Lost tools and missing equipment add up to costly problems for most tools and equipment companies.
In addition to the cost of replacing missing equipment, there are hidden operational costs that accrue when equipment goes missing, too.
For example, a worker’s time and focus must be redirected to finding and replacing equipment.
Sometimes, the cost of the tool you bought this time last year, has almost doubled. Sometimes your newly purchased equipment will arrive late, causing further project delays.
You may even be forced to borrow equipment from a sister project, slowing that project’s completion date, too.
Essentially, the knock-on effect of missing tools translates into lost productivity and lost profitability, and that’s not good for you, your team, your customer, or your wallet.
That’s why this year you’re going to stop the loss by implementing three simple steps.
When taken together, these steps can result in a 90% reduction in lost and missing tools, which for some companies can add up to hundreds of thousands of dollars in savings annually!
Best of all, these steps are easy to implement.
In this article...
Step 1: Track Chain of Custody
Create a Chain of Custody process to ensure that you (and your team) know which person is accountable for each tool no matter where it is or what project it’s being used on.
What does this look like?
Ensure that a team lead is given the responsibility for checking tools in and out to individual team members.
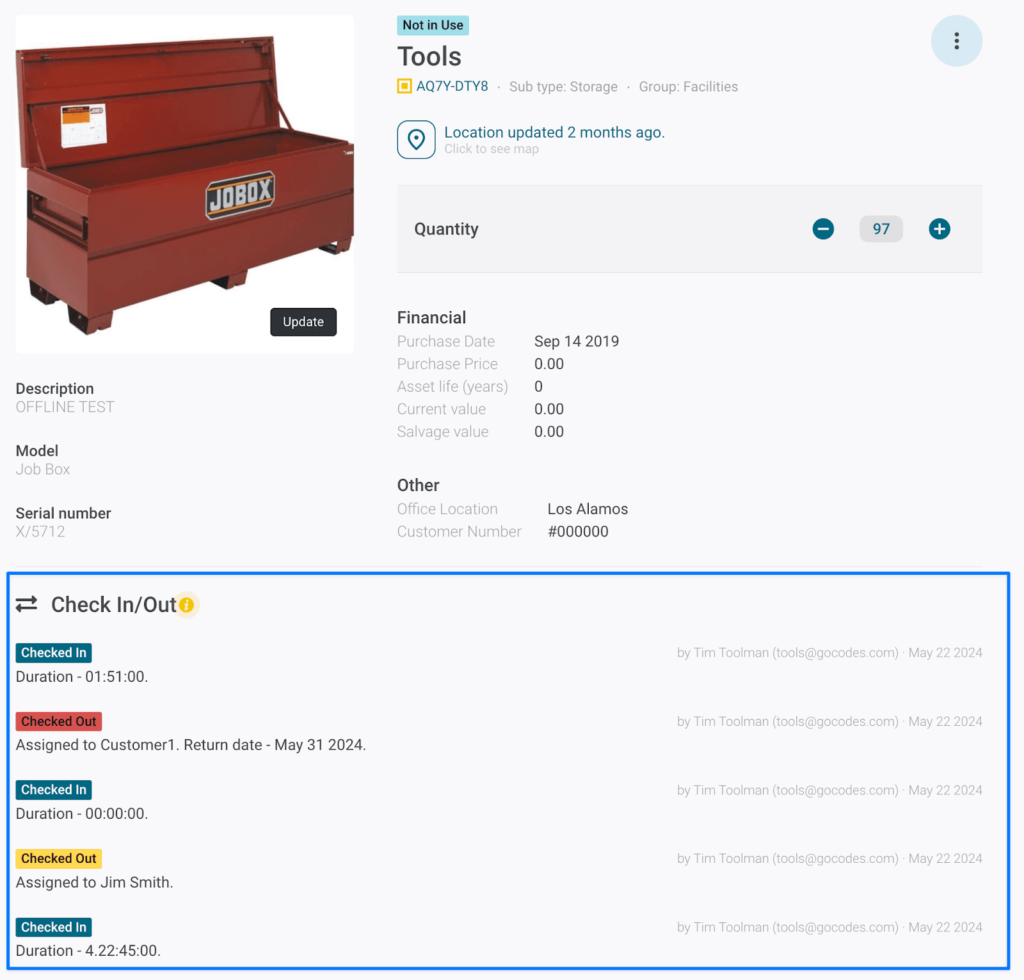
Then implement an incentive scheme to ensure that team members take accountability for the tools checked out to them.
