When an organization ventures on a complete equipment audit, it can seem like a daunting task, but with some knowledge and a few guidelines in place, the job can become much easier.
A business undertaking an equipment audit does not regret the time and effort dedicated to focusing on its assets, both fixed as well as intangible.
Once an equipment audit is complete, it’s easy to move forward with plans to save money, help employees work more efficiently, and work more productively with asset life cycles.
This post will help decision makers and managers zero in on the objective of equipment audits, as well as explain what such audits usually discover.
Let’s dive in!
In this article...
What Is an Equipment Audit?
For a company, undergoing an audit can take on many meanings.
There are many different types of audits, and their definitions also depend on which industry or department is running a particular audit.
Undertaking an equipment audit can meet several objectives at once.
Among other purposes, audits usually fall into any of these categories, and might fulfill multiple categories at the same time:
- Compliance audit: How well and in what ways the company is meeting standards set by federal, state, local, union, or corporate entities such as OSHA (Occupational Safety and Health Administration).
- Efficiency audit: Whether the company’s operations are running smoothly and at a reasonable cost, without unnecessary duplication or bureaucracy.
- External audit: An independent assessment of any aspect of an organization’s operation, such as by an accounting firm or government agency.
- Assets audit: Inventory of each item or each item in a category owned by an organization. May be comprehensive (each item) or targeted (each item in a category, such as information technology).
- Internal audit: Audit performed from within the company, either at the behest of a local manager or corporate headquarters.
What about equipment audits? This type of audit might not inventory every asset a company owns but instead focus on equipment or a specific type of equipment.
For example, a construction company might conduct a full audit on every physical asset it owns pertaining to fieldwork, or it could study only heavy-duty vehicles.
An equipment audit might also explore only IT items, or just office assets (chairs, tables, employee break room equipment.)
The Objective of Equipment Audits
Equipment audits can carry many different objectives.
Defining what you’d like to accomplish with your equipment audit before beginning to undertake it helps to provide employees and management with valuable information.
For example, it shows team members how long an audit should take, what kind of information to note, and the ways in which the undertaking will benefit the company.
Here are a few examples of equipment audit objectives:
- Efficiency of equipment movement
- Correct reporting of transactions and bill pay
- Effectiveness of safety measures regarding equipment use
- Comprehensive count of equipment, along with its condition
- Assessment of equipment life cycle
- Consideration of equipment security procedures and effectiveness
- Study of ethical equipment use
To find the best objectives for your organization, consider what you’d most like to accomplish as a company, as well as how the equipment audit can serve your mission statement.
Are you seeking to streamline a specific action, such as online ordering, so as to increase client satisfaction?
Do you have concerns about compliance with federal regulations? Are you trying to drastically decrease theft and equipment loss?
Clarifying these issues will help you set your objectives and concentrate attention and energy in the most useful places.
What do Equipment Audits Usually Discover?
Equipment audits can result in a number of different revelations. While the most important objective of an equipment audit includes increased efficiency, other surprises may arise.
Working wisely with this information can bring about a more streamlined workday, no matter what equipment is in question.
Some tool rental, construction, and inventory-heavy companies discover the following issues after an equipment audit:
- Incorrect tools used for a task
- Security breaches
- Equipment mismanagement
- Contractors or employees failing to undertake cleaning tasks
- Missing updates to maintenance actions
- Change of equipment custody not documented
- Failure to establish standard operating procedures
- Preventive maintenance skipped
Catching these problems early can not only increase efficiency, but it also helps to avoid run-ins with regulatory compliance officials and increases the life cycle of your equipment.
All types of companies stand to profit from a thorough equipment audit.
Once the work invested in one is complete, regular teamwork and scanning can maintain an accurate database going forward.
Benefits of Auditing Your Equipment
If your company clearly defines your equipment audit and decision makers apply the information it yields wisely, the benefits of auditing your equipment can manifest quickly and for quite some time.
Here are just a few of the benefits to consider:
Effectively Identifying and Eliminating Ghost Assets
Ghost assets are items that are no longer available for company use.
