Key Takeaways:
- Maintenance logs are usually managed within a single spreadsheet or software system.
- Well-kept logs reduce unplanned equipment downtime.
- 60% of fleet managers still rely on spreadsheets and 52% on paper forms for maintenance tracking.
Keeping construction equipment in top shape isn’t just about fixing what’s broken. It’s about staying ahead of problems before they start.
That’s where equipment maintenance logs come in.
These simple but powerful records help track service history, plan future maintenance, and avoid costly breakdowns.
In this guide, we’ll cover the types of logs, what to include, why they matter, and how to maintain them effectively.
In this article...
Types of Equipment Maintenance Logs
An equipment maintenance log is a record-keeping tool used to track the service history of machinery, vehicles, and tools.
In construction, where equipment is constantly exposed to wear and tear, these logs help teams stay on top of maintenance, avoid breakdowns, and meet safety standards.
Depending on the company’s size and needs, different types of logs can be used.
While the log categories may vary, they’re usually tracked within a single document, spreadsheet, or software system, giving you a unified view of all maintenance activities.
Here are some usual types of maintenance logs:
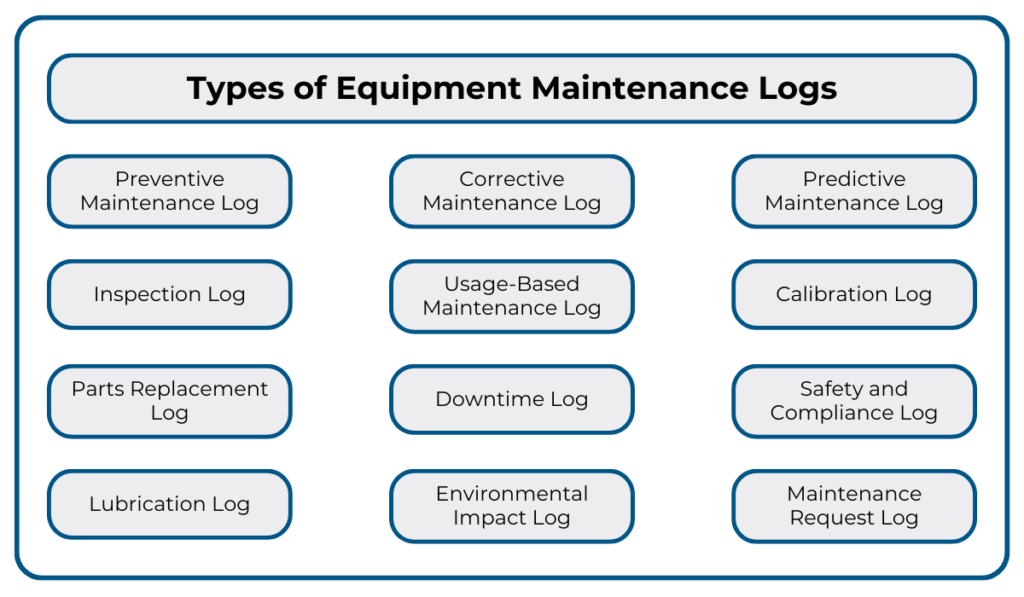
Source: GoCodes
For instance, predictive maintenance logs capture servicing activities based on equipment condition monitoring, often using GPS, sensors, or other data-driven insights.
Environmental impact logs are another type worth exploring.
Typically for sustainability reporting purposes, these track maintenance actions that help reduce environmental harm, such as replacing filters or fixing fluid leaks.
Likewise, maintenance request logs allow managers to monitor service requests submitted by operators or employees, along with their priority levels and any actions taken.
When all or some of these logs are combined, they provide a complete picture of your equipment’s condition and care.
Next, let’s look at what key details every maintenance log should include to stay useful and reliable.
Key Components of an Effective Maintenance Log
An effective equipment maintenance log serves as a comprehensive record of your machinery’s service history.
