When your day is packed with deadlines and putting out fires, it can be difficult to stay on top of industry trends or know how you stack up against competitors.
This statistical overview aims to lift you out of the weeds and give you a much-needed high-level perspective.
We’ve compiled 10 telling statistics and insights to help you manage your fleet more effectively and create a data-backed plan for 2025 and beyond.
Let’s dive into the data!
In this article...
74% of Fleet Managers Find Their Role Challenging
In 2024, the J. J. Keller Center for Market Insights ran its fourth annual survey on the state of fleet management.
It revealed that 74% of fleet managers consider their jobs moderately to extremely stressful.
More precisely, 40% of respondents rated their job as ‘moderately challenging,’ while 34% rated it as extremely or very stressful—the same proportion as in the previous year’s survey.
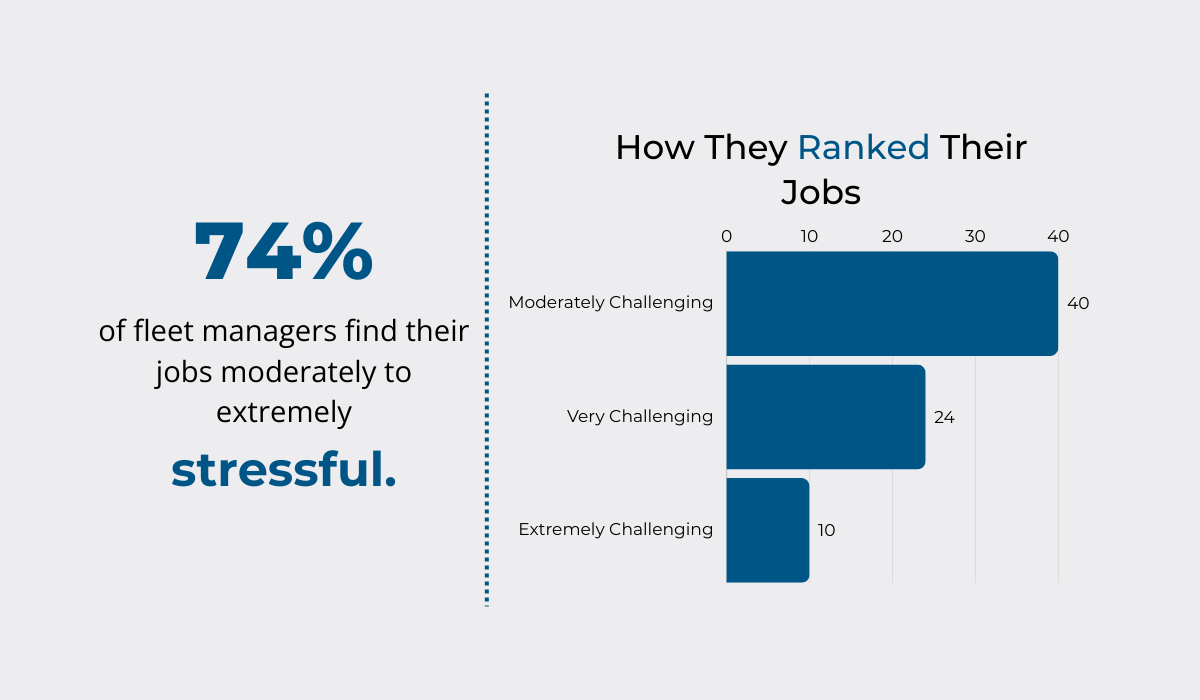
While many factors are adding to fleet managers’ stress levels, the most prominent concerns include safety and loss avoidance.
Fleet managers are highly concerned about safety and want their leadership to prioritize it.
They also face mounting pressure to avoid losses during unforeseen circumstances, such as breakdowns and accidents.
There are many ways in which companies can help them alleviate these concerns.
For example, they can consider implementing more robust driver vetting and retainment procedures, as well as performing regular vehicle maintenance.
However, to really learn what’s necessary, the leadership must sit down and open up a dialogue with fleet managers and frontline employees.
As Dr. Timothy Ludwig, a safety consultant and professor, emphasizes:
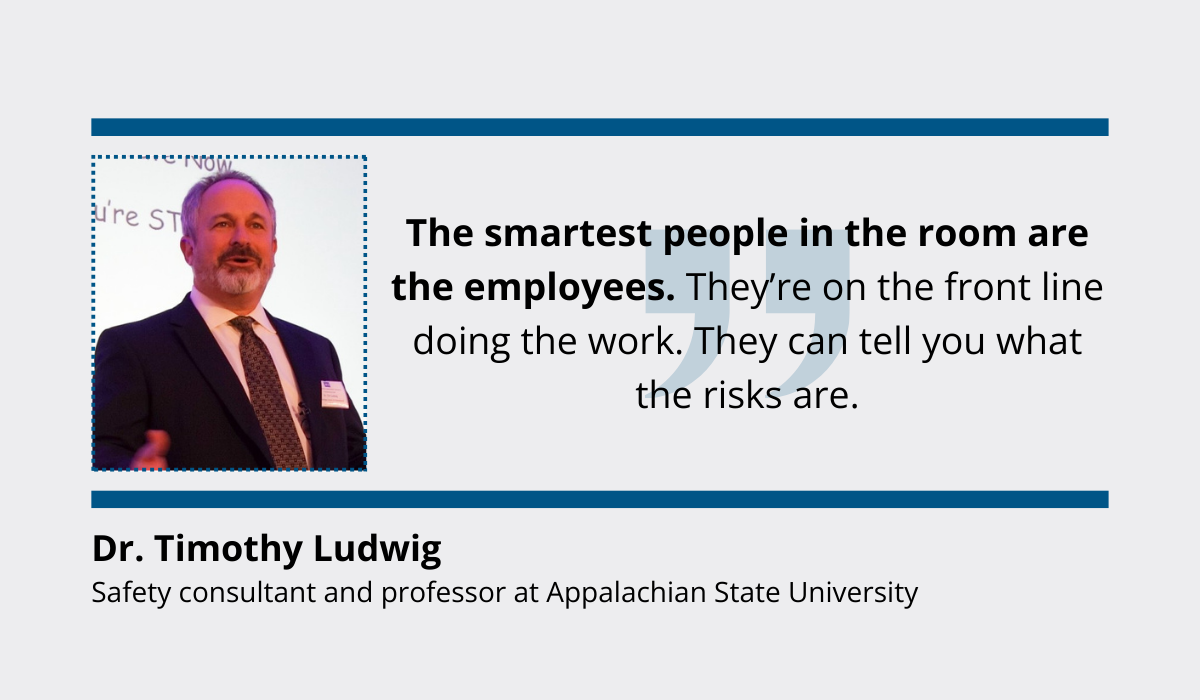
So, despite fleet managers’ challenging and stressful roles, leaders who actively listen can better identify the key stressors and implement practical solutions.
