Key Takeaways:
- Proper acquisition balances cost and quality for long-term value.
- Preventive maintenance cuts emergency repair costs by 3–10 times.
- Disposal planning at purchase improves sustainability and reduces waste.
- Asset tracking software improves visibility, reduces loss, and optimizes utilization.
Did you know that in 2018, aging assets were responsible for 44% of unscheduled downtime in manufacturing?
That’s definitely a costly problem—one that proper asset life cycle management can help prevent.
Every asset goes through a life cycle, from acquisition to disposal, and managing each stage effectively can mean the difference between healthy assets/efficient operations and unexpected breakdowns.
In this guide, we’ll explore the asset life cycle, how to manage the five stages, and what benefits you can yield from it.
Let’s dive in.
In this article...
What Is the Asset Life Cycle?
Think about the heavy equipment on your job sites, the fleet of trucks delivering materials, or even the IT systems running your business.
Every asset—whether a bulldozer, a generator, or a software platform—has a life cycle.
From the moment you acquire it to the day it’s retired, that asset goes through different stages outlined below:
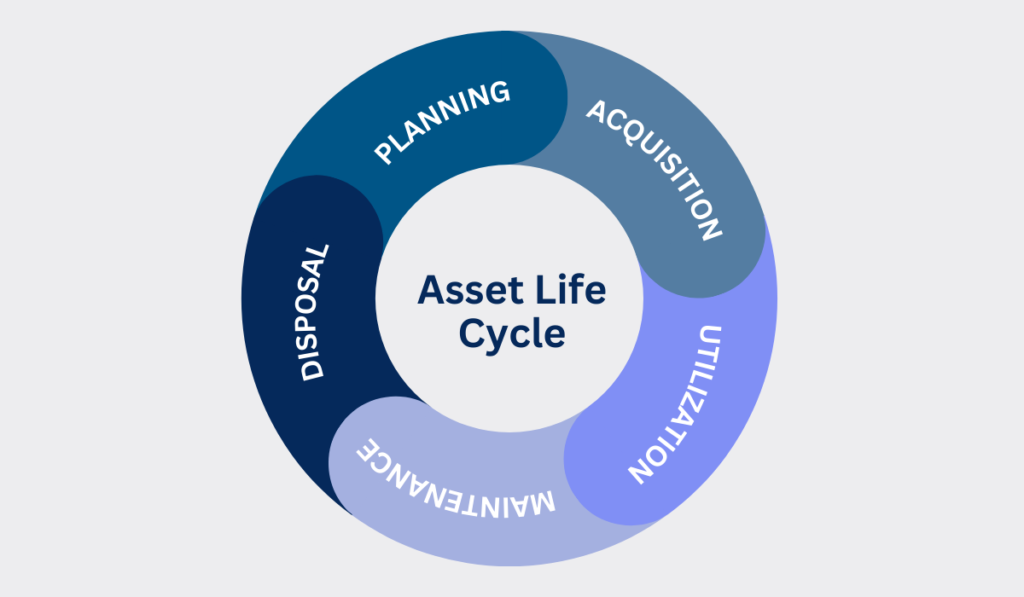
Source: GoCodes Asset Tracking
How well you manage each phase determines whether your equipment remains a valuable investment or turns into an expensive liability.
This is where asset life cycle management (ALM) comes in.
ALM is a strategy to optimize each stage, so the assets perform efficiently for as long as possible.
A strong ALM ensures your assets last longer and don’t drain your budget with unexpected breakdowns.
And when you get it right?
You minimize downtime, control costs, and keep your operations efficient, as we will explain later in more detail.
The 5 Stages of the Asset Life Cycle
Managing assets properly demands the understanding of the journey they take—from the moment you acquire them to the day they’re retired.
This journey goes through the five stages we will now break down.
1. Planning
Every great investment starts with a plan.
Whether you’re acquiring heavy machinery, fleet vehicles, tools, or IT systems, you need to think ahead.
Ask yourself:
- What do you need?
- Why do you need it?
- How will it fit into your operations?
Usually, organizations start by analyzing demand, considering how the asset will contribute to productivity, efficiency, or cost savings.
Naturally, budgeting is an important factor here.
But instead of just thinking about the purchase price, it’s important to also include other costs in estimations, including maintenance, fuel, insurance, depreciation, and eventual disposal.
In other words, at the planning stage, you should already consider the total cost of ownership for each asset you plan to buy.
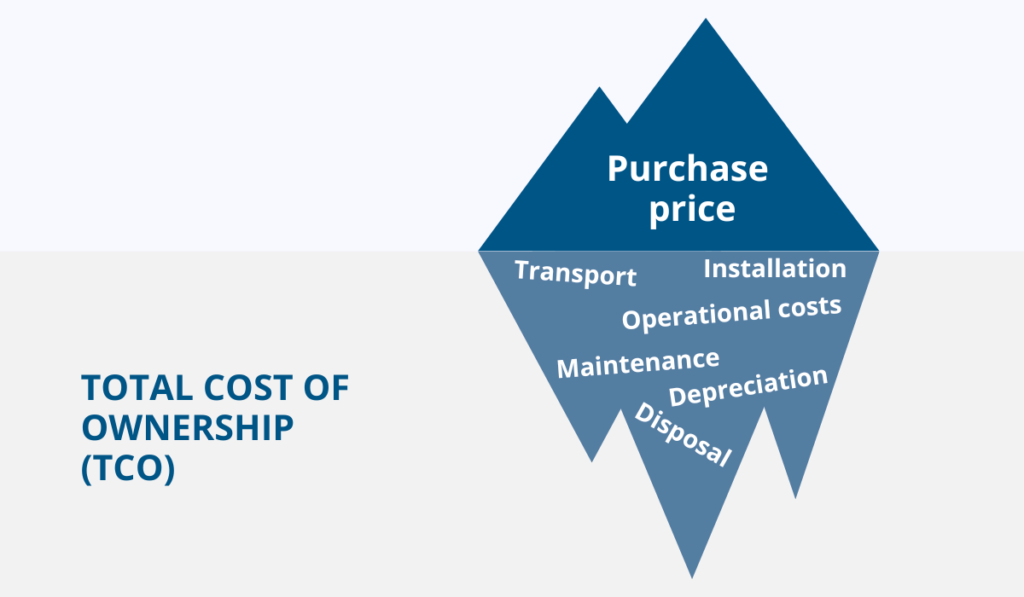
Illustration: GoCodes Asset Tracking
A well-thought-out cost-benefit analysis will help you avoid investments that may become financial burdens over time.
