Asset tracking can yield a lot of data, but these findings are only truly valuable when decision-makers understand what to measure and know how to properly apply the information they’ve extracted.
The different goals and needs of each company will dictate which construction performance metrics to focus on.
Nevertheless, this post provides a strong starting point, offering information that is easily adaptable to any type of construction.
In this article...
Financial Metrics
Financial metrics reveal the economic reality of your business. They are the basic indicator of the health of any enterprise, and often act as a warning or affirmation for other metrics.
Discerning the financial health of your business entails much more than monitoring cash in vs. cash out.
Investments and the purchases of necessary equipment, for example, should be weighed against taxes, charitable giving, and seasonal income distribution.
Placing these numbers into context can help you make informed decisions about steering your enterprise.
Here are some financial metrics to take into consideration:
Profit margins | The amount of revenue a company has earned after expenses |
Cash flow | The amount of ready cash flowing in and out of a company |
Accounts Payable | All of a company’s liabilities, debts, and service purchases |
Accounts Receivable | Money owed short-term by customers or vendors |
These are just a few measures to show your company’s progress towards both short-term and long-term goals.
By tracking them over a longer period of time, it’s possible to see patterns and challenges that might lie ahead.
Consulting these numbers is especially useful when making major financial decisions, such as purchasing a major piece of machinery or opening a new branch.
Understanding financial metrics is also useful when taking a macro look at your industry.
Here, for example, is a chart from the Construction Financial Management Association, presenting the numbers gathered in a voluntary questionnaire completed by members of the construction industry:
It measures their financial data from the fiscal year 2020.
Given that nearly all companies of every trade felt the impact of the COVID-19 pandemic, this information is an invaluable resource.
It allows companies to measure their struggles, recovery, and sales against companies in the same sector in the same time frame.
Safety Metrics
Safety metrics are of great importance in the construction industry, more than in most others.
Construction work is often inherently dangerous; it involves working with heavy machinery and sometimes hazardous materials in adverse conditions, sometimes at great heights, or underground.
Keeping track of incidents, training, meetings, and compliance actions isn’t just a good idea—it’s often the law.
The Occupational Safety and Health Administration (OSHA) not only sets the safety standards for construction sites, it enforces these policies as well. OSHA conducts inspections, investigates accidents, and levies penalties for code violations.
This process involves data collection from companies that have more than ten employees in high-risk categories. These employers must submit records about serious illnesses and work-related injuries that occur in their companies.
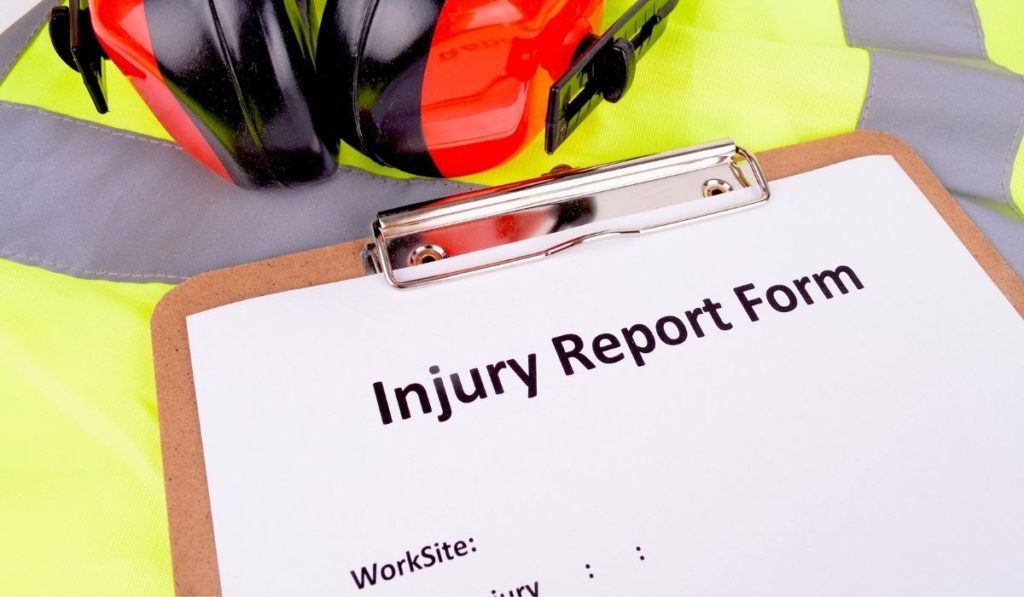
Federal regulations require them to publicly post this information as well.
