Before sending your employees to the construction site, you must provide them with proper training and make sure they have the necessary skills to perform their job.
On top of that, you need to provide personal protective equipment (PPE) for each employee at your own expense to ensure their safety.
Sadly, despite companies fulfilling these conditions, accidents are still very prevalent in the construction industry.
This article will explain the ten most common hazards at the worksite and explain how you can prevent them from causing injuries or fatalities.
In this article...
Heights
Heights are the number one cause of death at the construction site.
Why? Sadly, the top OSHA-cited standard is fall protection, which means that OSHA most commonly finds safety hazards related to falls during construction site safety inspections.
Workers often have to use ladders, scaffolding, or work on roofs on the construction site.
If they’re not sufficiently protected, falls and accidents can easily happen, resulting in injuries and even fatalities.
On top of that, your employees can fall into holes or larger pieces of equipment unless you ensure fall protection to prevent falls from happening.
If you want to keep your worksite as safe as possible, invest in fall protection.
Major Fall Prevention
You have to protect your workers from falls by investing in protective measures like personal protective equipment (PPE), toeboard, and guardrails, among others.
If your employees work at the height of four feet or higher, you must provide them with fall protection, as per OSHA’s standards.
In addition, you have to cover each hole on the ground or larger equipment to prevent workers from falling in.
Use toeboards to prevent employees from falling into something and guardrails to prevent falling out of scaffolding.
If they are working on elevated platforms, you need to provide handrails as well.
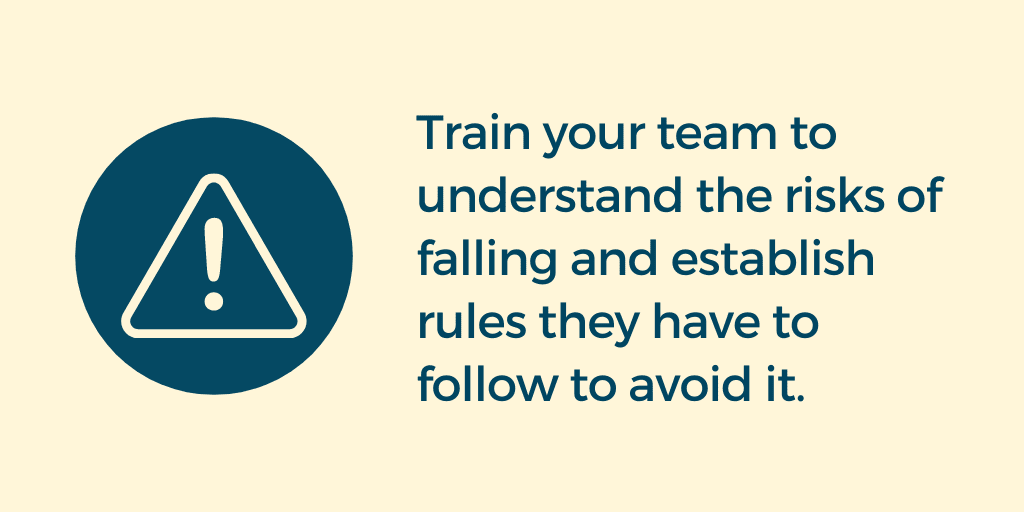
An important aspect of fall protection is training your team to understand the risks of falling and the rules they have to follow to avoid it.
Additionally, when possible, avoid working at heights altogether as much as you can. If you can do certain aspects of the job on the ground, opt for that, even if it takes more time.
For more information on fall protection, check OSHA’s recommendations.
Collapses
A big problem at the worksite is the risk of collapses, whether of trenches, parts of a building, or a construction site structure like scaffolding.
If the workers are unprotected, they can get stuck between the debris and the ground, which can result in fatalities.
In trench collapses, the workers can get buried under the dirt. The fact that trenches are deeper than they are wide also poses a risk in case of a collapse.
Factors that can affect building or wall collapses include old materials, excess moisture, and lack of proper support.
Of course, accidents can happen with improper handling of heavy machinery, which can unexpectedly bring down a piece of a structure.
Think of the safety of the worker who has to enter the trench and perform the task.
Collapse Prevention
If you have to use trenches at your worksite, ensure maximum safety by using PPE and enforcing a protective system for the employees.