Therefore, it should capture essential details that help monitor and manage the life cycle of each asset.
These details can be broadly categorized into two groups:
- Fixed data points such as the equipment’s ID number, serial number, make and model, purchase date, warranty conditions, etc.
- Dynamic data points such as service dates, parts replaced, inspections performed, operational hours, technician details, etc.
To illustrate these elements, here’s what a typical maintenance log can look like.
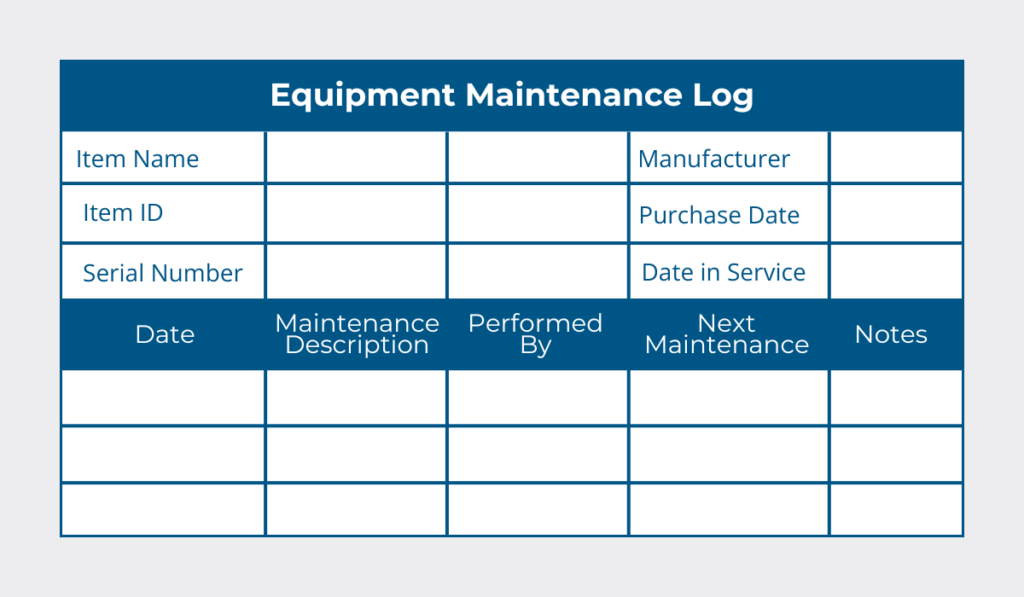
Source: GoCodes
The accuracy of both non-changeable and changeable data, along with regular updates to the dynamic data, makes for an effective and operationally useful maintenance log.
For clarity, an asset’s ID is typically distinct from its serial number.
The ID is assigned by your team or service provider and serves as the primary unique identifier in your maintenance tracking system.
While the serial number should still be recorded, keep in mind that it may not be unique and can often be found in hard-to-see spots.
So, using it as the only identifier could lead to duplication, confusion, and errors in your records.
For this reason, it’s better to use unique equipment IDs while keeping serial numbers on file for warranty and proof-of-ownership purposes.