At this point, you should also consult with the employees who will use the asset to ensure that the investment aligns with actual workplace needs.
In the planning stage, companies also define performance metrics and set key indicators to measure whether the asset will deliver the expected return on investment (ROI).
With a strong plan in place, the next step is acquiring the asset.
2. Acquisition
Once an asset is approved for purchase, the focus shifts from planning to action.
Selecting the right vendor, negotiating terms, and ensuring the asset meets the organization’s standards are all important at this stage.
But the biggest challenge is balancing cost and quality.
David Rudge, professor at Western Michigan University, gives a simple example on Quora:
“Let’s assume you are an adult and need to purchase a pair of shoes that you plan to wear every day. You might be better off purchasing a more expensive pair that is of high quality (i.e., it will last longer) than purchasing the cheapest pair, knowing that you will regularly have to replace them.”
The same logic applies to other assets.
The cheapest option may seem budget-friendly upfront, but if it’s unreliable or costly to maintain, it could drain your finances in the long run.
Beyond the purchase, this stage includes logistics such as shipping, installation, and integration into existing systems.
Setting up the asset correctly ensures that it operates at peak performance from day one.
Training employees on its proper use is equally important, as improper handling can lead to premature wear and tear, unexpected breakdowns, and higher safety risks.
Once the asset is fully operational, it enters its longest and most active phase—utilization.
3. Utilization
This is where your asset starts proving its worth. It’s in daily operation, contributing to your business.
But simply using an asset isn’t enough—you need to track performance and optimize its use.
What’s the easiest way to do that than with the right tools?
With asset tracking software like our GoCodes Asset Tracking, you attach QR-coded labels to your assets and store all asset data in one place, including usage history and maintenance records.
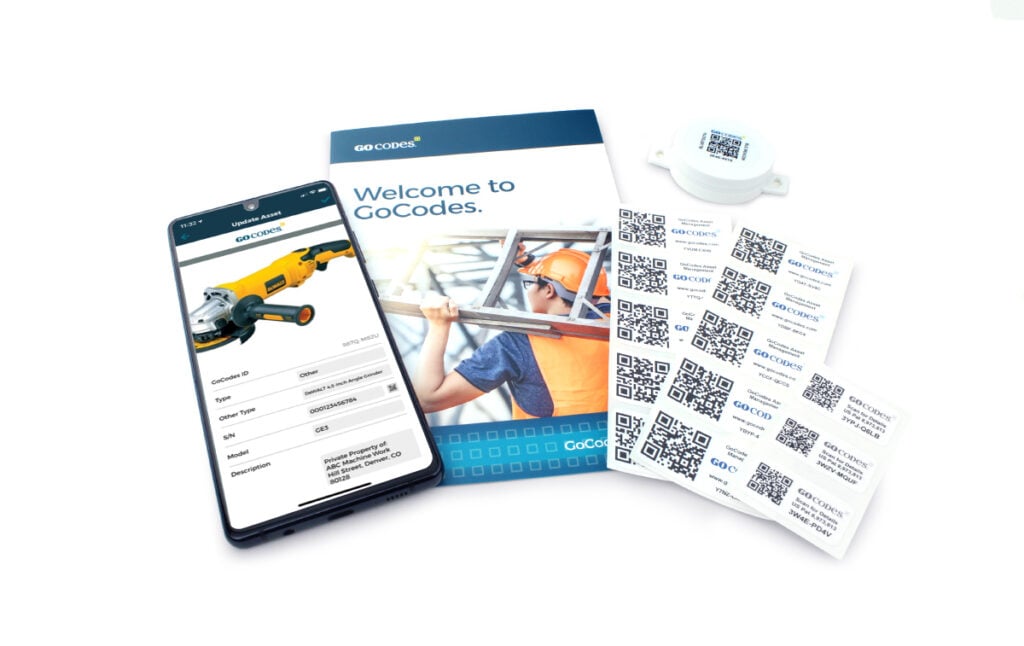
Source: GoCodes Asset Tracking
Every time your employees scan an asset with their smartphones, the system will detect the asset’s location.
They can easily scan assets in and out, and you will have all the information on asset usage right there in the system.