Always inspect a trench before allowing your workers to use it—it has to have a safe entrance and exit, and its sides have to be supported.
Otherwise, you’re facing a considerable risk of a collapse. If a worker happens to be inside a trench at the time, they can be gravely injured or even killed.
When working on a building, determine the collapse risk of the whole structure or a part of it.
Then, inspect the materials and measure moisture before letting employees work on the building.
Also, determine the level of support the walls have, especially if you’re working on demolition.
When there’s an error in judgment, and you take the wrong wall down, the others might come down unexpectedly, posing a dangerous threat to anyone working at the site.
Moving Objects and Vehicles
Construction sites are never still—there’s always something going on in each phase.
Vehicles come and go, and so do workers and equipment.
What you see on the first day of construction is not the sight you’ll see in a week or two, which is why there are many safety risks to consider.
One of such risks is precisely the moving equipment on the site, including vehicles.
Construction sites are rarely on even ground. As a result, there are always some holes, trenches, and unevenly distributed dirt around, which causes the moving equipment to pose an even bigger risk as it can tip over and harm employees.
Vehicles can hit employees, especially if the driver cannot see them. They can also crash into objects, causing them to fall over and harm those around them.
Accident Prevention
The person in charge of running the equipment and driving the vehicle needs to be trained on the proper usage and the importance of safety when using such equipment.
If the driver hasn’t attended safety courses, they might drive in an unsafe way.
For example, they may speed on uneven ground, causing the vehicle to fall over and risking the lives of everyone around.
Workers shouldn’t leave the keys in the ignition, and they should lock down moving equipment after use to prevent the assets from moving on their own, posing a risk to others.
Other employees should steer clear of moving equipment to avoid injuries.
However, if they have to work around such equipment, they should remain careful, and wear high-visibility PPE to ensure the driver sees them.
In cases when vehicles and moving equipment have to work around pedestrians, you must create a pedestrian zone so it’s clear where there is no risk of moving equipment.
Those leaving the designated area should be extremely careful when doing so.
Of course, the employees should wear protective equipment and clothing at all times.
Electricity
Exposure to electricity can cause severe injuries and even death in the construction industry.
Because the worksite conditions are not ideal, electrical wires and protection can get damaged or worn out, posing a risk to those who use the equipment or touch electrical cables.
Factors contributing to equipment damage are bad weather conditions, excess humidity, and exposure to dust, steam, chemicals, and water.
Also, there is always the risk of exposing old live wires during demolition or work on a building.
This can also lead to accidents, especially if your employees aren’t aware of the danger or aren’t sure if the wires are live or not.
However, the real threat of electricity lies in the fact that you don’t have to touch any wire to get electrocuted—it’s enough to handle a nearby object or material with conducting properties to feel the consequences.
An employee may not even be aware that the object is touching a wire and therefore poses a safety threat.
It’s no surprise that electricity is one of OSHA’s so-called “fatal four”—the most common causes for construction site injuries—along with falls, caught-in-betweens, and struck-by injuries.
Electrical Injury Prevention
For your workers to be safe around electricity, ensure that everyone is wearing PPE. The higher the potential of an electrical incident, the more protected your workers have to be.
Of course, the staff also needs to have proper training.
Inspect the construction site before sending employees to work on it to determine the potential electricity risks.
Once you understand the weak points of your site, you can adjust your safety plan and training.
If there are wires around, educate everyone on the necessity of using testing equipment such as multimeters or megohmmeters instead of touching wires.
Moreover, if you need an employee to do electrical work, ensure that the person is a certified electrician and not just a regular employee with basic electrical skills and training.
Also, a worksite with many cords and outlets needs to have protectors for them so that no one is in danger if they accidentally come in contact with live wires.
Manual Handling of Heavy Objects
When working on a construction site, employees often have to carry tools, equipment, or waste from place to place as they move along.
While they’re carrying heavy objects, they can experience different injuries or falls.
To prevent this, it’s essential to train employees well on this point and teach them to recognize what tasks are within their realm of possibility.
An additional risk in the construction industry is the repetitive nature of specific workplace tasks, which leads to strains.
