Key Takeaways:
- When an asset’s repairs exceed half the replacement cost, it’s best to replace it.
- Holding on to aging equipment too long increases repair risks, drives up costs, and drags down productivity.
- Asset’s condition and market factors guide your decommissioning strategy.
- Asset management platforms enhance ALM processes by helping track utilization, forecast maintenance, and easily access relevant data.
Did you know that the costs of owning and operating equipment can account for 10% to 50% of total project costs?
Without a solid asset lifecycle management strategy, those costs can spiral quickly.
That’s why it’s critical to manage your assets with intention—maximizing their value while minimizing waste.
Still, knowing when to repair, replace, or retire an asset is easier said than done.
This guide breaks down the key factors to consider so you can make smarter, more cost-effective decisions.
In this article...
Importance of Asset Lifecycle Management
Asset lifecycle management (ALM) is essential for any company or facility that relies on heavy machinery, vehicles, and equipment.
Managing assets across the five key stages of the lifecycle helps ensure optimal performance, minimize unexpected downtime, and even unlock cost savings.
But to truly improve efficiency and keep operations running smoothly, you need to adopt a deliberate, strategic approach to managing your assets.
And that’s exactly what ALM is:
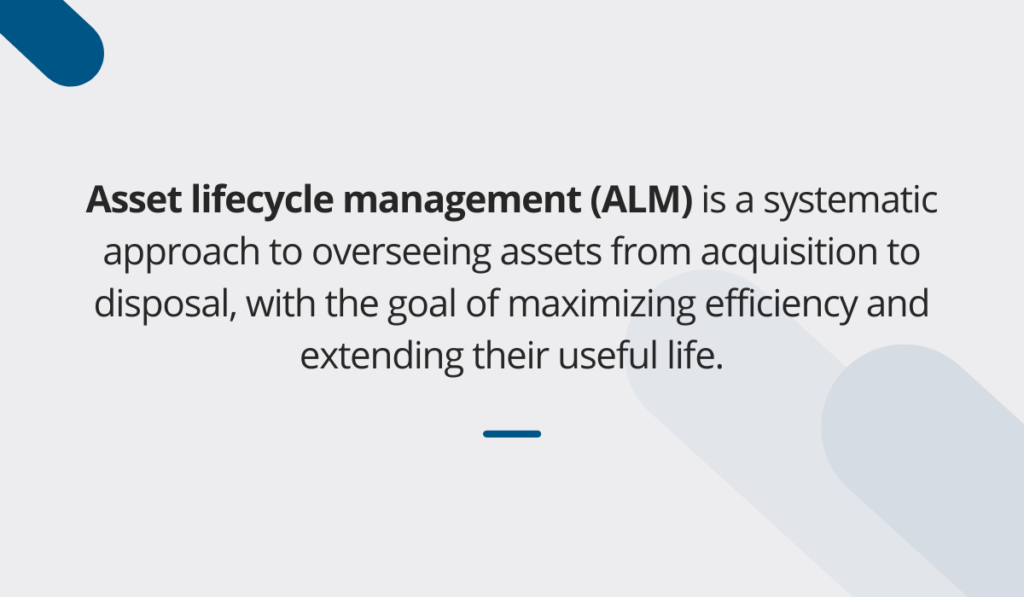
Source: GoCodes
For construction businesses operating on tight margins and strict deadlines, maximizing the value of every asset is a must.
Meanwhile, those without a clear lifecycle strategy risk overspending on repairs while still facing frequent equipment breakdowns and inefficiencies.
Add prematurely retired assets to that, and these missteps can quickly erode both productivity and profitability.
The key to avoiding these pitfalls?
Knowing when to repair, replace, or retire an asset.
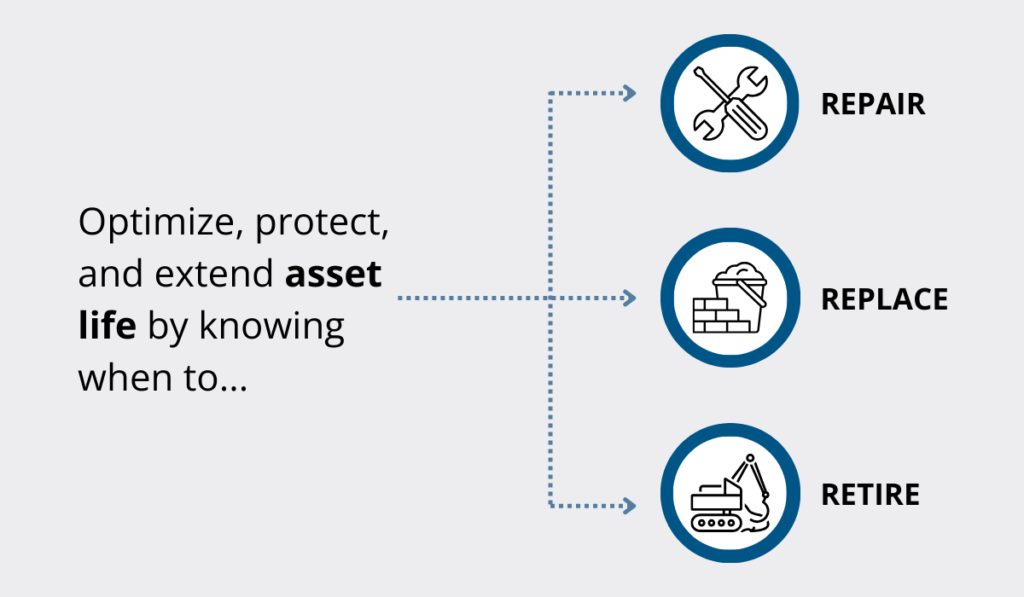
Source: GoCodes
And that decision-making process depends on more than just gut feeling.