In addition to these federal requirements, many companies, particularly smaller ones not covered by OSHA laws, must take care to comply with local and state codes as well.
The ability to automatically track and permanently store this information, along with the best practices for safety inspections, saves a great deal of time and money.
However, monitoring incidents and their occurrence is only the starting point of smart safety tracking in construction.
For example, time lost due to accidents is common in this industry.
Studying visual comparisons of this information against time spent in training, seasonal changes, job type, and hours on the job can yield valuable data about preventing future injuries and employee downtime.
A strong workplace safety culture is never a matter of just one measure or action. It’s an outcome of many different factors, and in order to gain an accurate picture of these, it’s important to track several data points.
Here, the Predictive Solutions Corporation uses this graphic to illustrate the importance of compiling and studying data from safety inspections and observations.
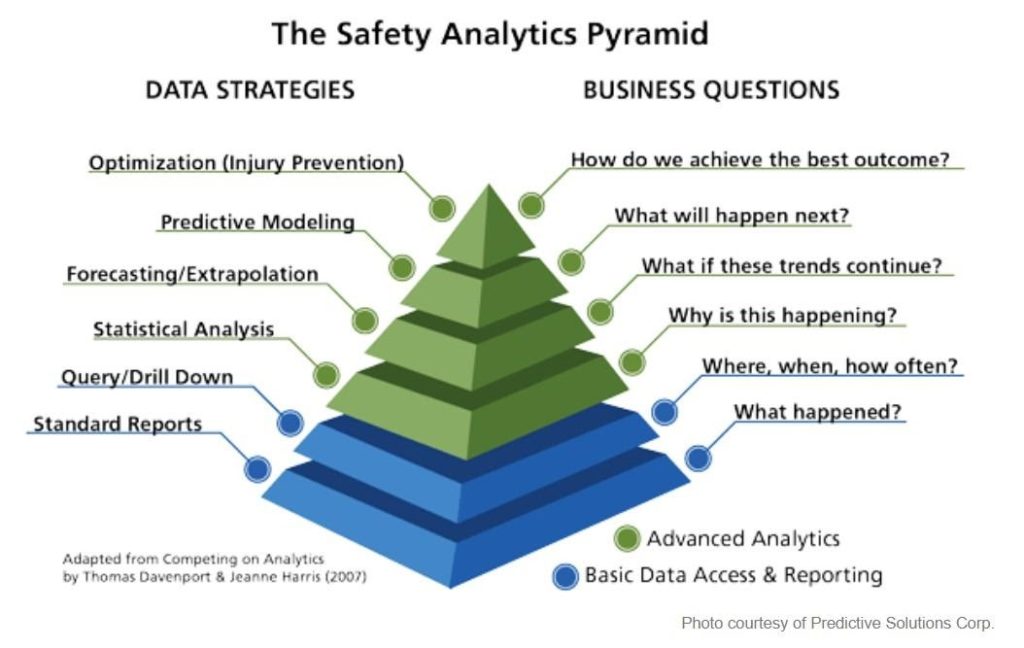
As you can see, the combination of raw data, analysis, and collection of employee input is vital to preventing accidents and leads to achieving better safety on site.
Work Quality Metrics
In construction, clients usually measure quality against speed. However, safety, scheduling, cost of materials, rework costs, and customer satisfaction all play a role in quality control and measuring.
Similarly, work quality metrics do more than merely calculate the amount of output from employees. Focusing on quantity alone runs the danger of ignoring quality, or how employees performed the job.