Some companies even bill employees who demonstrate excessive tool loss.
Talk to your team leads and decide upon a program that will drive accountability in your business.
Step 2: Perform Monthly Physical Audits
Physical audits are a must if you want to track your tools.
Ideally, physical audits should be performed on a monthly basis.
At a minimum, they should be undertaken annually at the end of the financial year, so that you’re able to report accurate financial results, including what fixed assets your organization owns.
What’s the best way to accomplish a physical audit?
We recommend performing a physical audit using our Scanner app and Audit Mode Scanning feature.
This feature enables your team to quickly scan all the equipment at their location and create a report that shows which equipment was scanned and which is missing.
The missing equipment list can then be used to drive further searches for missing and lost tools.
Step 3: Create Weekly Automated Audit Reports of Equipment at High Risk for Loss
Finally, use the GoCodes’ Reporting feature to create automatic weekly Audit reports that are emailed to key supervisors, as well as management.
The Audit reports can be used to identify specific equipment that you consider high risk for loss.
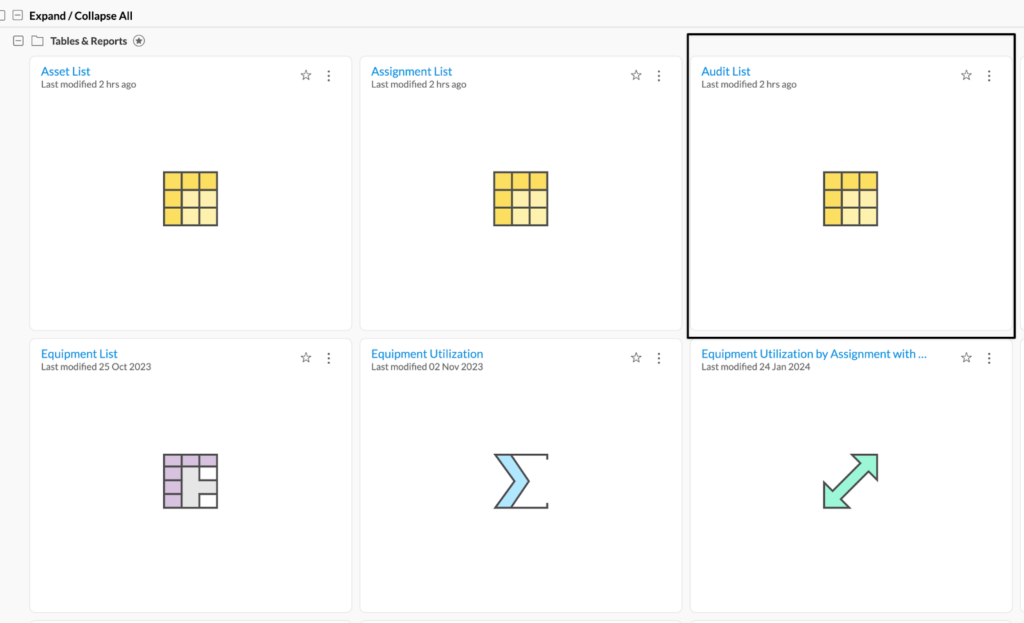
For example, you may decide that an Audit Risk report should include all tools with a value over $1,000, which are located offsite, are movable, and have not been updated in GoCodes for over 30 days.
Your supervisors can then implement a physical audit to determine whether the equipment is where it’s supposed to be.
The continuous follow-up each month will drive accountability, resulting in reduced tool attrition to stop the loss.