Rising Costs Are the Top Concern for 77% of Fleet Managers
According to The 2025 Fleet Technology Trends Report by Verizon Connect, increasing costs are the top concern for fleet managers for the fifth year in a row.
As many as 77% of them cite soaring expenses as their top challenge, only a slight drop from last year’s 79%.
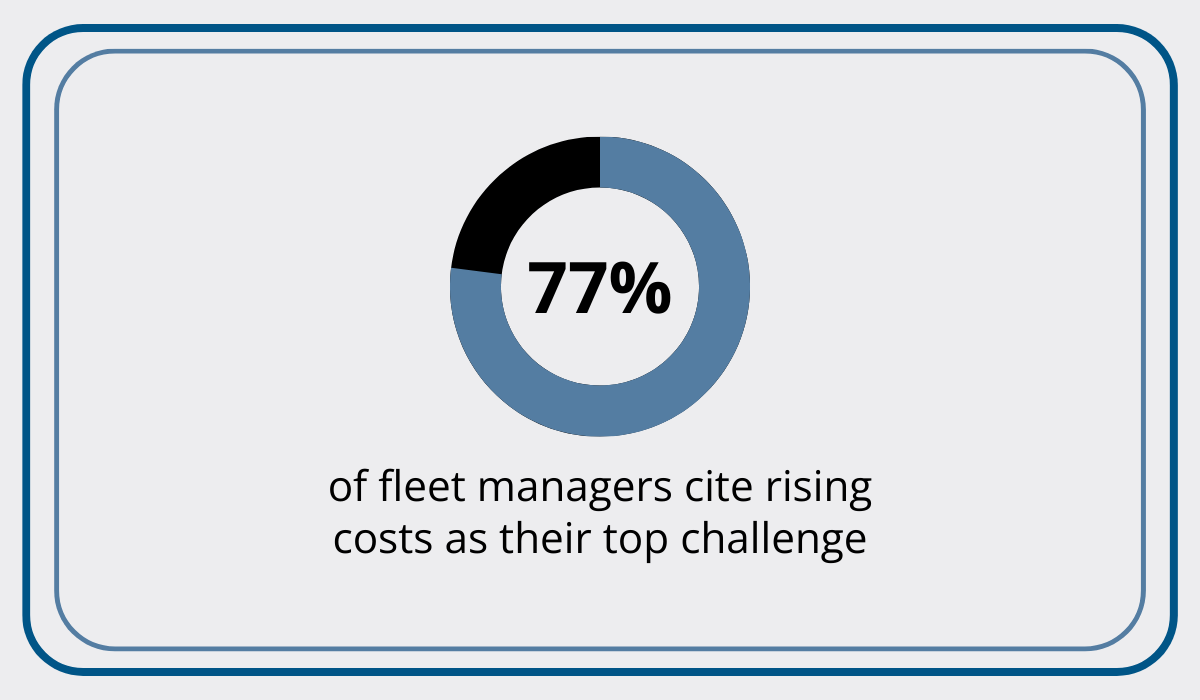
This concern is not without merit.
Fleet management costs are indeed rising.
This is largely due to the increased cost of critical expenses and factors such as:
- Increased vehicle complexity, requiring specialized and more expensive maintenance tools and expertise,
- Higher labor rates, driven by a long-standing shortage of qualified workers,
- General inflation, impacting everything from fuel to insurance prices.
At the same time, leadership may have unrealistic expectations that add to the pressure.
They may expect fleet managers to find creative ways to reduce costs, or at least keep them at the same level—despite the unfavorable market situation.
Again, there is a clear need for better understanding between both parties.
Open and honest conversations are essential, particularly in clarifying what is and isn’t feasible.
Knowing When a Repair is Needed is The Top Upkeep Challenge for 44% of Fleets
As mentioned, fleet managers feel pressured to minimize losses and address safety concerns.
So, it’s no surprise that 44% consider identifying repair needs before breakdowns or accidents occur as their most important vehicle maintenance concern.
This concern ranks just below knowing when a vehicle is damaged or non-compliant, and above effectively organizing routine vehicle maintenance.
