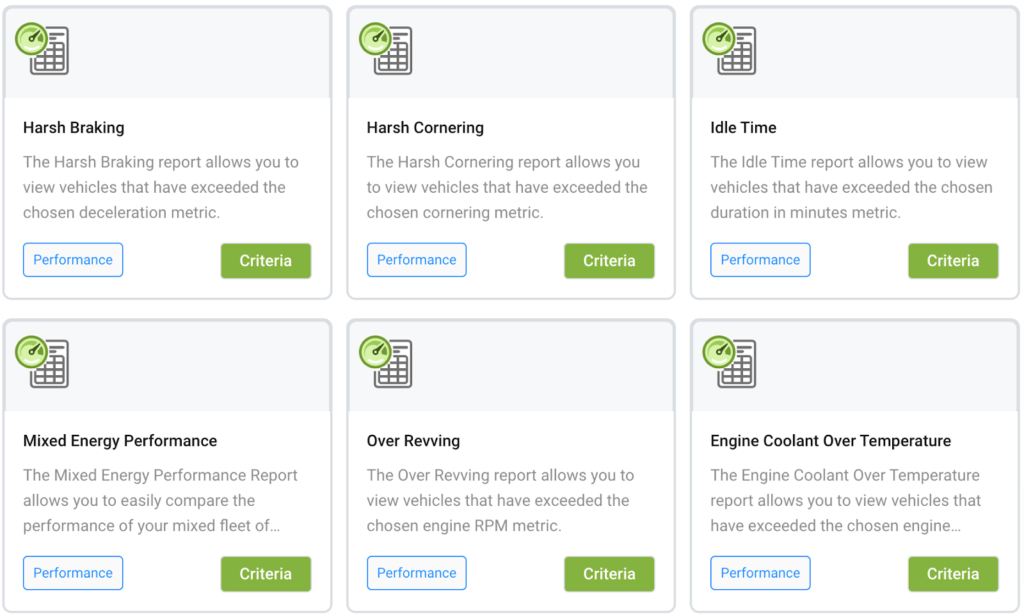
Source: GoCodes Asset Tracking
Or, if you’re looking to save money on fuel, check out our fuel consumption reports.
They will help you spot usage patterns and show you opportunities for cost savings.
The bottom line?
Gone are the days of drowning in data and slow decision-making.
Fleet management software does the hard work for you—and it does so faster, smarter, and with pinpoint accuracy—so you can steer your fleet toward success with confidence.
Centralizing Documentation for Quick Access
Fleet management software serves as a central document repository that drivers, managers, executives, and other stakeholders can access in real-time.
Below is an example of a typical asset view provided by such software.
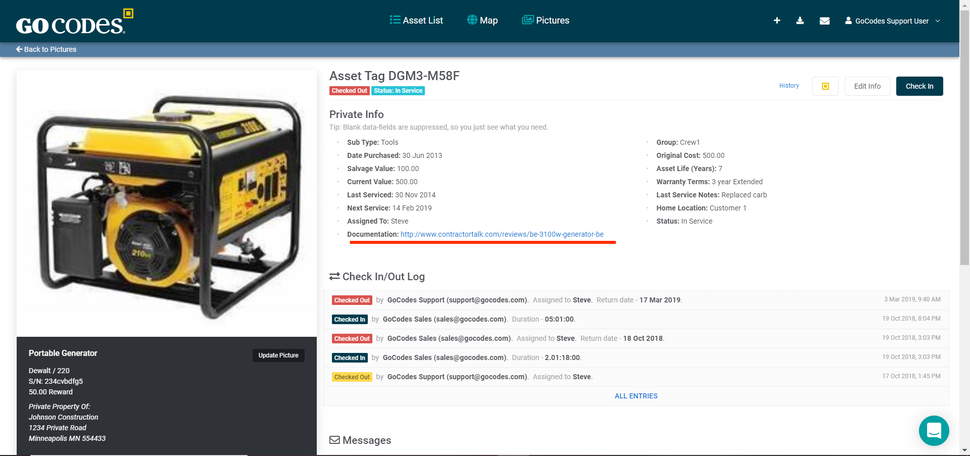
Source: GoCodes Asset Tracking
Warranty details, inspection history, operator manuals, and more—it’s all right there at your fingertips.