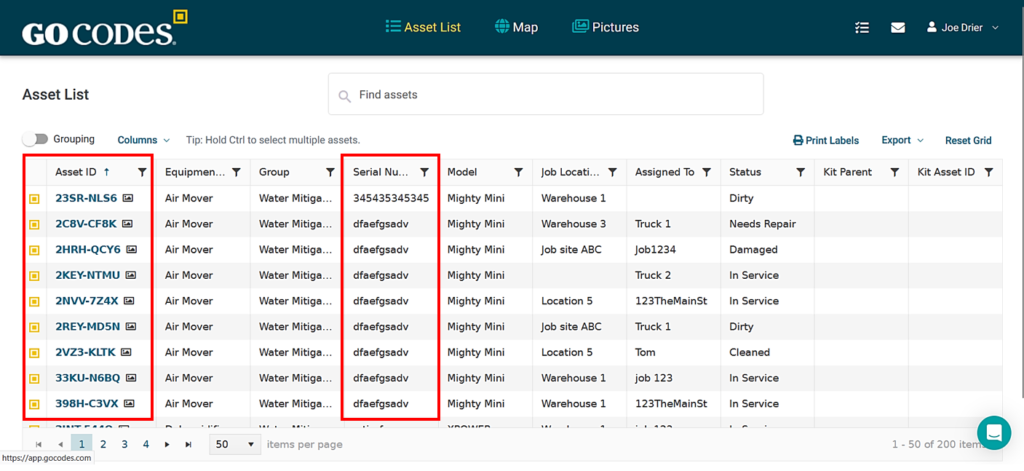
Source: GoCodes
Additionally, including more equipment data—such as fuel consumption, downtime duration, past users, and locations—can help enhance maintenance management and performance analysis.
With these key components in place, we can now explore the importance and benefits of keeping accurate equipment maintenance logs.
Why Equipment Maintenance Logs Matter
Maintenance logs provide a structured way to track service history, ensuring that small issues are addressed before they turn into costly failures.
So, they aren’t just about ticking boxes for compliance. They directly impact your operations, costs, and safety.
Let’s explore the top three reasons why equipment maintenance logs matter.
Reduced Equipment Downtime
Unexpected equipment breakdowns don’t just lead to repair costs—they can throw entire construction projects off track.
When a key machine goes down, schedules slip, crews wait, and progress stalls.
That’s where regularly updated maintenance logs come in.
They help teams stay on top of preventive maintenance and catch early signs of wear or malfunction.
This reduces the risk of failure and the costly ripple effects of downtime, which often exceed the repair costs themselves.
As Daniel Corbett, Equipment Manager at Lancaster Development, puts it:
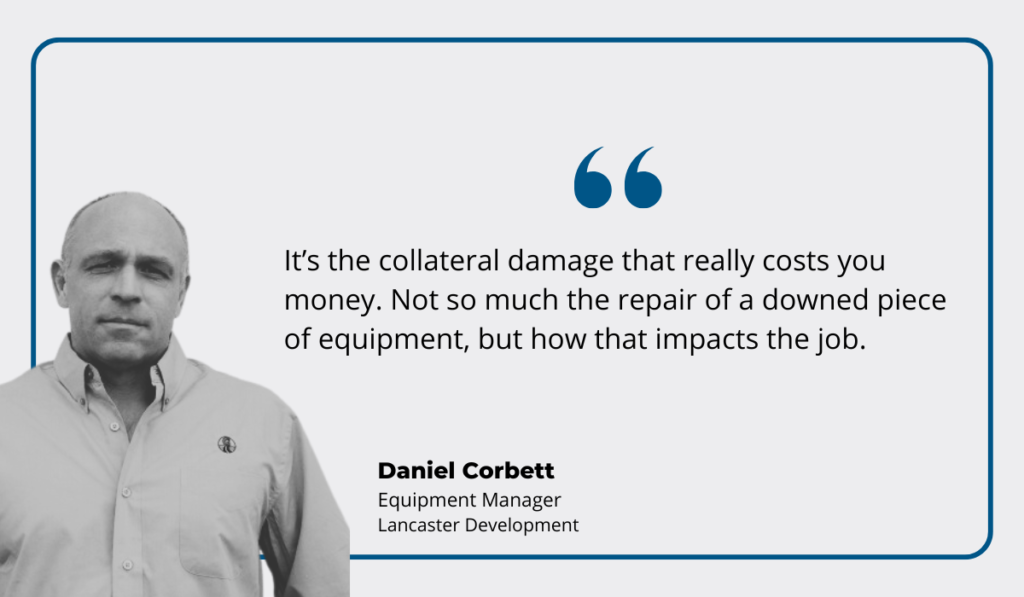
Illustration: GoCodes / Quote: For Construction Pros
Additionally, Corbett and other equipment managers agree that 20% to 30% of a project’s planned duration can be lost to issues related to unexpected equipment downtime.