It requires evaluating real performance data, usage patterns, financial impact, and how each asset aligns with your broader business goals.
Your ability to weigh these factors determines whether your assets become drivers of efficiency or sources of costly setbacks.
When to Repair Your Assets
Repairing equipment is often the most cost-effective decision, but only under the right circumstances.
For example, if you have a four-year-old excavator that runs well but needs minor hydraulic hose replacements or occasional engine tuning, it likely makes sense to repair.
Replacing it would mean a large upfront cost and losing out on an asset that still has years of useful life.
However, repairs aren’t always the right move.
They can become almost as expensive as replacing the asset, especially when you add ongoing maintenance to the bill.
That’s why many industry experts rely on the 50% rule.
If the cost of repairing a machine exceeds 50% of its replacement value, it’s usually more economical to replace it.
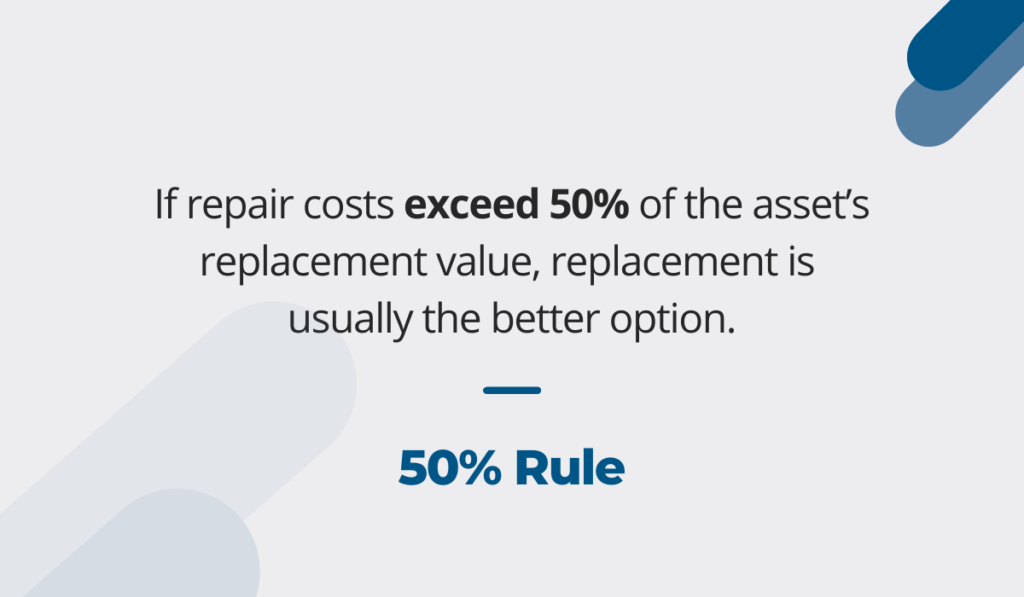
Source: GoCodes
While this rule isn’t absolute, it gives you a helpful starting point for weighing your options.
And ignoring it can lead to frequent breakdowns, delayed projects, and higher labor costs.
To prevent this, managers and maintenance teams should consider additional factors, such as overall maintenance history and total repair costs over time.
Lee Lackey, maintenance expert and Senior Product Manager at Noregon, outlines several key factors that help forecast future costs and the overall convenience of keeping the asset:
“In terms of predicting whether a trend of profitable operations will continue, you need to consider the age of the vehicle, depreciation schedule, cost of repairs, maintenance history, fuel efficiency, parts availability, resale value, ongoing operational cost,…”
One Reddit user’s advice on purchasing is just as applicable to the “repair or replace” dilemma because it highlights the asset’s market value and the functionality of its critical systems.
