In everything we consume, from the clothes we wear to the cars we drive, we strive for quality. It’s no different for the construction industry: we all want to live in well-built houses and work in well-built offices.
Unfortunately, not all contractors control the quality of their projects; according to research, 55% of construction defects are caused by human factors such as unskilled workers or insufficient supervision.
Furthermore, 12% are caused by system failures and poor choice of materials.
If you want to avoid being a part of these statistics and learn how to ensure the quality of your construction projects, keep reading.
In this article...
Have Skilled Workers on the Team
Workers are the essence of any business, so if you want to ensure quality products, you should pick your workers wisely.
The skill of your workers will directly affect the quality of your project. Before you even start, make sure to assign the right employees to the right jobs and let everyone know what standards you expect.
However, the construction industry is currently experiencing a labor shortage, which means you might struggle to find workers who will be able to deliver the kind of quality you strive for.
Research proves the severity of the situation; in 2019, 80% of contractors reported difficulties with hiring skilled workers, and 35% said they expected finding a workforce would get even harder in the future.
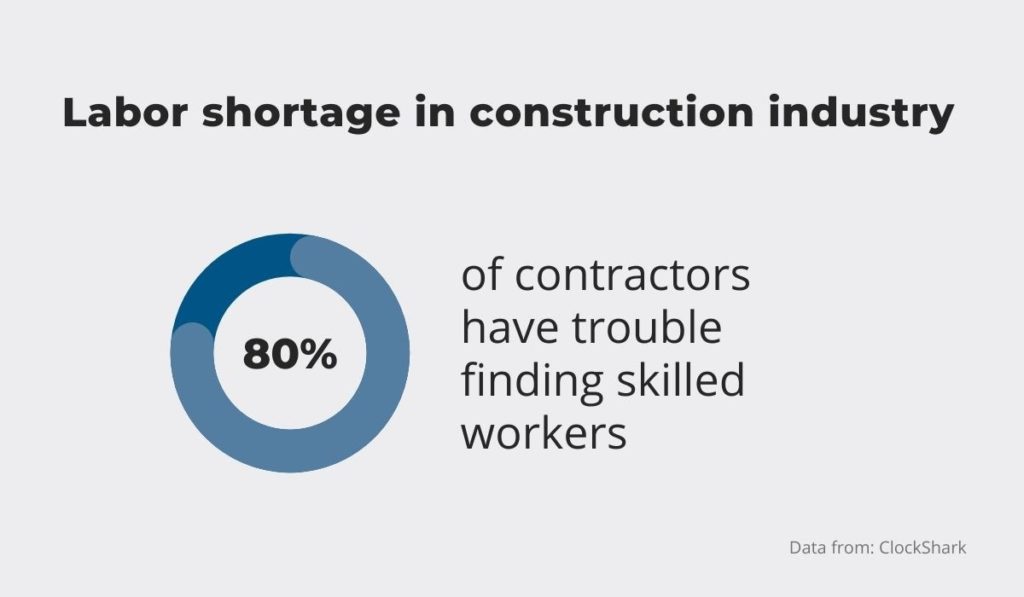
When we talk about a skilled workforce, we refer to workers with the relevant abilities, training, and experience. Their expertise and knowledge elevate the projects they work on.
On the other hand, unskilled workers who lack training and expertise have a negative impact on the quality of the work.
But since finding workers with specific skills or experience might be difficult, you can always hire less experienced ones and train them.
Training will improve their expertise and efficiency, which is crucial for ensuring the quality of your projects.
Realistically, education programs are no guarantee the worker has developed the required skills; on-site experience is.
For example, the amount of air mixed into concrete or the depth of a weld can be responsible for the success or failure of your construction project. That’s why you should invest in training for your workers in the field.
Simply put, even the best company won’t be able to uphold quality standards without skilled workers.
Finding a skilled workforce is a challenge in the construction industry nowadays, but if you invest in teaching your staff new skills, you will reap the benefits in terms of productivity and quality in no time.
Carefully Vet Your Material Suppliers
No matter how good your workers might be, if the materials you use are of poor quality, your project will fail, so be careful while choosing your suppliers.
Since the quality of your project depends on the materials you use, make sure that you order materials of the correct specifications and that they meet quality requirements and project specifications.
This should go without saying, but we will still point it out because it’s easy to forget; double-check the materials when they arrive to ensure they are in line with your specifications and that they aren’t damaged.
