Once you purchase a machine, it’s in your best interest to keep it functional and effective for as long as possible.
However, this can be a challenge.
Since heavy equipment is often used in harsh conditions, it can easily malfunction if not properly cared for.
Each machine requires a specific maintenance regime, but there are still some general practices you can implement to ensure your equipment performs well.
In this article, you will learn which methods you can apply to your equipment preventive maintenance so your machines can keep bringing value to your company.
In this article...
Clean Your Equipment Often
You probably clean your handheld tools regularly because you’re aware that a buildup of dirt interferes with their functionality.
The same applies to heavy-duty equipment, but because of its size, we tend to underestimate the amount of dirt on it.
Still, if you don’t clean it properly, your equipment will suffer from a buildup of hard-to-remove coatings. Here is a list of substances you have to stop from accumulating through regular cleaning:
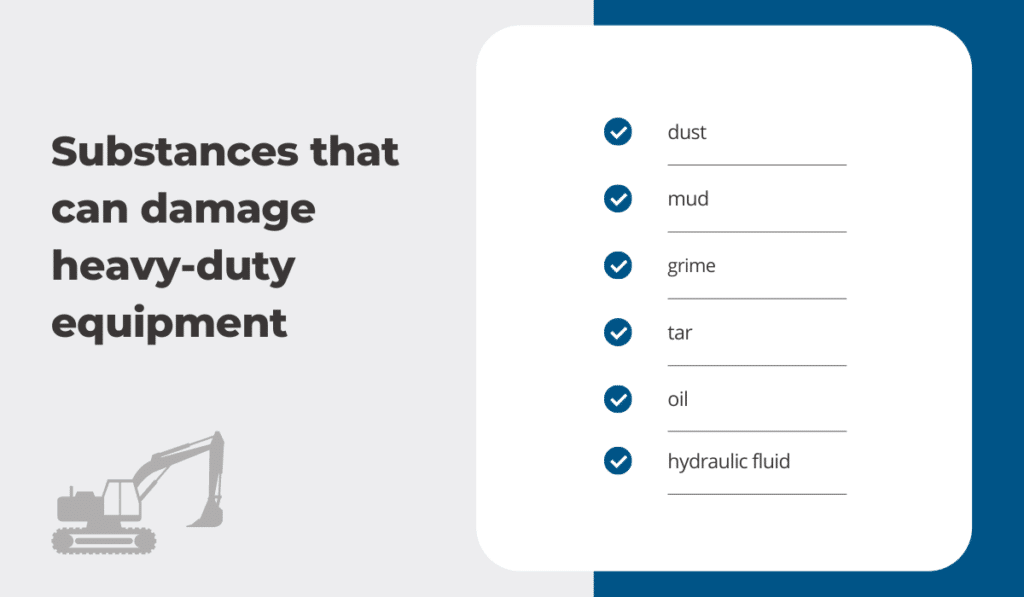
Additionally, since heavy equipment is almost always used outside, sun, rain, and wind will cake the coatings, making the cleaning process even more difficult.
What is more, when there is caked dirt on the machines, they might overheat. Also, if the accumulated dirt gets into bearings or seals, you’re risking damaging your equipment severely.
And while buying a new saw is not that big of a deal, getting a new excavator might be. This is why you have to make regular cleaning a priority in heavy equipment care.
Acting preventatively and maintaining the cleanliness of equipment is simpler than wasting hours and hours on scrubbing and abrading when the damage is already done.
An additional benefit of regular cleaning is that you can use it as an opportunity to inspect your equipment and see if everything looks the way it should. To learn how to do that, you can find our guide to heavy equipment inspections here.
Monitor Fluid Levels
If you’ve operated forklift trucks, backhoes, or other machines that rely on hydraulics, you know what happens when hydraulic oil levels get too low.
First, you’ll hear an unusual noise; then, your machines will start operating slower because there isn’t enough lubrication for the moving parts. At that point, workers will usually gather to inspect the problem, and all operations stop.
And in construction, downtime directly translates to lost business. In 2020, 57% of construction companies that experienced frequent downtime lost business as a repercussion.