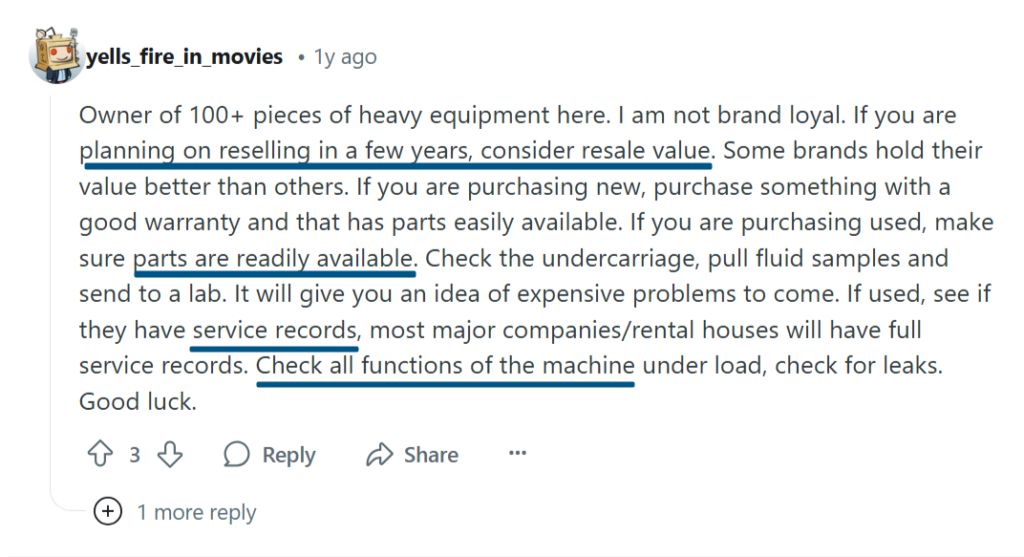
Source: Reddit
Technology also plays a major role in modern repair decisions.
Thanks to telematics and predictive maintenance tools, you can now catch issues early, interpret fault codes, and avoid surprise failures.
Patrick Brown from Mack Trucks emphasizes how diagnostics can help you decide whether a small issue could become a costly problem down the line.
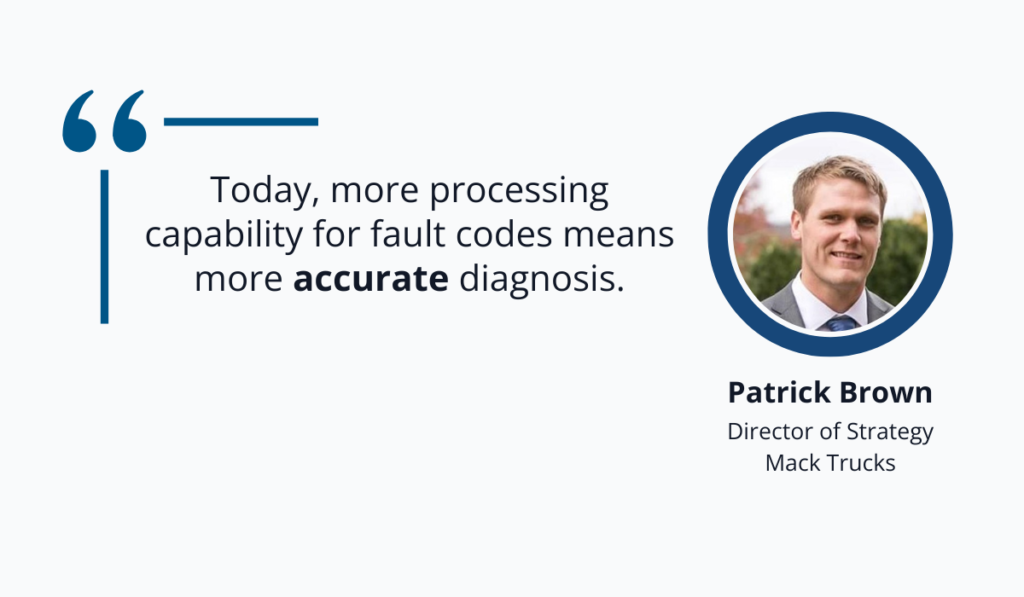
Illustration: GoCodes / Quote: Fleet Owner
In short, by combining data, expert insight, and smart technology, you can confidently determine when a repair is the right move—and when it’s time to start thinking bigger.
When Should You Replace Your Assets
At some point, repairing an asset is no longer a viable option.
Swapping an old piece of equipment for a new one is the natural progression of things, but many construction businesses are tempted to postpone it as much as possible.
And equipment prices are usually the biggest reason why.
A recent report by Equipment Watch indicates that the cost of owning and operating construction equipment amounts to anywhere between 10% to 50% of project costs.
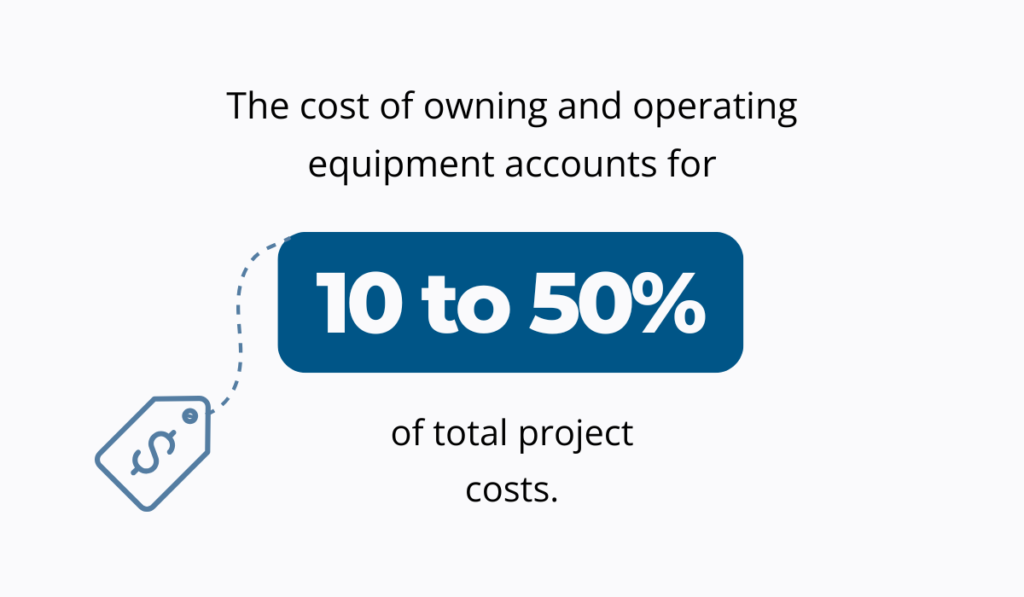
Illustration: GoCodes / Data: Equipment Watch
Given the high cost of both used and new equipment, it’s no surprise that companies want to get the most from their assets before making a switch.