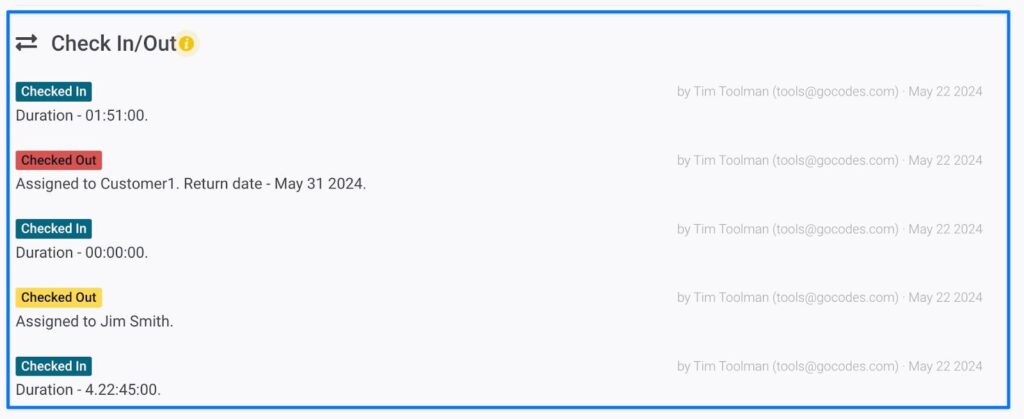
Source: GoCodes Asset Tracking
And for your most valuable assets, GoCodes Asset Tracking offers real-time GPS trackers, helping you combat asset loss and improve fleet management.
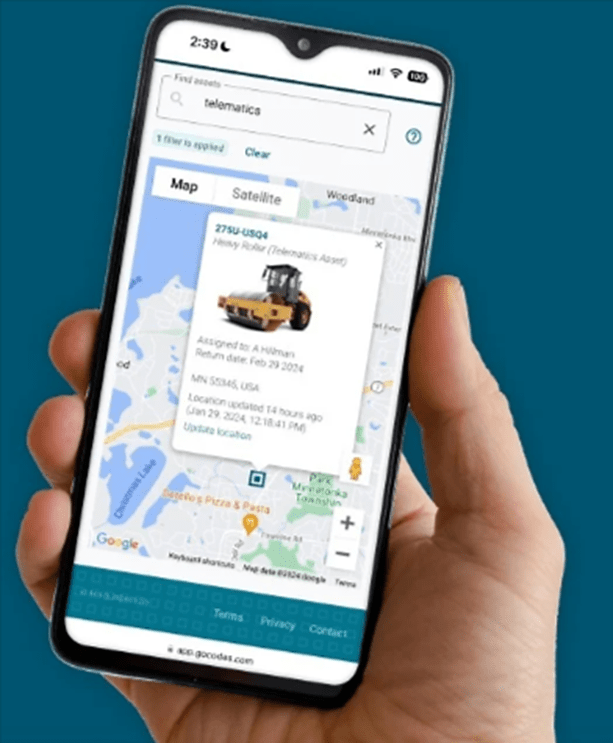
Source: GoCodes Asset Tracking
With all these capabilities of asset tracking systems, you can extend the utilization phase and get the most value from an asset.
Preventive maintenance, careful observation, and following manufacturer guidelines all contribute to prolonging its lifespan—and are easily achieved with asset tracking software.
Eventually, however, every asset needs servicing, which brings us to the maintenance stage.
4. Maintenance
This stage includes both scheduled preventive maintenance and unexpected repairs.
Maintenance activities vary depending on the asset.
For some, this might involve routine servicing such as changing filters, lubricating components, or replacing worn-out parts.
For others, it could mean software updates, deep cleaning, or even upgrading outdated technology.
At times, temporary downtime is required for significant repairs, such as replacing a key component, modernizing old machinery, or installing additional features.
Proper maintenance and utilization go hand in hand.
If a company consistently tracks asset usage, the maintenance team can use that data to anticipate issues before they become major problems.
Plus, scheduling maintenance is easy with asset tracking software.
In GoCodes Asset Tracking, for example, you can schedule preventive maintenance tasks—such as oil changes, part replacements, and inspections—in just a few clicks:
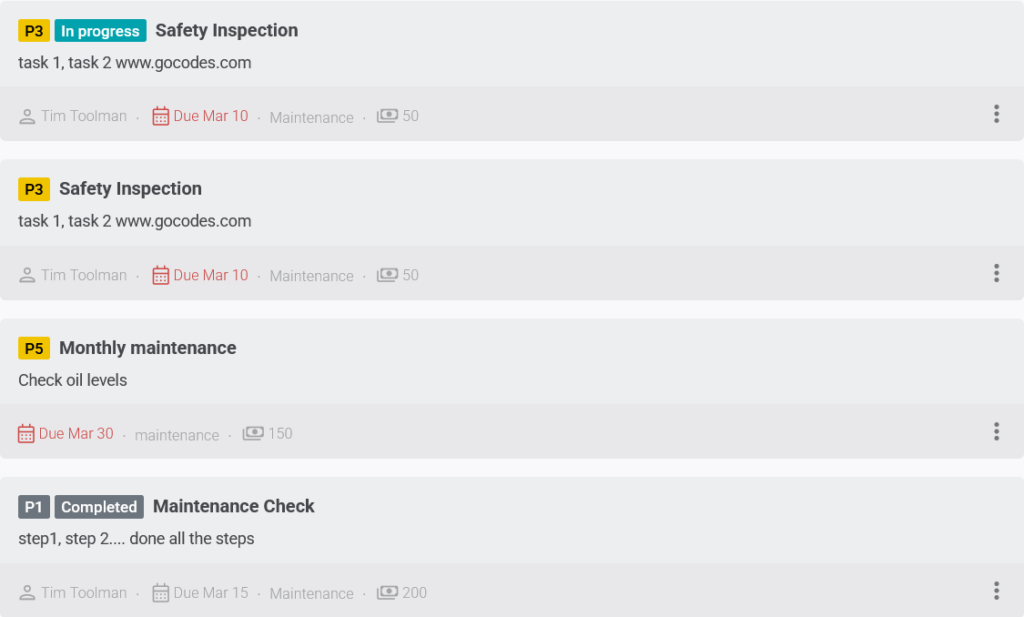
Source: GoCodes Asset Tracking
If maintenance is done properly and on time, this stage in the asset life cycle will do most to minimize asset downtime, extend its lifespan, and ensure consistent performance.