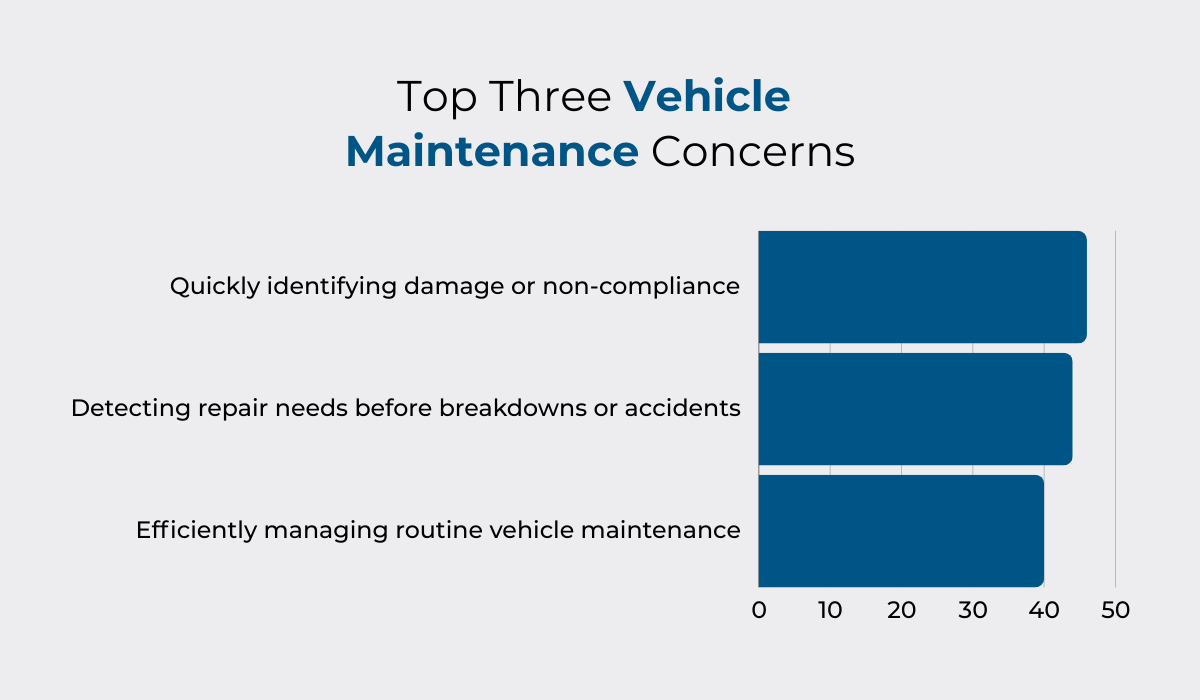
So, how can fleet managers effectively address these challenges?
One potential solution is using new, more advanced vehicle technology that can improve maintenance and potentially minimize breakdowns and accidents.
However, such technology is usually expensive, in terms of both purchase and repair costs.
As Chris Foster, fleet manager at Holman, highlights:
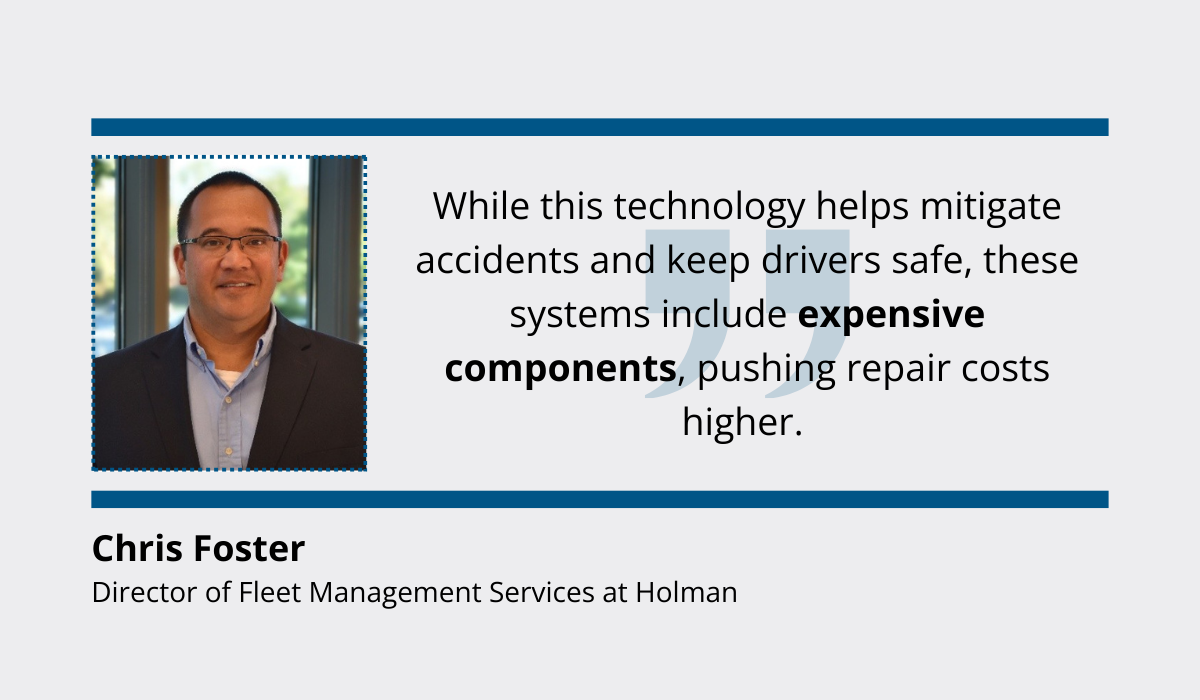
This brings us back to the fact that rising costs are fleet managers’ main concern.
There’s clearly a need to set clear fleet management objectives, priorities, and budgets, as well as figure out how to strike a balance between the three.
60% of Fleets are Managed Using Spreadsheets
In the age of advanced electronic solutions, it’s surprising that 60% of fleet managers still use spreadsheets to manage fleets.
But what’s even more shocking is that 52% use paper documents.