But take too long, and you’re likely to lose money.
Experienced construction equipment manager Pat Crail underlines that opting for repairs involves more and more risk management, as time passes.
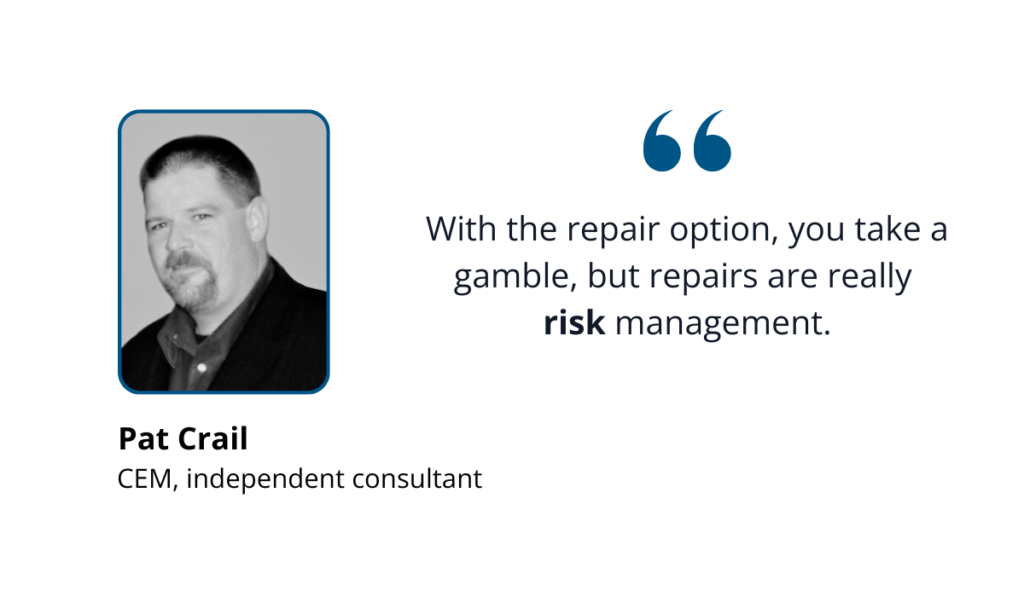
Illustration: GoCodes / Quote: Construction Equipment
If an asset has a long maintenance history, each new repair becomes a bigger gamble—one that might not stand up to the demands of future work.
And while taking that risk might make sense for a while, there eventually comes a point when it’s no longer worth it.
If your heavy machinery breaks down frequently, guzzles fuel, or drags down jobsite productivity, it’s probably time to move on.
As Josh Nickell, Former VP of Equipment Segment at American Rental Association (ARA), points out, the entire construction industry is rooted in equipment efficiency.
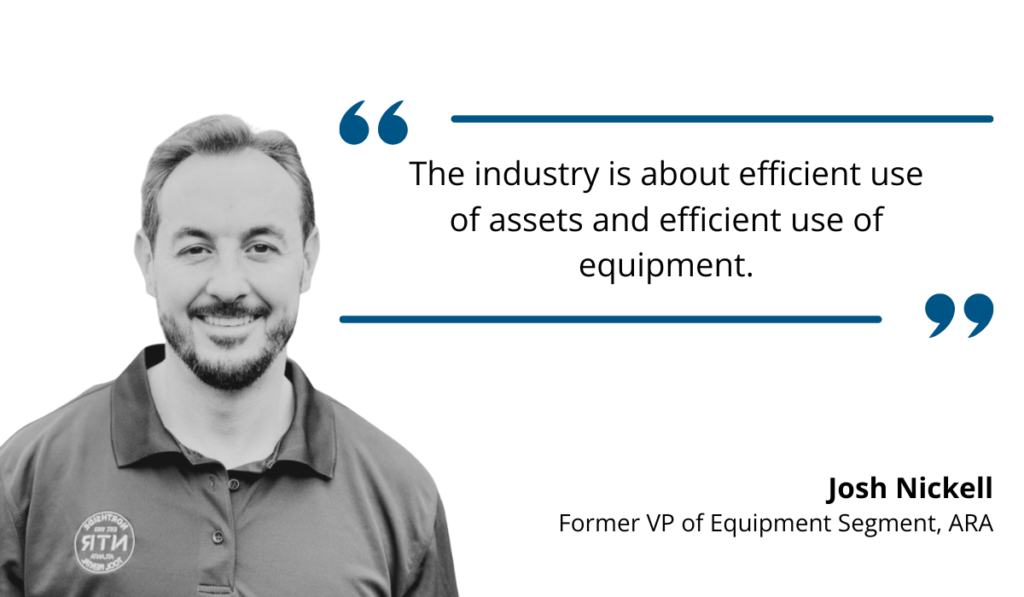
Illustration: GoCodes / Quote: For Construction Pros
If you can’t rely on your assets, you risk missing deadlines and turning down projects—two things that can seriously hurt your bottom line.