This quality control plan from Redbuilts shows how planning, material costs, feedback, safety measures, and procurement all play a role in work quality:
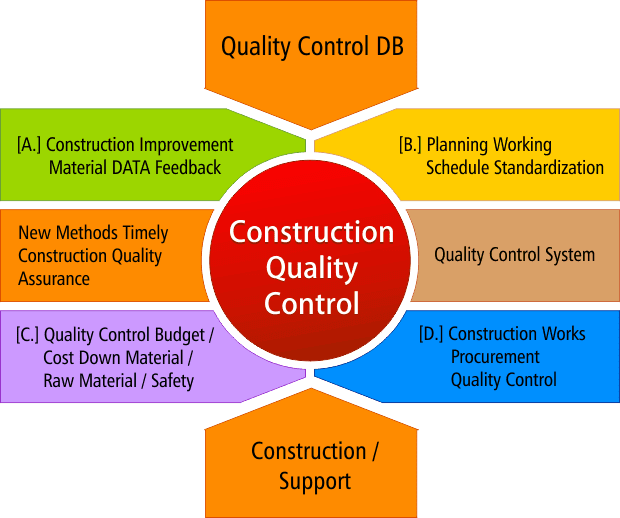
Combining these data streams can allow project managers and contractors to adjust goals and timelines as necessary.
Construction hinges on a physical deliverable: a house, a graded lot, or a new road. With this in mind, it does a company little good to quickly and inexpensively complete a bridge, for example, if it is unstable and prone to collapse.
However, on the other hand, clients will not take kindly to waiting ten years for the completion of a building, no matter how solidly the company ends up building it.
The answer seems to balance speed and quantity with work quality.
Work quality takes into account the full picture of the employee and the tasks he or she faces.
These criteria can include the amount of time they have spent with the company, specific goal matching, personality type, predicted potential, and task engagement.
Completion rates, error amounts, and inspection flags can also become part of a work quality metric.
Sometimes, pairing work quality with safety numbers or other data can yield vital information.
For instance, if employees are making many mistakes, engage in bad decision making, or become less effective, the cause could be a multitude of issues.
When was the last time these employees received a safety briefing? Do their team assessments show trust in their supervisor?
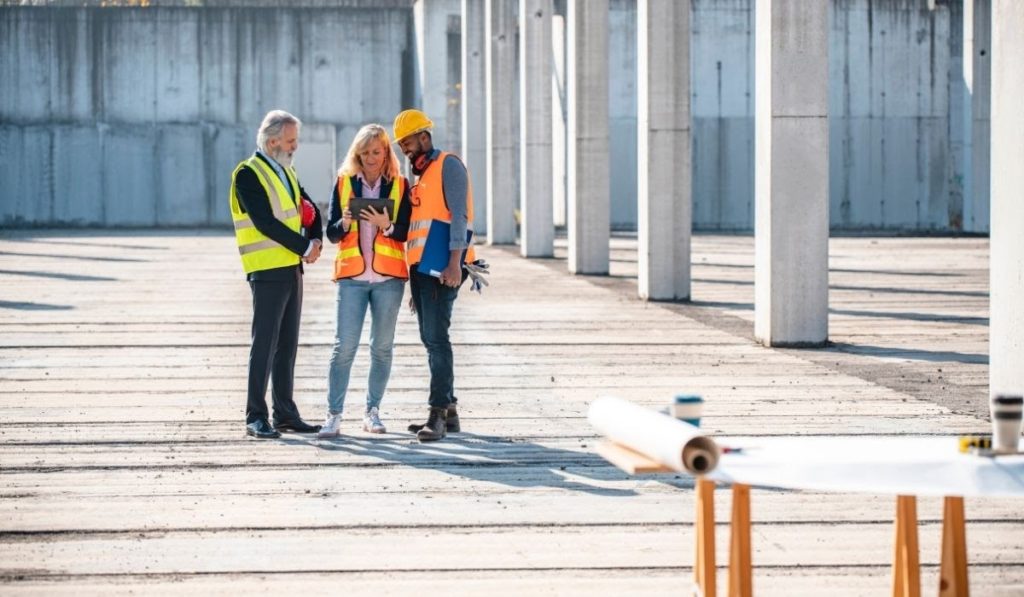
Are they taking directed breaks to allow mental and physical rest? Has there been an illness outbreak? Is the technology they are using recent and working correctly?