Manual handling of heavy objects doesn’t often result in fatalities. Still, it can cause injuries such as cuts, bruises, or more serious musculoskeletal conditions of the neck, limbs, and back.
This happens because of a lack of training, inexperience, impaired judgment, or refusal to use machinery instead.
The Prevention of Injuries Resulting From Heavy Objects
Always ensure that there are enough people around when workers have to carry something from one place to another.
If you have one worker for a two-person job, you should postpone the task or use machinery instead.
Train your employees to recognize when they can manually handle heavy equipment on their own and when they should ask for help or opt for machines.
As a rule, if the equipment is heavy, the worker shouldn’t carry it.
Instead, they should use machinery and save on time if there is more equipment to move to another place.
Plan to have equipment delivered precisely to where employees need it instead of leaving it all at the same spot and expecting workers to carry equipment around.
Allow your workers to practice safe lifting techniques to prevent injuries when picking up, carrying, and placing down heavy objects.
Harmful Materials
Remove or control harmful materials at the construction site to guarantee everyone’s safety.
Harmful substances are all over your construction site, starting from dust, gases, vapors, chemicals, cement, lead, and solvents.
These can cause injuries or fatalities, depending on the degree of exposure and severity of contact.
Some substances like solvents directly affect your brain and nerve function and get stored in your fatty tissue.
Other potentially hazardous materials like dust and mold can affect the respiratory system, while artificial mineral fibers affect your skin and eyes.
You have to be aware of all potential issues to prevent them from appearing in the first place and protect your workers.
Chemical Injury Prevention
Always inspect the work site for any hazards, including harmful materials.
If you believe your worksite is contaminated, invest in decontamination before sending your workers there and ensure everyone is protected.
Remove such materials from the worksite as soon as you can.
Determine what risks your workers will be taking on the field and provide them with the necessary PPE.
Introduce all potential hazards to your employees and pinpoint their location, so they can be even more cautious when in the general vicinity of such substances or materials.
If you have to use hazardous materials on the site, ensure that supervisors monitor them carefully.
Even more than other assets, you have to know where harmful materials are at all times.
Otherwise, you’re risking that it stays unsupervised on the site with a high risk of causing injuries.
Noise
Construction sites can be very noisy, which is why you have to invest in noise protection.
While noise cannot cause fatalities or immediate serious injuries, it poses a real threat if you expose your workers over a longer period of time.
The situation is so grave that around 25% of construction workers have a hearing impairment that affects their activities, while 31% admit to not wearing noise protection equipment.
If the noise at your workplace is at 85 decibels or higher, you’re required to protect your employees’ hearing—regular exposure to noises that loud can affect the hearing and cause permanent damage.
The more decibels a tool produces, the more it will damage your hearing.
Keep in mind that many tools are a lot louder than is optimal—a jackhammer registers at 100 dBA and a hammer drill at 115 dBA.
Even if only one employee is using loud equipment, each of them has to wear ear protection. The same goes for cases where any kind of demolition or planned explosions are happening.
Hearing Loss Prevention
The most important part of noise safety is wearing ear protection such as ear defenders. Ensure that all your employees have a pair and wear them by conducting inspections and monitoring them regularly.
Always stock up on such PPE to guarantee that there’s enough even if some gets damaged.
However, in this case, you should treat PPE as a last resort—remove the risks entirely or remove any employees from the scene when using loud equipment.
It’s also wise to invest in yearly hearing checks to determine whether construction site work is starting to affect your staff’s hearing.
If it is, it’s a sign that you need to invest in ear protection more and eliminate as many noise hazards as you can.
Train your employees to recognize when they need to wear ear protection.
You can do this by teaching them OSHA’s 2-3-foot rule, which states that if you can’t hear the person standing two to three feet away from you using a normal tone of voice, the noise is over 85 dBA and protective equipment is necessary.
Slips, Trips, and Falls
Because of the constant movement at the worksite, the risk of slips and falls is exceptionally high, especially if you didn’t work on preventing potential causes.
On top of that, the terrain at the construction sites is often uneven, and many materials are around.
Often, a solution for one problem might cause another threat.
You might use floor cable covers to protect your employees from electricity, but if you don’t make the cable cover visible, your workers can easily trip and injure themselves.