Beyond improving efficiency, proper maintenance is a critical factor in workplace safety.
Research from WorkNest found that among 200 “wholly avoidable” workplace incidents, the third most common root cause—accounting for 8% of cases—was a lack of machine guarding or maintenance.
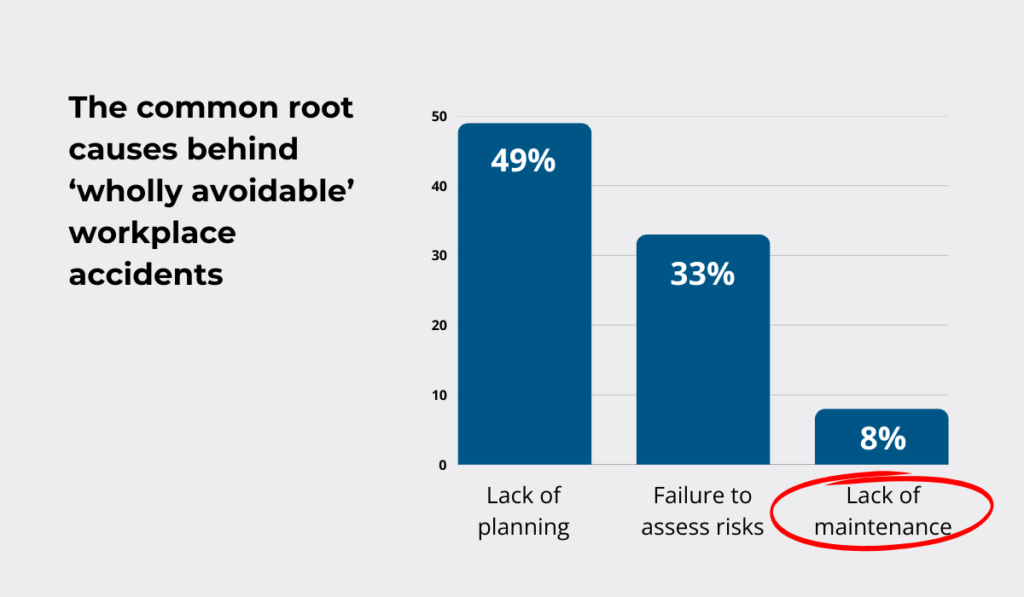
Illustration: GoCodes Asset Tracking / Data: WorkNest
So, neglecting maintenance doesn’t just lead to equipment failures, but it also puts employees at risk.
Still, no matter how well you maintain an asset, there comes a point when it’s no longer worth fixing.
That’s when it’s time for the final stage—disposal.
5. Disposal
When assets become unreliable, slow down productivity, or require excessive maintenance, businesses need to consider whether holding onto them is still worthwhile.
Frequent breakdowns can lead to downtime, which not only affects operations but also increases costs.
If replacement costs seem high, companies should calculate how much time and money they are already losing due to inefficiencies.
In many cases, investing in new equipment can prove more cost-effective in the long run.
Proper disposal is especially important for IT assets, as improper handling can lead to environmental, legal, and regulatory risks.
Yet, according to a Capterra survey, nearly a third of small and midsized businesses admitted to discarding old electronics rather than recycling or repurposing them.
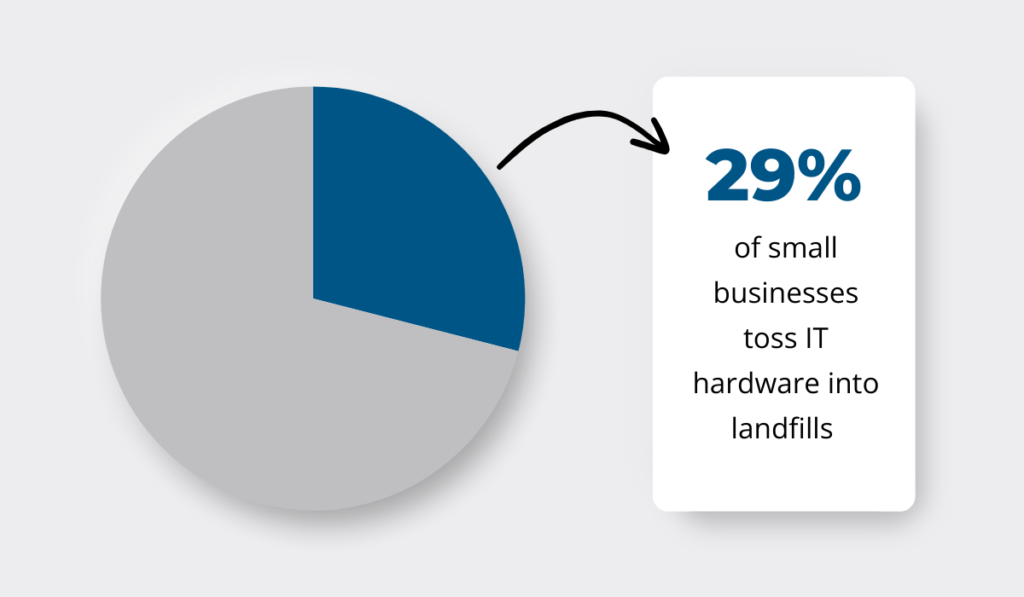
Illustration: GoCodes Asset Tracking / Data: Capterra
Zach Capers, senior security analyst at Capterra, warns that this practice carries serious consequences:
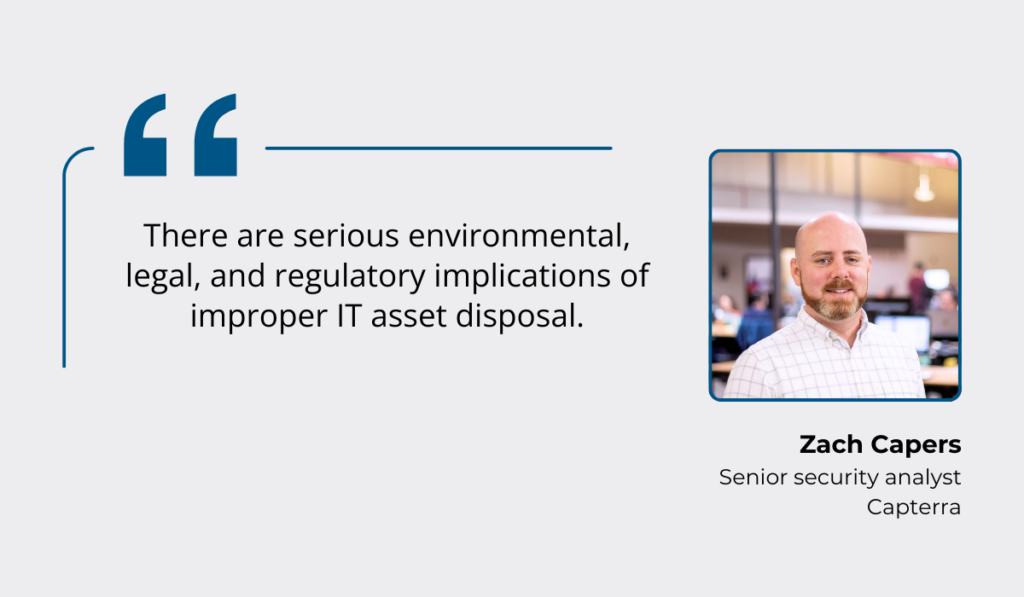
Illustration: GoCodes Asset Tracking / Quote: Business Wire