Metrics can provide these answers and reveal solutions in surprising places.
Team Performance Metrics
Team performance metrics can indicate how well the mixing and matching of employees works, as well as the feasibility of different challenges for stable teams.
For instance, possibly due to staff shortages, supply chain issues, and other challenges, in the UK, construction companies are more concerned with meeting immediate financial objectives than any other tangible factors, including inadequate budgets.
The lack of focus on long-term stability, team building, or commitment to flexible resilience to financial challenges is worrying for a leading-indicator industry like construction.
Companies can begin to look beyond the short-term by keeping an eye on these performance metrics:
- Amount of waste per job
- Percentage of downtime due to equipment malfunction
- Per-hour revenue
- Resource failures
Looking at this information can give employers an idea of how company practices are working on a micro-level.
For example, if your analysis reveals a large amount of waste, it’s vital to dig into why it’s occurring—is it lack of training, substandard materials, or unreasonable timelines?
Placing this data into context with the full input of employees and a close look at the supply change is a beneficial use of this information.
Some performance metrics can result in new business opportunities. Have a look at this statistic about construction recycling from BigRentz:
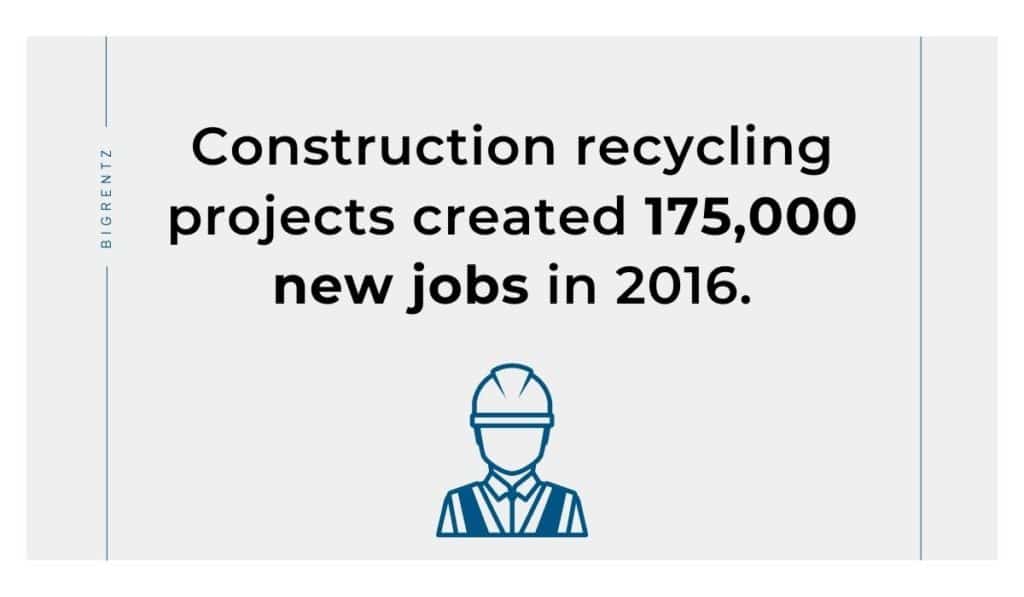
These entrepreneurs, while studying debris and garbage removal, saw that much of this material was eligible for recycling or repurposing. They turned this information into new jobs.
One metric which employers should not overlook is equipment downtime. Unusually high amounts of downtime signal the need for better tool tracking, preventive maintenance, or equipment updates.
Understanding what employees truly need, and why, constitutes the first step in applying team performance metrics.
In addition, if workers were constantly running short of supplies, or if raw materials were inefficiently placed, it’s a good idea to reconsider the way these assets are directed across worksites.
For instance, performance metrics can reveal the need for a more nimble and flexible supply system. The answer may lie in GPS tracking, employee swing shifts, or better communication between office dispatches and staff in the field.