That’s why tracking service history through maintenance logs is so critical.
These logs allow teams to identify recurring equipment issues, spot patterns in component failures, and adjust maintenance schedules accordingly.
For example, if a log reveals frequent overheating in a particular excavator, technicians can start inspecting the cooling systems on all excavators more frequently.
Over time, such preemptive actions minimize surprise breakdowns, help keep projects on track, and—as discussed next—extend equipment lifespan.
Extended Equipment Lifespan
One of the most effective ways to maximize the return on your equipment investments is to simply make them last longer.
Maintenance logs play a crucial role in this.
By helping teams consistently track servicing and repairs, they reduce wear and tear and keep machinery in optimal condition.
This proactive approach not only prevents major breakdowns but also delays the need for costly replacements.
Since logs support continuous asset monitoring and targeted maintenance, their impact on equipment lifespan can be significant, as shown in OxMaint’s research.
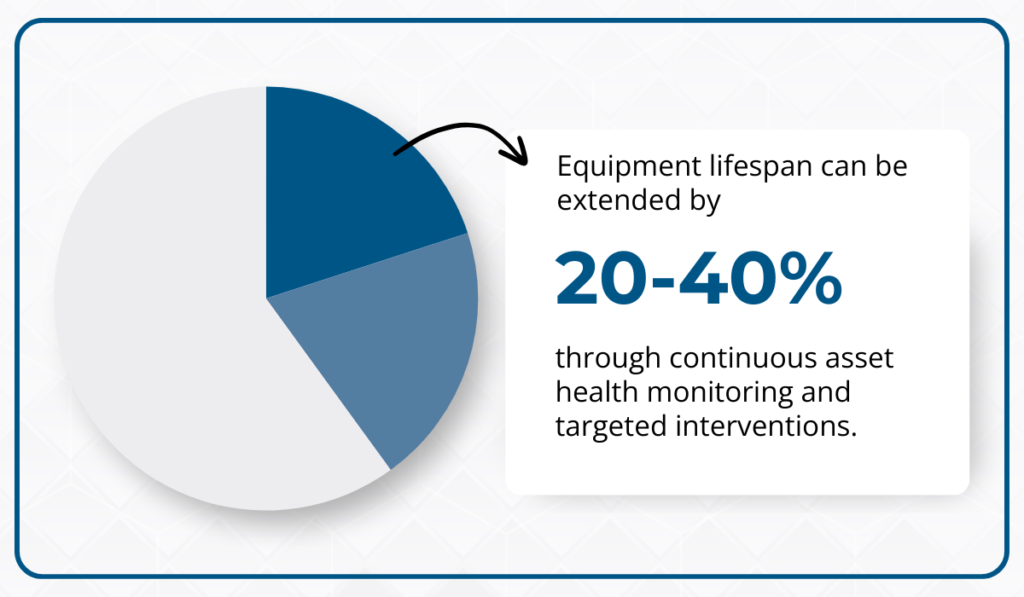
Illustration: GoCodes / Data: OxMaint
To illustrate how logs help in extending equipment lifespan, let’s look at a few examples.
For instance, logs can reveal recurring issues like oil pressure drops or abnormal engine noise, prompting early investigation and corrective action.
And, when managed with the right software, logs can also automate maintenance reminders based on usage hours or other parameters.

Source: GoCodes
Another advantage of using logs is in tracking parts replacements.
If a component is consistently replaced sooner than expected, the log can indicate deeper mechanical problems or improper operation, allowing for timely intervention.
Over time, insights from logs help teams refine maintenance schedules, improve equipment handling, and train operators more effectively.
By learning from past data, equipment managers can take smarter steps to reduce wear, prevent major failures, and extend each asset’s usable life.