The injury can be even worse if employees are manually handling equipment at the time or carrying hazardous materials.
Minor Fall Prevention
To avoid the risk of slips, trips, and falls, determine access routes and keep them clean. That way, the workers will know where they can work and walk without any risk.
You should also ensure that the access routes are on even ground. If they are not, even them out and provide sufficient lighting, so your workers have a safe walkway around the worksite.
If you’re worried about the equipment and materials lying around, make workers responsible for putting away everything they use.
For example, when they no longer need a tool, they should return it to the storage room or to a designated area, where it can’t cause accidents.
Avoiding cords is challenging, but when possible, choose cordless tools. If there’s no alternative, opt for tools with cords, but make the cables visible and ensure that they’re not in anyone’s way.
Also, you need to properly mark any wet and slippery surfaces to warn workers of potential danger and treat the areas as soon as possible to avoid accidents.
Hand Arm Vibration Syndrome (HAVS)
HAVS is a painful, debilitating disease caused by occupational exposure to vibrating tools, often used in construction.
It affects joints, nerves, and blood vessels, making it impossible for the worker to do fine work or work in colder conditions—cold triggers finger pain.
This syndrome is preventable, but it’s incurable, so it’s wise to protect your workers from its effects.
HAVS Prevention
Begin preventing HAVS by opting for non-vibrating tools whenever you can. Even if such equipment is more expensive, they pose a lot less danger to your team.
If you have to use such tools, assess the risk and determine which employees are most threatened by HAVS.
It’s important to note that workers with pre-existing conditions like diabetes and certain diseases affecting hands, arms, wrists, or shoulders are at a higher risk of this syndrome.
Before you ask such employees to handle vibrating tools, consult with a medical professional first.
Then, think of the daily exposure limit and determine which employees use such tools more than the limit.
Working with vibrating tools above the daily limit isn’t advisable, so always stick to the limit to ensure you’re protecting your workers.
For additional protection, purchase and ensure employees use protective equipment, such as anti-vibration gloves.
Also, don’t forget to invest in the equipment itself. Maintain it well to remove any risk of excessive or too powerful vibration. Worn-out or blunt tools will vibrate more.
On top of that, you should also think about the working conditions. Keep the construction site warm and dry since the opposite allows HAVS to develop.
Asbestos
Asbestos is a dangerous mineral linked with asbestosis and different cancers like mesothelioma (malignant tumor), lung, ovarian, or laryngeal cancer.
Mesothelioma is almost exclusively caused by asbestos, so the fact that around 3,000 Americans are diagnosed with it every year shows the real danger of this disease.
What’s even worse, mesothelioma’s 5-year survival rate is only 10% because it’s often diagnosed too late.
When you inhale asbestos, some of its particles can get stuck in your respiratory system, unable to get out.
Over time, with prolonged exposure, these particles cause inflammation and damage your DNA.
Because of this, no amount of asbestos exposure is acceptable.
Construction workers are the number one group at risk of asbestos exposure because the construction industry used materials containing asbestos.
Sadly, some of these materials are still used today in roofing and flooring, putting existing and future construction workers at risk.
Asbestos Exposure Prevention
Since workers can inhale asbestos, they must wear PPE to ensure that none of the particles can enter their respiratory tract.
The PPE in question should include:
- a respirator
- eye protection
- rubber boots
- disposable coveralls
- disposable gloves
After asbestos exposure, the workers have to wash all equipment and exposed skin before leaving the area.
In addition, they should throw away disposable equipment into specifically designed containers, ensuring that it doesn’t pose a threat to others.
Before allowing employees to work on an asbestos-contaminated worksite, inspect it and determine the risk of asbestos exposure.
Pinpoint the exact areas where asbestos is present to properly inform your workers of potential dangers.
Conclusion
Unfortunately, there are many hazards at a typical construction site, ranging from those less dangerous, like noise, to electricity or asbestos.
Before sending workers to any construction site, properly inspect the worksite and assess risk, considering the most common hazards mentioned here, like falls, collapses, moving objects, and HAVS.
Once you understand the risks, educate your workers to deal with and notice such hazards on time. Also, train them on the importance of PPE and ensure that they always use it.
Eliminate or lower the risks as much as possible for a safer working environment!