Businesses should prioritize responsible decommissioning methods such as recycling, repurposing, or donating old IT equipment instead of sending it to a landfill.
For other types of assets, sustainability considerations can also play a role in disposal decisions.
Some equipment is easier to recycle than others.
Resin-type transformers, for example, are designed with inert materials that make disposal more environmentally friendly, and their windings can be easily recycled.
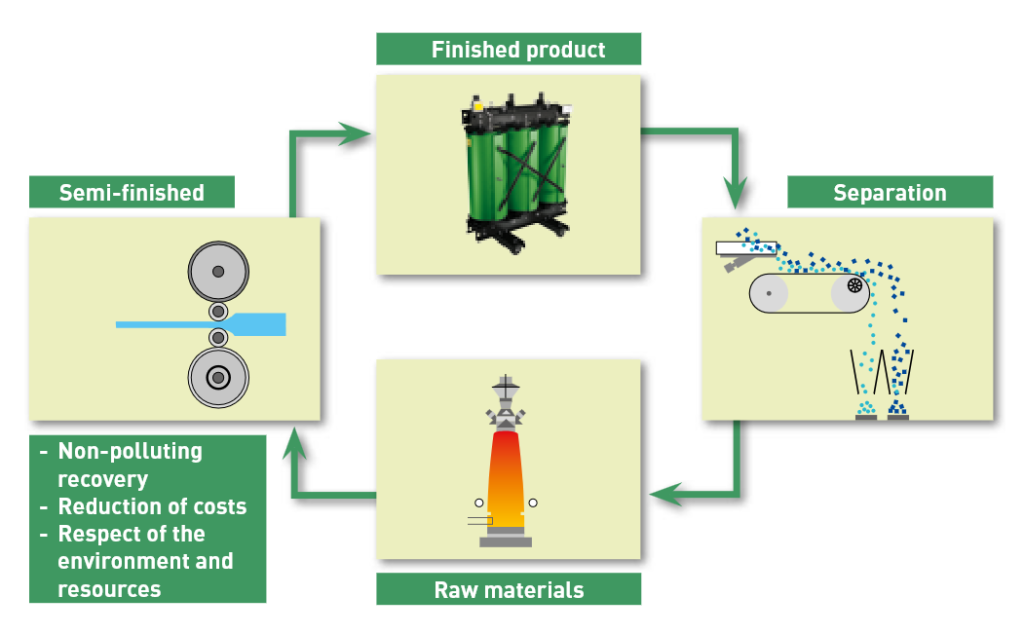
Source: BTicino
Planning for an asset’s eventual disposal even before purchasing it can lead to better long-term sustainability decisions, ensuring that future investments align with environmental and cost-saving goals.
At the end of the life cycle, the process begins again.
By carefully planning for disposal and replacement, businesses can seamlessly transition to acquiring new assets that are more efficient, cost-effective, and environmentally responsible.
Key Benefits of Asset Life Cycle Management
Now that you know what stages every asset goes through, let’s see what benefits await you if you properly manage its life cycle.
Cost Savings
Unexpected asset breakdowns and emergency repairs are some of the biggest cost drivers in asset-heavy industries.
Emergency repairs, for example, cost between three and ten times more than a good maintenance program, says David Auton, senior director of reliability engineering for Cushman & Wakefield:
“Run to fail or repair easily costs somewhere between three and ten times as much as a good maintenance program. When the equipment does fail, the actual repair costs are exorbitant, and you typically didn’t plan for them, so there’s a financial issue.”