Improved Safety Compliance
Preventive maintenance—made possible through consistent logging—is essential for keeping equipment safe to operate and reducing the risk of workplace accidents.
Detailed maintenance records also help construction companies comply with regulatory requirements, including safety inspections and audits.
By documenting maintenance activities, inspections, and repairs, logs demonstrate that your company is actively working to protect employees and ensure equipment safety.
This documentation is often required by safety authorities and standards organizations.
In short, compliance isn’t just about following the rules.
It’s also about proving that you do, as Daren Hansen from J. J. Keller & Associates points out:
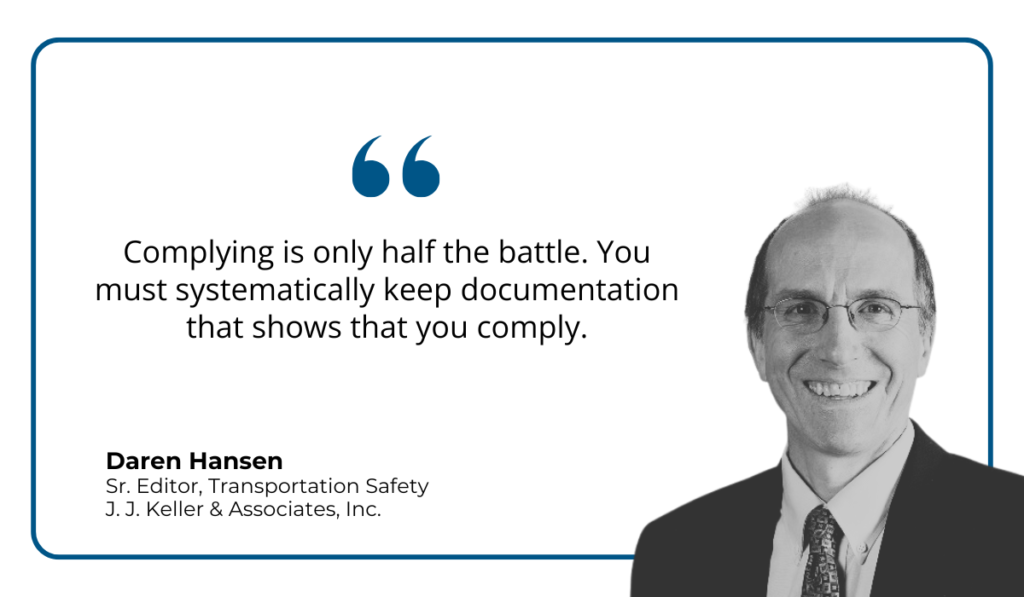
Illustration: GoCodes / Quote: CCJ Digital
He adds that detailed maintenance logs are a great way to demonstrate your company’s compliance to inspectors, auditors, insurance providers, and other third parties.
Likewise, if something goes wrong while your equipment is still under warranty, logs can prove that the asset was properly maintained—a key condition for warranty coverage.
Ultimately, well-kept maintenance logs help protect your workers from injury, your equipment from causing harm, and your business from legal and financial repercussions.
Now that we’ve covered why maintenance logs matter, let’s look at best practices for keeping them accurate, consistent, and easy to use.
Best Practices for Maintaining Equipment Logs
Keeping accurate maintenance logs isn’t just about recording information.
It’s about recording it in the right way.
To ensure your logs remain useful and reliable over time, it’s essential to follow some core best practices.
Let’s look at three key ones: standardization, automation, and regular reviews.
Standardizing Data Entry
Consistent and standardized data entry is essential for maintaining reliable and actionable equipment logs.
Without clear guidelines for recording maintenance data, errors and inconsistencies can easily arise, compromising the integrity of your logs.
This is where standardization becomes crucial.
By ensuring that key information—such as asset details, service history, and repair records—is entered in the same format across all logs, you make data more accessible and reliable.
In practice, standardizing data entry means defining specific data fields and deciding on the formats (numbers, words, codes, sentences) to be used for each.