Having everything so easily accessible and well-organized drastically reduces the time spent tracking down and distributing crucial documents and information.
Without such a system, on the other hand, you expose your fleet to various inefficiencies.
Steve Keppler, a Co-Director at Scopelitis Transportation Consulting, a consulting business with a focus on the transportation industry, elaborates:
“Fleets that use paper-based recordkeeping tend to have more challenges recording data, maintaining records, missing important deadlines, locating proper records on request, and easily identifying compliance gaps in documents and dates.”
Essentially, when key data is scattered, you’re far more likely to waste time searching for it.
If your business relies on spreadsheets or stores documents in multiple locations, you could be losing hours every day looking for critical information.
This is especially true if various stakeholders handle different data sets.
Now imagine needing to demonstrate compliance. If vital documents aren’t readily available, the repercussions can be severe.
A J.J. Keller survey confirms the importance of easily accessible documentation in this context.
As it turns out, most fleet professionals agree that maintaining accurate and well-organized files is the most important aspect of FMCSA compliance.
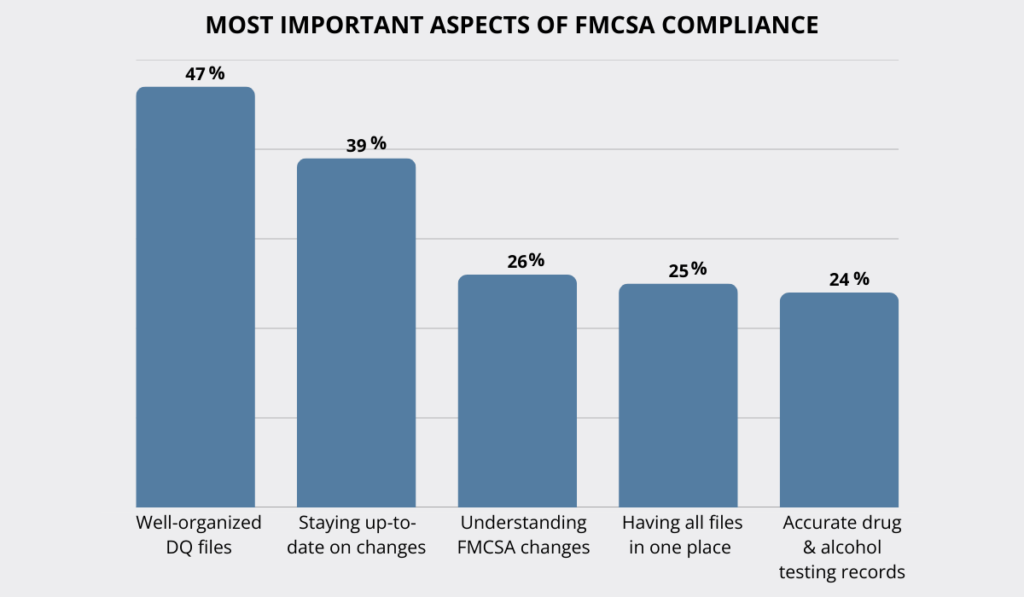
Illustration: GoCodes Asset Tracking / Data: J.J.Keller
At the end of the day, what’s the point of detailed fleet or driver data if you can’t find it when you need it?
Luckily, with fleet management software, you can get to each file anytime and anywhere in a couple of clicks, keeping your operations compliant and running smoothly.
Real-Time Area Monitoring
Thanks to the geofencing feature available in many fleet management software solutions, fleet operators can automatically monitor the areas where their fleets operate.
This reduces the need for manual tracking or phone check-ins.
But what exactly is geofencing?
Geofencing is a technology that allows users to create a virtual boundary or imaginary perimeter on a map, like the one you see below.