Employee Satisfaction
Employees who feel valued and satisfied in their work can contribute to a safer, healthier environment. Satisfied employees feel invested in their jobs and the company.
In fact, the safest workplaces are those in which non-safety employees are keeping watch for violations while demonstrating and promoting good practices.
One potential danger of low employee satisfaction is a high turnover rate.
If employees are departing for other opportunities after only a few months, ask yourself if these departures are pegged to a single supervisor, task, or job site.
Parsing this information can provide suggestions about causes and potential solutions.
Here are some factors to consider when measuring employee satisfaction in construction:
- Strong communication level between management and workforce
- Attention to safety
- Meaningful work
- Fair pay and benefits
- Strong social connections
- Opportunity for advancement, if desired
- Employee expectations from management
Overall, construction workers are among the happiest employees in the US. Why?
Since most construction jobs involve a high degree of responsibility, workers experience a feeling of accomplishment. Job tasks may change quite often, preventing mental fatigue.
These employees are also often free of most annoyances that plague employees that work indoors, such as office politics and the resulting drama, frustrating meetings, and boredom.
They are generally focused on measurable tasks, rather than dwelling on excessive self-contemplation or points of psychological grievance.
So what else can you do to make sure your employees are happy?
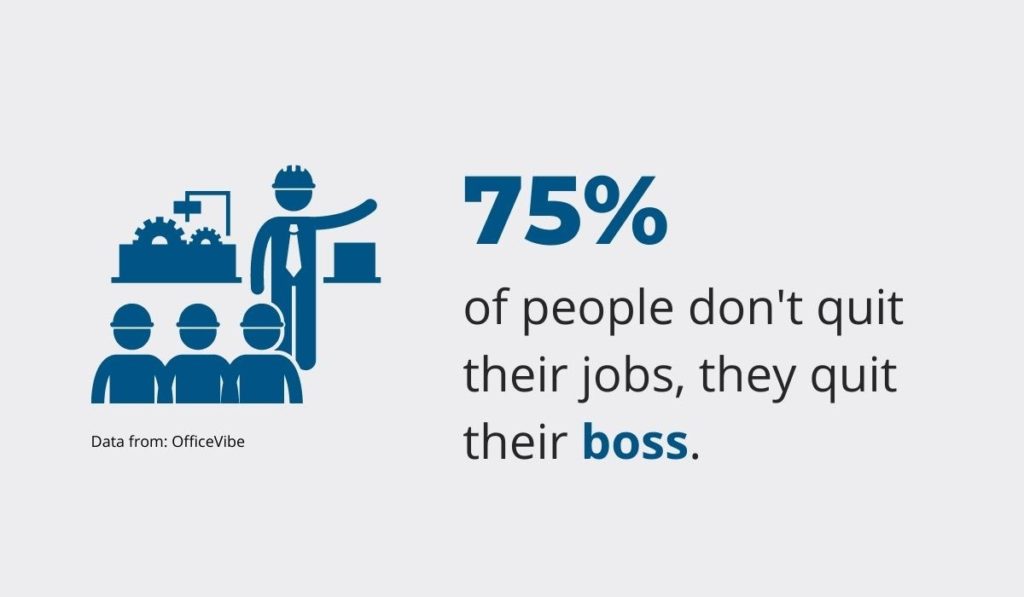
One of the most important things is to provide your workforce with a supervisor who is not necessarily well-liked, but is well-respected.
Employees feel most inspired by those who lead by example, display strong interpersonal skills, show consistent honesty, and pitch in where needed.
Like everything else in construction, the elements of employee satisfaction can shift depending on the environment, level of engagement, and work-life balance.
Aiming for high employee satisfaction, however, saves training costs, establishes a stable workforce, inspires client confidence, and improves relationships across the entire company.
Conclusion
It is useful for employers to combine data streams and track metrics to obtain a broader picture of the direction of the company.
Monitoring financial realities, safety, work quality, team performance, and employee satisfaction are all vital in meeting short-term and long-term goals.