Effective inventory management is the first step towards tightening finances, scaling up, selling to another owner for a profit, or retrenching.
For a construction company, maintaining strong inventory control is vital for saving money, understanding supply levels, and avoiding rush fees.
However, some owners of construction companies may be unaware that poor inventory management is plaguing their business, because that problem presents itself through a variety of seemingly unrelated issues.
Therefore, it’s beneficial to look for signs that faulty inventory management practices are leeching money, resources, employee time, and even goodwill with suppliers.
These can include rarely taking inventory audits, dealing with inventory shrinkages or shortages, storing unusable or excess inventory, and putting too much pressure on suppliers.
Let’s go over each of these signs of poor inventory management and look at what you can do to alleviate them.
In this article...
Lack of Inventory Audits
Frequent inventory audits enable you to keep track of materials and tools, which is critical for preventing and detecting inventory problems on time.
Nevertheless, some construction companies let inventory audits fall by the wayside, unaware of their true importance.
It’s easy to see why.
Physical inventory audits involve a great deal of time and resources, and might even necessitate hiring temporary workers to handle the increase in workload.
Inventory audits can also be difficult to schedule as they often must take place after regular business hours, or they can disrupt normal office or warehouse operations.
However, a lack of inventory audits is one of the first indicators of poor inventory management.
After all, if a company doesn’t periodically take stock of what it owns, it cannot use its inventory to its full potential.
Luckily, nowadays, there are digital solutions that make inventory audits a much less daunting affair than they used to be.
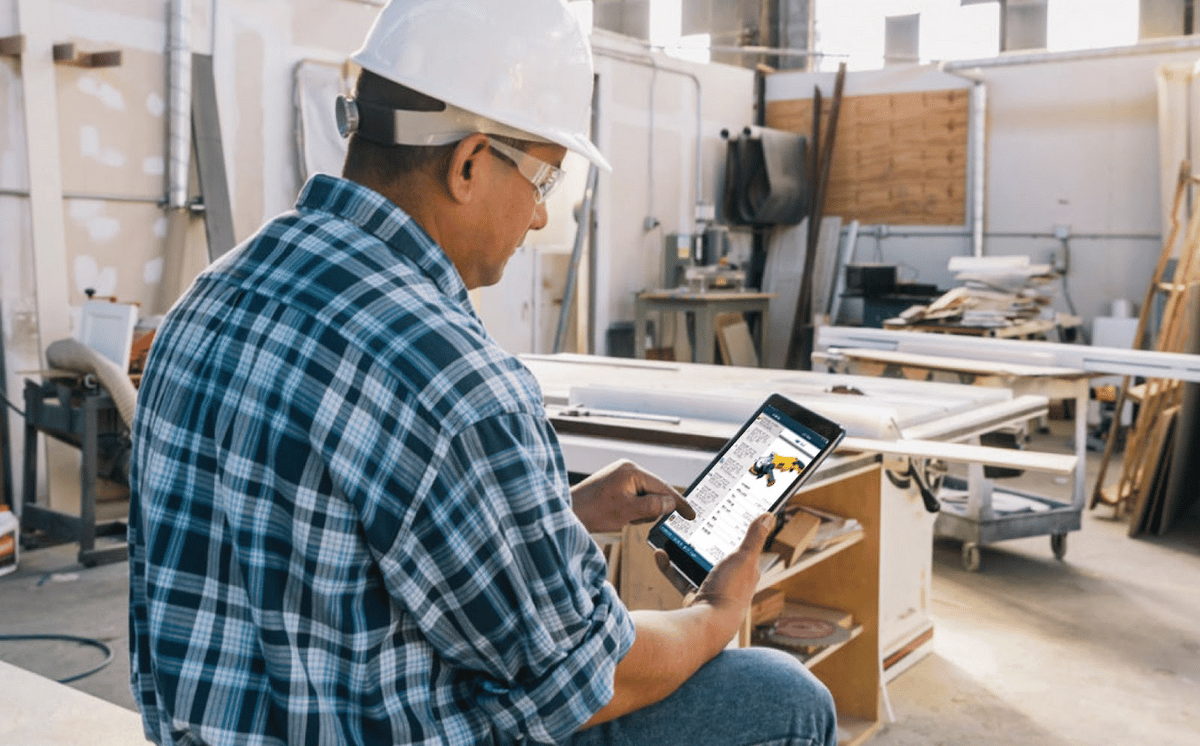
For instance, a cloud-based inventory tracker like GoCodes is an excellent resource for construction businesses that are wary of regular physical inventory audits or have little experience with them.
GoCodes helps construction companies automate much of their audit work.