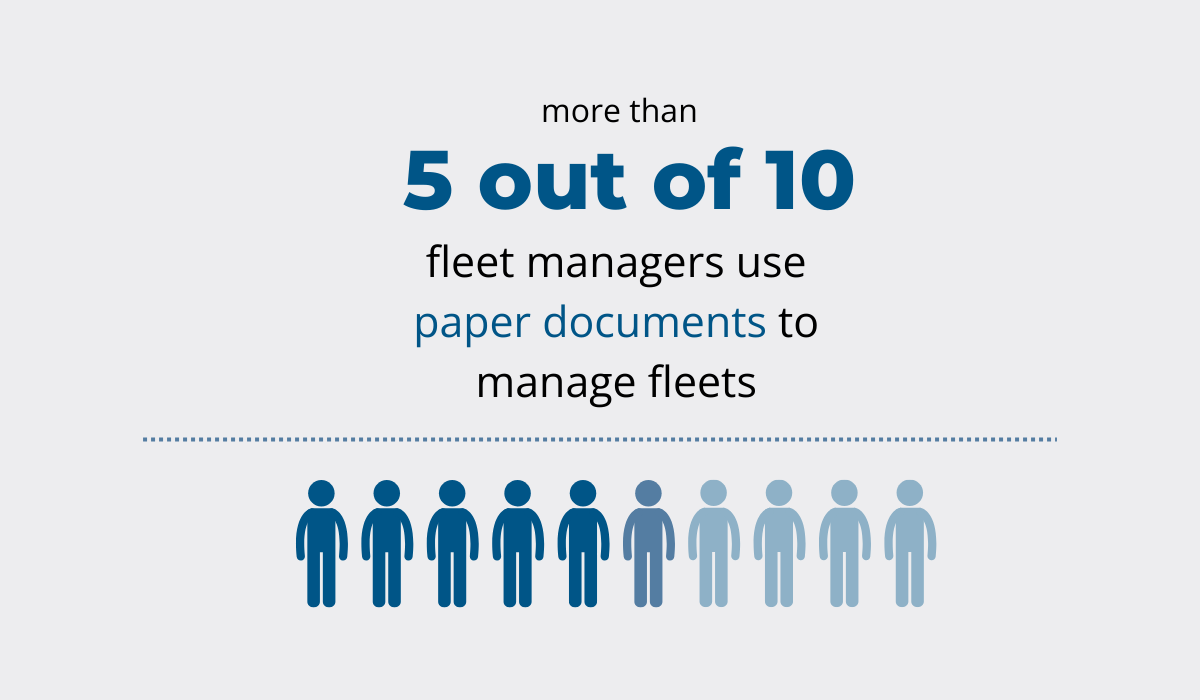
Even the more efficient option out of the two—using spreadsheets—is wasteful and risky.
About 94% of spreadsheets in use contain errors. In fleet management, these can lead to grave consequences, such as accidents and compliance issues.
Additionally, a typical office worker spends 3 hours working on spreadsheets every week. Fleet managers may spend even more.
This also translates to increased labor costs.
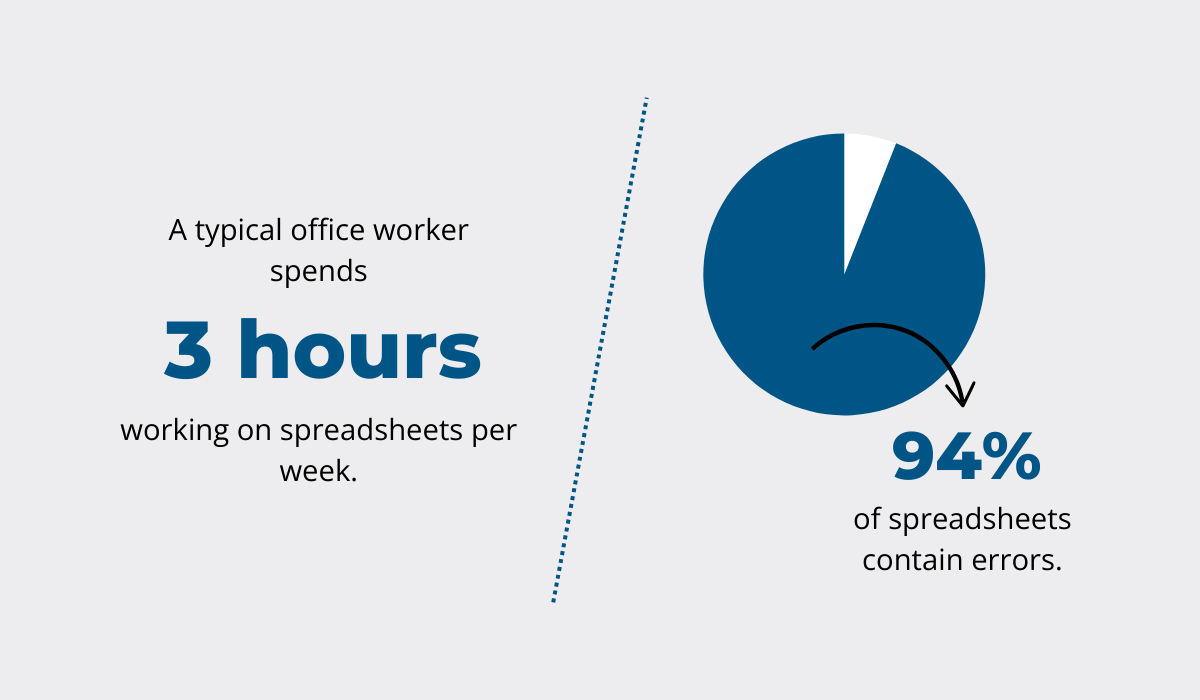
Using paper is, of course, not any more effective. Besides being tedious and prone to errors, it is also highly expensive.
When calculating the total cost of using paper, consider many more expenses than you initially may think. These include:
- Printing costs
- Document archiving costs
- Distribution costs
- Supply and equipment costs (e.g., office supplies and printers)
- Other costs, such as the cost of re-printing and labor
A better option would be to use specialized solutions for tracking your vehicles, like GoCodes Asset Tracking.

GoCodes Asset Tracking offers GPS trackers, those you plug into your vehicle’s ODB2 port, along with software that helps you streamline the whole process and avoid many mistakes that come with using spreadsheets.