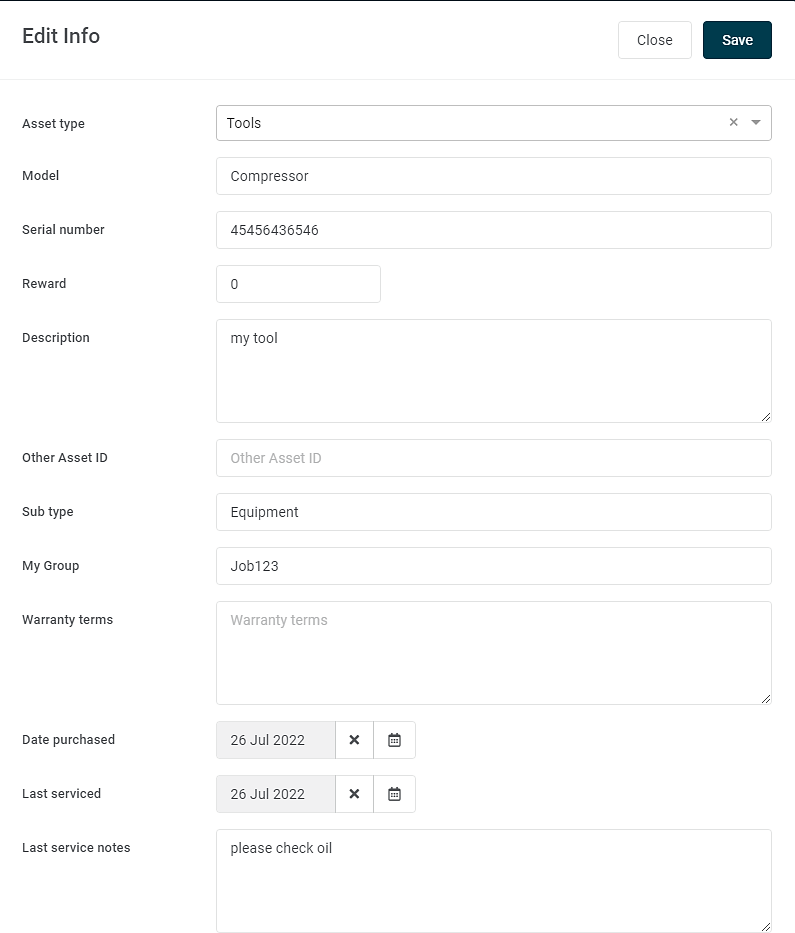
Source: GoCodes
But consistent data field names and standardized entry formats across all logs don’t just streamline maintenance processes.
They also make it easier to track performance and ensure compliance.
Ultimately, this consistency allows maintenance teams to analyze vital information more effectively and make better-informed, data-driven decisions.
It also simplifies audits and ensures adherence to legal and safety standards.
While consistent logs can be maintained in spreadsheets, digital logbooks or software can enforce input standards, such as mandatory fields or dropdown menus.
By doing so, they significantly reduce the risk of errors while automating much of the logging process.
Automating Maintenance Logging
As we just mentioned, maintenance logs are still often kept using a mix of paper forms and spreadsheet tables.
While this at least digitizes records, it offers little to no automation.
Ultimately, this makes the logging process both time-consuming and prone to error.
Still, a 2022 Motive survey of fleet managers across asset-heavy industries found that 60% of them continue to use spreadsheets.
52% pair them with paper documents to manage their fleet.