Meanwhile, finding replacement equipment can instantly improve productivity, especially if you’re willing to invest in newer models.
Rapid advances in technology mean that older models become obsolete faster, but it also brings a lot to those who are willing to pay for it.
Just take a look at Develon’s smart excavators.
These machines come with cutting-edge precision tools that optimize earthmoving operations and premium safety features, like human detection sensors and a “virtual wall.”
Source: Develon Global on YouTube
This virtual wall feature automatically stops the machine before it crosses a predefined boundary, adding an extra layer of safety for both operators and nearby workers.
Of course, new technology is costly, so if you’re purchasing new equipment, don’t overlook trade-in programs.
Many dealers offer credit for your old assets, thereby reducing the upfront cost of new equipment.
Not only does this make the switch more affordable, but it also turns outdated machinery into instant value.
At the end of the day, replacing aging assets is about more than just cost—it’s about staying productive, safe, and competitive in a fast-evolving industry.
When Should Your Assets Be Retired
When an asset is no longer useful, safe, or economical to keep, it’s time to consider retiring it from active use.
That doesn’t always mean you have a replacement ready to go—but once the decision to part ways is made, the focus shifts to choosing the best end-of-life strategy.
Whether it’s selling, scrapping, or repurposing the equipment, your goal is to extract as much remaining value as possible while minimizing risk.
But how do you know when it’s time to retire an asset?
For starters, consider the financials.
Equipment owners need a clear understanding of the total cost of ownership (TCO) for each machine in their fleet.
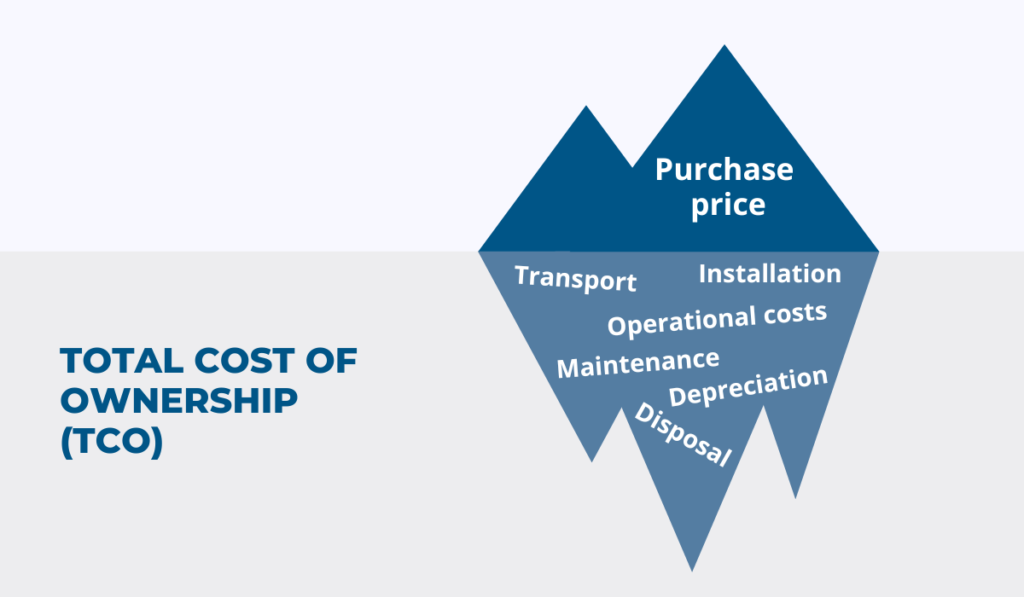
Source: GoCodes
If the asset is costing you more than it brings in value, it’s time to start planning its retirement.
Safety is another major trigger for retirement.
Whether it’s worn-out brakes that are no longer worth replacing or critical structural cracks, aging equipment can pose serious safety risks.
According to the U.S. Bureau of Labor Statistics, construction machinery was involved in 105 worker fatalities in just one year, making up 13.4% of all industry deaths.