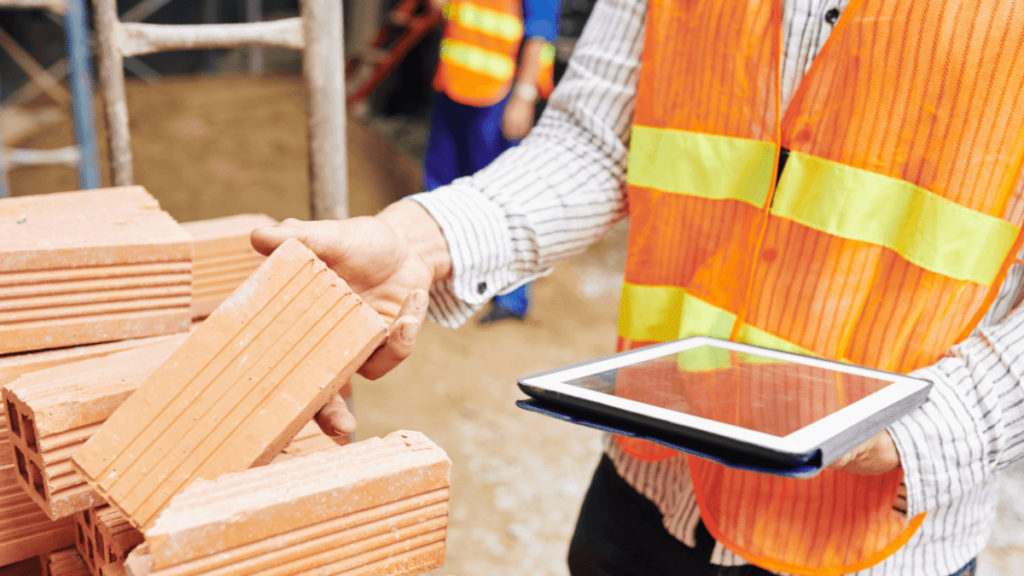
For example, imagine not catching a bad batch of concrete before pouring it; later, it will cost a huge amount of money to repair or replace it during the construction.
Yes, instances like that do actually happen, and it takes a lot of monitoring and checking to prevent them.
Other than monitoring, the solution to avoiding these types of situations is finding a good, reliable supplier. But, how do you do that?
Well, first of all, always check certifications. Only use suppliers that meet your quality standards. Another even better way of ensuring this is to check their references or testimonials.
Positive comments speak volumes about the supplier’s true abilities. Negative ones speak even more, so make sure to check other contractors’ comments before you complete your order.
Another thing to keep an eye out for is customer service.
Good customer service is essential because, more likely than not, you will need to make some exchanges or returns if the material you ordered doesn’t meet your quality requirements.
Of course, you want to do it as soon as possible to avoid delays with your project, so friendly and helpful customer service is a must.
So there you have it, to avoid having a poor quality project, you must avoid poor quality materials, and the best way to do that is to find a good, trustworthy supplier.
Establish Standards to Follow
To ensure the quality of your construction projects, you must have standards to follow in the first place.
Setting your standards high from the start is the best thing to do if you want to ensure the best results. Don’t forget that every project is unique, so quality should be measured based on the type of construction and terms stated in the contract.
Make sure the standards you set are easy to understand and monitor, in accordance with the type of your project.
Usually, they include international, national, and local building codes; third-party testing standards; and recommendations and requirements from the manufacturers of the products used in the construction.
Adhering to those codes and requirements results in improvements in the communication between the parties involved, as well as the production economy, safety and health, protection of consumer interests, etc.
The requirements are established in published documents called procedures, and their main purpose is to develop and codify the methods that will be used.
Perhaps the most widely accepted of such codes are the ISO standards. Some of the most relevant ones for the construction industry are ISO 9001, ISO 45001, and ISO 14001.
ISO 9001 is used to regulate quality. It manages subcontractors to ensure that processes and procedures are in place. Adhering to this standard also entails regularly monitoring suppliers and maintaining an approved supplier list.
ISO 45001 refers to health and safety so that you can have fewer on-site accidents and code violations. It will also improve your overall performance.
And last but not least, ISO 14001 will help you monitor and control your construction operations’ impact on the environment.
The benefits of this standard also include improving your image and credibility. In this way, you can get new customers and save on costs.