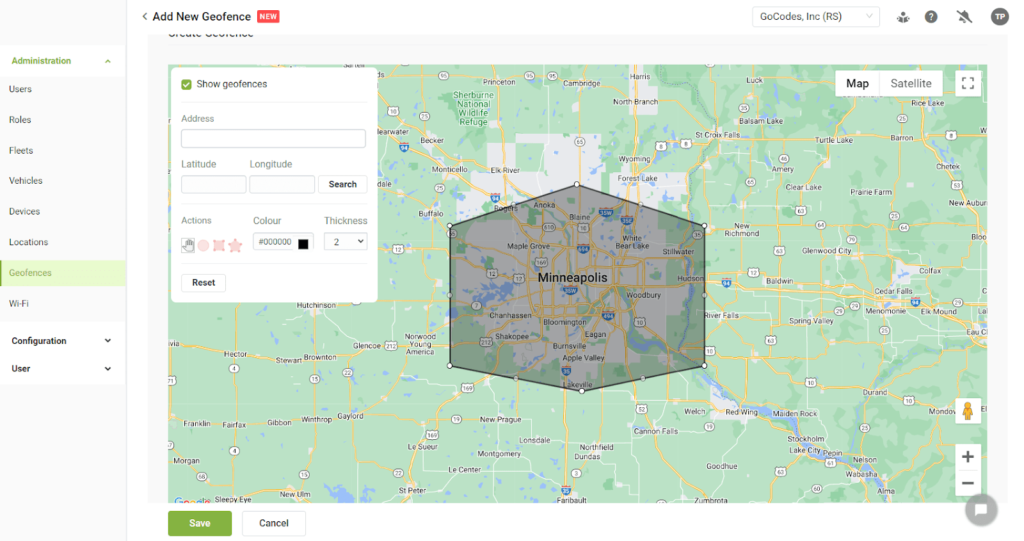
Source: GoCodes Asset Tracking
And once this boundary is established, users can set up alerts to be notified when a device enters or exits the defined area.
As such, this technology minimizes the time spent on routine activities by providing instant notifications when an asset reaches a location where a specific task is required.
Dominic Hand, VP of IT & Connected Products for Thermo King, provides a couple of practical examples of how this works:
“For example, [fleet managers] can precool all the refrigeration units in their yard each morning for on-time loading. They can see what alarms have been issued for any unit in their yard so that they can prioritize which vehicles are ready to load and which need service. They can notify customers that their deliveries are arriving or have arrived.”
One particularly innovative application of geofencing comes from fleet management solutions & automotive services provider Holman.
Kathryn Foster, Director of Strategic Services at Holman, explains:
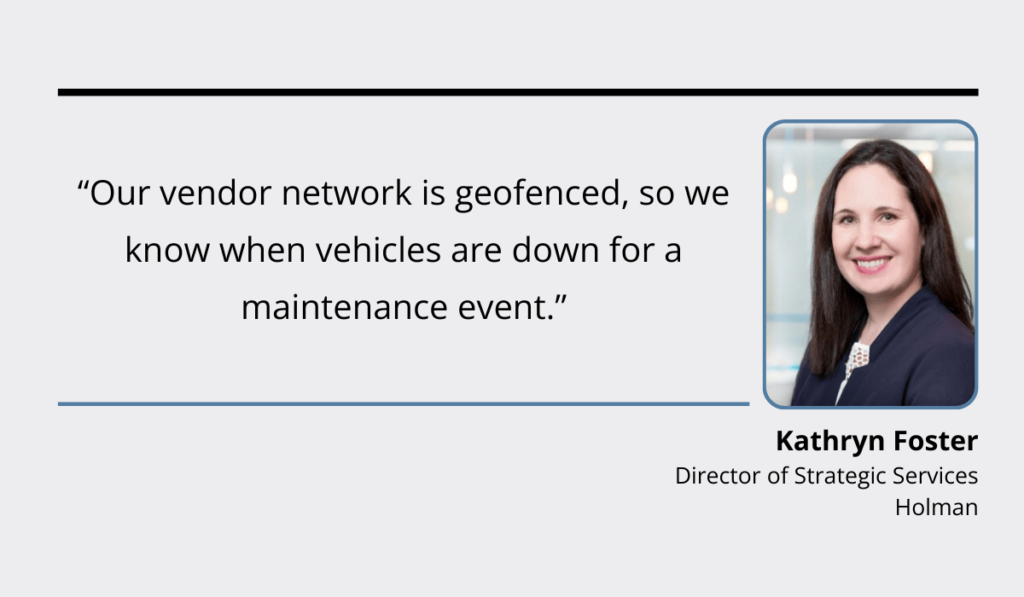
Illustration: GoCodes Asset Tracking / Quote: Autosphere
By tracking vehicles in the shop for repairs, the company can monitor how frequently specific vehicles experience issues.