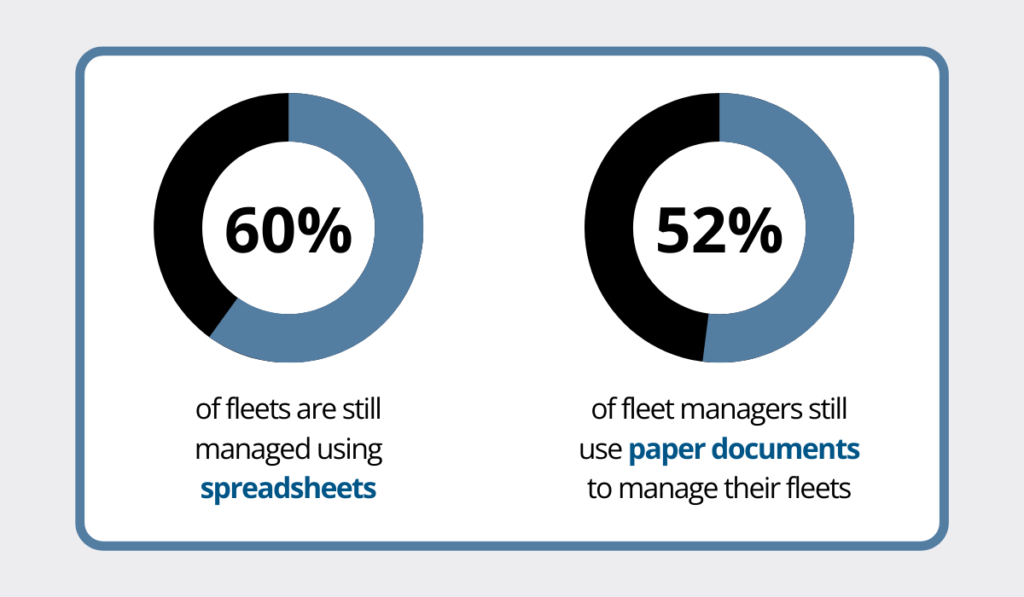
Illustration: GoCodes / Data: Motive
Needless to say, while this paper-and-spreadsheet combination can work for basic tracking, it falls far short of the efficiency provided by asset and maintenance tracking software.
Most modern solutions are cloud-based and accessible from any internet-connected device—smartphones, tablets, laptops, or desktops.
Unlike spreadsheets, this provides your entire construction team, including maintenance technicians, with:
- Instant access to centralized equipment data and logs from any location
- Reduced manual input, as some information is automatically captured
- Built-in data entry error prevention and real-time updates for everyone
- Automated log entries, service reminders, and low inventory alerts
Our solution, GoCodes, offers all this—and more—in one cost-effective platform.
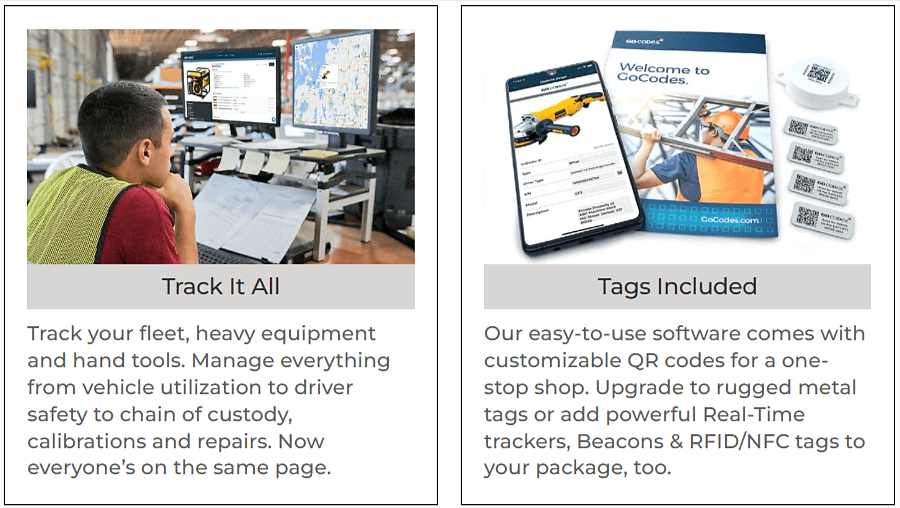
Source: GoCodes
With built-in QR code scanning and GPS tracking, GoCodes streamlines many aspects of construction operations—from fast equipment check-in/check-out to theft prevention.