To keep your machines up and running, make monitoring fluid levels your habit. After all, these, particularly exhaust fluid, engine and transmission oil, hydraulic fluid, and coolant can be considered your machine’s lifeblood.
So, what steps can you take to keep your fluids at optimal levels?
Start by reading the manufacturer’s manual to see how much fluid a machine needs. Low fluid levels are dangerous, but so is too much of it.
Next, always use recommended or specialized fluids.
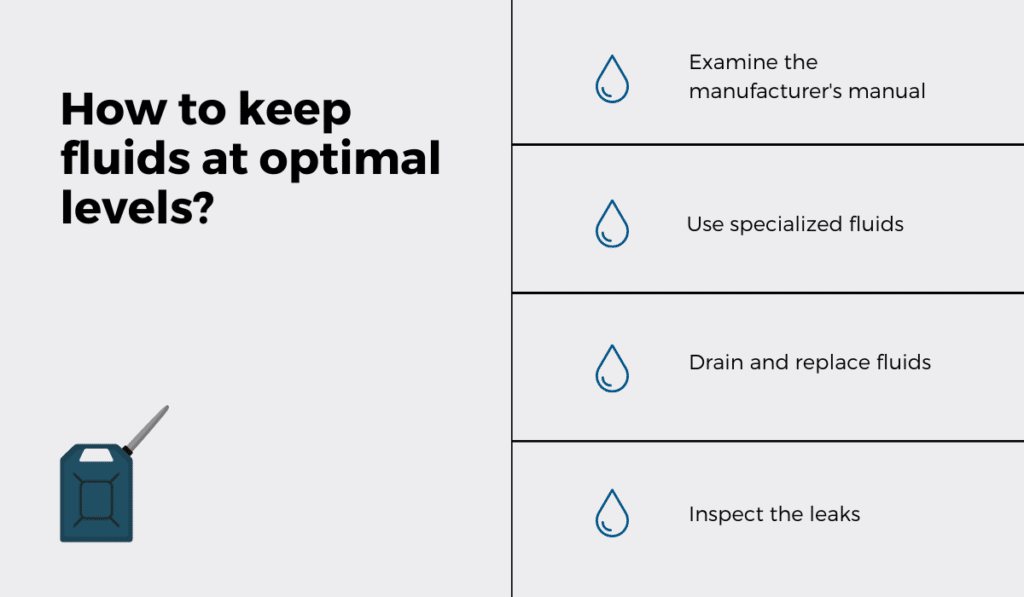
While some believe you can only use a specific brand of oil to maintain the warranty, that’s not always the case. What you should do is check the owner’s manual for each machine you own and see which type of fluid you need, not the brand.
When you buy the recommended fluid, store any leftovers in clearly labeled containers to prevent mixups.
However, don’t rely on topping the fluids up infinitely. Some fluids, such as hydraulic fluid, degrade over time, so you have to drain and flush the container before adding new fluid periodically.
If you find yourself dealing with low fluid levels more often than you should, it’s time to inspect your equipment for leaks.
When you monitor the fluid levels on your machinery and ensure that it’s sufficiently lubricated, you get the most of your equipment.
Lubricate Equipment Regularly
Making sure all moving parts are sufficiently lubricated is one of the essential parts of heavy equipment care.
Lubrication reduces friction by creating a film between two surfaces, which allows them to slide smoothly over each other. This film also helps protect your equipment from corrosion.
Without proper lubrication, moving parts grind against each other, exacerbating wear and tear.
Let’s take bearings as an example. Did you know that the most significant reason why bearings fail is inadequate lubrication?