57% of Fleet Managers Say Employees Waste Half Their Day
The same report discovered that fleet managers aren’t the only ones suffering from inefficient systems.
Their employees are, too.
In fact, 57% of fleet managers with over 100 vehicles estimate their employees spend half their day or more on repetitive administrative tasks—such as inventorying goods and assigning vehicles to drivers.
This inefficient management is not restricted to just large fleets, either.
Fleet managers across the board estimate their employees lose about 5 hours a day, or over 3 days in a 5-day workweek, on similar routine tasks.
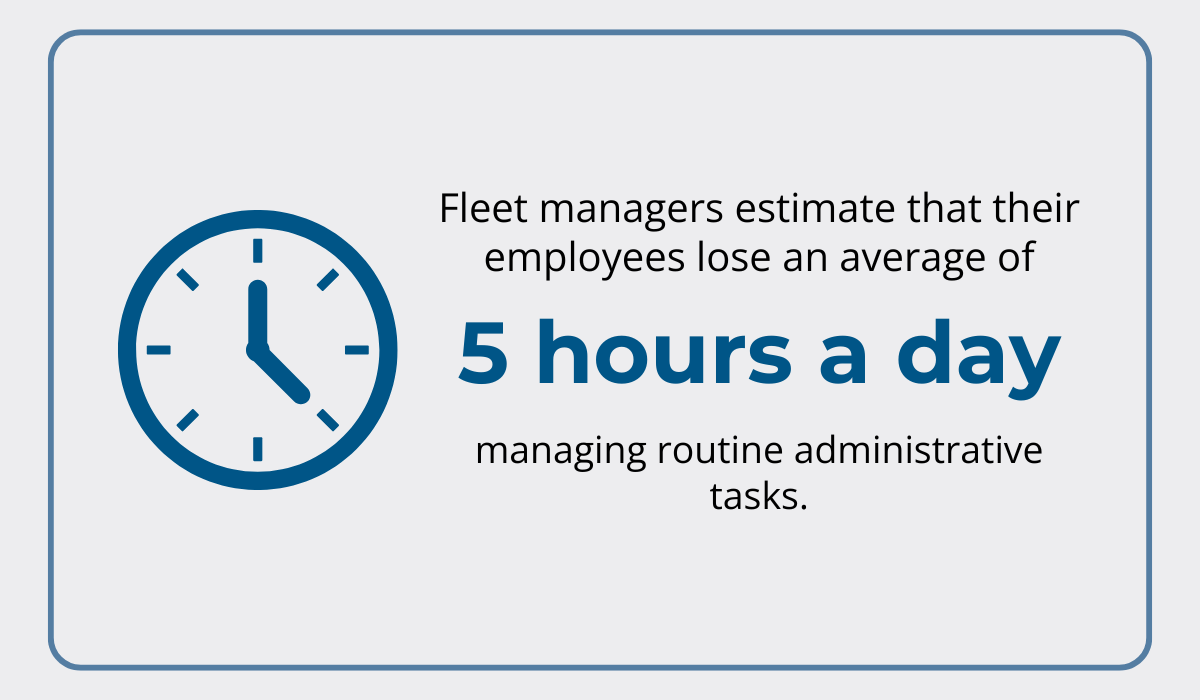
So, whether you have a smaller or larger team, the chances are that administrative work is stealing their time.
And the majority of this work can almost always be automated or at least significantly streamlined.
Apart from reducing company expenses, such automation can help employees feel more fulfilled.
Luckily, we may soon see automation as a way to allow humans to perform more high-level and meaningful work.
And this might make them less stressed.
37% of Drivers Resist Vehicle Monitoring
Though more and more fleets are adopting telematics, some are still struggling to get drivers on board.
According to the 2024 Telematics Report, 37% of fleet operators say that drivers resist vehicle monitoring.
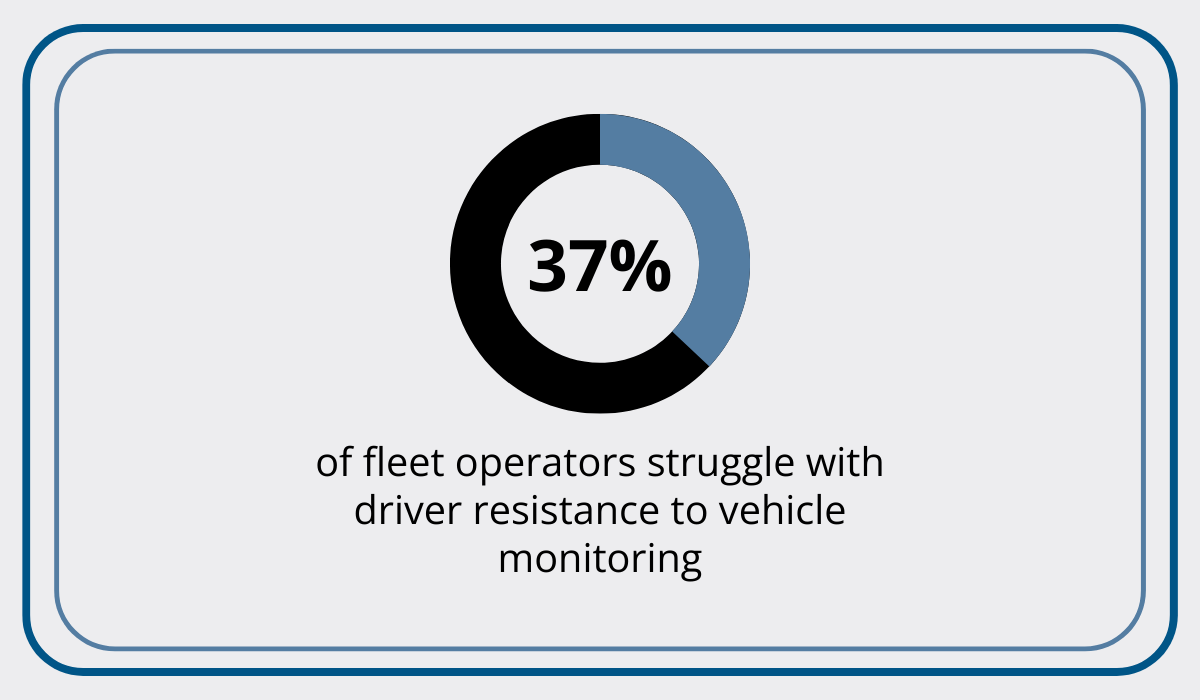
This resistance is more prominent in some industries than others.