But when a critical piece of equipment suddenly fails, it’s not just the repair bill that hurts—it’s also the ripple effect of lost production, idle workers, and project delays.
All this costs money.
Or consider this.
Aging equipment was responsible for 44% of unscheduled downtime in manufacturing in 2018, making it a leading cause of lost efficiency.

Illustration: GoCodes Asset Tracking / Data: Plant Engineering
Apparently, many companies hold on to outdated assets far longer than they should, leading to prolonged downtime and excessive spending on repairs instead of investing in newer, more reliable technology.
And not to mention the financial impact of asset downtime.
A study by Siemens found that one hour of unplanned downtime costs $36,000 in the fast-moving consumer goods sector, while in the automotive industry, that number soars to $2.3 million per hour, over $600 per second.
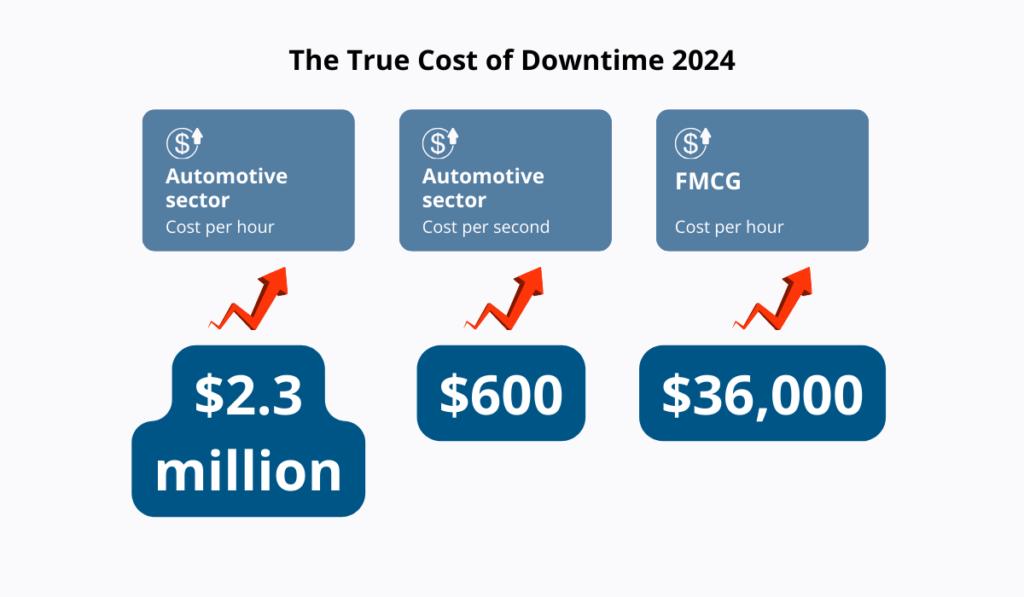
Illustration: GoCodes Asset Tracking / Data: Siemens
Asset life cycle management helps prevent these losses by focusing on proactive maintenance and knowing when to retire outdated assets.
Instead of waiting for failures, businesses can track asset conditions, schedule timely repairs, and extend equipment life where it makes financial sense.
But just as important, they can identify when an asset has become more of a liability than an asset, helping them avoid costly, last-minute breakdowns.
Additionally, by properly managing an asset through its life cycle, companies make sure they aren’t wasting money on premature replacements or over-purchasing assets they don’t need, leading to more strategic capital investments.
Longer Asset Lifespan
Equipment is a major investment, and businesses naturally want to get the most value out of their assets before replacing them.
The key?
Using them correctly and maintaining them on schedule.
Preventive maintenance plays a massive role in this, reducing wear and tear and helping companies extend asset lifespans instead of replacing equipment too soon.
It’s a priority for many businesses.
In fact, 83% of companies are actively working to extend asset lifespans with preventive maintenance, according to recent research.
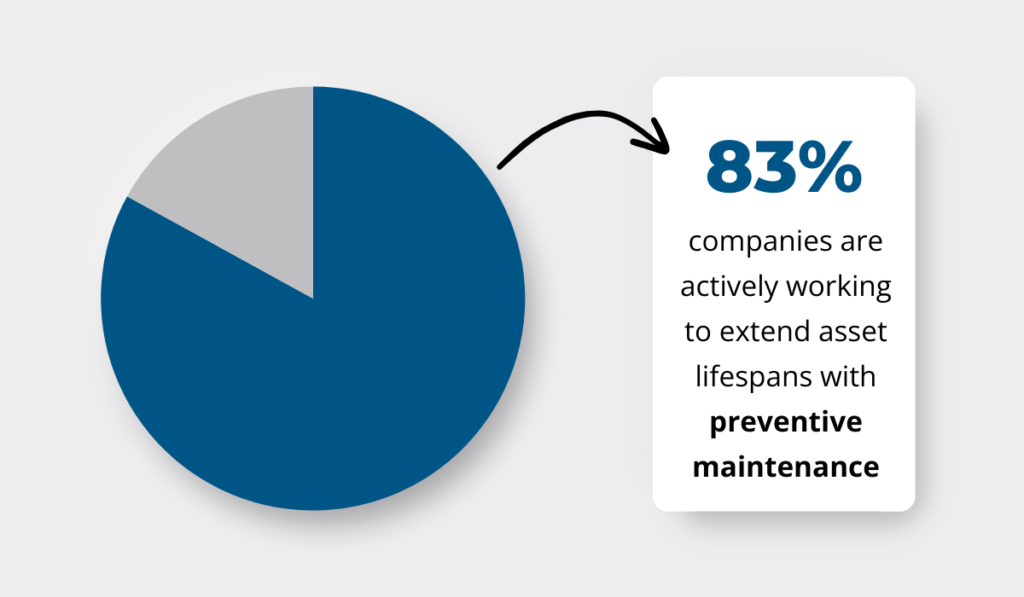
Illustration: GoCodes Asset Tracking / Data: Limble
But asset maintenance isn’t the only longevity enabler.