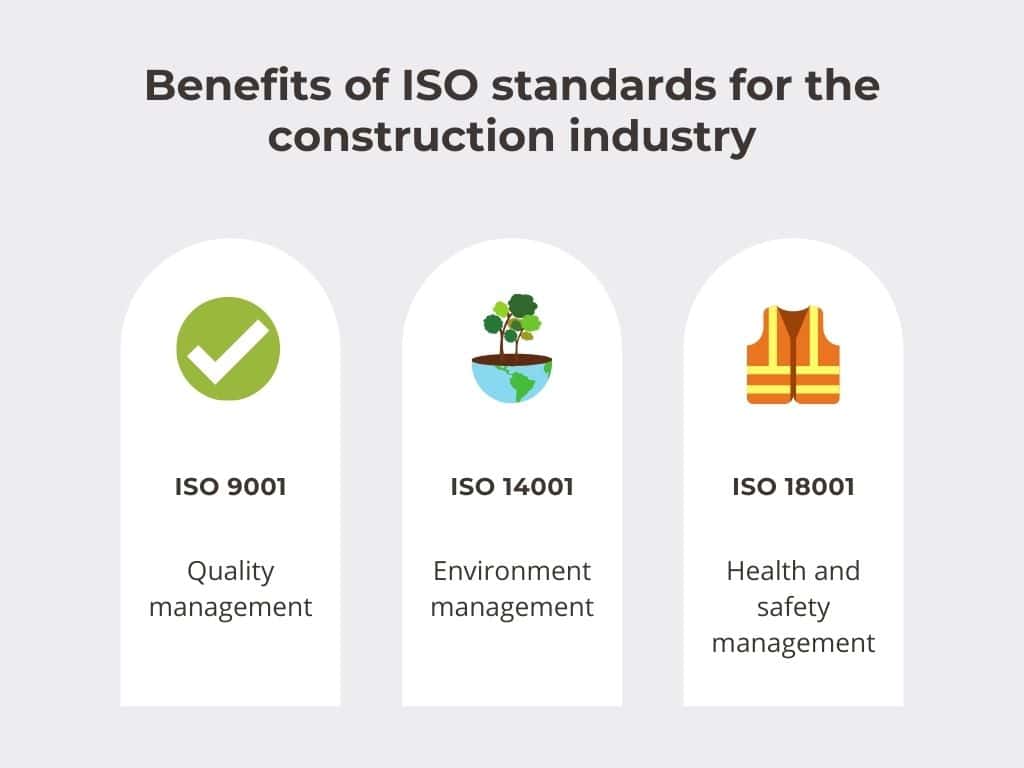
To sum up, if you establish standards and follow them, the quality of your construction products simply must improve.
Invest in Technology
Quality control and quality assurance require a lot of information, data, documents, and reports which is why it’s crucial to invest in technology.
Even though construction is one of the oldest professions, technology offers some amazing benefits to the industry that make running your business a lot easier.
However, a lot of companies are reluctant to invest in new technologies and one of the key reasons is that many decision makers find it difficult to convince their employees to adapt to new things.
But technology doesn’t need to be complicated; you can start with simple tracking solutions, like our own equipment tracking software, GoCodes. It will help track your equipment to ensure it’s in top shape, safe to handle, and available when you need it.
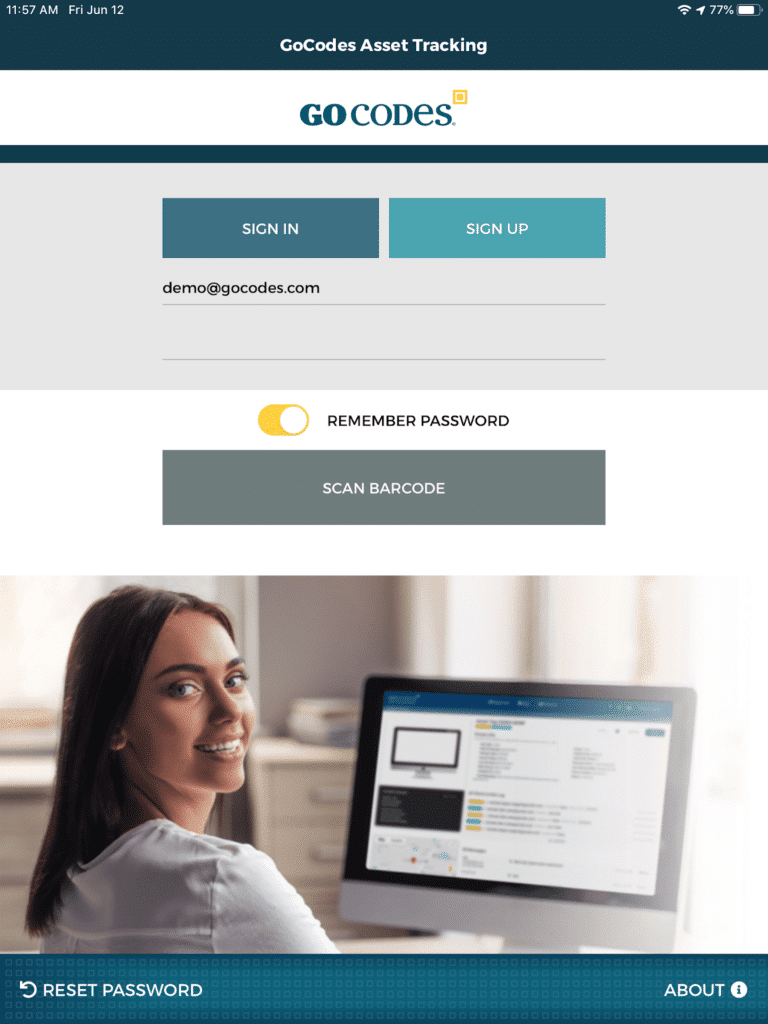
Software tools can also assist you during the quality control process, particularly by facilitating the flow of information between the stakeholders. We all know that communication is the key to any relationship, whether in a marriage or business.