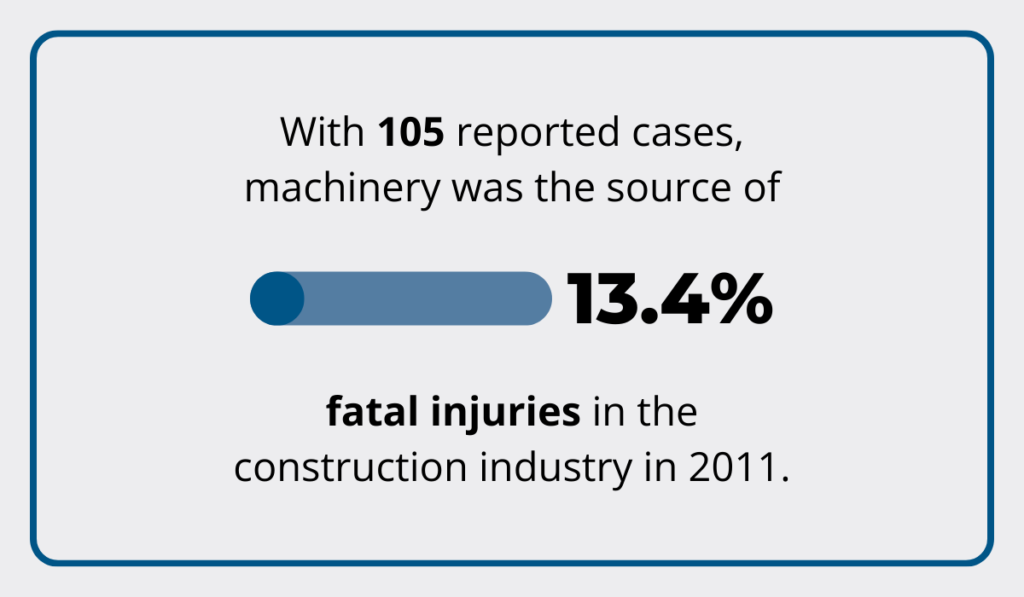
Data: BLS
More recent data shows the trend hasn’t slowed, with 199 machinery-related fatalities recorded across all industries.
While not all of these incidents are caused by old or failing equipment, the takeaway is clear: machinery must be kept in peak operating condition.
Neglecting this doesn’t just put your crew at risk.
It also increases the likelihood of project delays, compliance violations, and legal consequences.
So, once retirement is on the table, these are your main options:
Traditional or online auctions | Sell usable equipment quickly through platforms like Ritchie Bros., IronPlanet, or local auction houses. |
Used equipment dealers | Partner with companies that buy and refurbish machinery for resale to secondary markets. |
Online marketplace | Platforms like MachineryTrader, Machineryline, or Facebook Marketplace let you list both working and damaged assets for a wider audience. |
Equipment trade-in | As mentioned previously, some dealers offer credit for new purchases in exchange for old assets. |
Donation for tax credit | Donating equipment to nonprofits, schools, or community groups results in tax deductions while supporting a good cause. |
Scrap/recycle | Scrapping equipment allows you to get back some material value and reduce landfill waste. |
Which path you choose depends on the asset’s condition, resale market trends, environmental policies, and disposal costs.
Sustainable practices like repurposing assets for lighter duties or selling to emerging markets reduce environmental impact while extending the asset’s value.
And while scrapping typically brings the lowest return, it can be the most hassle-free solution—especially in uncertain markets.
In fact, Paul Hendrix, former Equipment Pricing Analyst at IronPlanet, notes that the convenience of quick disposal can easily trump financial concerns.
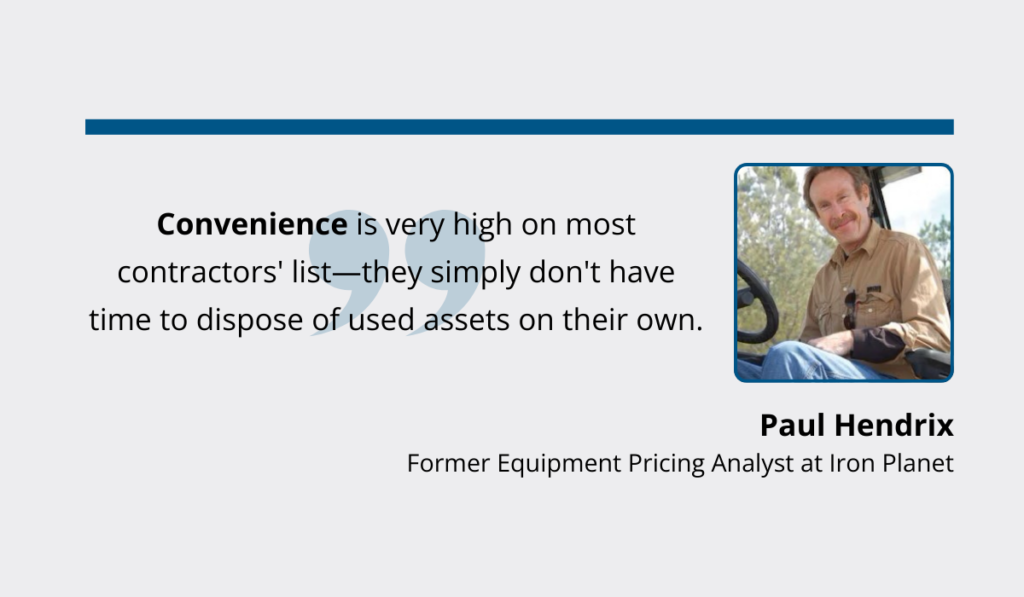
Illustration: GoCodes / Quote: Construction Equipment
The bottom line?
Retiring an asset isn’t a one-size-fits-all decision.