It’s a mobile solution, so employees can scan items in the field as they are warehoused or removed, and even as they are placed on the road to a distant worksite or moved to a different place in a warehouse.
Moreover, as GoCodes stores data in the cloud, up-to-the-minute information is available at any time and in any timezone to project stakeholders with the right credentials.
It is the perfect tool for automating and easing regular audits, which are a vital component in addressing poor inventory management.
Inventory Shrinkage
Regular audits are crucial for discovering inventory management mistakes and inventory shrinkage is one of the most glaring among them.
In simple terms, inventory shrinkage describes the difference between the construction company’s inventory records and its actual inventory.
The missing items that are listed in the inventory records but don’t exist in the field constitute shrinkage.
Inventory shrinkage is a difficult problem and it can be the result of:
- Miscounting
- Damaged parts
- Administrative errors
- Supplier fraud
- Employee theft
- Supplier error
- Moving items without recording the action
The Corporate Finance Institute recommends turning to automated inventory management to combat this issue.
As this graphic from WallStreetMojo indicates, automation can help address shrinkage in a variety of ways:
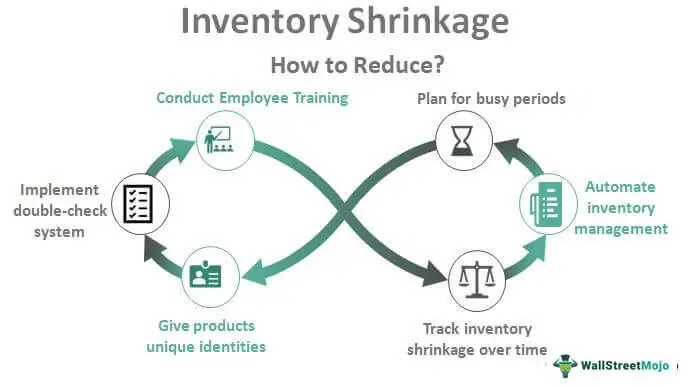
Relying on a digital solution for managing inventory can drastically lower the possibility of human error and produce a chain of custody for each item, no matter how large or small.
Inventory Shortages
Inventory shortages have been a worldwide occurrence since the COVID-19 pandemic.
The global disruption impacted supply chains tremendously, and its significance is still filtering throughout the construction industry.
What is more, many construction companies are currently grappling with a housing shortage, homebuilding boom, and laborer shortage at the same time, so late-to-arrive materials are yet another challenge to an embattled industry.
Even though many clients understand the difficulties of navigating the unreliable supply chain, and might be struggling with it themselves, inventory shortages are particularly detrimental to the construction industry.
The data collected by the US Census Bureau reflects that:
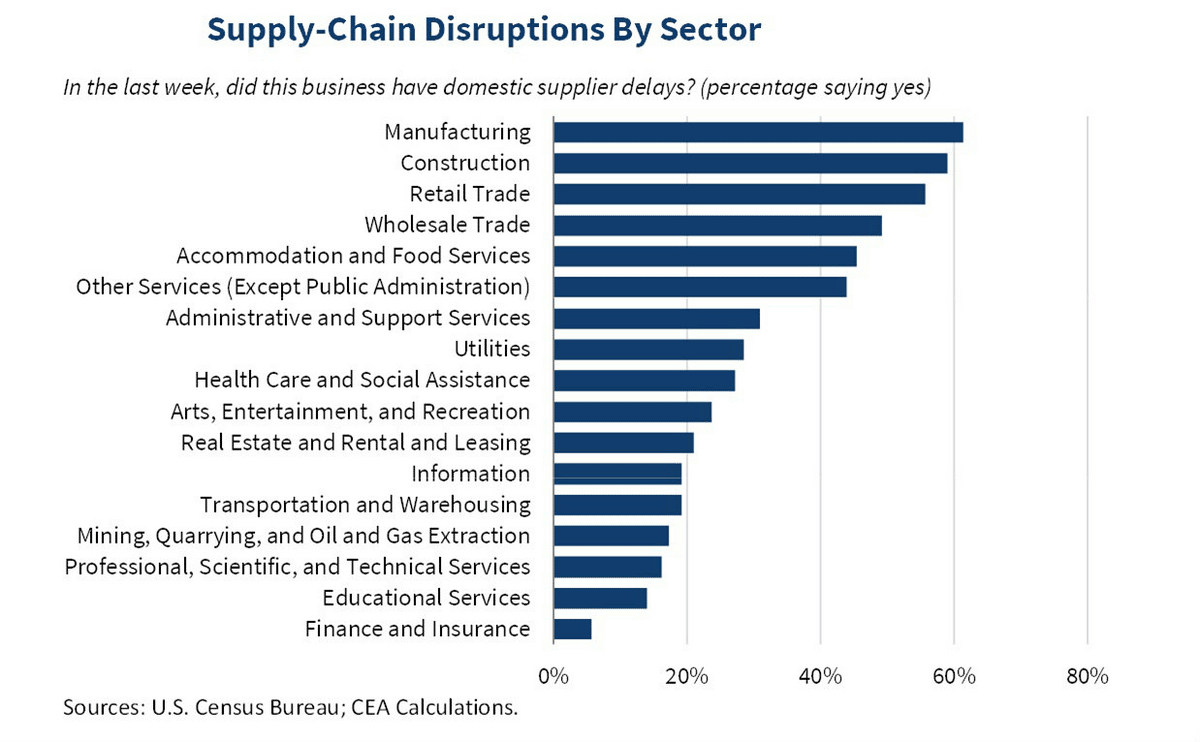
As this graph indicates, the impact of the supply chain issues on the construction industry was second only to manufacturing—and even the lack of supplies in manufacturing directly ripples into the construction industry.