The trucking and transportation industry, for example, has an overall high percentage of monitored vehicles.
Conversely, the adoption rate could be higher in medical, government, and education industries.
This may be because finding qualified workers is easier in some industries than others, making them more open to compromise.
Additionally, smaller fleets lag behind larger ones when it comes to effective telematics adoption.
This may be due to various reasons, such as a lack of innovation resources and smaller budgets.
72% of Fleets See Fewer Crashes and Claims With The Combination of Telematics and Training
The same report shows that, despite the resistance, drivers are clearly better off with telematics.
72% of fleet professionals say that telematics, combined with training, helped them reduce crashes and claims.
More specifically, there are reports that tracking driver behavior and vehicle health reduces incidents by 80% on average, and accident claim costs by 50%.
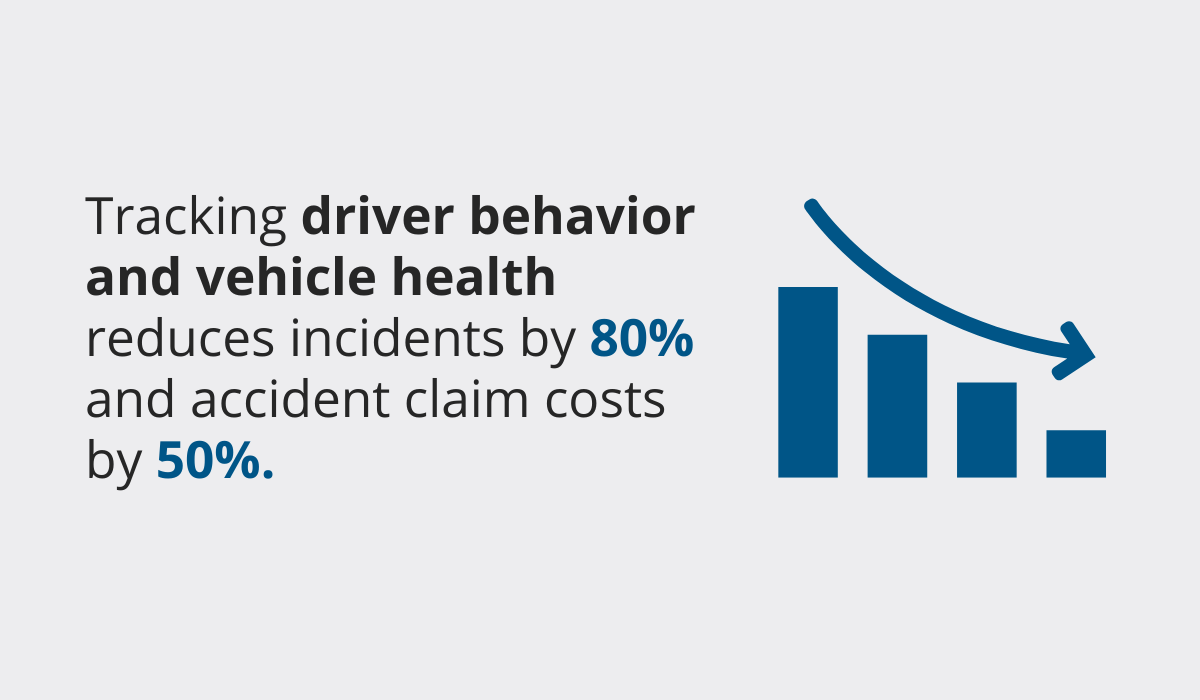
While training can be provided independently of telematics, field-based data makes it more efficient.
For example, managers can use telematics data to tailor training to every driver, ensuring they get the exact knowledge they need without wasting time on irrelevant stuff.
Additionally, telematics may also help reduce fuel costs, as drivers tend to be more mindful of their driving when they know they’re monitored.
This may lead to more balanced driving behavior.
69% of Fleets Have Adopted GPS Tracking Solutions
GPS tracking is becoming a standard in the industry, with the majority (69%) of fleets actively using GSP tracking solutions for logistics and operations.
It is not surprising that the most prevalent users are enterprises with 500+ vehicles.
Out of those, 87% use GPS tracking to track drivers and assets.
They are followed by medium fleets with 50 to 499 vehicles. 76% of them use GPS tracking, compared to just 59% of small fleets with up to 49 vehicles.