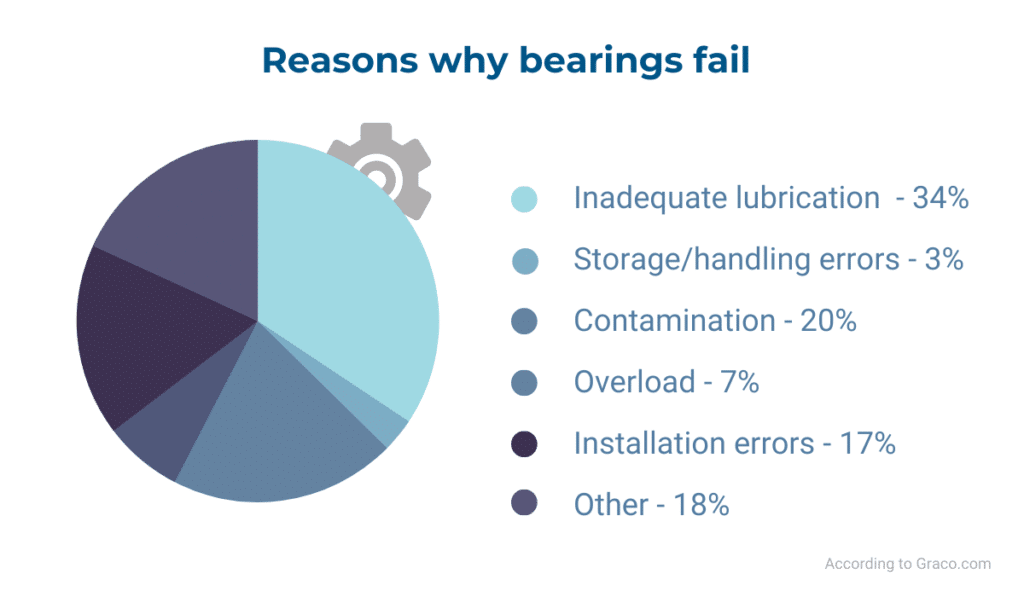
Another reason why keeping your heavy-duty equipment lubricated is necessary is because it prevents contamination.
Seeing that 80–90% of hydraulic problems result from contamination, it’s a good idea to schedule regular lubrication into your machine maintenance routine.
Before you apply lubricant or grease, make sure to remove all the dirt that may have built up. Otherwise, you’ll clog the very parts whose movement you were trying to aid in the first place.
The principle of removing the old hydraulic fluid before replacing it applies here as well.
Because some lubricants and greases are not compatible with each other due to the different thickeners, try to remove as much old grease as you can before applying a new dose.
However, no amount of lubrication can make up for failing to let the equipment cool down when needed. To keep the machines operable, you have to know their limits.
Know Your Equipment’s Limits
If you keep overworking your equipment, you invite trouble.
First of all, you’re risking your employees’ safety. When heavy-duty equipment runs for too long, the temperature of the components starts to rise, creating an unsafe environment for workers without heat-protective equipment.
Additionally, a buildup of pressure can lead to a pneumatic air burst, resulting in soft tissue injuries in your workers.
Overworking machinery is also dangerous for the equipment itself.
Pressed by the approaching deadlines, machine operators sometimes tend to load more weight than a machine can handle or move it around the site faster than they should.
Overloading a vehicle causes tires to overheat and wear down rapidly. But the damage doesn’t only affect such large parts of heavy equipment. Overworking machinery strains its components such as gears, silicone rings, and connection points as well.
Whether you’ve purchased or rented a piece of equipment, you want to keep it in a functional condition, so it doesn’t interfere with your operations.
Finally, before assigning a worker to operate a heavy machine, provide them with manuals and train them to balance the power and efficiency of a machine to extend the life of your machine fleet.
Invest in Storage
Leaving construction equipment on the site may save you some time short term, but that’s a high-risk practice in the long run because your machinery can get damaged or stolen.