A shortage of such materials as cement, bricks, and heavy machinery means that inventory management problems are almost guaranteed.
In fact, a construction company that was already suffering from inventory shortages even without these unusual circumstances, or had yet to recover at all from the effect of the pandemic, would be particularly affected.
Nevertheless, it’s important to keep in mind that material shortages can be the result of—or at least exacerbated by—inaccurate activity forecasts, which go hand in hand with poor inventory management.
When employees and project managers aren’t sure of how many items are in stock or available from local suppliers, this often leads to expensive and stressful last-minute rush ordering, complicating an already complex situation.
That’s why it’s important to implement good inventory management and purchasing practices.
Excess Inventory
With the supply chain in chaos, some construction companies may be fearing even greater supply shortages in the future.
In those circumstances, it is tempting for project managers and contractors to over-order materials and simply toss what isn’t needed into storage for a potential future project.
However, frequently having too much inventory left over after construction jobs is also a sign of poor inventory management.
You may wonder, with inventory shortages so prevalent, what’s wrong with excess inventory?
There are several reasons.
If a construction company frequently purchases more inventory than it needs, the costs add up.
Moreover, excess inventory can take up valuable storage space that could be used to store other much-needed items.
Finally, excess inventory can lead to employees wasting valuable time and resources trying to find what’s needed to complete a project.
Then, there’s the issue of transportation waste:
This is unnecessary motion or movement of products or materials that does not directly support immediate production, such as materials being transported from one job-site to another or materials being transported from the job-site back to the Building Partner. Ideally, transport should be minimized for two reasons: It adds time to the process during which no value-added activity is being performed, and the material is exposed to handling damage.
The above definition of transportation waste is directly tied to excess inventory. The phenomenon leads to damage, timeline slippage, and confusion.
Failure to move inventory from a completed project to one currently underway is a further symptom of a loss of supply control.
However, committing to a more efficient practice and intelligent maneuvering of raw materials helps avoid wasting gas and employee time, while improving employer oversight.
It can also eliminate the habit of wasting leftovers, prevent over-ordering, and avoid last-minute panic purchasing or using rental inventory.
Strained Relationships With Suppliers
Frequent rush orders put suppliers in an unfavorable position and ultimately damage the reputation of a construction company, as its relationship with the suppliers becomes strained.
Construction suppliers are often asked by clients to rush an order to meet important milestones. Pressuring them to do this a lot isn’t a good way to sustain a solid business relationship.
Suppliers who bail out construction companies one time too many might feel tempted to sever the connection, as last-minute demands force the supplier to scramble to gather and deliver materials as well.
And as the illustration below shows, good relationships are the cornerstone of running a successful business, especially in the construction industry.