If a particular vehicle requires maintenance too often, they can proactively address the underlying problem before it escalates.
In short, geofencing is a great way to streamline various workflows, reduce admin, and improve fleet management efforts as a whole.
It’s a tool that definitely shouldn’t be underestimated.
Streamlining Routing
Many fleet management systems use algorithms and real-time data—such as traffic conditions, weather, and road closures—to automatically determine the most efficient routes.
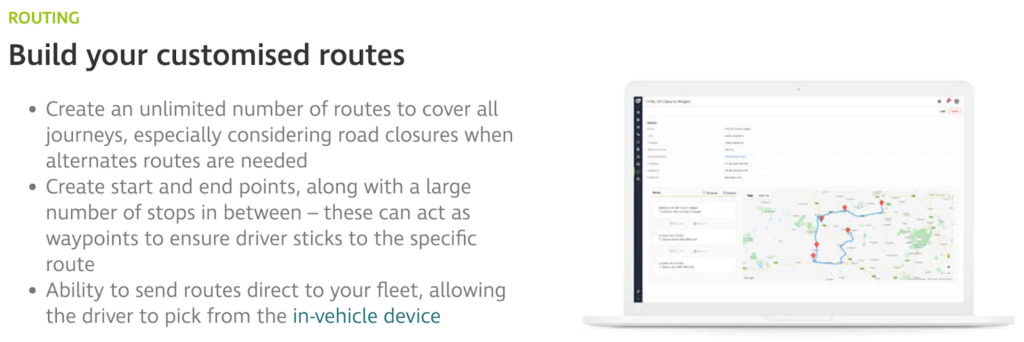
Source: Teletrac Navman
So, instead of planning routes manually, operators can simply set key parameters, such as delivery time windows or priority stops, and let the system handle the rest.
Simon Spriggs, Senior Sales & Partnerships Manager at FLS, a dynamic route optimization software provider, explains why this is such a lifesaver:
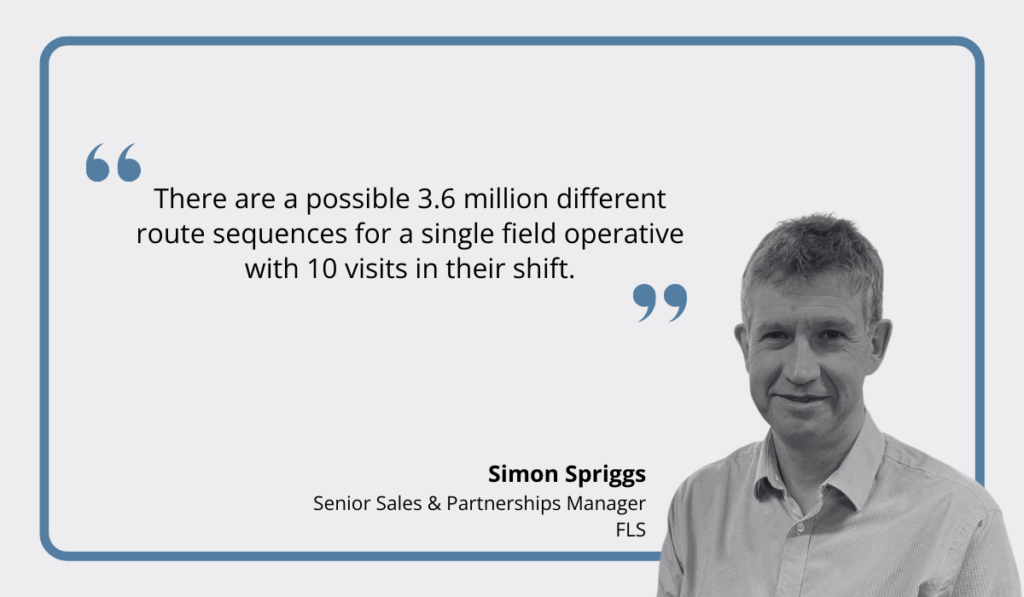
Illustration: GoCodes Asset Tracking / Quote: Fleet News
And that’s without even considering last-minute changes like emergency orders, cancellations, or sick days.