This definition can apply to a number of situations, including stolen items, equipment that is out of order, assets that were never entered into the company’s accounting system, or unsold inventory sitting in a warehouse.
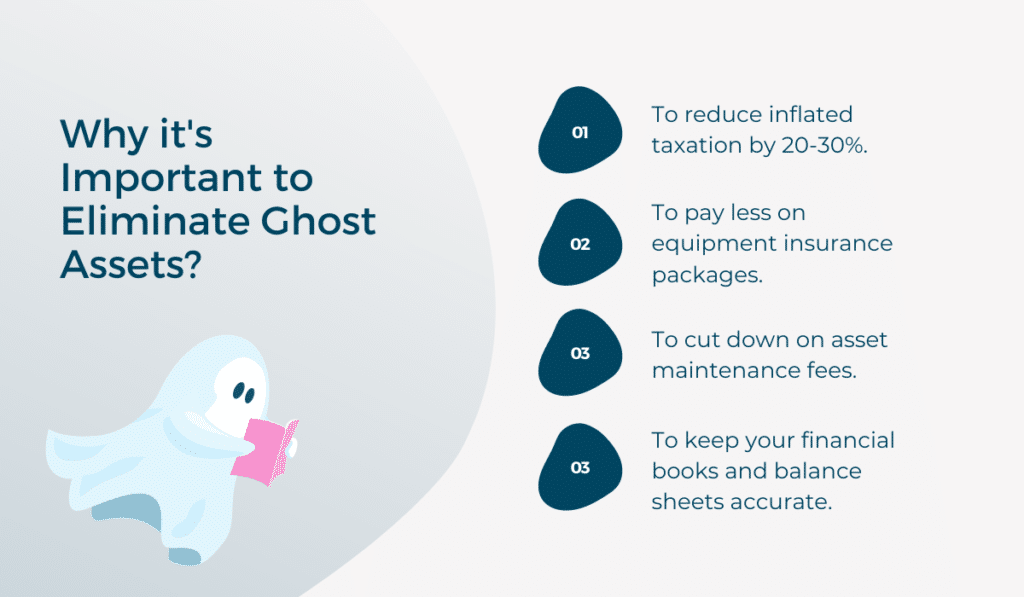
By eliminating ghost assets, a company can recoup or repair the equipment or inventory, sell them as used items, or eliminate them from item counts.
The organization is then able to rely on a more accurate reflection of the company’s equipment.
Optimizing Equipment and Employee Movement
A properly conducted equipment audit results in a clear picture of what the company owns, as well as where it is located and how well it is operating.
This data can also reveal information about employee movement and efficiency.
By learning where inefficiencies occur and how to apply lessons learned from well-run departments and operations, businesses can make the most of who it employs, as well as the tools they use.
Increased Transparency and Trust
Transparency is vital for building trust in each relationship involving the company.
These primarily include the company’s affiliation with its partners, clients, employees, and shareholders.
However, they also entail the public, employees, government entities, shareholders, and even its competitors.

When these connections are confident they can trust that the company is operating in the daylight, they are more apt to forgive mistakes and believe in the organization’s statements, explanations, and plans for the future.
Providing such information as part of an accurate equipment audit helps to build healthy bonds both within the company and outside of it.
Streamlining Rental Operations for All Parties
If a company is using a flexible and comprehensive software and scanning solution for its rental operations, such as the system from GoCodes Asset Tracking, the lender as well as the lessee can rely on the knowledge that the equipment in the system is available and properly maintained.
The system then provides lending companies with a chain of custody.
It also sends out alerts when equipment is overdue and, if desired, provides GPS tracking updates.

An equipment audit ensures that the customer doesn’t arrive for pick-up only to find that the requested item isn’t available at all and is only present in the company’s system as a ghost asset.
The benefits of rapid-scan check-in and check-out, combined with real-time updates, become apparent for both parties.
Asset and equipment scanning systems provide rapid data retrieval, while also sending out reminders to perform preventive or cyclical maintenance.