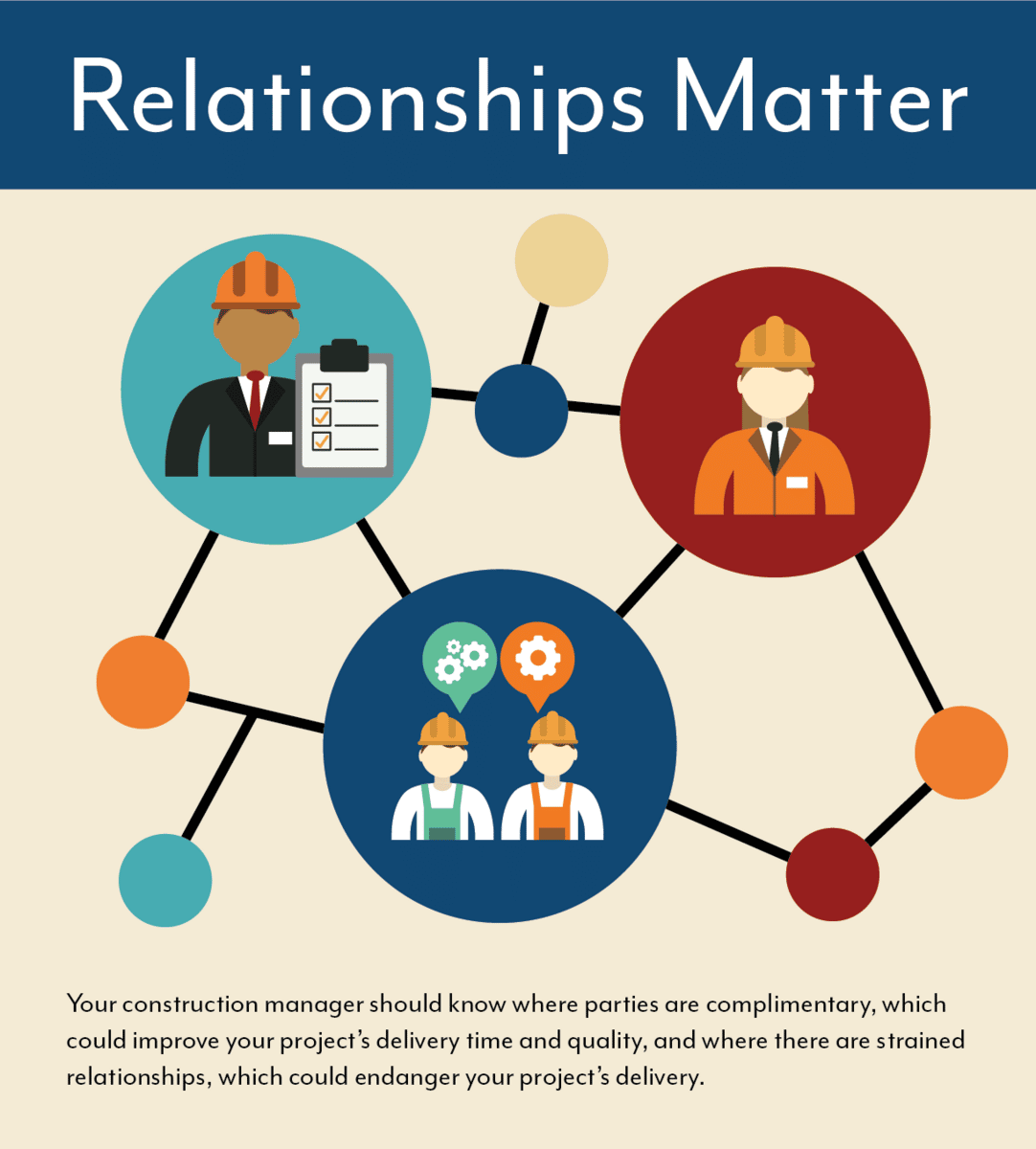
Project managers who don’t think of the impact of begging for favors time and time again are thinking only of how to extricate themselves from a momentary problem.
They are not concerned with the company as a whole, and certainly not how their requests might impact future projects.
Construction is a stressful enough endeavor without placing unnecessary strain on the connections contractors must rely upon.
The cost of toxic relationships with suppliers extends beyond uncomfortable encounters and the loss of much-needed connections in the construction industry.
Perhaps the starkest potential outcome of too many difficult relationships is losing a valuable supplier to bankruptcy if the business turns out to be unable to sustain the constant stress and cost of meeting the demands of their buyers.
In addition, once a communication gap occurs, it can be difficult to rebuild the relationship.
Suspicion and injured feelings can burden an already-weakened bond—and that can have devastating consequences for your business as well.
Therefore, make sure to manage your inventory wisely, to avoid unnecessarily burdening your suppliers.
Conclusion
Poor inventory management is often a symptom of larger problems.
Failing to control warehouse contents or raw materials can have a tremendous effect on a construction company’s bottom line, particularly when adjusting from periods of major activity to phases of recession or supply shortages.
Correcting poor inventory management begins with realizing that it presents a problem in your business.
Since poor inventory management can manifest itself as other issues, such as inventory shrinkage, excess inventory, or frequent shortages that place a burden on your supplier, understanding that connection is the first step towards finding a solution for the underlying issue.
It’s important for construction company owners to conduct a physical inventory audit and continue to track their assets with a multifunctional system such as GoCodes in order to stay on top of their inventory.