The reality is, manual optimization is a huge time sink that can’t keep up with the complexity.
However, with automated routing, this all changes.
Thanks to this tool, job dispatchers no longer need to track every move of operatives in the field. The system does it all, adjusting routes on the go, saving both time and resources.
QCD, a Golden State Foods company specializing in custom distribution services across the US, experienced this firsthand.
Since adopting automated routing, they have seen significant improvements.
Xavier Alcala, Director of Business Solutions at QCD, elaborates:
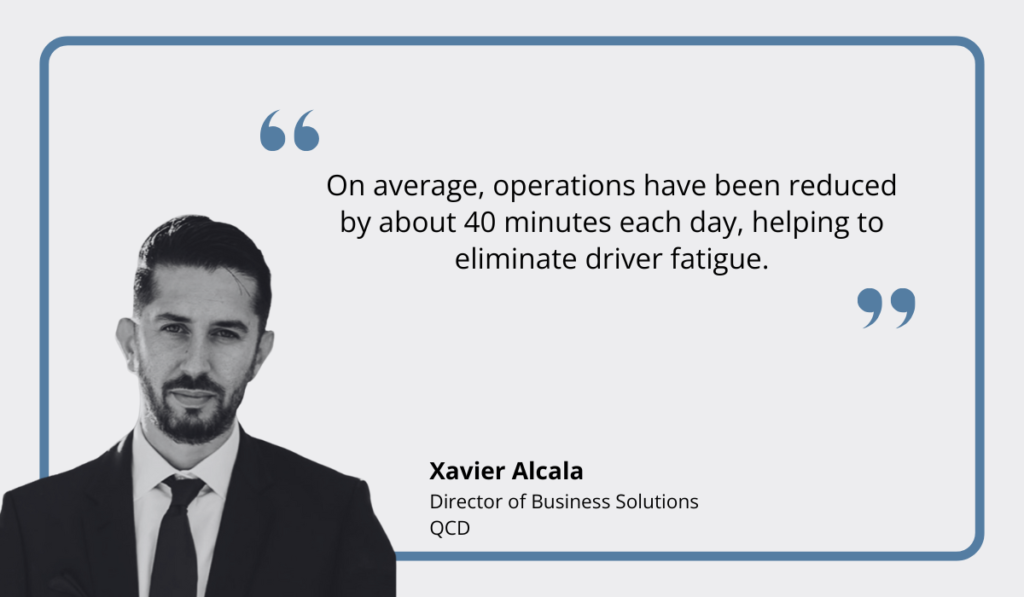
Illustration: GoCodes Asset Tracking / Quote: Fleet Owner
Alcala adds that transitioning to paperless processes has also allowed administrative staff to focus more on customer service rather than paperwork management.
So why stick with the old, slow manual process when modern fleet management software can do it better, faster, and smarter?
It’s time to leave all that repetitive, time-consuming work to technology and focus on what truly matters.
Conclusion
Ultimately, the benefits of fleet management software are undeniable.
Not only does it help you maximize the efficiency of your fleet and take better care of your vehicles, but it also reduces the overall workload while doing so.
Sounds too good to be true?
Yet, it is.
However, if you want to see for yourself, you can always test the system through a free trial before making a purchase.
This way, you can experience firsthand how much of a game-changer these solutions are.
And once you see how much smoother, smarter, and stress-free your operations can be, you’ll wonder why you didn’t jump on board sooner.