For instance, keeping all project documents, drawings, and reports in a centralized location in the cloud will reduce the chances of miscommunication, outdated documentation, and similar issues.
Cloud-based software will also make it easier than ever to capture quality-related datasets and share the results with your team or your clients.
Technology also helps you handle a contractors’ worst nightmare—improperly performed work. Reputation is everything, and you don’t want to jeopardize it, so it’s good to have technological solutions in place that help you ensure quality.
For example, Milwaukee M12 FUEL Digital Torque Wrench is a smart tool specifically developed to deliver accuracy and quality assurance in repeatable electrical installations.
With the help of this tool, you can automatically sync fastening data and generate reports for your clients. In this way, they will be assured that the job is being done properly.
Therefore, technology is not something to be fearful of. With the help of various tools, you’ll be able to ensure the quality of your team’s work and take your construction business into the future.
Regularly Audit Completed Work
Consistently monitoring progress and inspecting completed work is an important part of any quality management process. Doing so makes it possible to flag any potential issues on time and correct them on time.
In construction, stakeholders ensure that everything is performing properly with an audit.
The auditing and testing workflow needs to be clear and precise.
Everyone involved in the project needs to be on the same page about what qualifies as an acceptable result.
So, you’ll first need to define what it means to be “done.”
For example, you can specify that a project is regarded as completed when it has no visible defects and complies with minimum code standards.
Remember, be very clear with defining your criteria so that your employees will know how to meet your expectations.
The second thing to do is to create an inspection plan. Every construction project requires dozens or even hundreds of audits, so a good plan is a must.
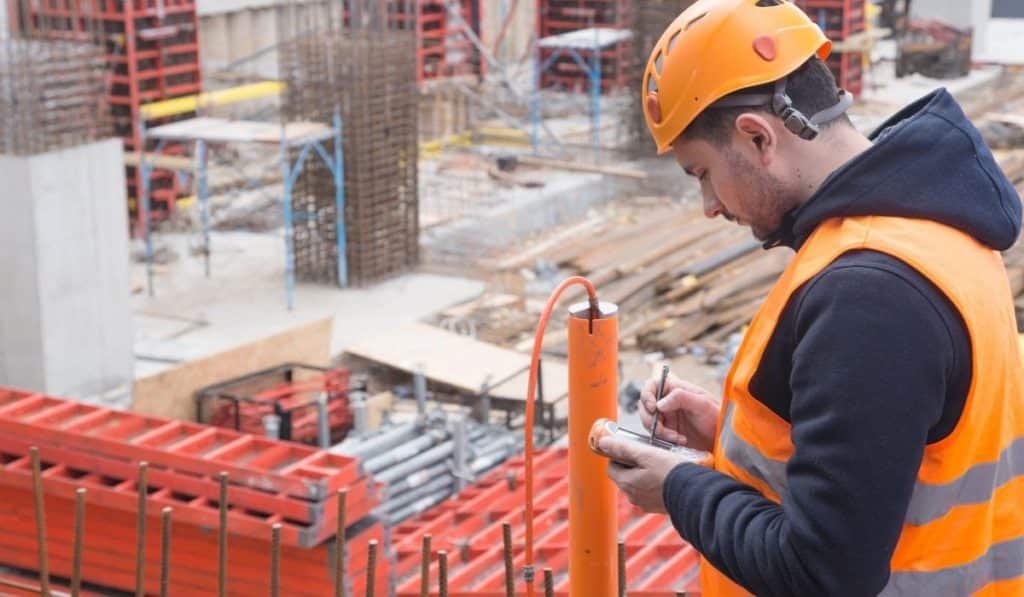
Your team needs to know what to inspect, when to do it and who is responsible for the inspections. Based on the skills and experience they possess, you can choose someone from your team or decide to hire an external specialist.