You need to weigh cost, safety, value recovery, and operational priorities to choose the most strategic option.
How Technology Helps with ALM
When it’s time to move on from an asset, having reliable data at your fingertips makes all the difference.
Construction companies are increasingly leveraging technology to optimize their ALM practices, from GPS tracking to IoT sensors that capture real-time data on equipment usage and detect signs of wear and tear.
Tyler Mitchell, a former equipment manager at Superior Paving Corp, explains that real-time reporting enables balanced utilization and supports predictive maintenance.
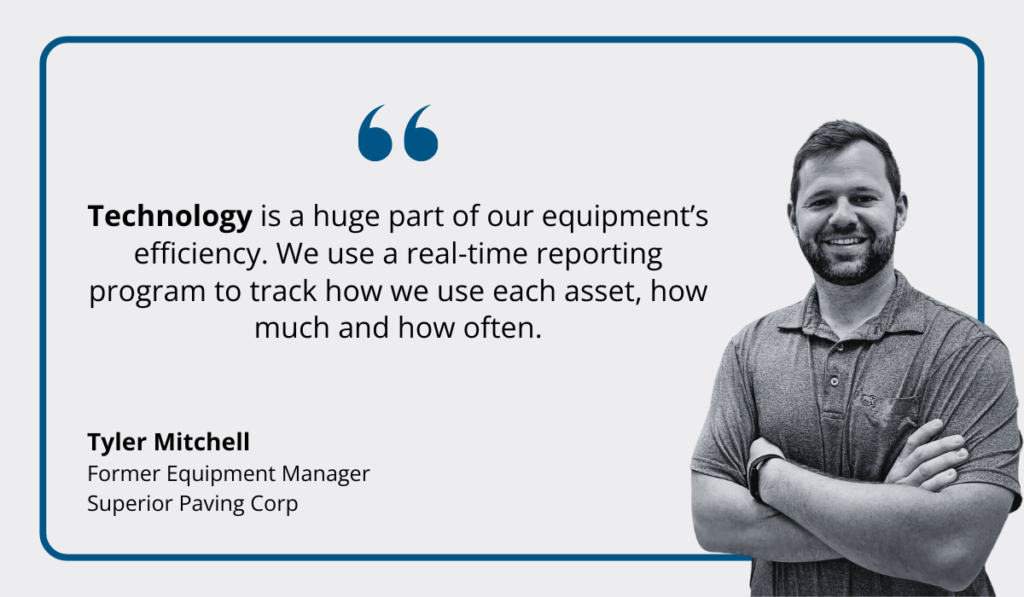
Illustration: GoCodes / Quote: Construction Equipment
With a constant stream of asset data, construction businesses can extend asset lifespan, minimize costs, and improve overall efficiency.
Deloitte’s findings on IoT as the key enabler of smarter ALM processes paint an even more optimistic picture.
Namely, potential benefits include drastically reduced unplanned downtime and a notable spike in quality and on-time delivery.
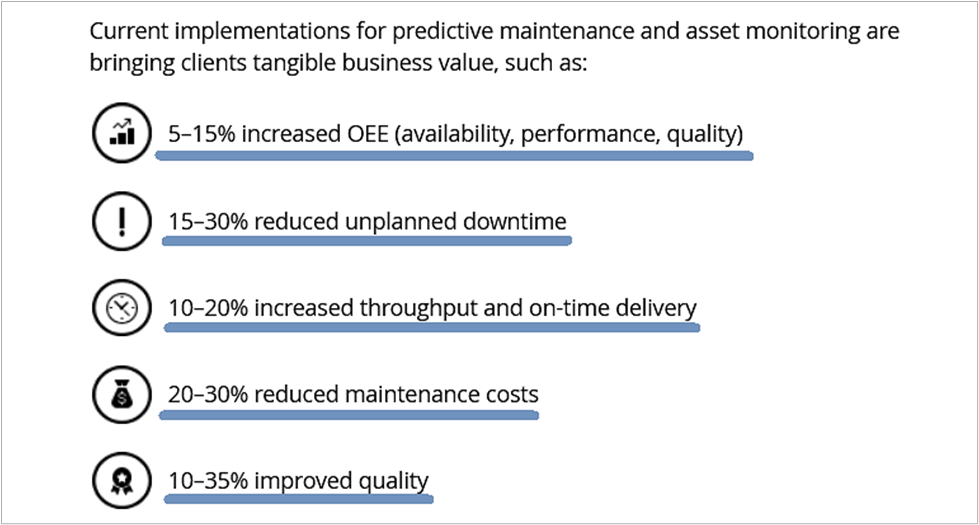
Source: Deloitte
But how does this work in practice?
Let’s break it down using the asset management solution we know best—our very own GoCodes.
GPS trackers and IoT sensors automatically log every movement and usage detail, compiling everything into a centralized, user-friendly database.
From there, companies can access actionable reports, such as under-utilization alerts or real-time utilization summaries.