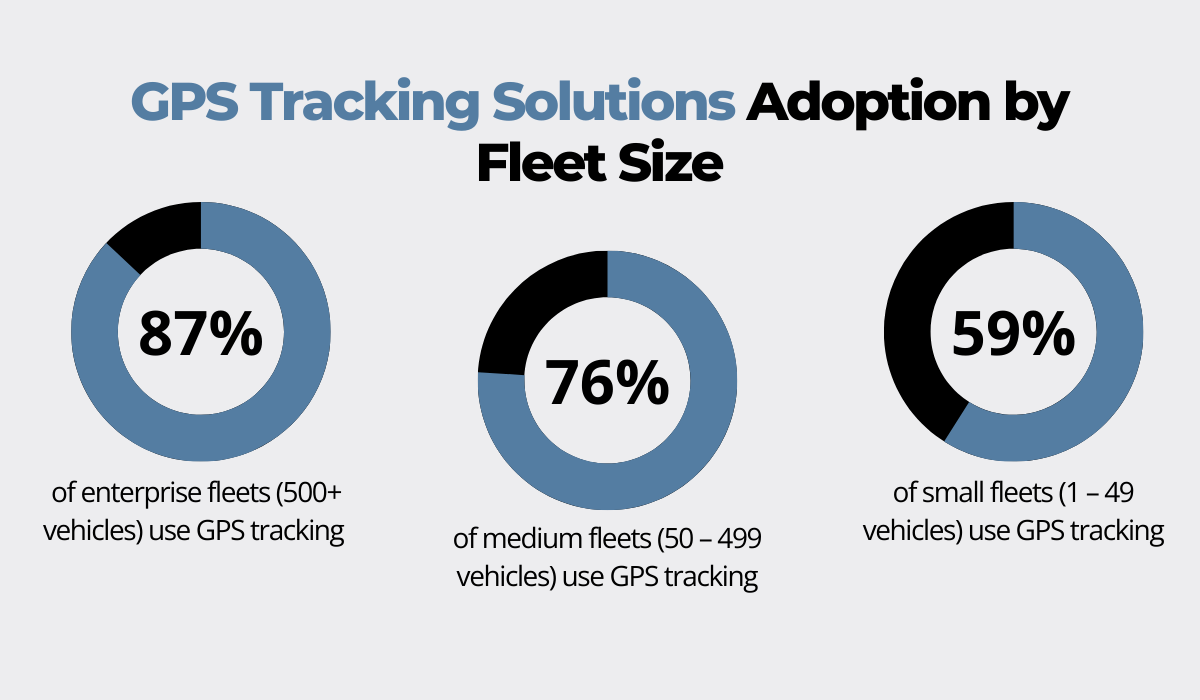
It is important to note that the majority of respondents in this survey (45%) had small fleets, while the smallest group of respondents (22%) had large fleets.
This uneven distribution may have somewhat influenced the findings.
Even so, one thing is clear.
Even smaller fleets—-with usually significantly smaller budgets—are doubling down on GPS tracking.
62% of Fleet Managers Say GPS Tracking Increases Efficiency
The same report reveals that 62% of fleet managers believe that GPS tracking helps them improve efficiency.
Real-time vehicle data helps them achieve critical outcomes, such as reducing costs and downtime, ensuring driver and vehicle safety, and mitigating theft.
However, GPS tracking delivers benefits on several other fronts as well:
More than half of fleet managers say it’s helping them address one of the most pressing industry challenges: driver shortage.
That’s because GPS tracking allows drivers to plan their routes more effectively and decrease frustration, making job offers more attractive.
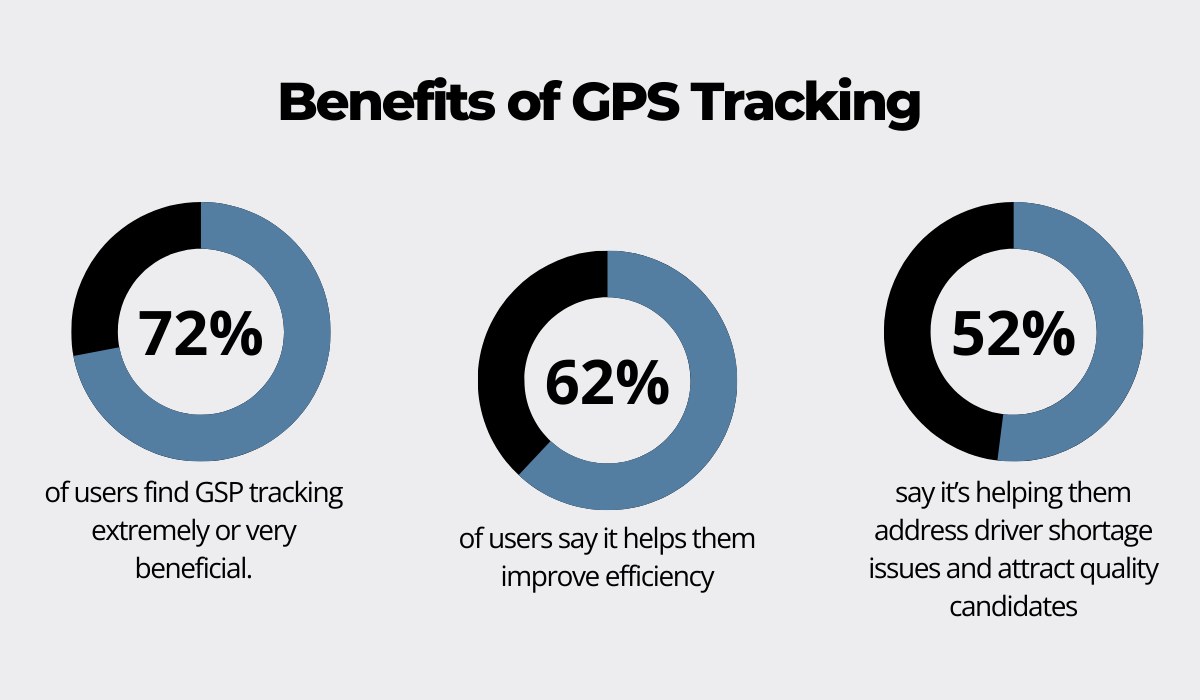
Overall, a big majority (72%) of users find it extremely or very beneficial.
Our GPS tracking solutions with telematics, for example, can also be used to plan better routes.
79% of Managers Expect the Majority of Their Fleets to Transition to Alternative Fuels in the Next 5 Years
The Telematics Report 2024, which surveyed over 500 fleet professionals globally, found that 79% expect more than half of their fleets to shift to alternative fuels in the next 5 years.
Many are already planning for this transition, with 27% planning to invest in converting to electric and alternative fuels in the next 12 months.