The National Equipment Register estimates that equipment theft incurs costs of about $400 million annually. Here’s what the equipment thieves are after:
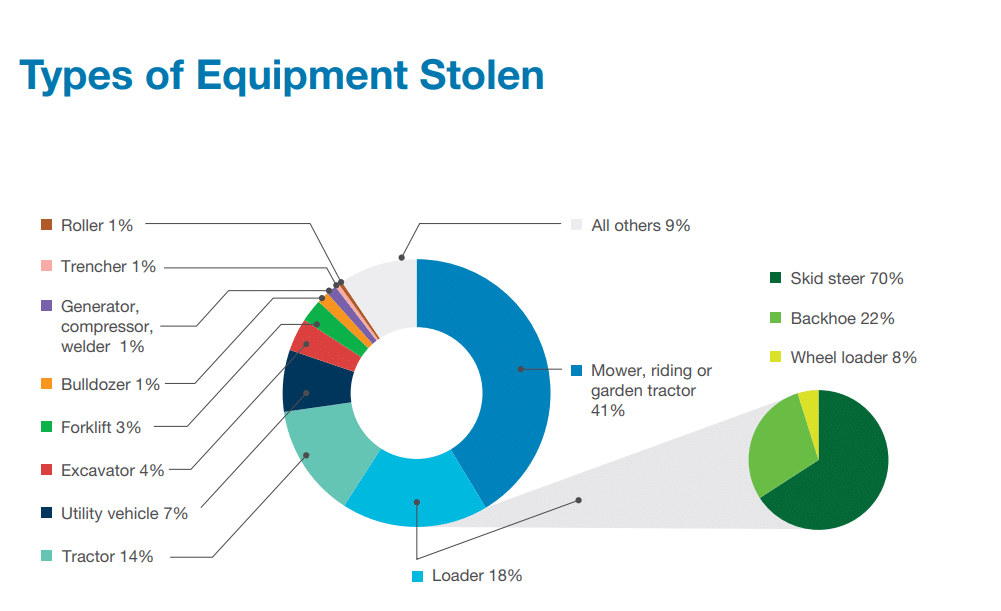
The fact that only 21% of the stolen equipment was recovered in 2016 is a good reason to rethink your storage practices.
Another motivator for storing your equipment properly is the potential damage that occurs when machines are left exposed to rain, sun, wind, or snow.
You can choose either an outdoor storage solution, like a storage yard, or opt for the pricier option, such as an indoor storage unit.
Heavy-duty equipment is large and, well, heavy, so if you end up storing it in an uncovered space, make sure to shrink-wrap the machines.
Investing in storage will preserve your machines, but only if you store them properly.
You have to store the machines in top condition, continue with regular maintenance, and implement security measures. Find our detailed post on best practices for heavy equipment storage here.
Educate Equipment Operators
Assembling a fleet of construction equipment is only the first step towards taking full advantage of machinery. The crucial part is having educated and skilled equipment operators.
Workers can operate most pieces of heavy-duty equipment with only a regular driver’s license. However, some vehicles often found on construction sites, such as tractor-trailers or tank trucks, will require a commercial driver’s license.
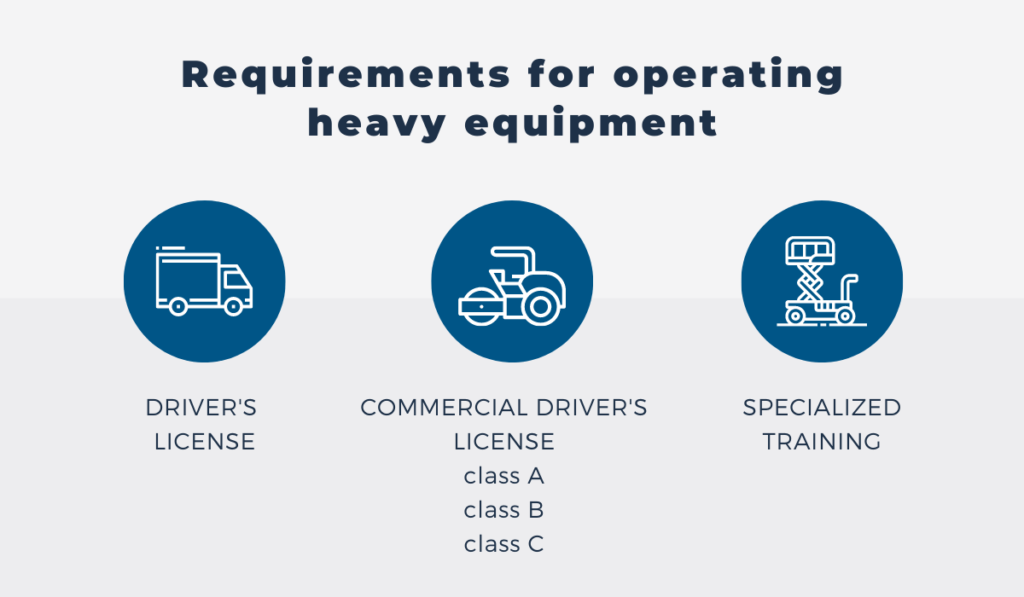
But even if your staff is legally allowed to drive and operate the machines, it’s still a good idea to invest in heavy equipment operator training.