When it comes to maintenance logging, it provides customizable data fields, maintenance scheduling and alert features, document attachments, and equipment usage tracking.
In short, GoCodes helps ensure your logs are complete, accurate, and consistently up to date.
Once your logging process is automated, the next step is keeping your records clean and actionable through regular log audits.
Conducting Regular Log Audits
Keeping detailed maintenance logs is important, but without regular audits, even the best records can lose their value.
Over time, mistakes creep in: missed entries, outdated information, or inconsistent data formatting.
That’s why periodic log audits are essential.
They help you catch and correct errors, spot irregularities, and ensure your records stay accurate, complete, and compliant.
Just as importantly, audits let you fine-tune maintenance schedules, aligning them more closely with actual equipment usage.
Naturally, this process is much easier when all your maintenance data is stored in a centralized, searchable database, like the one shown below.
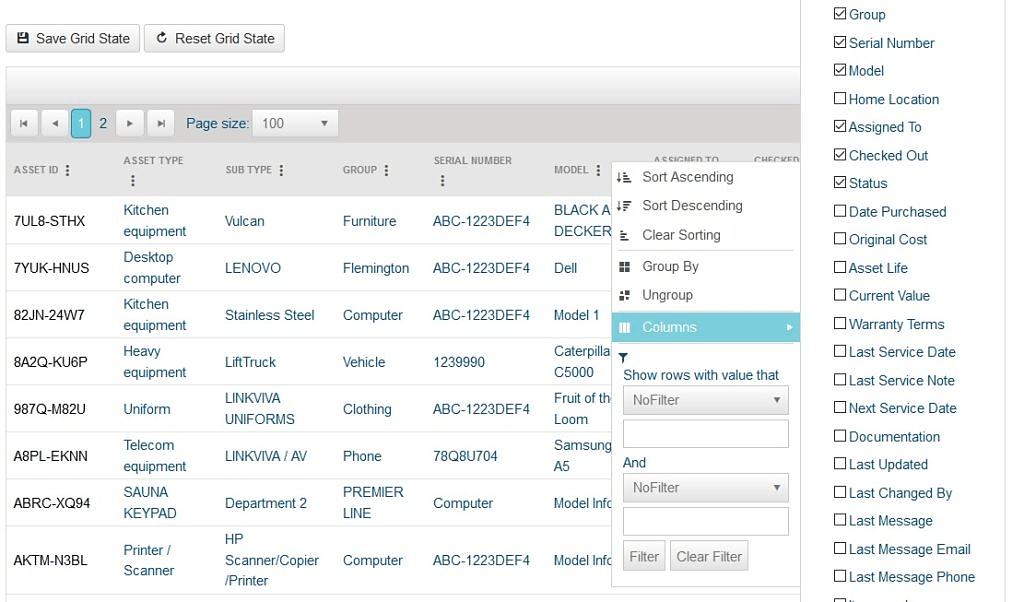
Source: GoCodes
A structured audit process typically involves:
- Reviewing logs for completeness
- Cross-checking them against maintenance schedules
- Validating critical fields like service dates and performed tasks
Depending on the size of your operation, audits might be performed quarterly, annually, or after major equipment cycles.
They’re typically led by maintenance managers, often with the help of software that offers automated reporting features to streamline the process.
Ultimately, regular log audits ensure your maintenance logs stay clean, trusted, and ready for analysis whenever regulators, insurers, or your own team need them.
Conclusion
From types and key components to their benefits and best practices, we’ve covered the essentials of equipment maintenance logs.
Accurate, well-maintained logs are clearly vital for keeping construction operations safe, compliant, and efficient.
With the right tools and procedures, you can standardize entries, automate logging, and perform regular audits.
All of this leads to smarter decisions, less downtime, and lasting operational success.