The last thing you should do is define which part of the site you plan to audit.
Because inspecting an entire construction site would be very time-consuming, site audits are normally conducted only on a small section of it. Based on those findings, you can then draw conclusions for the rest of the site.
A construction site audit is never an easy task, but it will be valuable both for the client and the contractor when done properly. It can reduce costs, enhance safety, and, best of all, ensure the quality of your project.
Address Deficiencies Immediately
If you detect some deficiencies while auditing, it’s vital to address them right away.
Deficiencies are common in construction, and most of them are minor and easy to fix. However, some of them can also be dangerous, and by not addressing them on time, you risk damage to the property or your workers.
Moreover, one small issue can snowball into a much bigger problem and sabotage the integrity of the whole process.
In order to resolve such issues on time, the first step you need to take is to determine what caused the defect in the first place.
Reasons can vary; for example, the defect can be in the design, a result of a failure to produce accurate construction documents. The solution is usually to do some sort of redesign and replacement of some parts or components.
Defects due to damaged or poor quality building materials are also very common. Fixing them is usually very expensive because it may require additional labor and new materials.
As implied in previous sections, skilled workers, a good supplier, and regular inspections are your best options to prevent material defects.
In the eyes of the court, you will most likely be responsible for any kind of defect, and your insurance company will have to pay for damages in case of any accidents resulting from it, so it’s important never to ignore the warnings.
For example, Frank P. Morabito, an engineer from Florida, tried to draw attention to a concrete slab that had sustained major structural damage years before a 12-story condominium collapsed in June 2021, resulting in 98 deaths.
According to his report, the major issue was the waterproofing below the pool deck and the entrance drive that was failing. There was also abundant cracking and crumbling in the underground parking garage.
If Morabito’s warnings about the quality of the construction work had been taken into consideration, the accident could have been easily avoided.
A similar thing happened in Fairfax County, Virginia, during the construction of the infamous Skyline Plaza Complex.
In 1973, while the commercial-residential complex was under construction, one of the apartment buildings collapsed, killing 15 laborers and injuring 40.
Investigators found that the original design plan had no deficiencies and that poorly managed construction processes caused the collapse.
The court found the contractor and the engineer guilty of negligence as they neglected to follow the building code or inspect the work properly.
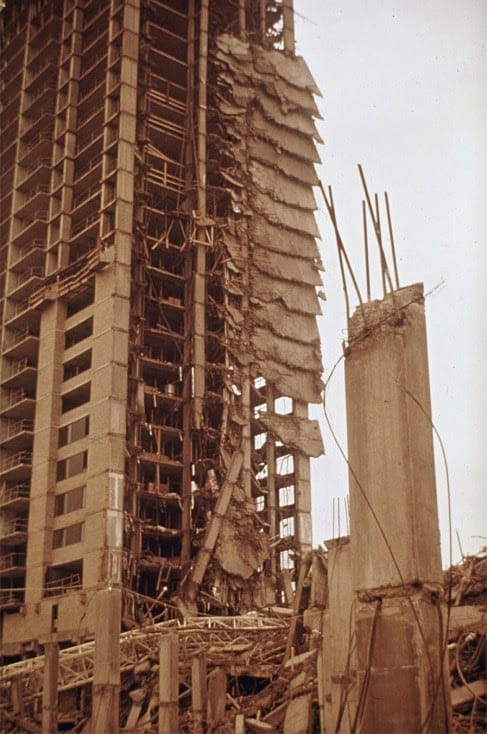
Therefore, make sure to fix any deficiencies immediately to avoid costly repairs or even major accidents later on.
Conclusion
Ensuring the quality of your construction projects is essential to prevent costly repairs and mistakes.
Good quality construction definitely requires teamwork; you’ll need some skilled workers, reliable material suppliers, and good management.
Every stakeholder in the project must do their part in ensuring that everything is up to par.
This includes following the construction standards, monitoring the work while it is ongoing and auditing it once it’s done, and most importantly, addressing the deficiencies immediately.
By following the advice from this article, you’ll be able to produce high-quality construction projects that will make you proud.