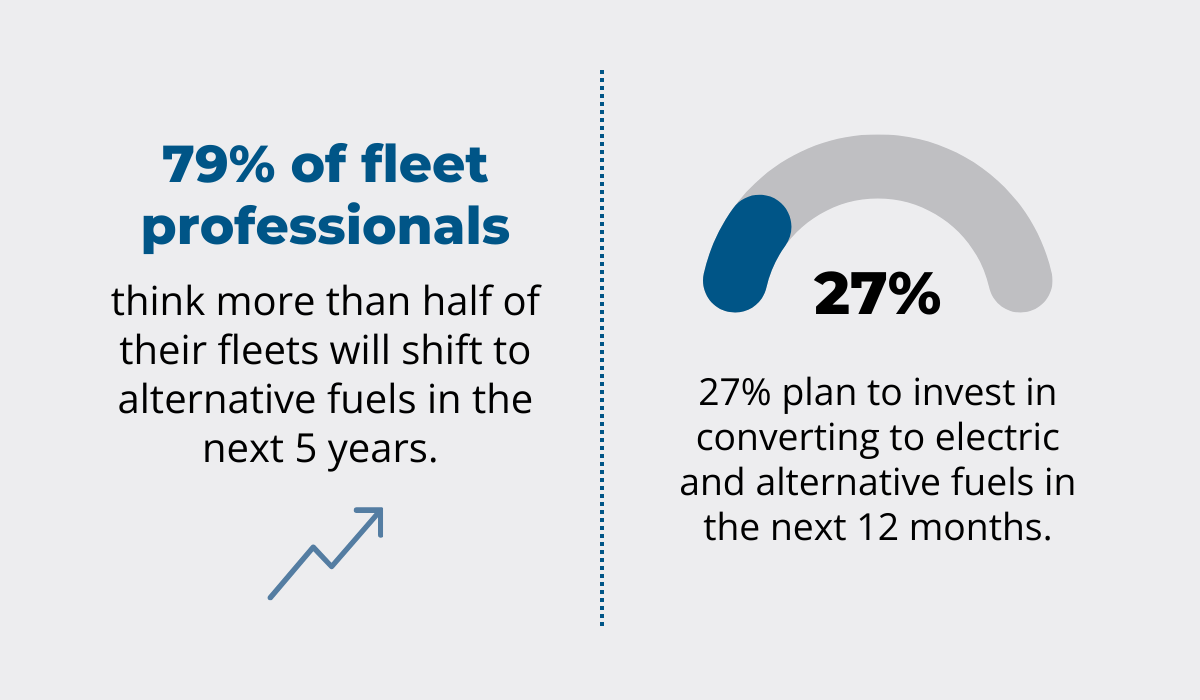
These findings should come as no surprise to industry professionals.
The industry is feeling more and more pressure to switch to more sustainable and eco-friendly practices, both from consumers and regulatory bodies.
That’s because some professionals believe customers will demand more sustainability initiatives in the next 1-3 years.
However, switching to alternative fuels may also help combat rising costs—one of the top concerns for many fleet managers.
This is especially true for fuels like electricity and LNG, which can be cheaper than diesel.
Pernilla Kemlin, a product manager at Volvo Trucks, shares her view on that:
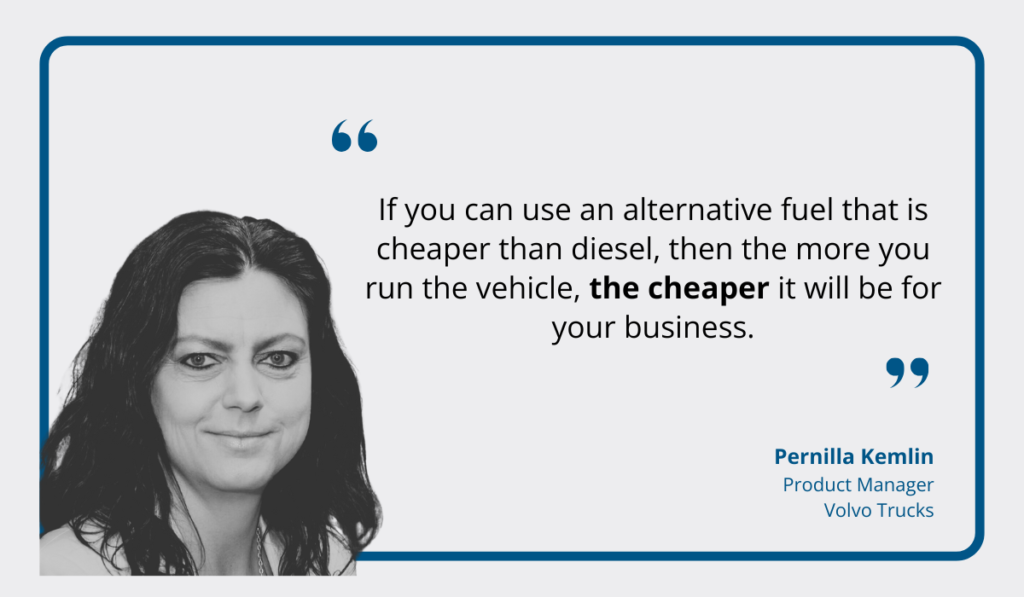
Of course, it’s no secret that this transition usually comes with higher upfront costs. Electric vehicles, for example, can be especially expensive.
Even so, it is likely that this initial investment will pay off in the long run.
So, consider following the example of fleet professionals already preparing for this transition.
Conclusion
The fleet management industry is always changing and shifting.
Staying on top of these changes can be difficult, but it’s absolutely essential—especially if you want to gain or just keep a competitive edge.
We believe that this data-driven overview will help you achieve just that.
Leverage the insights mentioned here to attract top talent, reduce losses and downtime, and stay competitive in an era defined by advanced technology and a focus on sustainability.
Happy planning!