Operator training usually covers site safety, machine operation, tires, wheels, fuel systems, repair and maintenance, and soil and soil testing.
By getting a formal education, your workers will learn the ins and outs of a machine, and they will be able to use it in a way that prolongs its useful life.
For instance, if your operators have in-depth knowledge of what’s under the hood, they won’t have to rely only on the dashboard to see how equipment is functioning at a given moment.
However, formal training is not always an option, so you can offer on-the-job training to make sure every operator gets sufficient experience before operating the equipment on their own.
Provide them with the manuals that come with every machine and make sure they use them to get familiar with the specifications and limitations of each machine.
Protect Electronics and Wiring
The requirements of the construction industry have changed, and you can now see built-in computers in backhoes, excavators, dozers, and other heavy equipment. Machines that used to be solely mechanical now often include some electronics.
This is a great step in improving the precision of your operations, together with increasing your productivity and enhancing safety on the site.
Still, despite the sturdiness of your heavy equipment, all these wiring bits and electronics can render your whole machine temporarily useless if they get broken.
And that’s not only true for modern equipment that comes with computers. You also have to protect the wiring of regular machines.
Rain, melting snow, or ice can find their way into the machinery and cause corrosion or even a short circuit.
Such small problems can take hours to diagnose, so it’s safer to implement preventative measures into your heavy equipment care.
Here are the main electrical components you always need to monitor:
- battery
- alternator
- starter
- spark plugs
When conducting regular equipment inspections, don’t forget to look for any exposed wires. If you know you won’t be using a machine for several days or weeks, secure it with a protective tarp.
Moreover, if you know the machine won’t be used for at least a month, you can shrink wrap it.
Check for Misalignment
Construction equipment is often used in rough terrains. Not all sites are accessible by paved roads, so your workers will sometimes find themselves driving over the ground covered in boulders or, on the contrary, across soft soil.
These conditions are not ideal for the state of your equipment.
While the purpose of heavy equipment is to be robust, it is still susceptible to wear and tear. If you’re working on rough terrains, securing proper alignment is essential for keeping your equipment in top shape.
Let’s start with the most apparent consequence of misalignment: rollovers.
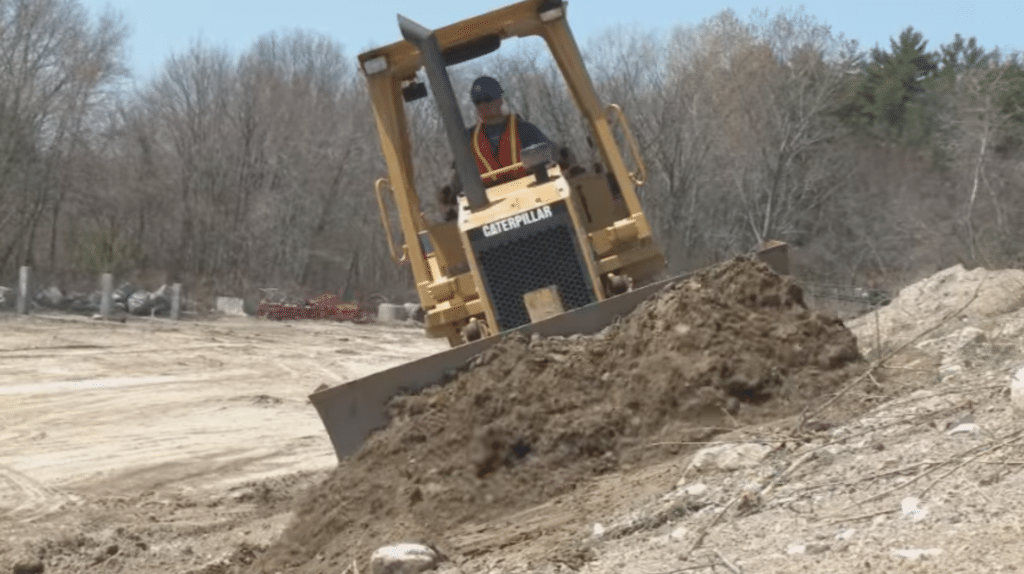
If a machine is not correctly aligned or the ground is unstable, it can lose balance and topple over. This presents a danger to the operator, site staff, or anyone passing by.