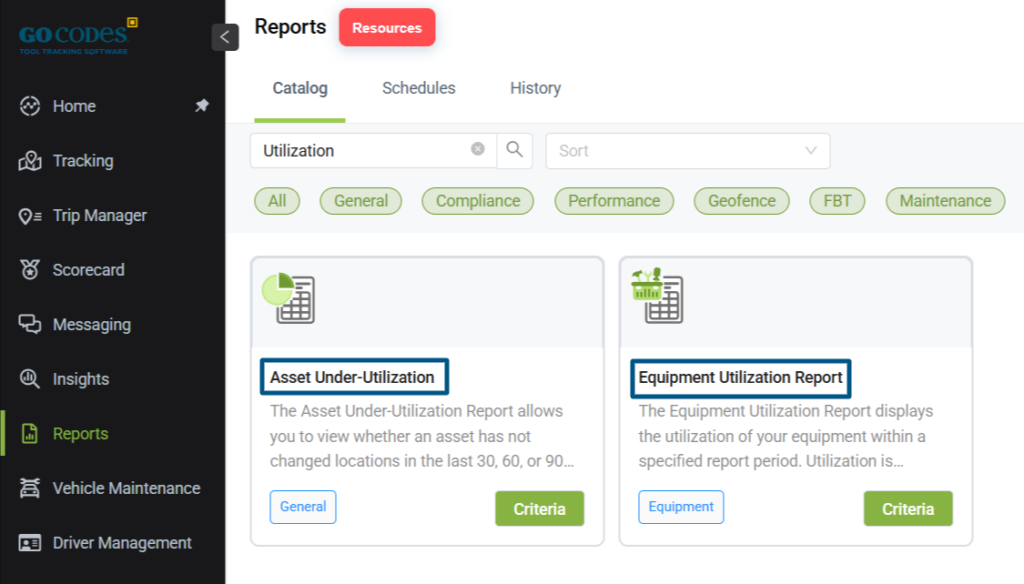
Source: GoCodes
Telematics insights lie at the foundation of predictive maintenance systems, helping you analyze performance patterns and alert managers before failures happen.
What’s more, GoCodes connects maintenance logs with essential financial data like purchase cost, depreciation, and salvage value.
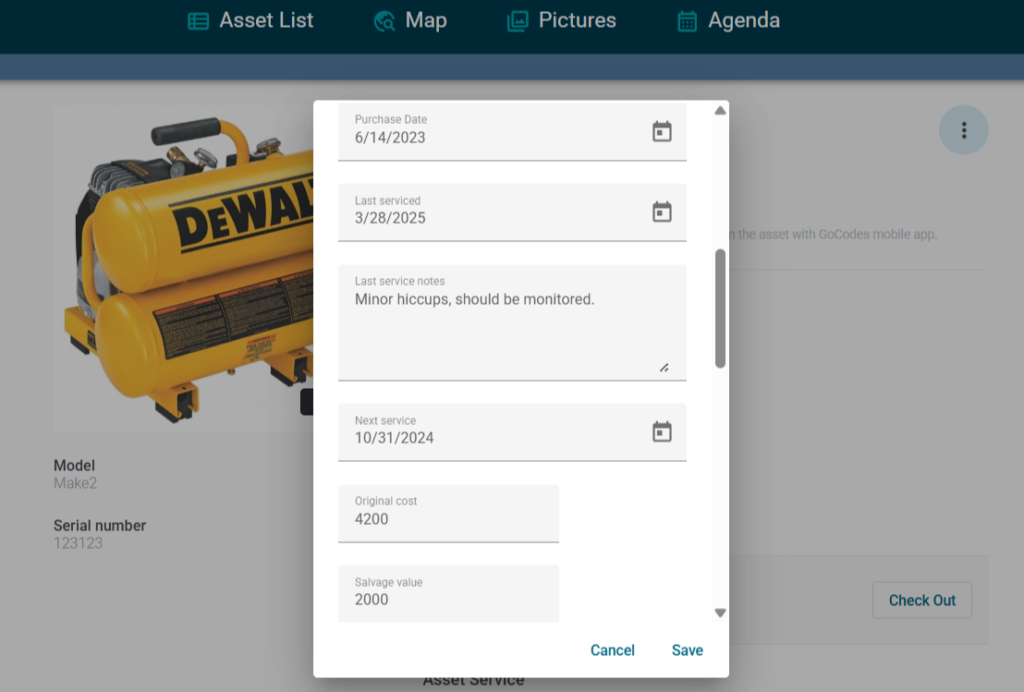
Source: GoCodes
This gives you a complete picture of your asset’s lifecycle, making it easier to decide when to acquire, repair, or retire equipment.
No matter which asset management tool you choose, technology is bound to transform how you manage your equipment.
It can help you boost efficiency, cut costs, and make smarter decisions every step of the way!
Conclusion
A single decision to repair, replace, or retire equipment can directly impact your project’s costs, safety, and timeline.
Holding on to aging equipment for a trade-in can be smart, but wait too long, and you risk unexpected breakdowns that stall operations and put your crew at risk.
General rules, like the 50% repair threshold, and a strong grasp of total cost of ownership are helpful starting points.
But to truly make the best call, you need real-time insight.
That’s where technology comes in.
Robust asset management solutions with telematics and GPS tracking help you monitor usage trends and enable data-driven decisions.
So, refine your ALM strategy with the right technology, and keep your business agile, efficient, and competitive.