An important part of asset life cycle management is also proper resource allocation.
In other words, using assets optimally throughout their life cycle so they aren’t overworked, underutilized, or mismanaged.
Strong asset life cycle management ensures that businesses always know where their assets are, how they’re being used, and when they need servicing or replacement, leading to smarter decisions and maximum value.
Increased Operational Efficiency
You’re on a construction site.
A piece of heavy machinery breaks down unexpectedly, leaving the entire crew standing around, unable to move forward.
The project falls behind schedule, labor hours are wasted, and costs start piling up.
So, what’s the plan?
As David Auton puts it:
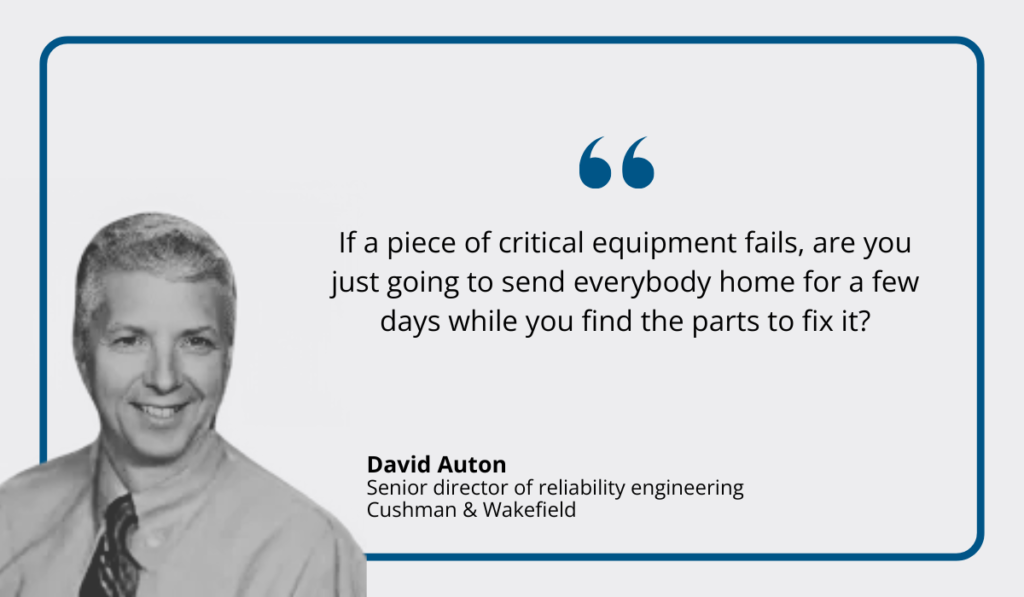
Illustration: GoCodes Asset Tracking / Quote: Buildings
Beyond being inconvenient, such situations are a major business risk.
And they happen far too often across industries.
According to an ABB study, 69% of plants experience unplanned outages at least once a month.
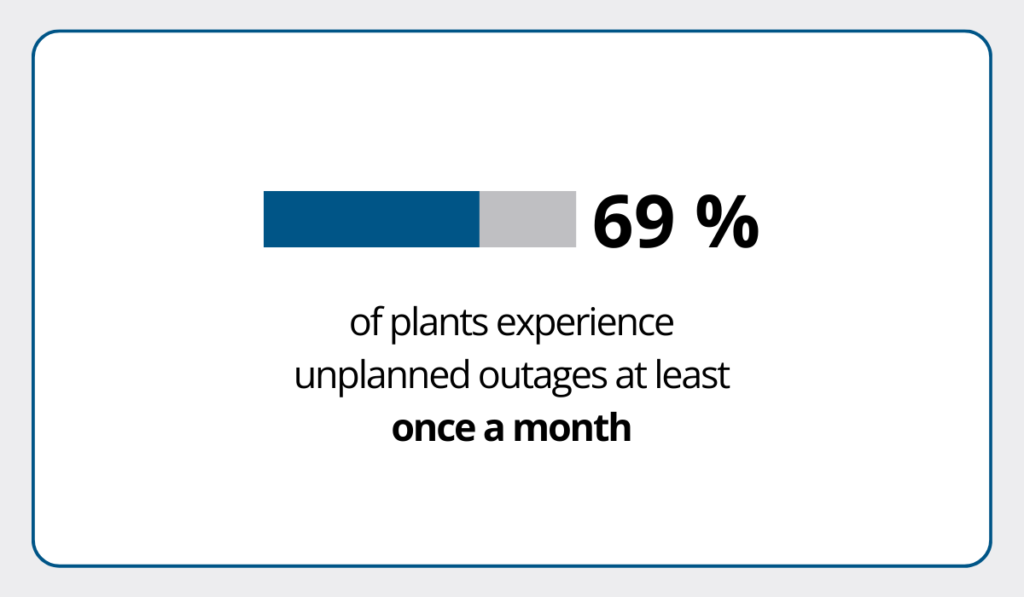
Illustration: GoCodes Asset Tracking / Data: ABB
That’s why leading companies don’t leave asset reliability to chance.
With proper life cycle management, teams know exactly when to service equipment, replace parts, and schedule downtime without disrupting operations.