But misalignment can also damage your equipment. When a heavy machine goes over uneven terrain, its components are affected by the force resulting from vibrations and shaking.
Machine parts can get loose, and the weight transfers to the other parts that weren’t supposed to bear any load.
To prevent this, you should routinely check the equipment for misalignment and schedule a repair for anything out of the ordinary.
Keep Detailed Equipment Records
Large machines are almost always used by multiple operators and transported from site to site. When a malfunction occurs, that makes it difficult to pinpoint when, where, and how the fault occurred.
Yet you need that kind of data to create a repair plan. It also helps you study the circumstances and prevent the same defect from happening again.
This is why you have to keep an equipment tracking log.
You should know the exact check-in and check-out time for each of your machines, as well as the person who operated the machine. If you own multiple assets, you also need a reliable system to track the location of each piece of equipment.
Since so much work goes into maintaining equipment, having a clear overview of repair and service activities helps you organize future maintenance scheduling.
However, entering all that information by hand is tedious, so operators often skip that task, leaving a hole in your asset history records.
To make things easier for your crew, you can start using a digital tracking solution, such as GoCodes Asset Tracking.
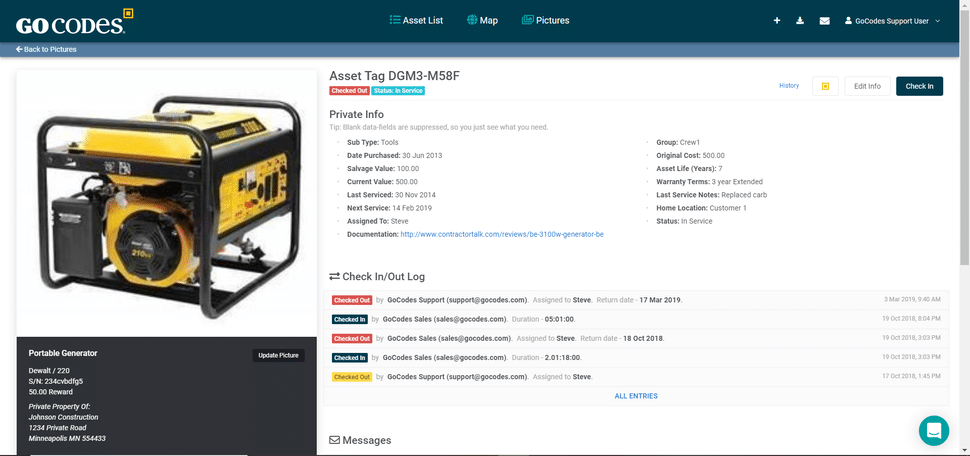
GoCodes Asset Tracking enables you to simply scan a QR code with your smartphone or tablet. You’ll instantly get the latest information on an asset.
As we stated earlier, heavy machines are used in all sorts of harsh environments.
That doesn’t have to worry you because GoCodes Asset Tracking offer sturdy metal QR labels with a strong adhesive. Depending on your requirements, you can also choose industrial hang tags, high-temperature resistant labels, and more.
Conclusion
As heavy-duty equipment is always a large expense, you have to take precautions to maximize its useful life.
A great way to start heavy equipment care is by monitoring fluid levels daily. Lubricating equipment is no less important.
Another measure you can take to protect your machines is to insulate wiring and electronics and to ensure your machines are properly aligned.
You’ll see the full benefits of these methods if you combine them with a proper storing solution and if you only let qualified staff operate your equipment.
Seeing that heavy machinery often changes hands, it’s also helpful to have a tracking system for all your equipment.