Procedure for Equipment Auditing
There’s no one procedure for auditing equipment. Companies differ in size, aims, genre, and processes. All businesses are in different stages of growth and facing disparate challenges.
However, certain practices are useful in nearly all equipment audits.
Here is a general outline for planning your organization’s audit.
- Choose an asset tracking software suite: When seeking out the best asset tracking software for your equipment audit, look for one that is flexible and suited to the needs of your company. It should offer cloud storage, a variety of tags, and real-time updates.
- Decide which items to include in the audit: Decide on your company’s goals for the audit. What are you seeking to learn and accomplish? What sort of data will yield the best actionable information? Narrowing down which equipment to audit will greatly assist in planning the rest.
- Affix tags: Employees place tags on equipment targeted for audit. GoCodes Asset Tracking offers a wide selection of high-quality material for tags, ranging from soft polyester to rugged, all-weather metal.
- Scan items: Members of the workforce begin the process of scanning each tag to place baseline data into the software. This is the foundation of the tracking that will provide so much valuable information in the future.
- Equalize and maintain system: Incoming employees should receive thorough training on how to properly scan and maintain equipment and asset tracking. Once the initial equipment audit is complete, this action will render the next one much faster.
Information will continue to build with each scan, providing an invaluable data stream on which to base decisions about equipment life cycles, employee movement, and asset scheduling.
Of all these steps, choosing an asset tracking and tagging system is the most important.
It forms the basis of not only how the system will operate initially; it is also a decision that will provide a data stream that affects decision-making for the foreseeable future.
That’s why it’s best to choose an established, reliable, and technology-forward company like GoCodes Asset Tracking.
How Does Equipment Tracking Software Help With Audits?
Modern app-based tool and equipment tracking is a major building block in conducting successful equipment audits.
Equipment management software may have had its roots in electronic spreadsheets, but this technology is now limiting and outdated.
Manual entry is often inaccurate, security is precarious, and the system does not update in real time.
Equipment tracking, however, is a vast improvement on all these detriments.
Not only are most employees innately familiar with how the app operates due to their probable familiarity with similar systems, they are usually able to use their personal devices or quickly adapt to company equipment.
One way GoCodes Asset Tracking embeds this valuable function in its software is to offer an Audit Mode.
Audit Mode is useful in confirming or updating data about where equipment is located. Any employee can accomplish this simply by using a tablet or smartphone to scan the asset’s QR code.
Here’s how Audit Mode works:
- Opening the app automatically logs the employee into the system
- The app automatically begins to scan—no need to waste time tapping in the command for each piece of equipment
- Scanning continues unless the user cancels the process
- If the employee cancels the scan, the app defaults to the main scanning screen
- Simply clicking “Scan” continues the scanning process without further interruption
- The user can easily toggle Audit Mode as necessary
- A gear icon located on the app’s main screen allows the employee to control the activation of Audit Mode
Here is a look at how GoCodes Asset Tracking software’s Audit Mode works to quickly locate tools and other valuable equipment.
As you can see, the system not only provides the location of the asset, but also the date, time of the scan, and name of the employee conducting the scan.
QR code scanning is fast, automatic, and accurate.
Once the scanning is complete, the software automatically stores and sorts its new data.
The user can quickly enter the system to manage bulk assets and verify other information.
While this feature is useful in many ways, it is especially helpful in speeding through audits which take place on a regular basis, such as quarterly or annually.
Tool tracking, then, is much more than simply knowing where equipment is located or maintaining a real-time data screen.
Using the right software or app opens many new possibilities to view, control, and streamline inventory processes.
Conclusion
Equipment audits can help you uncover critical data about your business and improve its operations. Luckily, they can be less stressful when you use modern solutions.
Clients are often surprised that an asset tracking system, in addition to providing real-time and easily sortable data, is also useful in conducting equipment audits.
A system like GoCodes Asset Tracking provides for an exploration of the many benefits of auditing your assets and equipment.