Nick Howell, president of T&N Asphalt Services, has seen firsthand how this improves efficiency:
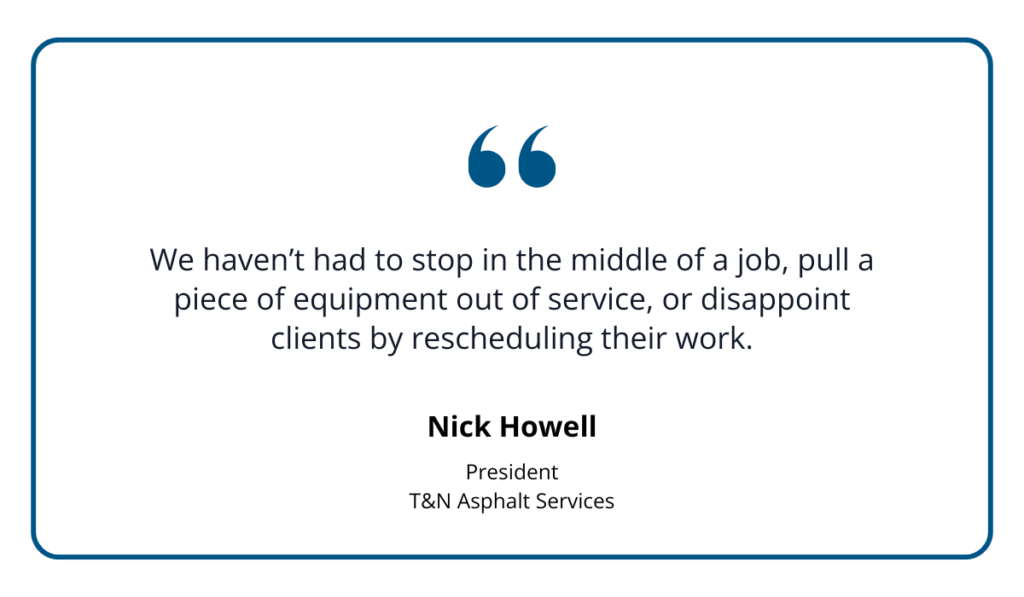
Illustration: GoCodes Asset Tracking / Quote: For Construction Pros
The benefits go beyond just preventing downtime and disappointing clients.
A well-structured asset life cycle plan also helps companies optimize resource allocation, ensuring that the right equipment is in the right place at the right time.
Instead of assets sitting idle or being overworked, businesses can maximize utilization and keep assets running at peak efficiency.
How Technology Enhances Asset Life Cycle
Now, all these benefits would hardly be realized without the right technology.
Managing an asset’s life cycle—from acquisition to disposal—requires constant tracking, timely maintenance, and data-driven decision-making.
But relying on outdated methods, like spreadsheets or manual logs, often leads to inefficiencies, unexpected failures, and wasted resources.
That’s where modern technology comes in.
Asset tracking systems, predictive maintenance, and automated workflows help businesses monitor asset health, prevent breakdowns, and optimize usage.
Deloitte’s research highlights just how much impact these solutions can have:
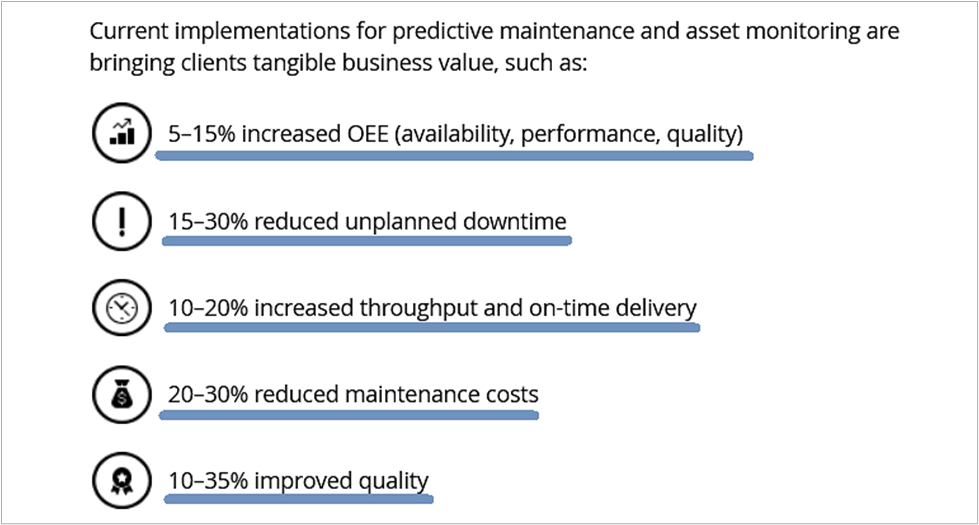
Source: Deloitte
Much of this relies on cloud-based platforms and mobile apps, which make asset management accessible anytime, anywhere.
Throughout the asset life cycle, these tools:
- Improve acquisition decisions by providing a complete view of asset needs, costs, and expected lifespan.
- Enhance utilization by tracking location, condition, and performance in real time.
- Simplify maintenance with automated scheduling and instant access to service histories.
- Streamline disposal by recording depreciation, repair costs, and regulatory compliance data.
So, with the right technology in place, you can ensure your assets last longer and deliver maximum value throughout their life cycle.
Conclusion
Every asset has a life cycle—how well you manage it determines its value.
Will your equipment run efficiently for years, or will unexpected breakdowns drain your budget?
The answer depends on the strategy and technology you put in place.
By tracking assets, scheduling maintenance, and leveraging data-driven insights, you can reduce costs, extend asset lifespans, and keep your projects on track.
So, take control of your assets and turn them into long-term investments, not unexpected liabilities.